ERP & S/4 für Serienfertiger
![[shutterstock:469390151, Solcan Sergiu]](https://e3mag.com/wp-content/uploads/2017/02/shutterstock_469390151-Kopie.jpg)
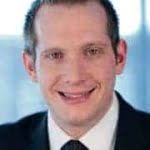
Hersteller innovativer Produkte im Maschinen- und Komponentenbau folgen marktgetriebenen Trends wie Standardisierung, Modularisierung, Plattformstrategien und „Downsizing“.
Die Produktionsprozesse wandeln sich hin zu Fließfertigung, synchroner Produktion und dezentralen Arbeitsformen im internationalen Umfeld. Gleichzeitig unterliegen die Produkte aber häufig einer variantenreichen oder kundenauftragsbezogenen Fertigung:
Typisch sind komplexe Fertigungsprozesse mit umfangreichen Arbeitsplänen und oftmals langen Durchlaufzeiten. Das erschwert die Planung.
Was kann ein ERP-System leisten?
Enterprise-Resource-Planning-Systeme (ERP) arbeiten mit dem klassischen Ansatz des Material Resource Planning (MRP) aus den 70er- und 80er-Jahren des vorigen Jahrhunderts.
Der Kern dieser Planung ist die Sukzessivplanung, bei der einzelne Teilbereiche schrittweise und zeitlich nacheinander geplant werden. Einflüsse aus späteren Planungsschritten werden dabei nicht berücksichtigt oder beruhen nur auf groben Schätzungen.
Im Rahmen der Programmplanung werden Kundenbedarfe und Planprimärbedarfe zum Produktionsprogramm zusammengestellt. Planprimärbedarfe können hierbei z. B. mittels einer Prognose aus Vergangenheitsbedarfen ermittelt werden.
Im Rahmen des MRP-Laufs im ERP findet dann die Mengenplanung statt – unter Berücksichtigung von Losgrößen und Lagerbeständen. Im Rahmen des MRP werden Elemente für Eigenfertigung und Fremdbeschaffung angelegt.
Bei Eigenfertigung kann die Durchlaufterminierung über Vorgabewerte in Arbeitsplänen vollzogen werden. Die Komponentenverfügbarkeit wird mehrstufig für Baugruppen und fremdbeschaffte Komponenten gegen Bestand und vorhandene Zugangselemente geprüft.
Planung im ERP nicht ausreichend
Im Ergebnis der MRP-Planung werden jedoch häufig unrealistische, nicht machbare Pläne erzeugt. Die Hauptgründe hierfür sind die Rückwärtsterminierung und die fehlende Kapazitätsprüfung bei der Durchlaufterminierung.
So können bereits während des MRP-Planungslaufs Verfügbarkeiten verletzt werden: Ausgehend von einem vorgegebenen Fertigstellungstermin wird in der Regel mit Rückwärtsterminierung gearbeitet.
In der Folge wird bei kurzfristigen Bedarfen dann häufig die (längere) Wiederbeschaffungszeit von Komponenten nicht eingehalten. Jedoch versuchen die Produktionsaufträge weiterhin den Bedarfstermin zu decken, obwohl benötigte Komponenten zur Fertigung nicht mehr rechtzeitig beschafft werden können.
Der Disponent muss diese Situation dann im ERP manuell korrigieren.
Die Durchlaufterminierung schließt nicht die Prüfung gegen Ressourcen mit ein. Erst im Rahmen der Kapazitätsplanung wird gegen die tatsächliche Auslastung der Maschinen geprüft.
Zeitgleich zur Maschinenverfügbarkeit muss der Planer sicherstellen, dass alle Komponenten zum benötigten Vorgang verfügbar sind, da es sonst zu teuren Fehlteilen in der Produktion kommt.
Ist keine ausreichende Kapazität an den Arbeitsplätzen vorhanden, kann nur noch manuell auf alternative Arbeitsplätze umgeplant werden. Hierbei muss der Planer jedoch die Reihenfolgen der Arbeitsvorgänge zur rüstoptimalen Einplanung beachten – zu hohe Rüstzeiten führen sonst zu langen Durchlaufzeiten.
Aufgrund der komplexen Kriterien ist die Einplanung mit sehr hohem Aufwand verbunden.
Dieser hohe zeitliche und personelle Aufwand zur Sicherstellung der Liefertermine sowie die mangelnde Effizienz in der Planung entwickeln sich zu einer Hürde im zunehmenden globalen Wettbewerb.
Um erfolgreich zu bleiben und ihre Position hier zu behaupten, müssen Maschinen- und Komponentenbauer ihre Geschäftsprozesse schneller und agiler gestalten und reibungslos miteinander verzahnen. Es gilt, Prozesse zu straffen, Durchlaufzeiten zu verkürzen und Produktionsressourcen optimal zu belasten.
Überlastungen müssen frühzeitig erkannt werden, um rechtzeitig Gegenmaßnahmen zu ergreifen und somit schneller und effizienter im globalen logistischen Netzwerk agieren zu können als die Mitbewerber.
Der Planungsprozess
Entsprechend muss die Planung an diesen Herausforderungen ausgerichtet werden. Die Erzeugung machbarer Produktionspläne unter Berücksichtigung verfügbarer Kapazitäten, Materialien und anderer Ressourcen wie Fertigungshilfsmittel steht dabei im Vordergrund.
Aufträge sollen so gebildet werden, dass Materialverfügbarkeit und Kapazitätsrestriktionen gleichzeitig berücksichtigt werden, um Ressourcenüberlastungen oder eine Einplanung von Fertigungsaufträgen ohne Materialverfügbarkeit zu vermeiden.
Zeitintensive und aufwändige Ermittlung von Termin- oder Kapazitätsverletzung, wie weiter oben beschrieben, gilt es zu vermeiden.
Oberstes Ziel ist es, dass einmal dem Kunden bestätigte Termine auch eingehalten werden. Bei Einplanung von kurzfristig auftretenden Aufträgen und Ersatzteilaufträgen muss die Kannibalisierung von bereits bestätigten Kundenaufträgen verhindert werden.
Dazu sollte von vornherein die automatische Einplanung von Aufträgen auf alternativen Anlagen und Maschinen gegeben sein. Alle notwendigen Komponenten sollen rechtzeitig zur Verfügung stehen, zu hohe Lagerbestände jedoch vermieden werden.
Angepasste Funktionen
SAP bietet seit Kurzem mit der Lösung SAP PPDS on ERP oder auch S/4 Hana integrierte und innovative Lösungen zur Produktions- und Feinplanung für das Supply Chain Management.
Feinplanungsfunktionalitäten, welche Kunden bisher nur in Verbindung mit einer eigenen SCM-Installation anwenden konnten, stehen nun im ERP zur Verfügung.
Bewährte ERP-Prozesse können somit in Verbindung mit Feinplanungsfunktionalitäten abgebildet und optimiert werden.
Diese Lösung ermöglicht eine genaue, mehrstufige Planung von Bedarfen und begrenzten Kapazitäten. Sie erzeugt zukünftig im SAP-ERP-System machbare und optimierte Produktionspläne auf Grundlage von Kapazitäts-, Fertigungshilfsmittel- und Materialverfügbarkeiten.
Bei Kleinserienfertigern im Maschinen- und Komponentenbau sind einige Besonderheiten zu beachten, auf die es Planungstools anzupassen gilt.
Charakteristisch sind hier variantenreiche (Klein-)Serienproduktionen bzw. ein Portfolio ähnlicher Erzeugnisse desselben Grundtyps mit einem gleichen Fertigungsablauf für alle Varianten, außerdem die Bildung von Fertigungslosen.
Typischerweise spielen Umrüstzeiten und -kosten eine wichtige Rolle.
Consilio: virdefinierte Funktionen
Mit speziellen Templates der Consilio IT-Solutions GmbH für diesen Anwendungsbereich wird daher das Ziel verfolgt, Maschinen- und Komponentenherstellern die Einführung des neuen Planungstools durch vordefinierte Funktionen zu erleichtern.
Dazu gehören Einstellungen zu Stammdaten im SAP ERP und S/4 Hana, Integrationsmodelle, Benutzer- und Planungsprofile, Customizing für den Produktionsplanungslauf sowie Einstellungen der Feinplanungstafel zur Auswertung von Ressourcenauslastungen.
Ebenfalls vordefiniert sind die grafische Auswertung von mehrstufigen Auftragsstrukturen sowie ein Fehlteilmonitor über alle Dispositionsstufen hinweg mit konsistenten Ausnahmemeldungen.
Die Lösung umfasst mehrere angepasste Heuristiken: MRP, finite Bottom-up- und Top-down-Heuristik, Rückstandsauflösung und Fixierungsheuristik sowie Implementierungen zur funktionalen Erweiterung von SAP-Standard-Heuristiken.
Der vorkonfigurierte „MRP Live“ der Consilio-Lösung basiert auf der Hana-Technologie. Untertägige Läufe sorgen für eine rasante Deckungs- bzw. Terminsituation, entlang der gesamten Supply Chain.
Planer besitzen somit stets ein aktuelles Bild der Situation und können im Falle von Ausnahmemeldungen z. B. bei Terminverletzungen schnell reagieren.
Speziell auf die Disponenten und Fertigungsplaner ausgerichtete Fiori Apps unterstützen den Planer bei seiner Lösungs- und Entscheidungsfindung.
Unternehmen werden schließlich darin unterstützt, Ausnahmesituationen wie Terminverletzungen und Kapazitätsüberlasten frühzeitig zu erkennen und darauf zu reagieren.
Sowohl die Priorisierung und Umterminierung von Aufträgen als auch die Berücksichtigung und Reduzierung von Puffern in Aufträgen (Fertigungsaufträgen und Netzplänen) zur Vermeidung von Um- oder Neuplanungen bei geringen Termin- und Mengenabweichungen können aktiviert werden.
Ein Produktivitätsgewinn wird so nicht nur durch die maschinen- und anlagenabhängige Rüstzeitoptimierung, sondern auch durch die Einplanung von Aufträgen auf alternativen Anlagen und Maschinen ermöglicht.
Im Ergebnis wird ein machbarer und robuster Produktionsplan erzeugt, der sowohl Kapazitäts- und Materialverfügbarkeiten als auch technische Restriktionen und betriebswirtschaftliche Kriterien berücksichtigt.
Der rechtzeitige Start von Beschaffung und Produktion sowie die frühzeitige Benachrichtigung der Disponenten bei Ausnahmen sorgen für eine höhere Termintreue. Durch die zeitgerechte Einplanung können die Bestände über alle Dispositionsstufen hinweg gesenkt werden.
Optimierung der Anlagenauslastung, der Rüstzeiten sowie verkürzte Durchlaufzeiten erhöhen die Produktivität – und somit auch die Wettbewerbsfähigkeit.