S/4 Hana Migration—Quick Steps to Success
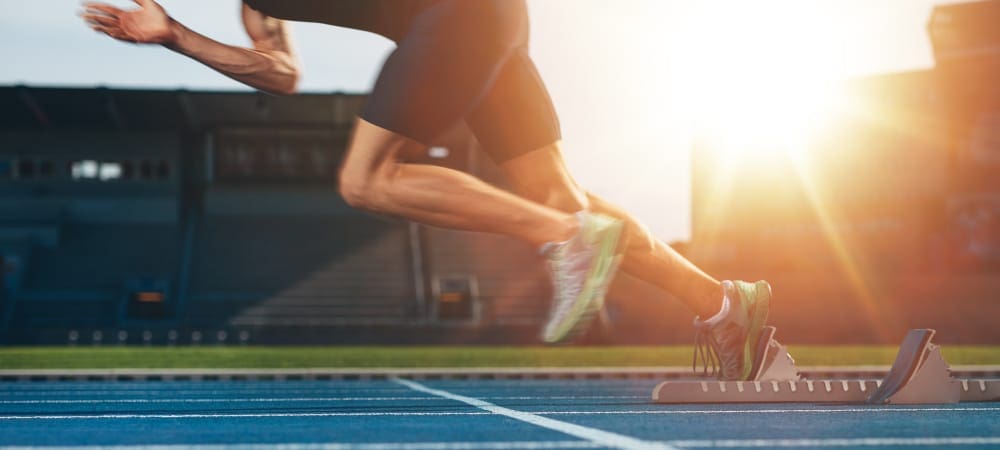

The footwear industry is facing far-reaching changes. The necessary proximity to customers requires decentralization of production, which is increasingly being relocated back to Europe. Consumers value sustainable production methods. Shoe machine manufacturer Desma supports manufacturers here with highly automated machinery and comprehensive support. Even in the past, the SAP ERP system acted as the master for all processes - from design and production to sales and accounting.
The company wanted a system that was easy to maintain. In-house interfaces were avoided wherever possible. If other systems required data, this was exported. With the support of SAP service provider Abat, it was possible to successfully transform from SAP R/3 to S/4, which means that internal processes can now be optimized and further innovative production solutions for Industry 4.0 can be implemented. "We didn't want consultants who would bend the system and then no longer be there tomorrow," says Desma Managing Director Christian Decker.
Reporting? Runs
One focus of the project was on strict compliance with SAP standards to ensure an easy-to-maintain system. The core project was completed after five months. New functions and increased performance led to immediate user familiarity with the new system. One advantage was the direct integration of dashboards and the ability to access the Hana database. A recurring issue with R/3 was the lack of data transparency and inadequate reporting options.
With the new S/4 solution, quick access to the dashboards has become easier. The SAP Analytics Cloud can now access the Hana database directly. This significantly improves the reporting functions and creates greater data transparency. However, some intensively used R/3 functionalities were no longer available in S/4. But here Abat demonstrated its expertise in developing alternative solutions and workarounds. The discontinued SAP CRM 7.0 was also converted as part of the conversion. Desma is now successfully using the CRM functionalities in S/4 (S4CRM). The initial CRM conversion was followed by the replacement of the SAP CS module and the introduction of the new SAP service. With the migration from CRM 7.0 to the CRM functionalities of S/4, a significant step was taken towards the integrated customer relationship management solution.
The new CRM functionalities enable seamless integration into the remaining business processes. Sales and service employees now have a comprehensive overview of the customer history and can respond to inquiries more quickly and in a more targeted manner. Replacing the old CS mode with the new SAP service has significantly improved service processes. The new functions support technicians in planning and carrying out maintenance work. Mobile solutions allow them to access all the necessary information on site and enter service orders directly in the system. This increases efficiency and customer satisfaction.
As part of the innovation project, many other user stories were implemented in all areas of the company. The aim was to achieve the best possible usability in the SAP standard. The continuous innovation sprints enabled the implementation of more than 100 new functions that were missing in the old ERP version. The changeover to S/4 was a comprehensive transformation project that affected all areas of the company. The focus was on harmonizing and standardizing processes.
In the old ERP landscape, numerous modifications and in-house developments had made maintenance and expansion difficult. With S/4, many of these modifications became superfluous, as modern and extended standard functions are available. The conversion included the consolidation of master data and the introduction of a central business partner concept. By merging debtors and creditors into business partners, a uniform and consistent database was created. This facilitates data maintenance, reporting and analysis. Another focus was on optimizing the financial processes. The new financial architecture of S/4 enables real-time consolidation and reporting. Integrated financial planning and analysis now enables Desma to make informed decisions based on up-to-date data.
Sprint followed by long distance
The changeover to S/4 was just the beginning. The aim was to continuously implement further user stories and functional enhancements. New requirements are regularly recorded and integrated into the system landscape as part of innovation projects. This is done in close cooperation with the specialist departments. One focus is on improving usability. The use of Fiori interfaces makes operating the system more intuitive and user-friendly. Users benefit from a uniform and consistent user interface that makes it easier to access the information they need.
Desma plans to further exploit the possibilities of the S/4 platform so that future projects can include the integration of machine learning and AI. The use of IoT technologies to monitor and control the production machines is also planned. The successful S/4 transformation at Desma demonstrates the importance of early planning and experienced SAP consulting. By working closely with Abat and using SAP standards, Desma was able to optimize its internal processes and install innovative solutions for the footwear industry. This gives Desma the necessary flexibility and performance to meet the future requirements of the industry.
Here to the partner entry:
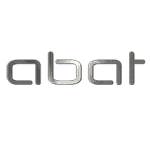