Rein in die digitale Produktion!
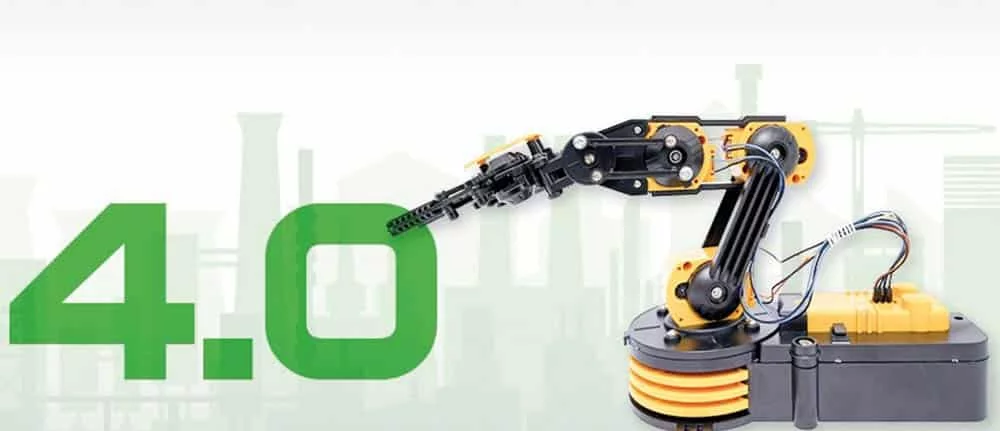
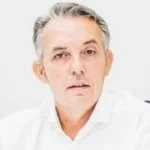
Um wettbewerbsfähig zu bleiben, müssen Hersteller immer komplexere und individuellere Produkte immer schneller entwickeln und produzieren. Die digitale Vernetzung ist deshalb das beherrschende Thema der Branche. Die Zielvorgabe: Immer besser sollen Mensch, Maschine und Produkt über digitale Systeme miteinander verbunden sein.
Doch die Wahrheit ist: Industrie 4.0 gehört noch immer lediglich zum Wunschdenken der meisten deutschen Produkthersteller. Die allermeisten haben bestenfalls erste Schritte in Richtung Digitalisierung unternommen. Das zeigt unsere langjährige Erfahrung als Software- und IT-Spezialist für die Fertigungsindustrie.
Aber wieso ist das so? Wieso sind diese Unternehmen nicht schon viel weiter in Sachen Digitalisierung und Industrie 4.0? Wo sie doch zweifelsohne wissen, dass sie ihre Produkte dadurch schneller und in besserer Qualität auf den Markt bringen und somit ihre Umsätze steigern können? An den technischen Voraussetzungen kann es auch nicht liegen – die existieren mittlerweile.
Die Antwort: Das Tagesgeschäft verhindert in vielen Fällen eine schnellere Digitalisierung. Eine Lösung für das Dilemma kann deshalb nur eine entschlossene Unternehmensführung liefern. Nur sie kann im Arbeitsalltag die nötigen Freiräume schaffen, um digitale Technologien zu testen und zu etablieren.
Und auch das weitverbreitete Silodenken in deutschen Mittelstandsbetrieben kann ausschließlich durch das Management überwunden werden. Verschiedene Abteilungen arbeiten in vielerlei Hinsicht oftmals nur für sich – so auch bei der Auswahl passender Software. Deshalb sollte die Geschäftsführung übergreifende Softwaresysteme auch als Managementaufgabe begreifen.
Nun könnte ausgerechnet die Coronakrise die digitale Stagnation beendet haben. So haben sich etwa Videokonferenzen in vielen Unternehmen endgültig durchgesetzt. Natürlich ist digitales Arbeiten mit zum Beispiel Zoom noch lange keine Digitalisierung. Jedoch könnte die neue digitale Normalität auch Lenkern aus der Fertigungsbranche verdeutlichen, dass es mit weniger Präsenz vor Ort durchaus klappen kann, ja sogar muss.
Verstärkt wird der Lerneffekt durch krisenbedingte Auftragseinbrüche – so schmerzhaft sie auch sind. Die resultierenden Überkapazitäten haben potenzielle Freiräume geschaffen, in denen für das drängende Thema Digitalisierung wieder mehr Zeit übrig war.
Vorausschauende Manager konnten diese Zeit nutzen, um die gegenwärtige Situation zu bewerten. Dann mussten sie fast zwangsläufig eine Schlussfolgerung ziehen: Es wird zukünftig zwingend notwendig sein, vermehrt abseits der realen Produktionsumgebung arbeiten zu können. Dazu gehört unweigerlich auch ein vollständiges digitales Produktmodell. Dieser „digitale Zwilling“ ist unserer Überzeugung nach der eigentliche Kern von Industrie 4.0.
Er enthält alle Informationen über das Produkt, seine Herstellung und seinen Zustand entlang der gesamten Wertschöpfungskette von der Entwicklung über die Planung und Produktion bis hin zum After-Sales-Service. Eigenschaften und Verhalten eines Produkts lassen sich durch dieses digitale Abbild bereits vor der physischen Fertigung perfekt simulieren. Bis zur Automatisierung selbst komplexer Produktionsvorgänge ist es dann nur noch ein kleiner Schritt.
Digitaler Wandel braucht Zeit
Letztendlich braucht es nicht zwingend eine Krise, um die Digitalisierung voranzutreiben – sondern vor allem die langsam und gründlich wachsende Erkenntnis, dass produzierende Unternehmen ohne vernetzte und selbstlernende Systeme langfristig nicht überleben können.
Deshalb ist Industrie 4.0 eben eigentlich keine industrielle Revolution, sondern eine Evolution. Gut so! Denn eine umfassende Digitalisierung bedeutet für die meisten Unternehmen nicht weniger als einen schmerzhaften Kulturwandel. Und den vollzieht man besser schrittweise als schlagartig.