Digital transformation in times of the pandemic
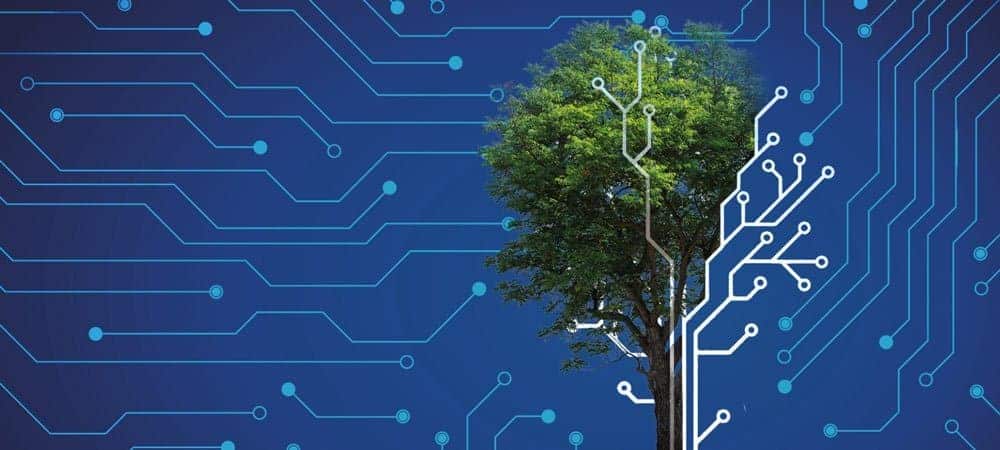
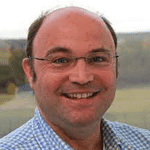
The companies of the world work in a very division of labor. Fiscal year after fiscal year, the company's own vertical range of manufacture has been reduced, more and more semi-finished products have been bought in from all over the world and, ideally, only those parts that make up a company's core competence have been produced in-house. There is nothing fundamentally wrong with this. This made goods cheaper and more diverse.
It becomes a challenge when a threat, such as the current Sars-CoV-2 virus with Covid-19 disease, emerges. The measures to combat it disrupt the flow of goods and restrict the movement of people through so-called non-pharmaceutical interventions.
What happens to the supply chain? If you ask buyers, it goes without saying that they know their suppliers. But are they asking the right questions and are the answers up-to-date? What about risk transparency across different manufacturing processes at multiple suppliers?
This alone is where most systems fail or are non-existent. There are industries where bottlenecks are easily recognizable for insiders, such as in the pharmaceutical sector.
From 50 preparations three years ago, which were only available irregularly or no longer, there are currently over 300, as can be seen on sites such as the Yellow List.
For example, ibuprofen is produced in only six factories worldwide, none of which are located in Europe. If we assume transport by sea freight, there is an additional two months of transport from production to further processing in Europe.
As long as local production is not possible, an order management solution, for example, can help to make the stocks and capacities of the connected warehouses visible.
This makes it transparent where which quantities (in which quality) are in stock. Already reserved quantities or minimum stocks are taken into account. With the help of historical data, the requested quantities of the company's own customers and ideally of its own customers, requirements can be better forecast and distributed. At the same time, new suppliers can be "on-boarded".
In the case of ibuprofen, this will only be possible if other suppliers enter the market.
However, in the case of other shortages such as those we are currently experiencing, such as disinfectants or respiratory masks, it is easier to find new suppliers. Thus, if the current supplier data is available, suitable suppliers can be approached if necessary in order to manufacture a product that was previously unfamiliar to the specialist.
As an example, the clothing manufacturer Trigema has announced that it will also be able to produce respiratory protection masks, as they differ too much from conventional clothing in terms of material but not production technology. Something that ZF is already doing.
For lack of affordable respirators, the gearbox manufacturer from Lake Constance simply produces them himself in China for his local employees. For disinfectants, for example, distilleries or manufacturers of perfume are obvious candidates. LVMH, for example, has announced that it will switch parts of its production to the urgently needed hand disinfectants for a certain period of time.
When an event results in such far-reaching cuts, it is often said that "nothing will ever be the same again". In the course of the events and acute experiences, this is a true statement. Nevertheless, much remained the same afterwards as it was before.
With regard to digital transformation, I do hope for a change in thinking. Better networking of companies in the supply chain, greater transparency, a fast and spatially flexible infrastructure combined with a bit of artificial intelligence - that could have helped a lot of companies right now. My final sentence comes from the heart: Please stay healthy!