Ordered today - delivered tomorrow
![[shutterstock.com:380086414, Narong Jongsirikul]](https://e3mag.com/wp-content/uploads/2017/03/shutterstock_380086414_CMYK.jpg)
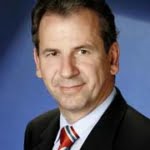
Viollier is the leading medical laboratory in Switzerland, with over 680 employees working at more than 20 locations. Its laboratory medicine is available to medical practices and clinics around the clock, 365 days a year.
In doing so, the company relies on high quality customer service throughout the country. Every day, a network of 80 drivers collects laboratory samples from doctors and clinics all over Switzerland, whether in the city or in the country, and transports them to one of Viollier's analytical laboratories.
In response to many customer requests, this service is flanked by v-shop, an online store system in whose range the company now stocks over 1,600 medical products.
This means that customer service not only picks up laboratory samples, but can also immediately supply the practices and hospitals with the items ordered via the store. Viollier's top maxim here is: "ordered today - delivered tomorrow".
Without a distribution warehouse in which individual processes are closely interlinked and can be handled efficiently, this high standard cannot be met.
"Due to the increase in the number of orders we deliver on behalf of our customers each year, we were reaching the limits of our capacity with our previous warehousing"
Martina Kiefer, ICT-SAP project manager at Viollier, describes the initial situation.
"Our warehouse staff were consistently subjected to high workloads and regularly had to work overtime to pick the order volume on time.
This was the trigger for setting up new warehouse structures at the headquarters in Allschwil, streamlining processes and establishing a modern warehousing system."
Martina Kiefer continues.
To this end, picking was to be largely paperless and multi-customer-capable with IT support in the future. Optimized routes and an intelligent pick & pack process should make it possible to pack the items in an order directly when they are picked.
Docking external warehousing to SAP
In a first step, Viollier wanted to overcome these challenges by connecting an external warehouse from a provider specializing in this area to the in-house SAP infrastructure via IDocs and interfaces.
"However, after six months, our support partner at the time was still unable to provide us with a business blueprint"
says Martina Kiefer.
"As a result, I re-advertised the project and, together with a colleague, came across the Mobisys GmbH website by chance."
Contact was then quickly established with Trimaster, an implementation partner based in Switzerland. The SAP experts then drew up a new offer, which quickly discarded the original idea and envisaged modernizing warehousing with the mobile data capture of the MSB Mobisys Solution Builder from the Walldorf-based SAP software solution partner Mobisys.
The SAP add-on is characterized by lean integration into the SAP ERP system, is user-friendly, and employees can record all logistics processes via handheld scanners while on the move.
In addition, the complete integration of the MSB into Viollier's SAP system eliminates the need for time-consuming maintenance of interfaces and the associated sources of errors from the outset, which also kept project costs within manageable limits.
The advantages of this lean, mobile logistics solution convinced Viollier. The go-ahead for the implementation project was given in July 2015. After only six months, the project team was able to go live with the mobile solution.
The days when warehouse employees had to print out their picking slips, process them by hand, and make awkward trips around the warehouse are now a thing of the past at Viollier.
With the use of the MSB Client, the flow of materials can be controlled more efficiently and warehouse employees can process all orders on time every day, even at peak times, within their regular working hours.
The employees can now quickly and easily post the goods receipt of the medical products directly in the SAP system with scanner support via the mobile MSB client and perform the storage in the chaotically organized delivery warehouse - this for up to four different deliveries at the same time.
Multi-customer picking is therefore possible without any problems with the 15 MSB clients in use. A special feature at Viollier is also a two-stage control function in goods receipt and storage: one employee checks the medical products for quality, quantity and best-before date and another employee checks this in a second step before storing the goods in the new container structure of the delivery warehouse.
These can be used to define a precise sequence as to which product must be retrieved first on the basis of its best-before date.
If a medical practice orders various medical devices via the v-shop website, the order in the SAP system triggers a sales order and the associated delivery. The v-shop employees decisively check the deliveries generated in SAP on a monitor specially developed by Trimaster for each item.
Only after this process has been completed are the deliveries released for picking and thus transferred to the mobile terminals. The complete time control and route management are of course observed by the monitor.
The MSB Client clearly shows employees open delivery items, which they can select, pick, and immediately pack using Pick & Pack. Only when all items for an order have been completed on the MSB Client can the goods issue be posted in the SAP system.
"In this way, we can pick the numerous individual items that our orders typically comprise quickly and without errors"
Martina Kiefer explains.
Finally, the responsible employee prints out the shipping documents and the orders are handed over to the courier service for speedy overnight delivery anywhere in Switzerland.
Order forms on demand
Viollier is not completely without paper, although the processes are now paperless. The reason for this is the so-called order forms that doctors and clinics need for their internal laboratory processing and can also order with the medical products.
Although the order forms are not inventory-managed and are individualized from practice to practice, processing with the MSB Client is the same as for medical devices. The order forms are printed via "printing on demand" only at the time of picking.
"Together with the specialists from Trimaster, we were also able to precisely map specific process flows in the MSB Client, which makes our daily work much easier."
says Martina Kiefer.
MSB Client relieves employees
In general, the user-friendliness and intuitive operation of the MSB Client is a key project highlight, according to Martina Kiefer:
"The speed with which our employees found their way around the new mobile solution was quite unique."
she tells.
Targeted training was simply unnecessary, as many employees simply picked up the handhelds and literally got on with their work.
"This high acceptance of the MSB Client shows me that our employees have quickly realized that using the MSB Client saves time, relieves them and is also modern and up-to-date."
Martina Kiefer explains.
Traceability a must
As a leading medical laboratory, Viollier does not neglect the topic of system validation. That is why the laboratory is certified according to EN ISO/IEC 17025 and ISO 15189. And in this area, too, the company benefits from the use of the mobile MSB Client.
From goods receipt to delivery to the respective customer, all processes can now be mapped transparently across the entire logistics process. This includes, above all, the individual product batches and the best-before date of the stored medical products.
"It was important to us that in the future we neatly document batches and best-before dates of our products along the entire supply chain with the support of IT and make them traceable.
With our new warehouse structure and with the help of the MSB Client, we have found a valid and reliable solution for this".
Martina Kiefer emphasizes.
Viollier is thus well equipped for the worst-case scenario: Products can be recalled immediately or returned to the supplier if quality defects or any damage is detected.
Outlook
The project was a success. The company was able to accelerate its throughput times and thus continue to keep its customer promise "ordered today - delivered tomorrow". With the complete integration of the mobile solution into the SAP system, those responsible for the project were able to improve the warehouse structure across the board, shorten routes and optimize picking with regard to paper.
"The cooperation with Trimaster was efficient throughout the entire project and has proven to be of the highest quality. That is why we have replaced our previous support partner for logistics and entrusted this area to Trimaster."
Martina Kiefer is satisfied.
The next steps have already been initiated: For example, the use of the MSB Client in an internal laboratory is currently being tested in a pilot project. There, a cold storage facility for reagents was converted to a mobile SAP warehouse management system.
With first success: It is already becoming apparent that the mobile platform can also provide reliable support and simplify processes in other areas without hesitation.
"The laboratory world is certainly not an SAP world and yet the MSB Client also knows how to impress our medical staff"
sums up Martina Kiefer. According to the SAP expert, it is entirely conceivable that Viollier will use the knowledge gained from the pilot project to rethink its laboratory logistics across all sites and rely on the MSB Client and Trimaster's expertise there in the future.