Digital Industry Transformation
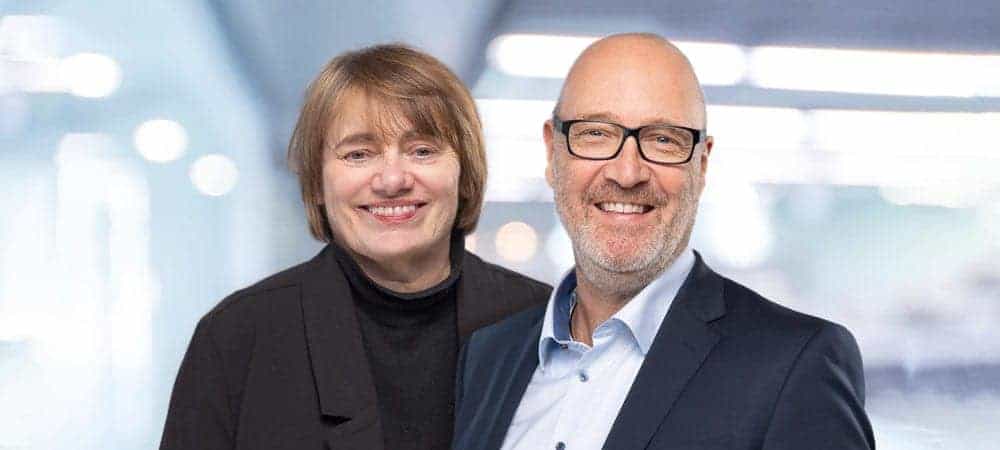
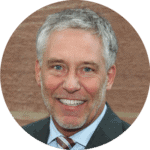
For some users it may be an evolution, others see Industry 4.0 and the Industrial Internet of Things (IIoT) as a revolution. The roots of this digital industrial transformation go back several decades: Who still remembers CIM, Computer Integrated Manufacturing? And what is Industry 4.0 now?
"The term Industry 4.0 describes it strikingly - it is the fourth industrial revolution of digitalization: after mechanization with steam and water power, after mass production through electrification and after the use of electronics and IT"
explains Forcam co-CEO Oliver Hoffmann at the beginning of the E-3 conversation. Digital transformation in industry means the totality of all steps towards the goal of using all technological possibilities of automation and intelligent networking of machines to achieve several goals: more efficient production and processes in terms of a near-zero defect factory; improved global supply and service chains; improved, more customized products.
From a technological point of view, it is about digitally capturing and standardizing data in order to convert it into a semantic layer. In English, this is called "information on a fingertip".
Oliver Hoffmann translates:
"We're saying Big Data is turning into Smart Data, real-time information that can be used analytically, in the form of a digital twin of production on a computer."
Networked production facilities, real-time communication between machines, individual support from colleagues robots: the digitalization of industrial companies in Germany is making progress, as the digital association Bitkom also knows.
Almost six out of ten industrial companies with more than 100 employees in Germany, i.e. around 60 percent, use special applications from the field of Industry 4.0.
This is the result of a study on the digitization of German industry commissioned by the digital association Bitkom, for which 552 industrial companies with 100 or more employees were surveyed from mid-February to early April 2020.
The path to digital industry transformation thus seems irrevocably predetermined. Andrea Rösinger, Oliver Hoffmann's colleague and Co-CEO at Forcam, points out the associated change management:
"Digital transformation has an important second level in addition to the technological one. The introduction of an IIoT platform always means a cultural change within the company. Therefore, a digital transformation in an industrial company can only fly with two wings:
The first is adequate IIoT technology, the second is the right cultural solution. Because improved efficiency and quality are only achieved through the passion of those who are supposed to deliver them - the employees themselves.
Leadership must therefore aim for a new learning culture with elements such as empowerment of skilled teams, virtual collaboration of interdisciplinary teams, new ways of communicating and dealing with mistakes."

According to Rösinger and Hoffmann, the company needs a broad understanding that only transparency and efficiency through data-driven manufacturing with precise KPIs are an opportunity for higher productivity and sustainable optimization.
Bitkom has found that almost three quarters of German industrial companies are changing not only individual workflows or processes in the course of Industry 4.0, but also entire business models.
Slightly more than every second company is developing new products and services or plans to do so. One in four is changing existing products or plans to do so. 28 percent are even withdrawing existing products and services from the market altogether. Change management thus seems to be the order of the day.
"Automotive producers are evolving into mobility solution providers and medical technology manufacturers into smart healthcare providers. This path must now be continued across the entire industry. The business models of the future are exclusively digital"
says Bitkom President Achim Berg.
"This also makes it all the more important that the topic of education - education and enablement - is included on the lists of measures for digital transformation"
emphasizes Andrea Rösinger in this discussion. The digital transformation in production and manufacturing is a business, organizational and technical challenge.
"It's a challenge for the whole company, so it's a challenge for all three areas mentioned."
explains Franz Gruber, founder of Forcam.
Business management, organization and technology must be viewed and worked on in an integrated manner. In the digital transformation, technology and business management are inseparable, then comes the organization.
"But I want to go further"
defines Gruber.
"The digital transformation in industry is a challenge for the national economy - and therefore for society. The prosperity of modern economies depends on vital industrial production.
Kuka manager Heinrich Munz proved in his presentation at a Forcam event: The more automation, i.e. the more robots, a society has, the lower its unemployment rate.
That's why the challenge is that we need to work on digital transformation in concert with all parties, especially the collective bargaining parties, not in conflict."
Securing skilled labor is an important topic among industrial companies, defines the Bitkom study mentioned above: 66 percent affirm that Industry 4.0 will create new jobs for well-trained skilled workers.
Almost all of them believe that work in the networked factory increasingly requires interdisciplinary skills, for example at the interface of mechanical engineering and computer science.
"The introduction of new technologies, tools and methods naturally has an impact on employees in companies. Digital education and training are essential now and in the future."
emphasizes Bitkom President Achim Berg.
"The need for knowledge and training is becoming ever greater due to faster innovation and shorter product cycles. Guaranteeing digital education in the long term must be in the common interest of politics and business."
The numerous requirements and opportunities lead to the question: Will IIoT also change business processes in the manufacturing industry? Does the organization of the "factory" have to change? "Definitely yes," says co-CEO Rösinger. She believes that companies need a strategically sound and operationally oriented organizational model, a Strategic Operating Model.
"Because leadership and process excellence are two sides of the same coin".
Andrea Rösinger specifies.
"With the introduction of new technologies, as already described, a new culture is also needed. The background to this is that, of course, the trend is continuing that low-skill jobs in industry are on the decline, but the need for skilled workers remains high. So the organization of a factory clearly needs that education component."
The digitization of production and manufacturing has a very long tradition, starting sometime decades ago with CIM, Computer Integrated Manufacturing: Why did it take so long to get to IIoT? What distinguishes the concepts of that time from current IIoT solutions? Forcam founder Franz Gruber answers this question:
"I started my career in the CIM era of the 1990s. That's why I can say: companies used to make revenue in the boom times. Costs didn't play such a big role.
A prominent example: Deutsche Telekom's very successful IPO in 1996 may be symbolic of this spirit of optimism across the board. Computerization had established itself as a magic bullet in the economy, and now investments were also being made briskly in manufacturing."
Andrea Rösinger adds:
"In addition, of course, the technological possibilities were not yet available - bandwidths, for example. It used to be the case that the less data, the better. Today, data volumes no longer play such a big role due to ever new bandwidths and digital capacities."
And Oliver Hoffmann explains the IIoT phenomenon:
"The investment rhythm of companies has already come up: Companies invest in machinery and equipment for long periods of time, ten, 15, 20 years.
This is another reason why it takes longer for a new technological era such as the IIoT to gain widespread acceptance in the industry. This makes it all the more important to rely on a modern IIoT platform that makes it possible to protect investments while enabling innovation."
The analysts at Gartner (USA) give Forcam a unique selling point: "Forcam Force is the only IIoT platform with out-of-the-box MES applications."
"Almost all companies have set out on the path toward Industry 4.0"
says Bitkom President Achim Berg. This realization is also anchored in the majority of companies: 94 percent see Industry 4.0 as a prerequisite for maintaining the competitiveness of German industry.
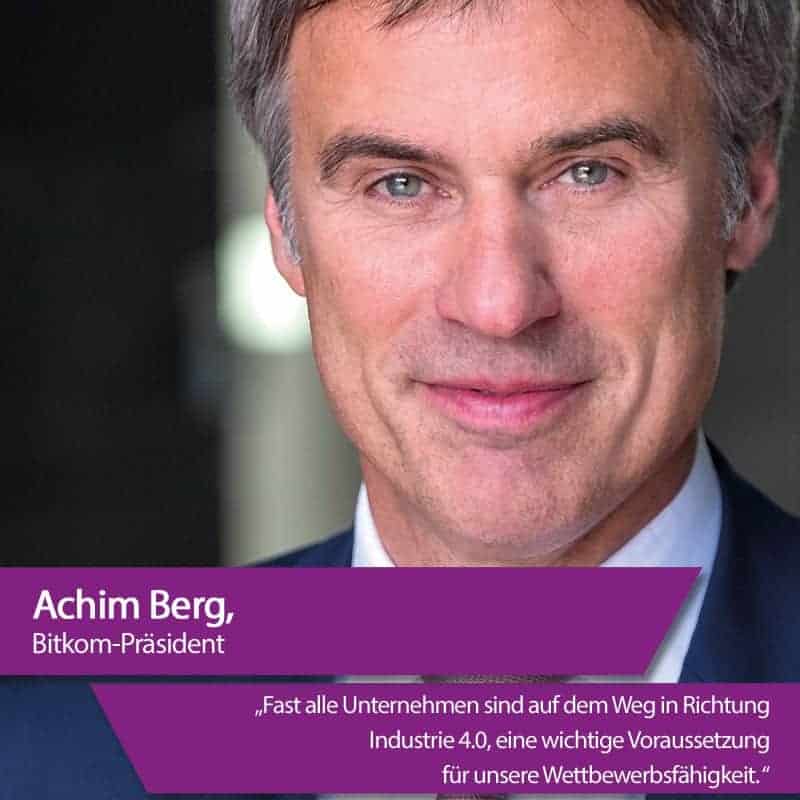
More than one in two emphasizes that Industry 4.0 generally gives their own business a new boost. Overall, an overwhelming majority of 93 percent of industrial companies see Industry 4.0 as an opportunity.
Industrial control systems, electronic planning boards, manufacturing execution systems - these have been around for many years. What is different and new in the "digital transformation"?
"The issues mentioned all continue to exist, they all continue to be present in everyday factory life. The investments are not lost"
reassures Oliver Hoffmann.
"What is different is networking, and today I can work much more efficiently with networked parts, products and units as well as with networked processes. Digital openness via open web interfaces - Open API - also makes it possible to build completely individual IT architectures and have existing or new solutions interact and collaborate on one platform."
What can be adopted from the "old" world into the digital transformation of industry? Franz Gruber:
"The old world goals remain: Lean and Clean manufacturing. The goals of the various concepts - whether CIP, TPM, etc. - apply. What is new are the technological possibilities for achieving the goals."
With the new technological possibilities of integrative IT architectures, of interoperability, composition and collaboration through open platforms and unified data lakes, new needs also arise, for example for good IIoT process consulting.
It should be carried out by experts who know both the factory from the inside and the new technological possibilities of the IIoT era. Bitkom has surveyed that the majority of industrial companies developing new products and services in the course of Industrie 4.0 are relying on platforms.
Artificial intelligence (AI) is also considered to be very important. One in seven companies is currently using AI in the context of Industry 4.0. Common AI applications include predictive maintenance, in which algorithms and sensors are used to monitor the operation of machines so that the AI indicates the need for maintenance before an impending failure. Robots that can independently adapt their workflows to current requirements are another such example.
"Forcam's semantic model is based on in-depth knowledge in the manufacturing process, in its versatility and distinct variability"
comments Olga Mordvinova, Managing Director Incontext Technology and Forcam partner. The model transforms pre-interpreted production data into consistent data structures that provide not only machine or workstation information, but also detailed information about the historical and current state of the production process across workstations.
Incontext's AI applications master the semantics of Forcam Force's production processes and learn to automatically identify problematic situations from the production line's "Small Data."
They combine self-learning algorithms with global insight into production and the ability to provide local instructions at workstations to employees based on their roles.
"Examples of our applications: predictive maintenance of workstations, detection of deadline-critical jobs, or predictive overall plant effectiveness."
Olga Mordvinova adds.
For Bitkom, the most important benefits of AI in industry include an increase in productivity and the optimization of production and manufacturing processes, in addition to the aforementioned possibility of predictive maintenance.
"AI is an epochal technology that will revolutionize the global economy and, in particular, industry"
explains Achim Berg.
What should an existing SAP customer look out for when IIoT is on their to-do list? Oliver Hoffmann:
"The existing SAP customer should look at all the IIoT platform solution providers for the store floor in the market, compare them and make a qualitative benchmark."
Transparency is provided by comprehensive connectivity for store floor and pot floor, i.e. the integration of existing heterogeneous machinery and also networking with corporate planning.
"Productivity exists through simple, turnkey integrated solutions because it determines how quickly I can achieve measurable results"
defines Hoffmann. Forcam comes with the most important MES apps pre-installed and ready to use.
"And ultimately, I get flexibility through web technology openness," Hoffmann knows from numerous successful projects. "So open web interfaces that allow me to integrate any existing or new solution I want."
Why is the Forcam IIoT offering particularly suitable for existing SAP customers?
"As Oliver has already pointed out: because we offer transparency through comprehensive connectivity on the store floor and pot floor; because we offer rapid productivity gains through simple, turnkey integrated solutions; because our solution offers the greatest possible flexibility through web technology openness"
adds co-CEO Rösinger, who emphasizes one point once again:
"The uniform data model from manufacturing to finance. Only precise data from the store floor enable accurate unit costing and planning on the pot floor.
Controlling representatives of our customers confirm this to us. Real-time controlling of unit costs through real-time data from the factory. It's about bringing controlling and quantity values together. A new transparency and thus the elimination of discrepancies in planning has enormous advantages for sustainable cash flow management."
Forcam has a strategic partnership with Accenture: what are the reasons and the benefits for an existing SAP customer?
"Manufacturing companies usually have very similar challenges, even if the solutions are then very individual"
recognizes Oliver Hoffmann. Core issues are: no unified view of manufacturing, no unified information and companies cannot learn from each other across plants; they work with functional IT silos; patchy store and top-floor integration causes errors and delays; resources cannot be measured, coordinated or planned globally.
"We address all these topics at Accenture's Industrial IoT Innovation Center in Garching near Munich, where we are an ecosystem partner. There, we aim at joint strategic design thinking with customers as well as demonstrating concrete technological solutions."
explains Forcam co-CEO Hoffmann.
"From Accenture, the existing SAP customer gets advice on strategies, architectures, the integration of systems and supply chains, and project planning"
defines Andrea Rösinger.
"From Forcam, he gets the technologically globally scalable cloud platform solution as well as our know-how in IIoT process consulting. The advantages of Garching are that we can talk, think and create there in an innovative atmosphere.
This is extremely important because, after all, it's about the digital business processes of the future - or, conversely, about the future viability of companies."
Forcam also has a strategic partnership with Microsoft, whose manager Sebastian Seutter is an Industry 4.0 expert and member of the Forcam Innovation Board.
"In fact, especially in Germany, we have a lot of common customers for whom a close partnership between SAP and Microsoft is key"
Seutter explains the added value for Forcam customers and the SAP community.
"The mission of our partnership is to support customers together with our partners in their digital transformation and in all innovations around integrated solutions and technologies from SAP and Microsoft in the best possible way.
The partnership between Forcam and Microsoft is precisely creating the added value for our customers to digitally redesign, optimize and comprehensively integrate their production and the underlying technologies of smart manufacturing. This leads to improvements in production."
Forcam co-CEO Rösinger specifies in an E-3 interview:
"With Azure, Microsoft is the world's largest cloud infrastructure provider. This means that there are virtually no limits to scalability. Due to its history, Forcam carries the SAP gene; SAP has one of the leading ERP solutions worldwide. With Microsoft as a partner, we can in turn solve interface issues of globally operating companies particularly well together."

At the moment, there is a clear trend to customize SAP systems on Microsoft Azure: Would a complete factory plus administration from Azure thus be conceivable?
"A factory on Azure is indeed still a vision today"
Sebastian Seutter tells E-3 Magazine.
"However, with Microsoft Azure Cloud, we already bring all the foundational technologies to make this vision a reality."
First, all the prerequisites for the necessary integration of all systems and technologies also exist via the SAP Cloud Platform (SCP), which is also available on Microsoft Azure. Then the SAP credo "keep the core clean" comes into its own here.
This means that adjustments to the SAP core can be easily moved to Azure via the SCP where innovations are desired and can be implemented quickly.
"In conclusion, through our partners and their core competencies, we bring all the starting points to develop architectures and SaaS solutions with and on Azure. This makes it easy to automate, integrate and extend all the desired functions of this factory on Azure in our cloud."
Seutter also knows from his professional experience.
"Azure offers, among other things, a complete IoT hub. Included there are tools that enable the integration of edge components."
adds Andrea Rösinger.
SAP itself is trying its hand at the digital transformation of industry with products such as SAP ME and the Leonardo framework: what is Forcam's position vis-à-vis these SAP offerings?
"Our solution concept as a platform provider is comprehensive and provides that we can integrate any solution required by companies or at least ensure that it can be integrated smoothly"
emphasizes Co-CEO Rösinger in an E-3 interview.
"Our claim to openness is comprehensive. In addition, we also offer the Forcam IIoT platform solution as a white label product. And since the leading minds in our company come from SAP themselves, our solution integrates SAP offerings such as SAP ME, SAP EWM and others very smoothly accordingly. The point is, we protect investments in IT like SAP, and we enable innovation at the same time."
