ERP & S/4 for series producers
![[shutterstock:469390151, Solcan Sergiu]](https://e3mag.com/wp-content/uploads/2017/02/shutterstock_469390151-Kopie.jpg)
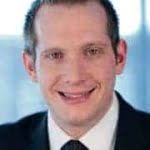
Manufacturers of innovative products in mechanical and component engineering follow market-driven trends such as standardization, modularization, platform strategies and "downsizing".
Production processes are changing towards flow manufacturing, synchronous production and decentralized forms of work in an international environment. At the same time, however, products are often subject to variant-rich or customer order-based manufacturing:
Complex manufacturing processes with extensive work plans and often long lead times are typical. This makes planning more difficult.
What can an ERP system do?
Enterprise Resource Planning (ERP) systems work with the classic approach of Material Resource Planning (MRP) from the 1970s and 1980s.
The core of this planning is successive planning, in which individual subareas are planned step by step and in chronological order. Influences from later planning steps are not taken into account or are only based on rough estimates.
In Demand Management, customer requirements and planned independent requirements are combined to form the demand program. Planned independent requirements can be determined, for example, by means of a forecast from past requirements.
Quantity planning then takes place as part of the MRP run in the ERP - taking lot sizes and inventory levels into account. Elements for in-house production and external procurement are created as part of the MRP.
For in-house production, lead time scheduling can be carried out using standard values in routings. Component availability is checked on several levels for assemblies and externally procured components against stock and existing receipt elements.
Planning in ERP not sufficient
However, as a result of MRP planning, unrealistic, unfeasible plans are often generated. The main reasons for this are backward scheduling and the lack of capacity checks in lead time scheduling.
In this way, availabilities can already be violated during the MRP planning run: Starting from a predefined completion date, backward scheduling is usually used.
As a result, the (longer) replenishment lead time for components is then frequently not met in the case of short-term requirements. However, the production orders continue to try to cover the requirement date, although required components for production can no longer be procured in time.
The dispatcher must then correct this situation manually in the ERP.
Lead time scheduling does not include the check against resources. It is only during capacity planning that the actual capacity utilization of the machines is checked.
At the same time as machine availability, the planner must ensure that all components are available for the required operation, otherwise expensive missing parts will occur in production.
If there is insufficient capacity at the workstations, the only option is to reschedule manually to alternative workstations. In this case, however, the planner must observe the sequences of the operations for setup-optimal scheduling - otherwise, excessive setup times will lead to long throughput times.
Due to the complex criteria, scheduling involves a great deal of effort.
This high expenditure of time and personnel to ensure delivery dates as well as the lack of efficiency in planning are developing into a hurdle in the increasing global competition.
To remain successful and maintain their position here, machine and component manufacturers must make their business processes faster and more agile and dovetail them smoothly. Processes need to be streamlined, lead times shortened and production resources optimally loaded.
Congestion must be detected at an early stage so that countermeasures can be taken in good time, enabling the company to act faster and more efficiently in the global logistics network than its competitors.
The planning process
Accordingly, planning must be aligned with these challenges. The generation of feasible production plans taking into account available capacities, materials and other resources such as production resources/tools is at the forefront.
Orders should be formed in such a way that material availability and capacity restrictions are taken into account at the same time in order to avoid resource overloads or dispatching production orders without material availability.
Time-consuming and costly determination of schedule or capacity violations, as described above, must be avoided.
The primary objective is to ensure that deadlines once confirmed to the customer are also met. When scheduling orders and spare parts orders that occur at short notice, the cannibalization of customer orders that have already been confirmed must be prevented.
To this end, automatic scheduling of orders on alternative systems and machines should be provided from the outset. All necessary components should be available on time, but excessive stock levels should be avoided.
Customized functions
SAP recently began offering integrated and innovative solutions for production and detailed planning for supply chain management with its SAP PPDS on ERP or S/4 Hana solution.
Detailed planning functionalities, which customers could previously only use in conjunction with their own SCM installation, are now available in the ERP.
Proven ERP processes can thus be mapped and optimized in conjunction with detailed planning functionalities.
This solution enables accurate, multi-level planning of requirements and limited capacities. In the future, it will generate feasible and optimized production plans in the SAP ERP system based on capacity, production resource/tool and material availabilities.
For small batch manufacturers in machine and component construction, there are a number of special features to consider, to which planning tools must be adapted.
Characteristic here are variant-rich (small) series productions or a portfolio of similar products of the same basic type with the same production sequence for all variants, as well as the formation of production lots.
Typically, changeover times and costs play an important role.
Consilio: virdefined functions
With special templates from Consilio IT-Solutions GmbH for this application area, the goal is therefore to make it easier for machine and component manufacturers to introduce the new planning tool through predefined functions.
This includes settings for master data in SAP ERP and S/4 Hana, integration models, user and planning profiles, customizing for the production planning run, and settings for the detailed planning board for evaluating resource utilization.
Also predefined are the graphical evaluation of multi-level order structures and a missing parts monitor across all MRP levels with consistent exception messages.
The solution includes several customized heuristics: MRP, finite bottom-up and top-down heuristics, backlog resolution and fixation heuristics, as well as implementations to functionally extend standard SAP heuristics.
The preconfigured "MRP Live" of the Consilio solution is based on Hana technology. Intraday runs ensure a rapid coverage or deadline situation, along the entire supply chain.
Planners thus always have an up-to-date picture of the situation and can react quickly in the event of exception reports, e.g. in the event of schedule violations.
Fiori apps specifically geared towards schedulers and production planners support planners in their solution and decision making.
Finally, companies are supported in recognizing and responding to exceptional situations such as schedule violations and capacity overloads at an early stage.
Both the prioritization and rescheduling of orders and the consideration and reduction of buffers in orders (production orders and networks) to avoid rescheduling or rescheduling in the event of minor deviations in dates and quantities can be activated.
A productivity gain is thus made possible not only by machine and plant-dependent setup time optimization, but also by scheduling orders on alternative plants and machines.
The result is a feasible and robust production plan that takes into account capacity and material availability as well as technical restrictions and business criteria.
The timely start of procurement and production as well as the early notification of the dispatchers in case of exceptions ensure a higher adherence to schedules. Timely scheduling allows inventories to be reduced across all scheduling levels.
Optimization of plant utilization, setup times and shortened throughput times increase productivity - and thus also competitiveness.