Greenfield approach in the private cloud: on two tracks to the S/4 big bang
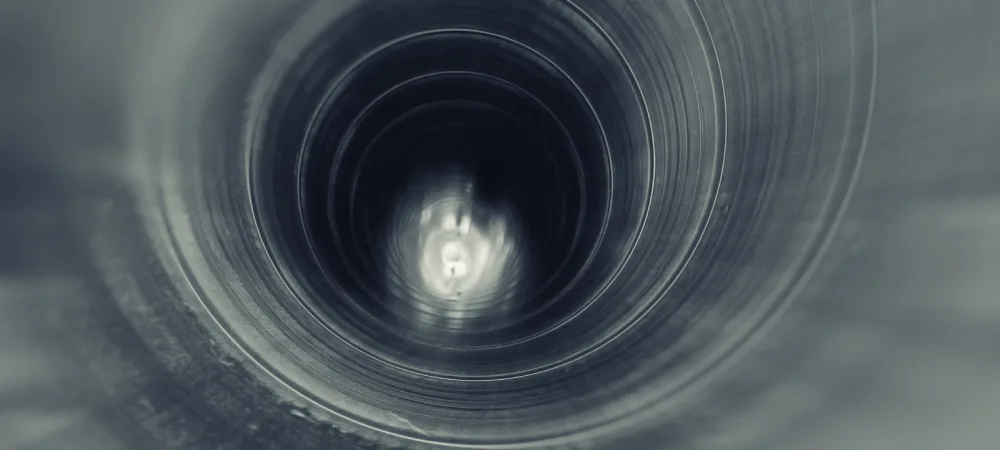
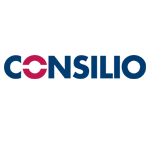
In order to integrate future-oriented technologies such as analytics, artificial intelligence, machine learning, supply chain planning and modern financial solutions in the long term, the international stainless steel pipe manufacturer Fischer decided to switch to SAP S/4 Hana in the private cloud. The previous ERP system was outdated and was no longer being developed further - a new start was required. The management therefore deliberately opted for a greenfield approach in order to build a modern, scalable IT landscape. "Our old ERP system was no longer being developed further. With S/4, we are taking a step into the future and driving forward the internationalization of the Fischer Group," explains Hans-Peter Fischer, Managing Director of the group of companies.
Transparency and traceability
With the changeover, the Fischer Group is pursuing the goal of creating a future-proof production environment: more transparency and traceability in production, improved processes on the store floor and in the Manufacturing Execution System (MES) as well as the integration of state-of-the-art quality management technologies, such as the connection of measuring machines in production and in laboratories.
"We wanted a standardized ERP platform that could map all processes. SAP S/4 Hana offers the ideal conditions for this," emphasizes Hans-Peter Fischer. Thorsten Obert, CIO of the Fischer Group, also underlines the strategic importance of the decision: "With the greenfield approach in the private cloud, we have not only created a flexible and scalable IT landscape, but have also been able to clean up legacy issues and build a completely new architecture."
How has Fischer worked so far?
The division manufactures pipes with different outside diameters. In order to keep the set-up costs on the machine low, those responsible grouped the requirements with identical diameters into a "campaign". This meant that the machine was set up for a specific diameter and the required pipes were then produced for the next four weeks.
In the old system, this was very time-consuming because the requirements could not be sorted by diameter, but only by the requirement date. To improve this inefficient process, Fischer developed an interface that retrieved the current demand figures from the system every night and saved them in a PDF document. In this file, the requirements were sorted manually according to diameter, material and wall thickness.
Daily media breaks
Manuel Hoferer, deputy production manager at Fischer Edelstahlrohre, was not happy with this process: "Planning in this way was incredibly tedious, as we had to deal with daily media disruptions in planning. On the one hand, we had the PDF with the sorting and we practically had to copy the data from left to right before we could plan accurately at the end." This completely changed with the switch to the new SAP system. "With the introduction of S/4 Hana in the private cloud, we have combined the individual steps. This means that with the new SAP system, there is no longer any media discontinuity - we no longer have to copy the requirements from left to right, but have mapped all the relevant data in the resource planning board in PP/DS and can therefore implement the planned orders directly in the system," explains Hoferer.
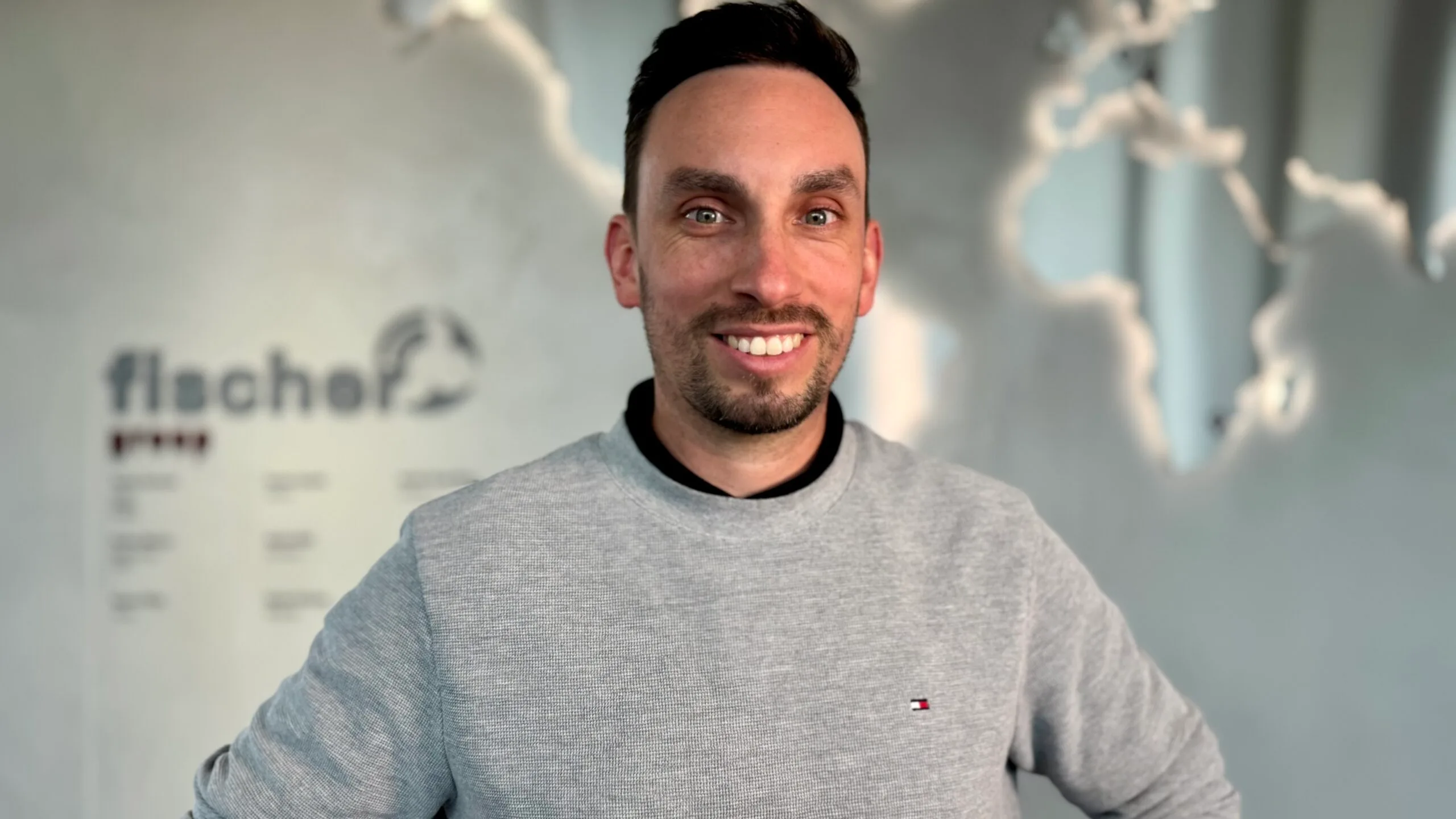
Manuel Hoferer, Deputy Production Manager, Fischer Edelstahlrohre
The planners at Fischer not only work much more efficiently, but the entire planning process has become much more robust and less prone to errors, as the copying step for the employees has been eliminated.
Introduction with obstacles
The switch to S/4 Hana was not always easy for the Fischer Group at first. The biggest obstacle was employee resource planning. "At the beginning, every employee had to estimate how much time they could spend on this project," recalls Hoferer. "Some said a maximum of one hour a day." Background: "The problem was that at the beginning of the project, nobody could really imagine what was going on." This only changed when Consilio took over the project from NTT with the two partners David Reibnegger and Martin Kreutz from Consilio.
The new project managers explained straight away: "It doesn't matter whether an order says 1030 or 1010, because the process flows are now de facto identical under S/4 Hana." At the beginning, it was not clear to the workforce what the Fischer Group was aiming to achieve with the transformation and how everyone could benefit from it - including the individual employees.
"With S/4 Hana, employees can combine their technical expertise with ERP know-how. This not only increases the added value for the company, but also opens up many positive effects for them personally," describes David Reibnegger. According to the employees themselves, this statement was a real eye-opener, as they could now see what the new system could do for the company and for themselves. "Previously, no one had really explained to us in a plausible way what the goal was and how we could benefit from it," Hoferer sums up.
Although the employees now knew the intention of the change, they were not aware of how much work still lay ahead of them. After all, the switch to S/4 Hana also had a serious impact on the processes that had been in place up to that point. Hoferer describes it as follows: "The big challenge in the project was to get to the heart of all the interrelationships. As employees in the project team, we set up a class system, defined characteristics for products and classified our workstations that are relevant for realistic planning." According to those involved, bringing this complex, interwoven planning into reality was relatively difficult, but was very well supported by Consilio. While for some companies the switch to S/4 Hana is initially limited to a purely technical migration of the legacy system, the Fischer Group took a holistic approach.
Herculean task of transformation
Instead of simply converting the existing system, the entire IT landscape was consolidated. Third-party systems were replaced or seamlessly integrated into S/4, while the SAP experts from Consilio customized the planning interfaces to the needs of the Fischer Group. The result: a fully integrated overall system that offers greater transparency on the store floor, in production and in the MES. Thanks to the in-depth system integration, the logistics, production planning and control processes were networked across the entire value chain. In addition, state-of-the-art functionalities were used in Extended Warehouse Management (EWM).
This has not only enabled the Fischer Group to achieve greater transparency in the storage system, but also to make its production processes significantly more efficient. A new material provisioning method in EWM ensures that the machines are optimally utilized and work more productively. Consilio continuously supported this transformation process and optimized the workflows on an ongoing basis. The result: maximum transparency in logistics and production as well as significant cost savings. The successfully implemented transformation also forms the basis for the upcoming global roll-outs, which are also being carried out with Consilio as a strategic and technical partner.
The entire expertise of the company is concentrated at the Fischer headquarters in Achern-Fautenbach. This means that all divisions are represented here. These include Fischer Edelstahlrohre, Fischer Power Solutions, Fischer Rohrtechnik and Fischer Maschinentechnik. Previously, all divisions had developed and applied their own processes. Ultimately, before the transformation, these were separate plants - in other words, islands or separate worlds. Everything was to change with the S/4 Hana project. Consilio organized cross-plant workshops in which those responsible could discuss their processes and the reasons for them.
Connecting what belongs together
Hoferer recalls: "Until before the change, the divisions were like separate worlds. For me, the best effect of the project was that an internal Fischer network was established across all areas during the course of the project and as a result of the workshops. For example, stainless steel pipes, pipe technology, machine technology, QM and sales." According to him, they knew their colleagues from the telephone, but that was the end of the exchange. The standardization was a great benefit for the Fischer Group as a whole, because a large overhead was eliminated. Philipp Schneider sums it up: "As part of the project, we restructured and harmonized the processes. Previously, they were handled differently depending on the plant." In other words, each division at Fischer had developed its own processes and there had been no exchange of information. The restructuring mainly developed in working groups. In these working groups, the individual processes were put up for discussion, discussed, analyzed in detail and checked for practicability.
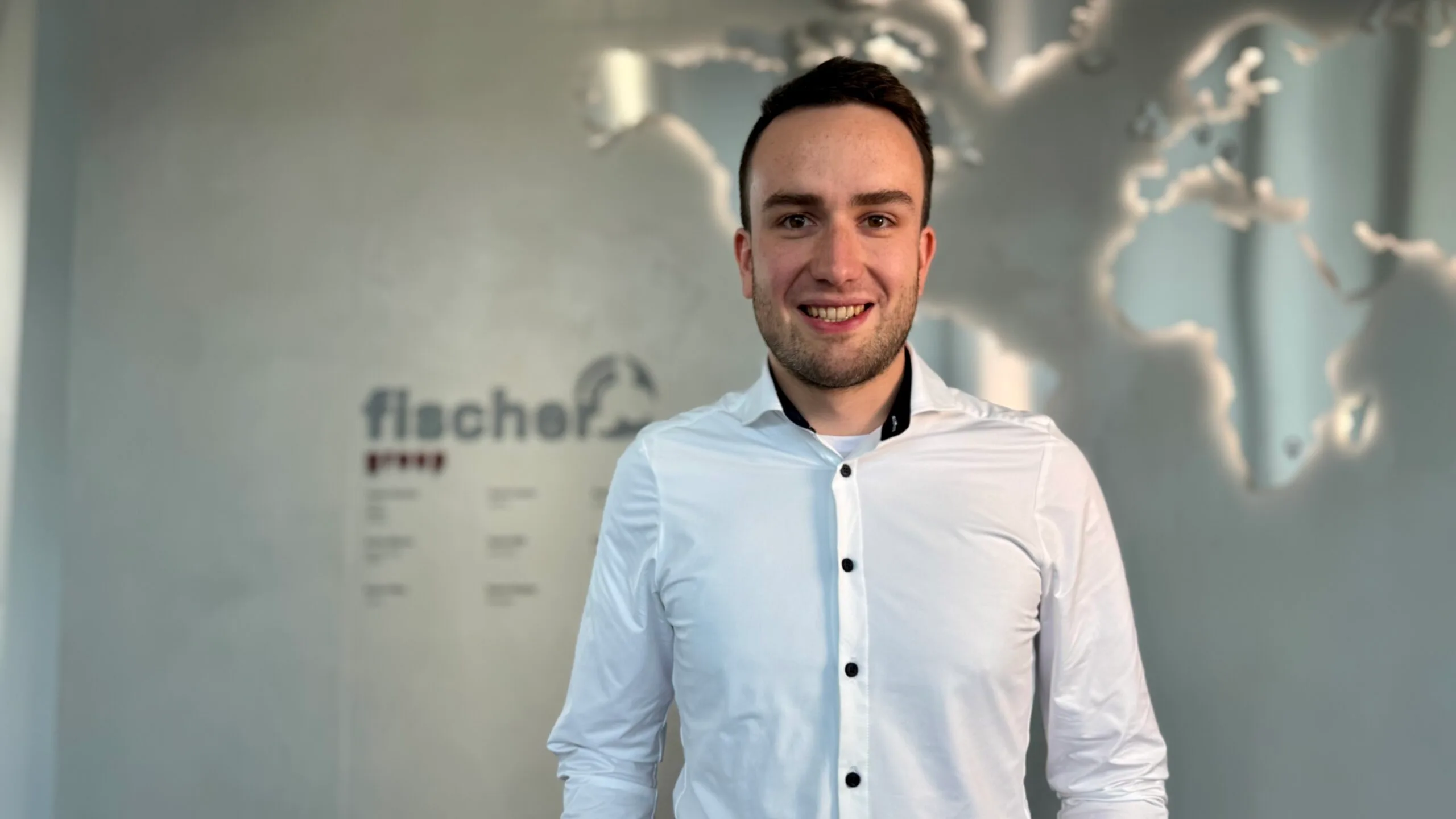
Previously, they were handled differently depending on the plant."
Philipp Schneider, Senior Consultant, Consilio
If the experts thought this was the optimal process, it was adopted. In many cases, this resulted in the harmonization of processes in such a way that every area could be found. This resulted in a de facto consolidation of processes. The resulting new processes combine the best of all worlds. "As not only were the processes converted, but many processes were also redesigned, we had to rethink many things in the working groups and bring the different approaches together. That was a challenge that should not be underestimated," emphasizes Thorsten Obert.
In detail, it looked like this: Eleven technical planners sat down in a working group and carried out planning together. This meant that everyone involved could already see how to plan for the future. This form of change management was well received by colleagues. The new structures in teams, the new hardware equipment with laptops, the easy access to the meeting rooms and the very short communication channels to colleagues and managers have also had a very positive effect on the entire project. "Compared to before, the Fischer Group has reinvented itself digitally as part of the project, which we all appreciate," emphasizes Hoferer. The process consolidation was accompanied by the harmonization of master data in the PLM area, in which Consilio provided significant support.
Product Lifecycle Management (PLM) refers to the system-based mapping and management of the product lifecycle from the idea to requirements, logical and functional structuring and mapping in product descriptions, properties and validation from planning to production and documentation through to recycling. The harmonization of master data gives the Fischer Group a holistic view of product development, optimizes collaboration between departments and reduces errors and costs. This gives the company a central database for all product information, which speeds up decision-making and shortens time-to-market. PLM thus maximizes the efficiency, quality and profitability of companies in an increasingly digitalized world.
Optimal change management
Consilio's change management was also considered appropriate by the employees. There was a kind of "command bridge" in the training rooms that anyone who had problems or questions could turn to. "The distances were very short, as the training center is located very centrally in the plant, and so we didn't have much travel time if there was an emergency," recalls Philipp Schneider, Senior Consultant at Consilio. "This meant we could simply go along with the employees and look at the challenge and overcome it together." Manuel Hoferer adds: "The Consilio employees were available almost around the clock, Philipp mainly in the morning and David and Martin then took over later - that's how you imagine service."
Change in one go
At the beginning of April 2024, the four main plants in Achern-Fautenbach were then converted to S/4 in a big-bang approach - smaller plants in the surrounding regions followed suit. As part of the S/4 greenfield private cloud implementation, Consilio provided support in the areas of production, planning, quality management, technology & development, EWM & logistics and finance, thus making a significant contribution to the successful go-live. In the weeks that followed, all production facilities and areas at the Achern-Fautenbach site were ramped up to full capacity and reached the same volume as before the changeover.
"Delivering on time on the very first day after the changeover was always our top priority, and we managed to do that," recalls Manuel Hoferer. "Various customers have also praised us for this. Especially because we changed both our ERP and MES systems in this mammoth project. We are really proud of this achievement."
Two-pronged strategy
The fact that the changeover went so smoothly can probably also be attributed to the strategy chosen. For several weeks before the go-live, Fischer took a two-pronged approach. This means: "We ran our entire ERP system on a test system a few weeks before the go-live," recalls Obert.
For the employees on the store floor and in planning, this meant an increased workload as they had to maintain the relevant data twice. "But that was probably the key to success for us, as it allowed us to put our planning through its paces in advance," emphasizes Hoferer. The commitment of the employees is a unique selling point for the Fischer Group, as they literally had to press the button twice during this preparation phase.
The result shows that this approach has paid off. Another advantage of this implementation strategy was that employees were able to familiarize themselves with the new system at an early stage and see how the processes will work in the future. "This took the fear out of many colleagues because they found out early on what to expect," explains Obert. Consilio also provided support by training the key users.
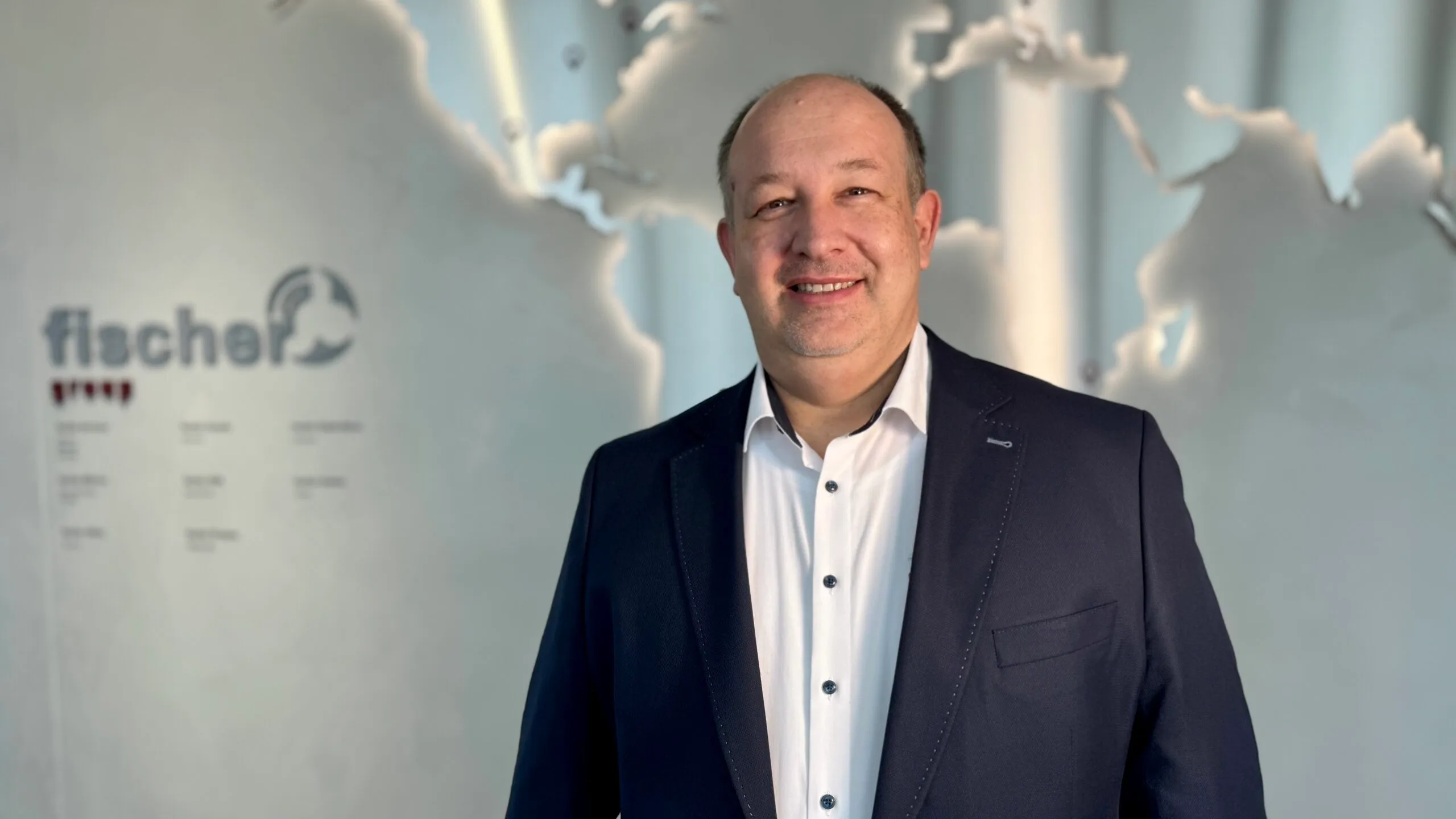
decided on a private cloud."
Thorsten Obert, CIO, Fischer Group
Paperless with S/4 Private Cloud
The fact that the S/4 Hana Private Cloud is the gateway to the intelligent, digital company is also evident in other respects. "The requirements for digitalization and automation can only be ideally implemented in this way," Thorsten Obert is convinced. Since going live in 2024, Fischer has been working 100% paperless - before that it was 100% paper. The reason: since the EWM was introduced in production, all labels are now printed using label printers. A funny detail in passing: "As we doubted that paperless planning and production was possible, we had stocked up on enough folders before the go-live. We no longer need these folders and can give them to other colleagues for filing," smiles Obert. In future, those responsible plan to expand these capabilities even further.
After the go-live, Consilio took over the hypercare phase. Consilio's SAP specialists optimized the new processes, rectified any errors that occurred and adapted the process structures to the company's day-to-day operations to ensure the project was completed smoothly. In July 2024, Fischer transferred the complete AMS service across all areas, including consulting and optimization, to Consilio. Background: Today, technologies and new solutions are emerging faster than ever before. As a result, not only are business requirements changing, but IT has also evolved from a supporting role to an active role in the digital transformation of companies.
But how can IT and business strategy be brought closer together when those responsible have their hands full managing the current IT landscape? The magic word is: Application Management Services (AMS). The service aims to give IT the time and resources it needs for routine tasks. With Consilio AMS, companies like the Fischer Group significantly reduce their operational workload in IT - giving them back the freedom they need to innovate and transform their business into an intelligent company. With its Application Management Services, Consilio supports the monitoring and optimization of applications in day-to-day operations, proactively ensuring that critical business processes, workflows and interfaces function flawlessly.
Fischer Group's commitment to Consilio's Application Management Service lays the foundation for a long-term collaboration based on trust. The aim of the strategic partnership is the further development and joint support and project implementation with the Fischer Group in the areas of SD, PP, QM, PP/DS, EWM, Procurement, GTS, Technology & Development, Finance, Controlling and Basis & Authorizations. Within this framework, Consilio has now introduced a rework process in the areas of PP/EWM/MES and PP/DS. This ensures efficient reworking across all levels with batch management. The solution implemented by Consilio not only strengthens process reliability in the Fischer Group, but also contributes significantly to the optimization of the implemented processes.
Worldwide roll-outs planned
Now that the head office and its plants have been converted to S/4, it is the turn of the remaining branches. The Fischer Group comprises a total of 18 companies in eight countries. Starting from the headquarters in Achern-Fautenbach in southern Germany, the locations are strategically spread across the globe - especially in the hotspots of the automotive industry. As the locations are also to be brought onto the system with a time delay, the project group - made up of employees from Consilio and the Fischer Group - took this issue into account during the transformation. During this time, a template was created that meets 90 to 95 percent of the Group's requirements.
Why not 100 percent?
For Germany, the template covers the requirements 100 percent, but there are other requirements abroad, for example because the documentation is specified by the authorities for a topic or the bureaucracy requires special records. At Fischer, the project team set itself the task of designing the template in such a way that it can be rolled out dynamically to other countries and circumstances with comparative ease. For example, Germany may require different documentation - for hazardous substances, for example - than Canada, the USA, Mexico, South Africa or China. "Even during the transformation, we took great care to ensure that the template could be adapted relatively easily not only to existing locations, but also to potential new ones," recalls Hoferer. As Achern-Fautenbach, according to the company, has the most complex production facility in the group, the management decided that the ideal conditions existed here to develop the prototype for a template that could then be rolled out to the foreign subsidiaries.
"We are very active internationally and our customers require the same processes worldwide, which is why it is essential for us to have a strong partner like Consilio at our side to support us with the international roll-out," emphasizes Hans-Peter Fischer. To ensure maximum flexibility during the roll-out, the template was not hard-coded by the developers - in other words, it was geared towards plants. Instead, the developers at Consilio opted for a dynamic approach. This ensures the necessary flexibility to adapt the template in retrospect, both conceptually and in terms of processes and technical implementation.
Conclusion
With the changeover, Fischer is taking an important step towards sustainable production. The new system lays the foundation for increasing transparency in both planning and production. In addition, it is now possible to raise production worldwide to a common level. This means that those responsible in the company have a concrete overview of what is going on in the company and can take proactive countermeasures in an emergency - regardless of the country in which production is located. Philipp Schneider, Senior Solution Consultant SCM at Consilio, puts it in a nutshell: "Transparency in logistics and production has increased enormously at Fischer. Friction losses between processes are now minimized and those responsible can tell at a glance how and where their goods are being produced - this makes scheduling much easier."
Fischer Group
The Fischer Group is one of the world's leading suppliers of longitudinally welded stainless steel tubes and components. The group of companies based in Achern-Fautenbach in Baden-Württemberg combines the Fischer Edelstahlrohre, Fischer Power Solutions, Fischer Rohrtechnik and Fischer Maschinentechnik divisions. According to its own figures, the company produces 127 million meters of tubing every year, processing over 169,000 tons of material. Production is carried out precisely according to individual customer requirements - from processing the slit strip to manufacturing highly complex components. Each production step is monitored and continuously optimized by specialists. Fischer Power Solutions also develops innovative battery storage systems for industry, the energy sector and manufacturers of special vehicles.
fischer-group.com
Arguments for the cloud
The Fischer Group is a company that is open to all technologies. In order to be prepared for the challenges of a volatile market in the future, the company has opted for the private cloud concept. There are several good reasons for switching to the private cloud: firstly, cloud technology is currently the strategic focus at SAP and secondly, these flexible, scalable technologies can be used to drive efficiency not only in administrative processes, but also in production processes in particular. Fischer can also save on personnel resources with this concept, as the maintenance of the systems is outsourced.

To the partner entry:
