Digitale Industrie-Transformation
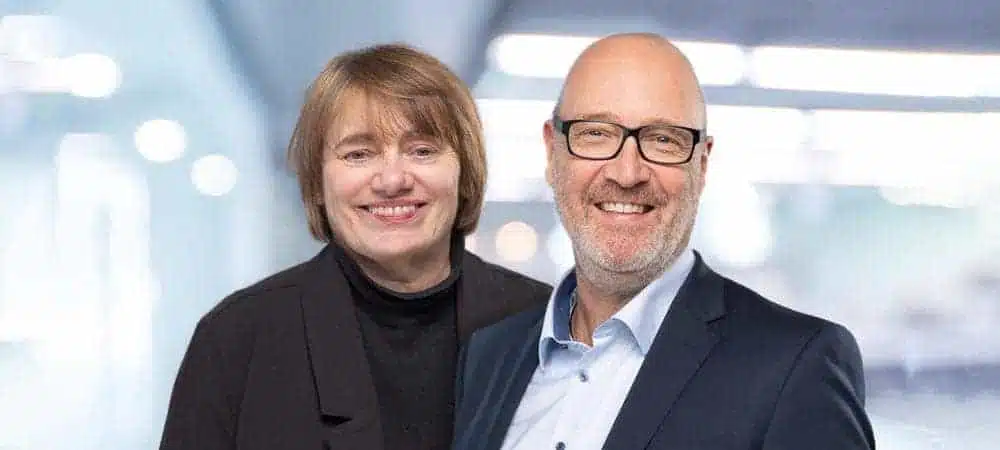
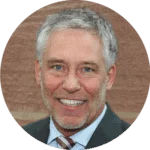
Für manche Anwender mag es eine Evolution sein, andere sehen in Industrie 4.0 und dem industriellen Internet der Dinge (IIoT) eine Revolution. Die Wurzeln dieser digitalen Industrie-Transformation liegen mehrere Jahrzehnte zurück: Wer erinnert sich noch an CIM, Computer Integrated Manufacturing? Und was ist nun Industrie 4.0?
„Der Begriff Industrie 4.0 beschreibt es plakativ – es handelt sich um die vierte industrielle Revolution der Digitalisierung: nach Mechanisierung mit Dampf- und Wasserkraft, nach Massenfertigung durch Elektrifizierung und nach dem Einsatz von Elektronik und IT“
erklärt Forcam-Co-CEO Oliver Hoffmann zu Beginn des E-3 Gesprächs. Die digitale Transformation in der Industrie meint die Gesamtheit aller Schritte hin zu dem Ziel, alle technologischen Möglichkeiten der Automatisierung und intelligenten Vernetzung von Maschinen zu nutzen, um mehrere Ziele zu erreichen: effizientere Produktion und Prozesse im Sinne einer Nahe-null-Fehler-Fabrik; verbesserte globale Liefer- und Serviceketten; verbesserte, kundenspezifischere Produkte.
Technologisch geht es um das digitale Erfassen und Normieren von Daten, um sie in einen semantischen Layer zu überführen. Im Englischen sagt man „Information on a fingertip“.
Oliver Hoffmann übersetzt:
„Wir sagen Big Data in Smart Data verwandeln, in analytisch nutzbare Echtzeit-Informationen in Form eines digitalen Zwillings der Produktion am Computer.“
Vernetzte Produktionsanlagen, Echtzeit-Kommunikation zwischen Maschinen, individuelle Unterstützung vom Kollegen Roboter: Die Digitalisierung der Industrieunternehmen in Deutschland macht Fortschritte, weiß auch der Digitalverband Bitkom.
Fast sechs von zehn Industrieunternehmen mit mehr als 100 Mitarbeitern in Deutschland, also etwa 60 Prozent, nutzen spezielle Anwendungen aus dem Bereich Industrie 4.0.
Das ist das Ergebnis einer Studie zur Digitalisierung der deutschen Industrie im Auftrag des Digitalverbands Bitkom, für die 552 Industrieunternehmen ab 100 Mitarbeitern von Mitte Februar bis Anfang April 2020 befragt wurden.
Der Weg in die digitale Industrie-Transformation scheint somit unwiderruflich vorgegeben zu sein. Andrea Rösinger, Kollegin von Oliver Hoffmann und Co-CEO bei Forcam, verweist im Gespräch auf das damit einhergehende Change Management:
„Digitale Transformation hat noch eine wichtige zweite Ebene neben der technologischen. Die Einführung einer IIoT-Plattform bedeutet immer auch einen kulturellen Wandel innerhalb des Unternehmens. Daher kann eine digitale Transformation in einem Industrieunternehmen nur mit zwei Flügeln fliegen:
Der erste ist die adäquate IIoT-Technologie, der zweite die passende kulturelle Lösung. Denn verbesserte Effizienz und Qualität werden nur durch die Leidenschaft derer erreicht, die sie liefern sollen – die Mitarbeiter selbst.
Die Führung muss deshalb auf eine neue Lernkultur abzielen mit Elementen wie Selbstverantwortung von qualifizierten Teams, virtuelle Zusammenarbeit von interdisziplinären Teams, neue Wege der Kommunikation und des Umgangs mit Fehlern.“
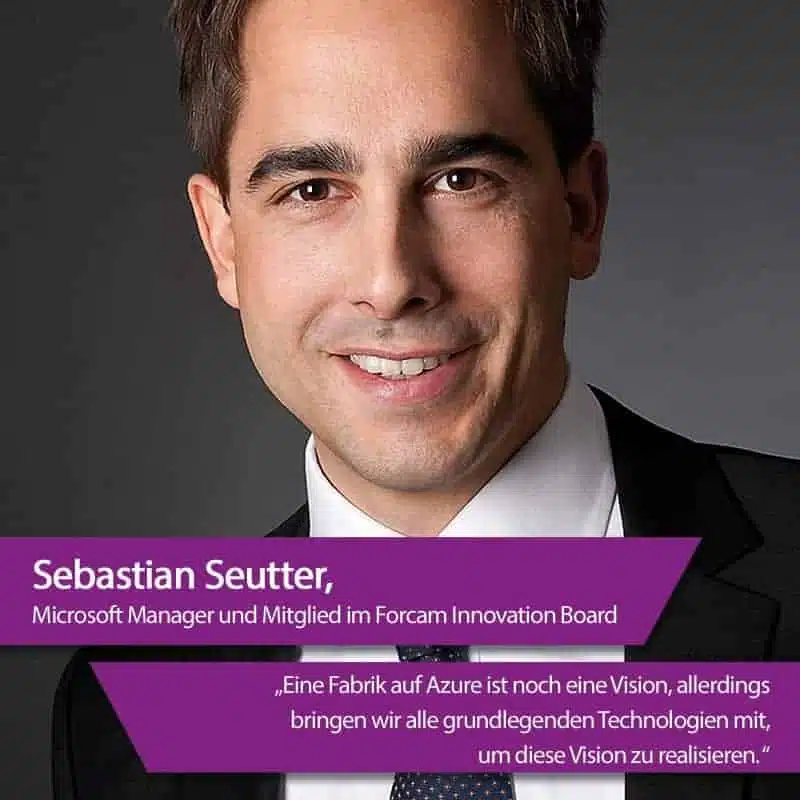
Das Unternehmen braucht nach Ansicht von Rösinger und Hoffmann ein breites Verständnis dafür, dass nur die Transparenz und Effizienz durch datengestützte Fertigung mit präzisen KPIs eine Chance für höhere Produktivität und nachhaltige Optimierung sind.
Bitkom hat dazu erhoben, dass bei fast drei Viertel der deutschen Industrieunternehmen im Zuge von Industrie 4.0 nicht nur einzelne Abläufe oder Prozesse verändert werden, sondern ganze Geschäftsmodelle.
Etwas mehr als jedes zweite Unternehmen entwickelt neue Produkte und Dienstleistungen oder plant dies. Jedes vierte verändert bestehende Produkte oder hat dies vor. 28 Prozent nehmen bisherige Produkte und Dienstleistungen sogar ganz vom Markt. Change Management scheint somit angesagt zu sein.
„Automobilproduzenten entwickeln sich zu Anbietern von Mobilitätslösungen und Hersteller von Medizintechnik zu smarten Gesundheitsdienstleistern. Dieser Weg muss nun branchenübergreifend in der gesamten Industrie fortgeführt werden. Die Geschäftsmodelle der Zukunft sind ausschließlich digital“
so Bitkom-Präsident Achim Berg.
„Umso wichtiger ist auch, dass das Thema Bildung – Education und Enablement – mit auf die Maßnahmenlisten der digitalen Transformation gehört“
betont Andrea Rösinger in dieser Diskussion. Die digitale Transformation in der Produktion und Fertigung ist eine betriebswirtschaftliche, organisatorische und technische Herausforderung.
„Es ist eine Herausforderung für das ganze Unternehmen, daher eine Herausforderung für alle drei genannten Bereiche“
erklärt Franz Gruber, Gründer von Forcam.
Betriebswirtschaft, Organisation und Technologie müssen integriert betrachtet und bearbeitet werden. In der digitalen Transformation sind Technik und Betriebswirtschaft untrennbar, dann kommt die Organisation.
„Ich will aber noch weiter gehen“
definiert Gruber.
„Die digitale Transformation in der Industrie ist eine volkswirtschaftliche – und daher eine gesellschaftliche – Herausforderung. Von einer vitalen Industrieproduktion hängt der Wohlstand moderner Volkswirtschaften ab.
Der Kuka-Manager Heinrich Munz hat in seinem Vortrag auf einer Forcam-Veranstaltung nachgewiesen: Je mehr Automatisierung, also je mehr Roboter, eine Gesellschaft hat, desto niedriger ist ihre Arbeitslosenquote.
Deshalb ist es die Herausforderung, dass wir digitale Transformation im Konzert aller Parteien, insbesondere der Tarifparteien, bearbeiten müssen, nicht im Konflikt.“
Die Fachkräftesicherung ist ein wichtiges Thema bei den Industrieunternehmen, definiert die erwähnte Bitkom-Studie: 66 Prozent bekräftigen, dass durch Industrie 4.0 neue Arbeitsplätze für gut ausgebildete Fachkräfte entstehen.
Fast alle meinen, dass die Arbeit in der vernetzten Fabrik verstärkt interdisziplinäre Kompetenzen erfordert, etwa an der Schnittstelle von Maschinenbau und Informatik.
„Die Einführung neuer Technologien, Werkzeuge und Methoden hat natürlich Auswirkungen auf die Beschäftigten in den Unternehmen. Digitale Bildung und Weiterbildung sind jetzt und in Zukunft essenziell“
betont Bitkom-Präsident Achim Berg.
„Der Wissens- und Ausbildungsbedarf wird bedingt durch schnellere Innovations- und kurze Produktzyklen immer größer. Digitale Bildung langfristig zu garantieren muss gemeinsames Interesse von Politik und Wirtschaft sein.“
Die zahlreichen Anforderungen und Chancen führen zur Frage: Ändern sich auch Geschäftsprozesse in der fertigenden Industrie durch IIoT? Muss sich die Organisation der „Fabrik“ ändern? „Eindeutig ja“, sagt Co-CEO Rösinger. Sie meint, dass Unternehmen ein strategisch fundiertes und operativ ausgerichtetes Organisationsmodell benötigen, ein Strategic Operating Model.
„Denn Führungs- und Prozessexzellenz sind zwei Seiten einer Medaille“
präzisiert Andrea Rösinger.
„Mit Einführung neuer Technologien wird, wie bereits beschrieben, auch eine neue Kultur benötigt. Hintergrund ist, dass sich natürlich der Trend fortsetzt, dass Low-skill-Jobs in der Industrie auf dem Rückzug sind, aber der Bedarf an Fachkräften weiter hoch bleibt. Die Organisation einer Fabrik benötigt daher eindeutig diese Bildungskomponente.“
Die Digitalisierung der Produktion und Fertigung hat eine sehr lange Tradition, die irgendwann einmal vor Jahrzehnten mit CIM, Computer Integrated Manufacturing, begann: Wieso hat es bis zu IIoT so lange gebraucht? Was unterscheidet die damaligen Konzepte von aktuellen IIoT-Lösungen? Dazu antwortet Forcam-Gründer Franz Gruber:
„Ich begann meine berufliche Laufbahn in der CIM-Zeit der 1990er-Jahre. Deshalb kann ich sagen: Die Unternehmen haben früher in den Boomzeiten immer Revenue gemacht. Kosten spielten keine so große Rolle.
Prominentes Beispiel: Der sehr erfolgreiche Börsengang der Deutschen Telekom 1996 mag symbolisch für diese Aufbruchstimmung in der Breite stehen. Computerisierung hatte sich als Wunderwaffe in der Wirtschaft etabliert, nun wurde auch in der Fertigung munter investiert.“
Andrea Rösinger ergänzt:
„Zudem waren natürlich die technologischen Möglichkeiten noch nicht vorhanden – etwa Bandbreiten. Früher galt: je weniger Daten, desto besser. Heute spielen Datenvolumina durch immer neue Bandbreiten und digitale Kapazitäten keine so große Rolle mehr.“
Und Oliver Hoffmann erklärt das IIoT-Phänomen:
„Der Investitionsrhythmus von Unternehmen ist schon zur Sprache gekommen: Unternehmen investieren in Maschinen und Anlagen für große Zeiträume, zehn, 15, 20 Jahre.
Auch deshalb dauert es in der Industrie länger, bis sich eine neue technologische Ära wie das IIoT in der Breite durchsetzt. Umso wichtiger ist es, auf eine moderne IIoT-Plattform zu setzen, die es ermöglicht, Investitionen zu schützen und gleichzeitig Innovationen zu ermöglichen.“
Die Analysten von Gartner (USA) stellen Forcam ein Alleinstellungsmerkmal aus: „Forcam Force is the only IIoT-Platform with out-of-the-box MES applications.“
„Fast alle Unternehmen haben sich auf den Weg in Richtung Industrie 4.0 gemacht“
sagt Bitkom-Präsident Achim Berg. Diese Erkenntnis ist auch im größten Teil der Unternehmen verankert: 94 Prozent sehen in der Industrie 4.0 die Voraussetzung für den Erhalt der Wettbewerbsfähigkeit der deutschen Industrie.
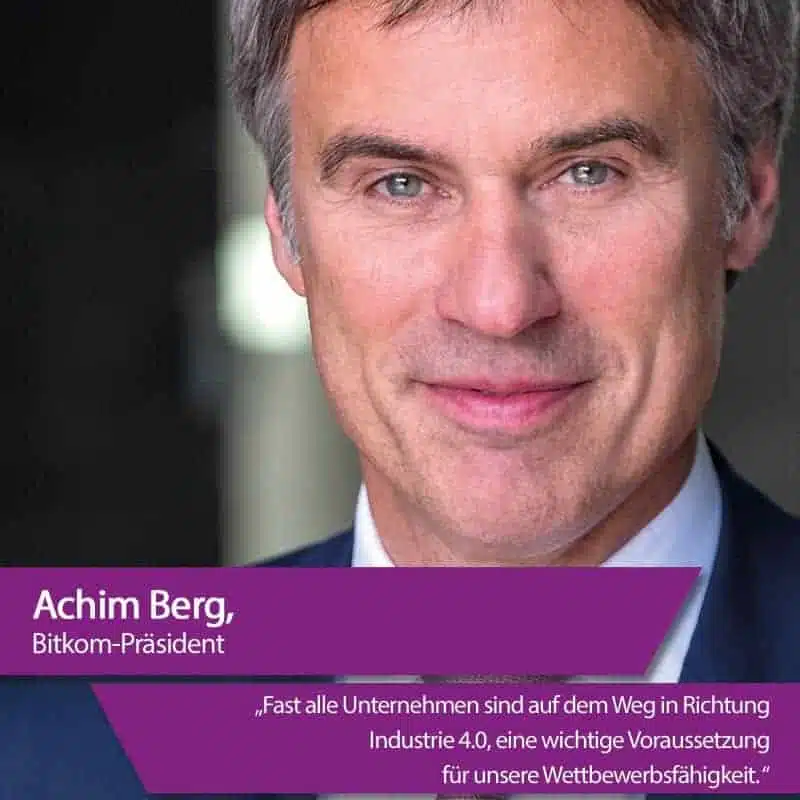
Mehr als jeder Zweite betont, Industrie 4.0 gebe dem eigenen Geschäft generell neuen Schub. Insgesamt sieht eine überwältigende Mehrheit von 93 Prozent der Industrieunternehmen Industrie 4.0 als Chance.
Industrielle Steuerungssysteme, elektronische Plantafeln, Manufacturing Execution System, das gibt es seit vielen Jahren. Was ist in der „digitalen Transformation“ anders und neu?
„Die genannten Themen gibt es alle weiterhin, sie sind weiter alle präsent im Fabrikalltag. Die Investitionen sind nicht verloren“
beruhigt Oliver Hoffmann.
„Was anders ist, ist die Vernetzung, und heute kann ich mit vernetzten Teilen, Produkten und Einheiten sowie mit vernetzten Prozessen viel effizienter arbeiten. Durch digitale Offenheit über offene Web-Schnittstellen – Open API – ist es zudem möglich, ganz individuelle IT-Architekturen zu bauen und vorhandene oder neue Lösungen auf einer Plattform interagieren und kollaborieren zu lassen.“
Was kann aus der „alten“ Welt in die digitale Transformation der Industrie übernommen werden? Franz Gruber:
„Die Ziele der alten Welt bleiben: Lean und Clean fertigen. Die Ziele der verschiedenen Konzepte – ob KVP, TPM usw. – gelten. Neu sind die technologischen Möglichkeiten, die Ziele zu erreichen.“
Mit den neuen technologischen Möglichkeiten von integrativen IT-Architekturen, von Interoperabilität, Komposition und Kollaboration durch offene Plattformen und einheitliche Datenseen entstehen auch neue Bedarfe, zum Beispiel für eine gute IIoT-Prozessberatung.
Sie sollte von Experten ausgeführt werden, welche sowohl die Fabrik von innen kennen als auch die neuen technologischen Möglichkeiten der Ära des IIoT. Bitkom hat erhoben, dass die Mehrheit der Industrieunternehmen, die neue Produkte und Dienstleistungen im Zuge von Industrie 4.0 entwickeln, auf Plattformen setzt.
Eine ebenfalls große Bedeutung wird künstlicher Intelligenz (KI) beigemessen. Jedes siebte Unternehmen nutzt aktuell KI im Kontext von Industrie 4.0. Zu den gängigen KI-Anwendungen zählen etwa Predictive Maintenance, bei der mithilfe von Algorithmen und Sensoren der Betrieb von Maschinen überwacht wird, sodass die KI noch vor einem drohenden Ausfall auf die notwendige Wartung hinweist. Auch Roboter, die ihre Arbeitsabläufe auf aktuelle Erfordernisse hin selbstständig anpassen können, sind ein solches Beispiel.
„Das semantische Modell von Forcam basiert auf fundierten Kenntnissen im Fertigungsprozess, in seiner Vielseitigkeit und ausgeprägten Variabilität“
kommentiert Olga Mordvinova, Geschäftsführerin Incontext Technology und Forcam-Partner. Das Modell wandelt vorinterpretierte Produktionsdaten in konsistenten Datenstrukturen, die nicht nur Maschinen- bzw. Arbeitsplatzinformation bereitstellen, sondern auch detaillierte Information über den historischen und aktuellen Zustand des arbeitsplatzübergreifenden Produktionsprozesses.
Die KI-Anwendungen von Incontext beherrschen die Semantik der Produktionsprozesse von Forcam Force und lernen, aus den „Small Data“ der Produktionslinie problematische Situationen automatisch zu erkennen.
Sie kombinieren selbstlernende Algorithmen mit einer globalen Einsicht in der Produktion und der Fähigkeit, lokal Anweisungen an den Arbeitsplätzen den Mitarbeiter rollenabhängig bereitzustellen.
„Beispiele für unsere Anwendungen: vorausschauende Instandhaltung der Arbeitsplätze, Erkennung von terminkritischen Aufträgen oder vorausschauende Gesamtanlageneffektivität“
ergänzt Olga Mordvinova.
Für Bitkom zählen zu den wichtigsten Vorteilen von KI in der Industrie neben der genannten Möglichkeit der vorausschauenden Wartung eine Steigerung der Produktivität sowie die Optimierung von Produktions- und Fertigungsprozessen.
„KI ist eine epochale Technologie, die die Weltwirtschaft und gerade auch die Industrie revolutionieren wird“
erklärt Achim Berg.
Auf was sollte ein SAP-Bestandskunde achten, wenn IIoT auf seiner Aufgabenliste steht? Oliver Hoffmann:
„Der SAP-Bestandskunde sollte sich alle Anbieter von IIoT-Plattform-Lösungen für den Shopfloor am Markt anschauen, sie vergleichen und eine qualitative Benchmark machen.“
Transparenz gibt es durch umfassende Konnektivität für Shopfloor und Topfloor, also die Integration von bestehenden heterogenen Maschinenparks und auch die Vernetzung mit der Unternehmensplanung.
„Produktivität gibt es durch einfache, schlüsselfertig integrierte Lösungen, weil sich danach entscheidet, wie schnell ich messbare Ergebnisse erzielen kann“
definiert Hoffmann. Bei Forcam gibt es schlüsselfertig vorinstalliert die wichtigsten MES-Apps dazu.
„Und letztendlich erhalte ich Flexibilität durch webtechnologische Offenheit“, weiß Hoffmann aus zahlreichen erfolgreichen Projekten. „Also offene Web-Schnittstellen, mit denen ich jedwede gewünschte vorhandene oder neue Lösung integrieren kann.“
Warum ist das Forcam-IIoT-Angebot für SAP-Bestandskunden besonders passend?
„Wie Oliver schon ausgeführt hat: weil wir Transparenz durch umfassende Konnektivität auf Shopfloor und Topfloor bieten; weil wir schnelle Produktivitätssteigerung durch einfache, schlüsselfertig integrierte Lösungen bieten; weil unsere Lösung größtmögliche Flexibilität durch webtechnologische Offenheit bietet“
ergänzt Co-CEO Rösinger, die einen Punkt noch einmal hervorhebt:
„Das einheitliche Datenmodell von der Fertigung bis zu den Finanzen. Erst präzise Daten aus dem Shopfloor ermöglichen auf dem Topfloor eine präzise Stückkostenrechnung und -planung.
Das bestätigen uns Controlling-Vertreter unserer Kunden. Echtzeit-Steuerung der Stückkosten durch Echtzeit-Daten aus der Fabrik. Es geht darum, Controlling und Mengenwerte zusammenzubringen. Eine neue Transparenz und damit die Beseitigung von Diskrepanzen in der Planung hat enorme Vorteile für ein nachhaltiges Cashflow-Management.“
Forcam hat eine strategische Partnerschaft mit Accenture: Was sind die Gründe und die Vorteile für einen SAP-Bestandskunden?
„Fertigende Unternehmen haben meist sehr ähnliche Herausforderungen, auch wenn sich die Lösungen dann sehr individuell darstellen“
erkennt Oliver Hoffmann. Kernthemen sind: keinen einheitlichen Blick auf die Fertigung, keine einheitlichen Informationen und Unternehmen können nicht werksübergreifend voneinander lernen; sie arbeiten mit funktionalen IT-Silos; eine lückenhafte Shop- und Top-floor-Integration verursacht Fehler und Verzögerungen; Ressourcen können weder global gemessen noch koordiniert oder geplant werden.
„All diese Themen adressieren wir im Industrial IoT Innovation Center von Accenture in Garching bei München, wo wir ein Ökosystempartner sind. Wir zielen dort auf gemeinsames strategisches Design-Thinking mit Kunden ebenso wie auf das Demonstrieren von konkreten technologischen Lösungen“
erklärt Forcam-Co-CEO Hoffmann.
„Von Accenture erhält der SAP-Bestandskunde die Beratung zu Strategien, Architekturen, die Integration von Systemen und Supply-Chains sowie Projektplanungen“
definiert Andrea Rösinger.
„Von Forcam erhält er die technologisch global skalierbare Cloud-Plattform-Lösung sowie unser Know-how in der IIoT-Prozessberatung. Die Vorteile von Garching sind dabei, dass wir dort in aller Ruhe in einer innovativen Atmosphäre ins Gespräch sowie zum Nachdenken und Kreieren kommen.
Das ist überaus wichtig, denn schließlich geht es um die digitalen Geschäftsprozesse der Zukunft – oder andersherum um die Zukunftsfähigkeit von Unternehmen.“
Eine weitere strategische Partnerschaft unterhält Forcam zu Microsoft, deren Manager Sebastian Seutter ist Industrie-4.0- Experte und Mitglieder im Forcam Innovation Board.
„Tatsächlich haben wir gerade in Deutschland sehr viele gemeinsame Kunden, für die eine enge Partnerschaft zwischen SAP und Microsoft von zentraler Bedeutung ist“
erklärt Seutter den Mehrwert für Forcam-Kunden und die SAP-Community.
„Die Mission unserer Partnerschaft ist es, Kunden zusammen mit unseren Partnern in ihrer digitalen Transformation und in allen Innovationen rund um integrierte Lösungen und Technologien von SAP und Microsoft bestmöglich zu unterstützen.
Die Partnerschaft zwischen Forcam und Microsoft schafft für unsere Kunden gerade den Mehrwert, ihre Produktion und die zugrunde liegenden Technologien einer intelligenten Fertigung digital neu zu gestalten, zu optimieren und umfassend zu integrieren. Dies führt zu Verbesserungen in der Produktion.“
Forcam-Co-CEO Rösinger präzisiert im E-3 Gespräch:
„Microsoft ist mit Azure der weltweit größte Cloud-Infrastrukturanbieter. Das heißt, der Skalierbarkeit sind quasi keine Grenzen gesetzt. Forcam trägt aufgrund seiner Historie das SAP-Gen in sich, SAP hat eine der führenden ERP-Lösungen weltweit. Mit Microsoft als Partner können wir gemeinsam wiederum besonders gut Schnittstellenthemen weltweit agierender Unternehmen lösen.“
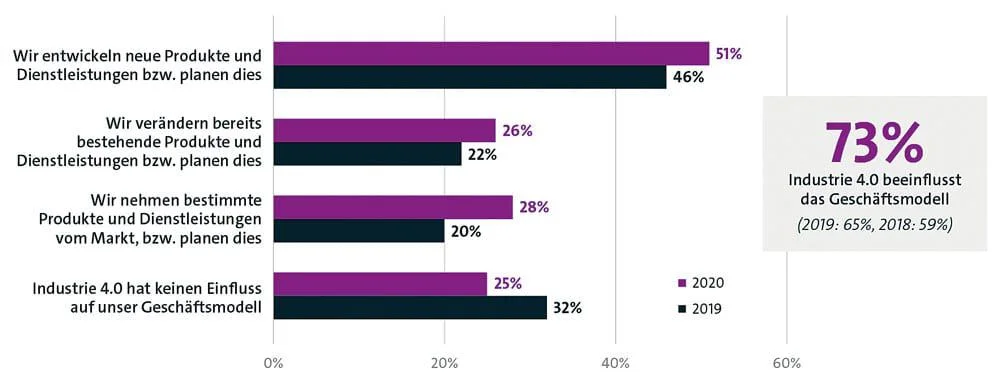
Momentan gibt es einen deutlichen Trend, die SAP-Systeme auf Microsoft Azure zu customizen: Wäre eine komplette Fabrik plus Verwaltung aus Azure somit denkbar?
„Eine Fabrik auf Azure ist heute tatsächlich noch eine Vision“
meint Sebastian Seutter gegenüber dem E-3 Magazin.
„Allerdings bringen wir bereits heute mit der Microsoft Azure Cloud alle grundlegenden Technologien mit, um diese Vision zu realisieren.“
Zunächst bestehen alle Voraussetzungen für die nötige Integration aller Systeme und Technologien auch über die SAP Cloud Platform (SCP), die ebenfalls auf Microsoft Azure verfügbar ist. Dann kommt das SAP-Credo „keep the core clean“ hier voll zum Tragen.
So sind über die SCP Anpassungen des SAP-Kerns einfach dort auf Azure zu verlagern, wo Innovationen gewünscht und schnell zu realisieren sind.
„Abschließend bringen wir durch unsere Partner und deren Kernkompetenzen alle Ansatzpunkte mit, um Architekturen und SaaS-Lösungen mit und auf Azure zu entwickeln. Damit lassen sich in unserer Cloud alle gewünschten Funktionen dieser Fabrik auf Azure einfach automatisieren, integrieren und erweitern“
weiß Seutter auch aus seiner beruflichen Praxis.
„Azure bietet unter anderem einen kompletten IoT-Hub. Enthalten sind dort Tools, die die Integration von Edge-Komponenten ermöglichen“
ergänzt Andrea Rösinger.
SAP selbst versucht sich bei der digitalen Transformation der Industrie mit Produkten wie SAP ME und dem Framework Leonardo: Wie ist die Position von Forcam gegenüber diesen SAP-Angeboten?
„Unser Lösungskonzept als Plattformanbieter ist umfassend und sieht vor, dass wir jedwede von Unternehmen benötigte Lösung integrieren oder zumindest zügig dafür sorgen können, dass sie leichtgängig integriert werden kann“
betont Co-CEO Rösinger im E-3 Gespräch.
„Unser Anspruch der Offenheit ist dabei umfänglich. Zudem bieten wir die Forcam-IIoT-Plattform-Lösung auch als White- Label-Produkt an. Und da die führenden Köpfe unseres Hauses selbst von SAP kommen, integriert unsere Lösung entsprechend SAP-Angebote wie SAP ME, SAP EWM und andere sehr leichtgängig. Es gilt: Wir schützen Investitionen in IT wie SAP und wir ermöglichen gleichzeitig Innovationen.“
