Die Fünf-Tage-Fabrik
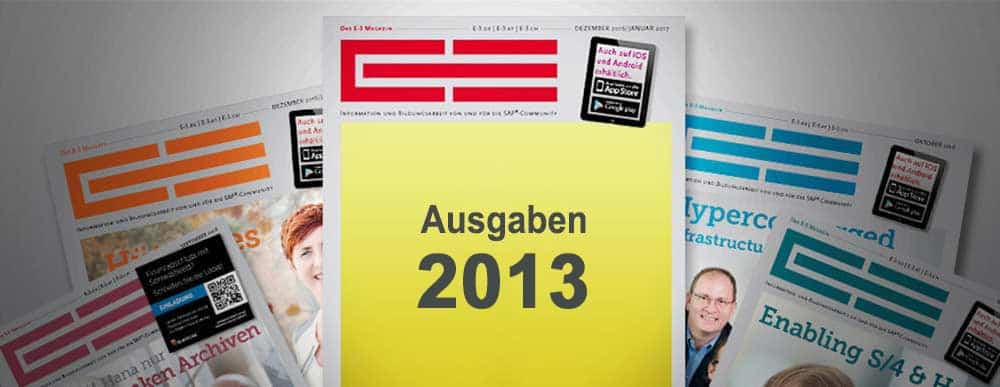
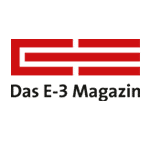
Mit dem Neubau der Budapester Fabrik im Jahr 2010 forderte die Geschäftsleitung des Herstellers von Brems- und On-Board-Systemen für Schienenfahrzeuge die Einführung der Fünf-Tage-Fabrik.
Bei der konkreten Umsetzung wurden die Arbeitsbereiche in der Produktion sowie die physische Materialversorgung nach modernsten Erkenntnissen komplett neu gestaltet. Auch die Abläufe für die Planung der Aufträge konnte Knorr-Bremse mithilfe einer speziell entwickelten IT-Lösung grundlegend verbessern.
Gesucht wurde eine integrierte Lösung, mit der die Ziele der Fünf-Tage-Fabrik und des geplanten Heijunka-Prozesses erreicht werden sollten. Es befand sich bereits SAP ERP im Einsatz und so galt es nun, dieses an die speziellen Herausforderungen in Budapest anzupassen.
Wurde in der alten Fabrik noch in einer nach dem Werkstattprinzip organisierten Fertigung an sechs Tagen in der Woche produziert, so reduzierte Knorr-Bremse Engpässe unter anderem durch Investitionen in eine Galvanik- und Lackierstraße, durch Wertstromanalysen und eine enge Verzahnung der Supply Chain mit dem Produktionssystem. Einen weiteren Schritt in Richtung eines Lean-Manufacturing-Ansatzes war die Umstellung des Fertigungsprinzips auf eine Zellenfertigung.
Lösungen dieser Art gelten im mit hohen Stückzahlen betriebenen Automotivesektor als alltäglich. In der Schienenfahrzeugindustrie, deren Produktion tendenziell auf geringe Stückzahlen oder Einzelfertigung ausgerichtet ist, stellt dieses Konzept jedoch ein absolutes Novum dar.
Das wichtigste Element des Fünf-Tage-Prinzips ist die drastische Herabsetzung der Durchlaufzeiten der internen Produktion. Darauf wurden auch die Produktions- und Arbeitsorganisationsabläufe ausgerichtet.
Knorr-Bremse Budapest betrat damals Neuland. Früher rechnete man beispielsweise bei der Produktion einer Klotzbremseinheit von der Bereitstellung des Rohmaterials bis zu Endmontage und Test mit einer Zeitspanne von 15 bis 25 Arbeitstagen.
In der Fünf-Tage-Fabrik muss die gesamte Produktion in fünf Arbeitstagen realisiert werden, was etwa 20 bis 25 Prozent der früher veranschlagten Zeit ausmacht. Parallel damit wird auch die Menge der im Prozess gebundenen Materialien und damit der Bestandswerte auf ein Viertel der ursprünglichen Menge herabgesetzt.
Die Änderung auf den neuen Produktionsablauf bietet Vorteile: Die Abwicklung von Kundenaufträgen funktioniert flexibler und zuverlässiger, Änderungen können schneller umgesetzt werden, Kapazitäten werden optimal genutzt, außerdem wurde die Effizienz der Versorgungskette verbessert.
Durch den Einsatz moderner Entwicklungstechniken erhalten Kunden Produkte, die den höchsten Qualitätsstandards genügen.
Der Lean-Manufacturing-Ansatz
Wie aber funktioniert die Fünf-Tage-Fabrik im Detail? Wichtig ist, dass die Produktion vorab abgestimmte Durchlaufzeiten kapazitiv reserviert und möglichst bereits am ersten Tag nach Freigabe mit der mechanischen Bearbeitung startet.
Die Zuverlässigkeit und Belastbarkeit des Systems werden in hohem Maße von der Lieferfähigkeit des Lieferanten beeinflusst, deshalb muss auf die Zuverlässigkeit des externen Versorgungsnetzes großer Wert gelegt werden.
Jedes zu beschichtende Werkstück muss am Ende der Produktions- und Einkaufsschritte, jedoch innerhalb der vorgegebenen Zeitgrenzen (am dritten Tag) in das Oberflächenbehandlungs- und Beschichtungszentrum gelangen, welches mit einer Durchlaufzeit von etwa einem Tag (vierter Tag) alle beschichteten Teile an die Montage weitergibt.
Gleichzeitig müssen auch die zur Montage erforderlichen Teile eintreffen, schließlich ist eine absolut zuverlässige Materialversorgung in konstant guter Qualität unabdingbar.
Der Ablauf (fünfter Tag) wird mit der Endmontage und der Funktionsprüfung abgeschlossen. Das Produkt steht somit nach nur fünf Tagen zur Ablieferung an den Endverbraucher bereit.
Ausgangssituation
Die Prozesse und Systemumsetzung im alten Budapester Werk orientierten sich an der klassischen MRP-Planung. Hier wurden ausgehend von den Primärbedarfen über den MRP-Lauf die Stücklisten aufgelöst, Bedarfe geplant und Bestellvorschläge (Planaufträge und Bestellanforderungen/Lieferplaneinteilungen) generiert.
Es wurde versucht, meist in großen Losen zu fertigen. Dabei orientierte sich die mechanische Fertigung überwiegend an den Terminvorgaben aus dem MRP und weniger am geplanten Montageprogramm.
Die Kehrseite der Medaille war unter anderem, dass zu viel zu früh produziert wurde, dadurch entstand eine Überschussproduktion. Große Losmengen führten in der Folge zu Kapazitätsengpässen und reduzierter Flexibilität in der Fertigung; das fehlende Beziehungswissen zwischen Komponentenfertigung und Endmontage resultierte in einer Überproduktion auf Komponentenebene; unerwartet hohe Bedarfe in bestimmten Zeiträumen führten zu kapazitiver Überlast beim Lieferanten und damit zu fehlender Komponentenverfügbarkeit. Ebenso war der Aufwand bei Kapazitätsglättung, in Steuerung und Terminverfolgung höher.
Realisierung
Um die Ziele der Fünf-Tage-Fabrik zu erreichen, war es notwendig, einerseits Systemeinstellungen wie Losgrößenverfahren zu ändern und andererseits die SAP Tools zur Produktionsplanung und -steuerung an die Ziele der Fünf-Tage-Fabrik und den geplanten Heijunka-Prozess anzupassen.
Für die exakte Planung und Steuerung der Montage und der mechanischen Fertigung wurde die grafische Plantafel eingesetzt. Im ersten Schritt wurden dazu in den einzelnen Fertigungslinien in der Montage die Engpässe analysiert und in den Arbeitsplänen mit realistischen Zeiten versehen.
So ermöglichte Consilio eine finite Planung der Linien. Mithilfe der Plantafel können nun die einzelnen Montagelinien unter Berücksichtigung der tatsächlichen Kapazitätssituation optimal belegt werden. Ausgehend von den eingeplanten Aufträgen werden im Anschluss über den MRP die Bedarfe geplant und Bestellvorschläge (Planaufträge) generiert.
Um sicherzustellen, dass in der mechanischen Fertigung nur das gefertigt wird, was auch in der Montage an den Folgetagen montiert wird, können nur Planaufträge in Fertigungsaufträge umgewandelt werden, deren Bedarfsverursacher auch tatsächlich eingeplant sind, das heißt, tatsächlich in der Montage ein Fertigungstermin geplant ist. Die Einplanung der mechanischen Fertigung erfolgt ebenfalls über die Plantafel, um eine realistische Belegung der Maschinen zu erreichen.
Ergebnis
Mit der Umsetzung von Heijunka im Rahmen der Fünf-Tage-Fabrik auf Basis von SAP ERP ECC 6.0 ist es gelungen, einerseits die Ziele wie Reduzierung der Durchlaufzeit und Bestände, Erhöhung der Flexibilität und Lieferfähigkeit und andererseits die Transparenz für alle am Prozess beteiligten Fachbereiche wie Einkauf, Disposition, Planung, Fertigung und Vertrieb zu erhöhen, da die Heijunka-Planung nicht nur auf einem Board in der Fertigung dargestellt wird, sondern im System für jeden abrufbar ist.
Die Auswirkungen von Ein- und Umplanungen (Terminänderungen) werden sofort an alle weitergeleitet und sind damit transparent. Die Umsetzung von Heijunka mit SAP Tools hilft auch, schnell und flexibel auf Bedarfsveränderungen zu reagieren, und dies trotz der meist geringeren Stückzahlen als in der Automobilindustrie.
So werden die Kapazitäten schon bei Kundenauftragseingang berücksichtigt, es herrschen optimale Lagerbestände über alle Dispositionsstufen, der Produktionsfluss findet ohne Verschwendung statt und zudem stehen hilfreiche Tools für die Auftragsreihenfolgeplanung zur Verfügung.
„Mit den in Budapest entwickelten Konzepten ist es uns gelungen, zwei Dinge miteinander zu vereinen: eine hohe Variantenvielfalt mit niedrigen Stückzahlen einerseits und sehr kurze Durchlaufzeiten mit hoher Flexibilität andererseits.
Wir haben dadurch einen messbaren Mehrwert für unsere Kunden geschaffen und darauf sind wir sehr stolz. Eine völlig neue Form der Zusammenarbeit mit unseren Lieferanten sowie eine wertstromorientierte Struktur der Fertigung sind ganz entscheidende Faktoren für den großen Erfolg der Fünf-Tage-Fabrik“
sagt Albrecht Köhler, Mitglied der Geschäftsleitung von Knorr-Bremse Systeme für Schienenfahrzeuge.