Schlüsselanforderung 4.0
![[shutterstock: 285280127, Hamik]](https://e3mag.com/wp-content/uploads/2021/03/infrastruktur-mag2103.jpg)
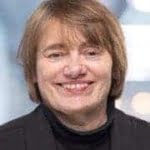
Bei der Erneuerung der Infrastruktur sollte der Fokus auf Wertschöpfung vor Ort liegen, bevor global skaliert wird. Denn, so die McKinsey-Studie „Industry 4.0 – Capturing Value at Scale in Discrete Manufacturing“: Viele Anwendungsfälle liefern ihren Wert über die Infrastruktur vor Ort.
Allerdings stellt schon die Anforderung „Infrastruktur erneuern mit Fokus auf Wertschöpfung vor Ort“ viele Unternehmen vor eine zentrale Herausforderung. So verlangt die digitale Transformation der Produktion nach einer integrierten IT/OT-Architektur – zum Beispiel die Industrie 4.0 Solution Blueprint von SAP. Gleichzeitig sind die Voraussetzungen für Maschinenkonnektivität und Datenerfassung in jeder Fertigung unterschiedlich.
Der Grund ist, dass üblicherweise Maschinen, Anlagen, Steuerungen und Sensoren unterschiedlichen Alters sowie unterschiedlicher Hersteller zum Einsatz kommen, berichtet die weitere McKinsey-Studie „Industrielles IoT“. Daher sind spezielle Lösungen erforderlich, die sorgfältig zu Clustern zusammengeführt werden müssen. Weiter heißt es: Ohne Konnektivität geht im digitalen Raum nichts.
Brownfield anbinden
Weil in den allermeisten Fabriken rund um den Globus Unternehmen mit älteren Maschinen oder gar einem komplett alten Maschinenbestand arbeiten, dem sogenannten Brownfield, lautet die eine zentrale Frage: Wie bindet man sowohl moderne und neue als auch vorhandene ältere Maschinen digital an? Die Antwort darauf treibt viele Firmen um.
In Umfragen gibt eine Mehrheit der Unternehmen an, dass sie rund 30 Prozent ihres bestehenden Anlagenbestands im Zuge einer digitalen Transformation auswechseln müssten. Das aber hieße gerade für große Fertigungsunternehmen, dass sie Investitionen in Maschinen und Anlagen in Milliardenhöhe abzuschreiben hätten. Das grenzte an betriebswirtschaftlichen Irrsinn.
Strategisch aber gilt es, getätigte Investitionen zu schützen und benötigte Innovationen zu ermöglichen. Daher muss schon für den entscheidenden ersten Schritt der digitalen Reise eine passende und möglichst einfach zu implementierende Lösung gefunden werden. Nur mit einer umfassenden Brownfield-Konnektivität selbst für Maschinen, die lange vor dem digitalen Zeitalter ausgeliefert wurden, können die weiteren Stationen der digitalen Reise folgen: Visibilität, Transparenz, Vorhersagbarkeit und Anpassungsfähigkeit, wie es die deutsche Akademie der Technikwissenschaften (Acatech) definiert.
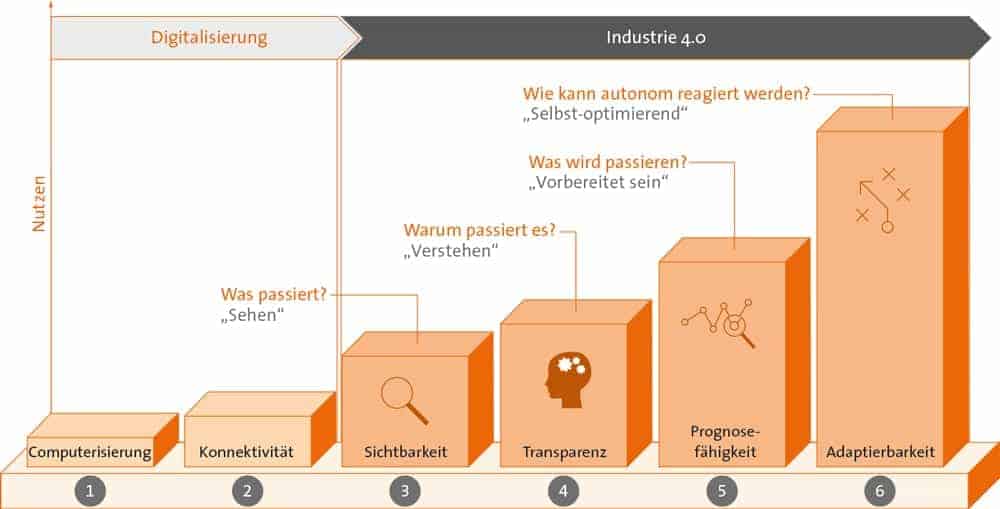
Konnektivität muss von Anfang in einer ganzheitlichen IT/OT-Architektur wie das Herz- Kreislaufsystem für den Datenfluss mitgedacht und eingebunden werden. Forcam und SAP bieten eine solche ganzheitliche Architektur in der DMC (Digital Manufacturing Cloud). Mit Forcam Force Edge können Brownfield-Anlagen angebunden und umfassend in Level 0 bis 2 im SAP Industrie 4.0 Blueprint abgebildet werden.
Die Edge-Lösung bietet Ausfallsicherheit und überträgt gleichzeitig alle relevanten Daten in weiterführende Systeme wie DMC oder SAP ME/MII, wo die gesammelten und normierten Maschinendaten nahtlos an alle relevanten Folgeprozesse integriert werden können. Dazu Mani Pirouz, Global Head of Partner Innovation bei SAP: „Mit Forcam Force Edge können Kunden ihr Brownfield mit SAP-Lösungen verbinden und in SAP-Prozesse integrieren, sodass sie die Vorteile von digitalen Zwillingen voll ausschöpfen können.“
Digitaler Zwilling
Die Fabrik der Zukunft arbeitet mit einem präzisen und einheitlichen Echtzeit-Datenmodell in Produktion und Planung. Für einen solchen digitalen Zwilling der Produktion ist Konnektivität die Basis. Der digitale Zwilling der Produktion entsteht, wenn die Shop-floor-Daten zu Informationen verdichtet werden, also die eingesammelten Maschinensignale in eine einheitliche digitale Sprache normiert und semantisch zugeordnet werden.
Big Data werden zu Smart Data. Erst dann können alle IT-Systeme in Shop–floor und Topfloor mit einer einzigen Quelle der Wahrheit arbeiten, der „Single Source of Truth“. Auch diese Normierung und semantische Zuordnung übernimmt die Lösung Force Edge. Jedes Signal erhält die richtige Bedeutung.
Ein Exkurs in den Shopfloor zeigt: Die Heterogenität der Maschinenparks in fertigenden Unternehmen aller Branchen ist groß. Doch lassen sich drei grundsätzliche Ansätze der digitalen Anbindung unterscheiden.Erstens, einfache und/oder ältere Maschinen haben keine netzwerkfähige Steuerung. Ihre internetfähige Anbindung erfolgt über den Direktabgriff von Signalen und Zuständen direkt aus der Maschine mittels eines Wandlers, einer I/O-Box. Übliche Signale sind: Maschine ein oder aus, Produktion oder Stillstand, Menge und Störung.
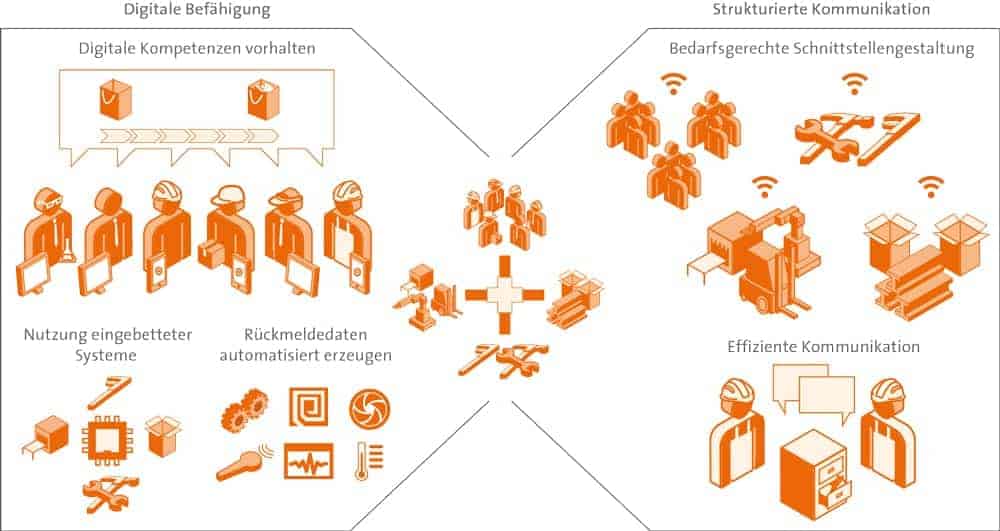
Zweitens, neuere Maschinen besitzen eine netzwerkfähige Steuerung. Bei ihnen werden die Signale über Plug-ins aus der Steuerung ausgelesen. Diese Plug-ins stehen in Force Egde für die gängigsten Steuerungstypen zur Verfügung.
Drittens, moderne Maschinen sowie komplette Bearbeitungszentren arbeiten mit den Kommunikationsprotokollen wie OPC, MTConnect oder MQTT. Diese Anlagen erzeugen in der Regel ein standardisiertes Datenpaket, welches sich zur Weiterverarbeitung eignet, ohne eine direkte Signalumwandlung aus der Steuerung vorschalten zu müssen. Die Herausforderung besteht in den inhomogenen Datenstrukturen der Datenpakete und den unterschiedlichen Maschinentypen.
Edge- und Cloud-Infrastrukturen
Zurück auf die strategische Ebene: Unternehmen benötigen für die Ära des IIoT eine Lösung, die gewünschte Innovationen ermöglicht und getätigte Investitionen schützt. Sie brauchen flexible und integrative IT-Architekturen, welche die Transformation in die globale Welt digitaler Liefer- und Serviceketten ermöglichen. Diese Anforderung lässt sich technologisch nur über hybride Lösungen aus Edge- und Cloud-Infrastrukturen digital abbilden.
Das gilt insbesondere für Fertigungsnetzwerke, die in Echtzeit international und multimandantenfähig arbeiten. Hybriden Edge- und Cloud-Infrastrukturen gehört daher in der Industrie die Zukunft. Eine solche flexible Edge- und Cloud-Lösung für Shopfloor-Konnektivität und Kollaboration in weiterführenden Systemen bieten Forcam und SAP.
Acatech-Studie: Industrie 4.0 Maturity Index
Der Begriff Industrie 4.0 wurde 2011 geprägt und beschreibt seitdem die weitreichende Integration von Informations- und Kommunikationstechnologien im industriellen Umfeld. Der Begriff wird seitdem jedoch teilweise missinterpretiert und fokussiert sich zu häufig lediglich auf technologische Elemente. Unternehmen müssen jedoch auch deren organisatorische Strukturen und die Kultur transformieren.
Ziel ist es, ein lernendes, agiles Unternehmen zu werden, das sich einer ständig ändernden Umwelt flexibel anpassen kann. Der Acatech Industrie 4.0 Maturity Index gibt den Unternehmen ein Werkzeug in die Hand, um die Transformation in ein lernendes, agiles Unternehmen zu unterstützen. Der Index beschreibt sechs Entwicklungsstufen für die vier Strukturelemente eines jeden Unternehmens.
Jede Stufe ermöglicht dem Unternehmen einen zusätzlichen Nutzen. Der Index kann dazu benutzt werden, eine individuelle digitale Roadmap zu entwickeln, um Industrie 4.0 in allen Unternehmensbereichen einzuführen. Aufbauend auf den Erkenntnissen und dem entwickelten Modell können zukünftig Werkzeuge zur konkreten Ausgestaltung der Transformation in Unternehmen entwickelt werden.
Hierbei empfiehlt sich, ein spezifisches Vorgehen für einzelne Industriedomänen zu entwickeln, um möglichst konkrete Handlungsempfehlungen geben zu können und den Unterschieden in den einzelnen Industrien Rechnung zu tragen. Hierzu sind die Eigenheiten verschiedener Industriezweige und Geschäftsbeziehungen im Rahmen weiterer Validierungen zu untersuchen.
Das Modell lebt, ganz im Sinne des kontinuierlichen Lernens, von zusätzlichen Informationen. Diese ergeben sich nicht nur aus Validierung, sondern auch durch den Austausch mit interessierten Industrie- und Forschungspartnern.
Quelle: Industrie 4.0 Maturity Index. Die digitale Transformation von Unternehmen gestalten. Eine Acatech-Studie von Günther Schuh, Reiner Anderl, Jürgen Gausemeier, Michael Hompel, Wolfgang Wahlster (Hrsg.). Download: www.acatech.de/publikationen
