Produktionsplanung mit SAP
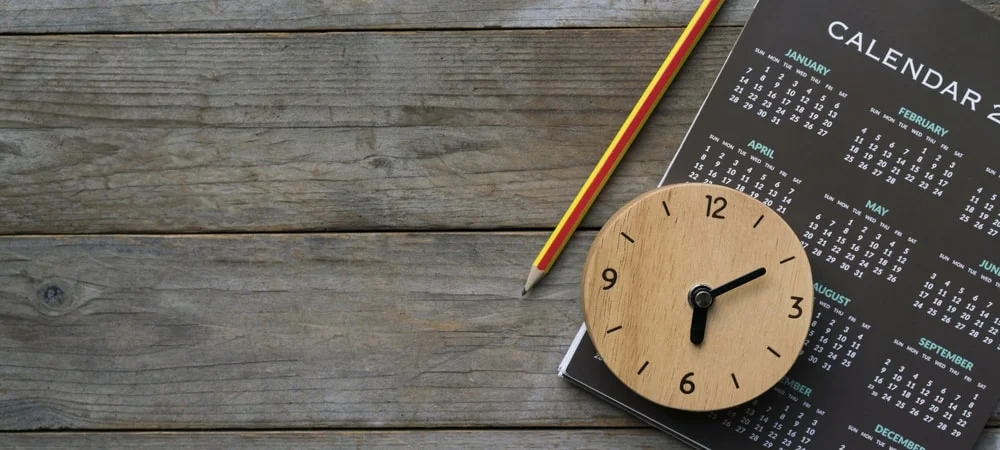
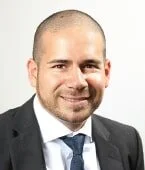
Als eines der größten Geschäftsrisiken sehen Unternehmensverantwortliche eine Betriebs-unterbrechung an. Das hat eine Studie des Versicherers Allianz Global Corporate & Specialty (AGCS) aus dem Jahr 2022 ergeben. Damit liegt die Sorge einer Betriebsunterbrechung noch vor der Furcht vor Cyberangriffen. Auch RHI Magnesita, ein global führender Anbieter von hochwertigen Feuerfestprodukten, -systemen und -dienstleistungen, hatte in den vergangenen zwei Jahren mit schwankender Nachfrage und schwer zu beschaffenden Rohstoffen zu kämpfen. Das Unternehmen mit Hauptsitz in Wien, Österreich, stellt jährlich mehr als 1,5 Millionen Tonnen Feuerfestprodukte an weltweit über 30 Hauptproduktionsstandorten her, die in indus-triellen Hochtemperaturprozessen über 1200 Grad Celsius zum Einsatz kommen – unter anderem in der Stahl-, Zement-, Nichteisenmetalle- und Glasindustrie. Die Produkte werden in verschiedenen mehrstufigen und komplexen Prozessen hergestellt. Um dabei flexibel auf Veränderungen reagieren zu können und Engpässe sowie Stillstände zu vermeiden, hat RHI Magnesita sich dazu entschieden, seine Produktionsplanung auf operativer Ebene zu optimieren.
Effizientere Produktionsplanung gelingt mit Production Planning and Detailed Scheduling (SAP PP/DS). Um den sich stets ändernden Marktanforderungen gerecht zu werden, soll die Bedarfs- und Produktionsfeinplanung weiter optimiert werden. Dazu wurde bei RHI Magnesita ein weltweites Template für den Planungsprozess definiert und SAP PP/DS als Advanced-Planning-and-Sche-
duling-System eingeführt.
Planning und Scheduling
Mit dem PP/DS-Optimizer wird unter Berücksichtigung der Rohstoffe, der Engpassressourcen sowie der Werkzeuge ein mehrstufiger Produktionsplan erstellt. Produktionsreihenfolgen lassen sich schnell unter Berücksichtigung von Rüstzeiten sowie Rüst- und Verspätungskosten erstellen, und zwar so, dass der Produktionsplaner nicht mehr manuell eingreifen muss (kunden-eigene Heuristik). Dadurch spart der Hersteller Zeit und Aufwand. In ähnlichen Projekten konnten die Bestandskosten um etwa 10 Prozent, Rüstzeiten um 20 Prozent reduziert sowie der Lieferbereitschaftsgrad auf über 90 Prozent erhöht werden.
Der wesentliche Vorteil ist aber, dass durch eine Alert-basierte Planung flexibel und schnell auf Schwankungen auf der Beschaffungs- und Absatzseite reagiert werden kann. Dadurch werden Engpasssituationen vermieden und einem Mangel an Rohstoffen vorgebeugt. Basis hierfür bildeten die enge Verzahnung der angrenzenden Systeme und ein daraus entwickelter digitaler Zwilling der Produktion. Das physische Abbild von SAP PP/DS ermöglicht Simulationsmodelle und liefert Echtzeitdaten für die Bedarfsplanung. RHI Magnesita kann nun Produktionsmengen, Maschinenzustände, Strom, Mengen oder auch Materialverbräuche betrachten. Damit lassen sich in Echtzeit nicht nur Probleme schneller erkennen, sondern auch Transparenz über die Ist-Situation gewinnen und als Basis für Unternehmensentscheidungen nutzen.
Die Implementierung eines PP/DS ist dementsprechend ein wichtiger Teil im Gesamtkontext bei der Realisierung einer modernen Produktionsplanung. Wichtig ist dabei jedoch, dass die bestehenden Prozesse, Systeme und Organisationsstruktur ebenfalls berücksichtigt und bei Bedarf angepasst werden. Letztlich ist die Akzeptanz des Tools ein weiterer wesentlicher Erfolgsfaktor. All das stellt RHI Magnesita durch die effektive und reibungslose Zusammenarbeit mit SAP und MHP sicher.
