Up(s) to the locomotive
![[shutterstock:458816314, Leonid Andronov]](https://e3mag.com/wp-content/uploads/2013/08/Redaktionell-ONLY.jpg.webp)
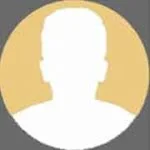
Single-unit and small-batch manufacturers in the mechanical engineering sector usually produce complex products with customized features. Production is usually project-related, with customer-specific variants often being developed.
Due to the numerous Components is the timely Production a challenge for the Production planning and control. With the SAP ERP-Module PS a tool is available with which the large quantity structure can be structured and mapped.
Since this system is transaction-oriented, it quickly and clearly presents information about individual Components ready. It is just as suitable for accompanying and documenting production.
Since the module PS but only a few functions for gaining an overview and Planning is possible through the replacement of a common Database with a faster Database alone, no improvement can be expected.
Discussed is the manufacture of Diesel locomotives, mainly for shunting operations. Such a Locomotive consists of 25,000 to 30,000 individual parts.
This Locomotives are offered in various basic types and then modified to a greater or lesser extent according to specific customer requirements. Considering that the annual output comprises more than 55 machines, one can easily get an idea of the quantity structure to be processed.
The Planning of the customer-specific characteristics of complex technical products can be achieved using the ERP–PS-Module from SAP for make-to-order production and the Small series well. The main production steps - in this example, the main assemblies - are mapped in networks.
Bills of material are assigned to these networks at the individual network activities. These BOMs can contain both purchased parts and anonymously produced standard assemblies. The standard assemblies can be broken down further over several production levels.
Thus, there is a mixture of customer-oriented and customer-anonymous production.
At Frame A customer is given a delivery date for a product on the basis of coarsened capacity estimates. Locomotive notified. This estimate is made on the basis of Data for standardized prototype locomotives and coarsened capacity requirements outside the SAP-System.
The challenge now is to transform this coarse into a fine Planning to transfer. On the one hand, this naturally concerns the scheduling of the production steps of a Locomotive. It is complicated by the fact that during manufacturing several Locomotives compete for the same capacities and materials.
The difficulty does not usually arise during final assembly, as this is not carried out until all the Components are available. The problem rather lies in the coordination and Planning of customer-anonymous manufacturing.
A single component or assembly can be manufactured in multiple Locomotives be obstructed. Here, for reasons of economic Warehousing the principle of "first come - first served" is applied.
If you were to work with order reservations, it would be easier to assign an assembly to a certain order. Locomotivebut this would also have a correspondingly higher Stock as a result.
In practice, one usually helps oneself by referring to individual Locomotives the so-called backlog hours are determined. The backlog hours are calculated by means of SAP calculated.
With the help of this information, priorities are then set in production when deadlines are tight in order to meet the production dates promised to customers. However, this is not Planningbut reactive control.
Therefore, in this context, users want a dynamic Pegging and a simultaneous Material- and resource allocation planning in order to be able to estimate the consequences of any change (new orders, postponement of deadlines, change in available capacity material deliveries or orders).
Solution approach
The aim must be to ensure the timely completion of the Locomotive to be able to plan. The aforementioned backlogs, which inevitably arise in the operating business, must be recalculated at any time for the future and firmly incorporated into the advancePlanning be integrated.
As a result, you get a statement about the production status of an Locomotive. Usually, the safety and float times that are required for the initial scheduling of a network or for the MRP-run are taken into account, reduced.
This reduction is not made across the board, but by finite Planning of the individual workstations, taking into account the dependencies of the individual Components to each other. However, this is only possible if a software tool is available that transparently displays the relationships in the order network and enables the desired finite scheduling.
Modern APS-systems meet the requirement of simultaneous Material- and capacity planning and are in principle suitable for fulfilling the tasks outlined here. However, it must be mentioned restrictively that only a few systems are currently capable of processing the complex interrelationships in a mixed customer-oriented and customer-anonymous order network.
Vossloh Locomotives has decided to use OR Soft's Enterprise Workbench. The decisive advantage of this solution is the complete integration with SAP ERP, especially its PP modules, PS, PM. The OR Soft system does not have its own master and transaction data.
All Data are made from the ERP extracts the results in the form of planned orders and production orders, purchase requisitions, network activities or WBS elements in SAP written. As a result, it is not necessary to maintain separate master data, establish interfaces or learn new terminology. As an additional benefit, this means that the operation of the ERP simplified with the help of an intuitive, graphical interface.
Thanks to the 64-bitTechnology of the Microsoft-There are no technical limits to the amount of data that can be processed with the Enterprise Workbench operating system. The Enterprise Workbench is usually installed locally on a PC; corresponding computers with 8, 16 or more GB of main memory are available on the market at low cost.
The Enterprise Workbench interface is accessed via a browser. There, all networks or all networks under construction are displayed. Locomotives is displayed. Three icons in the right area provide information about the current status of the Locomotive in the system:
- Scheduling conflicts: incorrect chronological arrangement of operations or Production orders in a production chain
- Capacity conflicts: an order has a capacity conflict if, for at least one of its operations, the respective work center is overloaded for the duration of the operation on at least one day in total.
- Availability check for purchased parts: In the event of non-availability, the display additionally distinguishes whether the part in question can be procured within the stored planned delivery time or not.
It should be noted that not only Production orders and network activities, but also planned orders (linked to the information of routings and bills of material) can be included in the calculation of conflicts.
The expandable tree browser contains all assigned data elements to a network including the information about the temporal position.
If the assigned data element is a plan element or a Production order, you can tell by the icons whether he has a 1:1 mapping to the Demand creator has or whether several Demand creator be covered. This connection results from the dynamic allocation of the customer-anonymous Production with the "first come - first served" principle.
The bar graph can be interpreted as follows:
- For all mesh elements, the time between corner start and corner end is shown as a thin blue bar
- The background of this bar is displayed in green or red according to the time schedule position
- A green background signals the permissible shift period without violating time dependencies to the predecessor or successor
- The red background indicates that at least one temporal relationship to the predecessor or successor is in conflict. Via a context menu, it is possible to have the system correct the temporal position of the order or the operation (as far as still feasible in terms of time). The system contains a number of other information options and functionalities - but describing them here would exceed the scope of this manual. Frame burst.
Summary
An add-on for the modules PP and PS supports the Planning competing order networks. It thus enables the user to switch from a reactive control in work preparation to a proactive one. Planning transition.
This gives rise to business potential, in particular through assured adherence to deadlines, smoothening of production and reduction of inventories.