Automated and Reliable
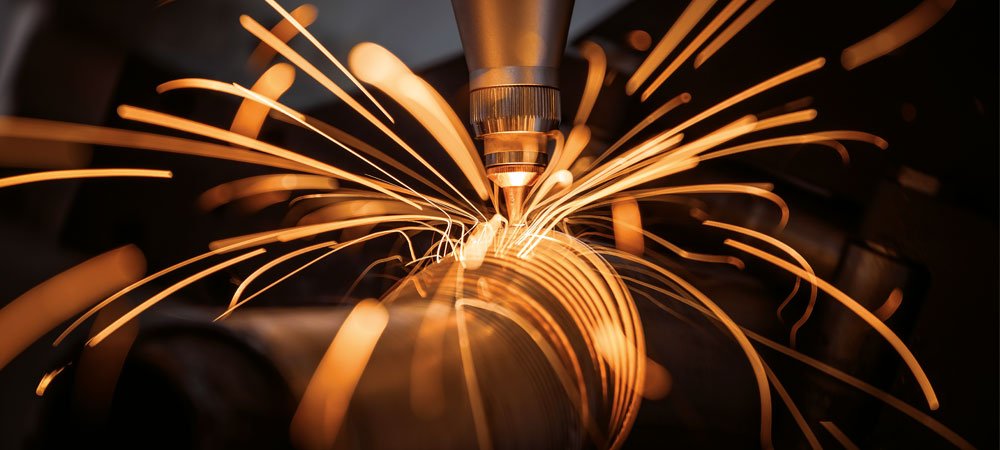
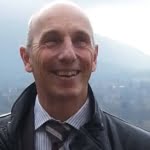
SAP inventory customer Vishay handles consignment processes with Speedi VMI
The consignment process with Vendor Managed Inventory (VMI) noticeably simplifies the work of the approximately 200 end users in Vishay's four customer service centers worldwide. Discrete semiconductors and passive components such as diodes, mosfets, power ICs (integrated circuits), optoelectronic elements, resistors, inductors or capacitors perform their services mostly invisibly in the background. They ensure that cars, computers, laptops, smartphones, wearables, TV and smart home devices as well as industrial plants and medical technology applications run smoothly. At the same time, they are an indispensable component in the implementation of digital innovations such as 5G network technology, the Internet of Things (IoT) or production in the sense of Industry 4.0. What few people know: In many cases, the electronic helpers come from Vishay, headquartered in Malvern, PA, USA.
The group of companies, founded by Felix Zandman in 1962 and named after his ancestors' village of origin Vishay in Lithuania, is one of the largest and most renowned manufacturers of electronic components. Vishay produces around 50 billion parts per year worldwide. In 2021, Vishay, which is listed in the Fortune 1000, generated sales of the equivalent of almost 3.2 billion US dollars with 22,800 employees in 22 countries. In addition to well-known automotive suppliers and industrial companies, its customers include service providers for electronic manufacturing services (EMS) as well as telecommunications providers and medical technology manufacturers.
The company's economic success is based primarily on the development and manufacture of innovative component solutions of the highest precision and quality. The consistently high level of the goods delivered is ensured by quality systems for each product line and excellently equipped test laboratories at the individual plants. Efficient and transparent business processes in all areas are also important for success. The manufacturer of electronic components has been managing these for years with integrated functions of the SAP ERP/ECC 6.0 business software. The processes in logistics handling with customers, in particular consignment handling with Vendor Managed Inventory (VMI) or Customer Managed Inventory (CMI), are particularly complex.
Tens of thousands of IDoc types
"Consignment with VMI and CMI is usually done for products that we mass produce and with which we regularly stock the customer's warehouses"says Melanie Kramer, Senior Manager SAP SD at Vishay Semiconductor in Heilbronn. Depending on the customer's location, the processes are handled in the relevant Vishay customer service center in Germany, France, Asia or the USA.
"This is quite complex, partly because we currently manage around 20,000 scheduling agreements for consignment in the SAP ERP system. Customers usually transmit their stock withdrawals once or twice a week. This means that we have to process between 70,000 and 80,000 IDoc messages every week." explains Melanie Kramer. This includes, for example, messages for goods receipt, goods withdrawal and daily collective delivery. In addition, the actual net replenishment quantity must be calculated in the VMI calculation based on the gross withdrawal that the customer passes on, and at the same time it must be calculated when and in which batch size the parts are to be produced and at what time they are to be delivered to the customer.
Stable VMI processes
However, the SAP standard does not adequately cover the processes involved in consignment processing with replenishment control via VMI or CMI. Those responsible therefore decided to use the Speedi VMI solution from WSW Software, whose functions extend and optimally complement the SAP standard at this point without modification.
With the add-on from the SAP-based Speedi platform, around 200 end users in the customer service centers now handle the VMI and CMI processes IT-supported, largely automated and uniformly across the sites. With every stock withdrawal and every delivery call from the customer, the add-on recalculates the replenishment deliveries and adjusts the shipping quantity due in each case to the new demand and stock situation. The solution also ensures that the minimum and maximum quantities agreed with a customer are adhered to in terms of consignment stock, and it also processes bulk data quite quickly.
"All this and the fact that the processes run stably and reliably like Swiss clockwork simplify and facilitate the work for the end users enormously. For them, this is a real added value, because it leaves them more time for other important activities such as clarifying orders or communicating with customers."Melanie Kramer explains. At the same time, the IT department also benefits from a reduction in workload. Since there are hardly any support requests thanks to the reliable process handling and experienced end users can largely set the parameters for replenishment control themselves and change them as needed, internal IT can focus more on its core tasks. These include the implementation of new processes and functions.
Change of Ownership
The fact that Speedi VMI also maps a very special process requirement in VMI processing is an additional plus: If replenishment quantities are on their way to the customer, a transfer of ownership of the goods takes place at Vishay from the producing plant to the respective sales company. In order for Controlling to be able to make the necessary postings correctly, this change of ownership must also be reflected in the SAP delivery schedules.
This special feature is covered by the add-on via an additional development, which WSW experts and internal IT created in partnership with the help of special functions and routines. "In addition to the consulting and process expertise and a solution-oriented approach, even for special process requirements, we appreciate the short response times of the support team and the early communication of innovations," says Melanie Kramer.
The positive experiences were the reason to also map other SD-related processes with Speedi solutions in an integrated and consistent manner in SAP. In the meantime, an IT tool checks the cumulative quantities in the SD delivery schedule for plausibility or calculates them if the customer does not transfer them. Another tool resets the company's own cumulative quantities in goods issue to the correct value at the change of fiscal year - the keyword here is zeroing. An SD scheduling agreement copier is also currently being introduced in order to carry out the cancellation of scheduling agreements that are no longer active and affect performance, as well as the creation of new scheduling agreements, with IT support in the future.