Finding the role of AI in the industry
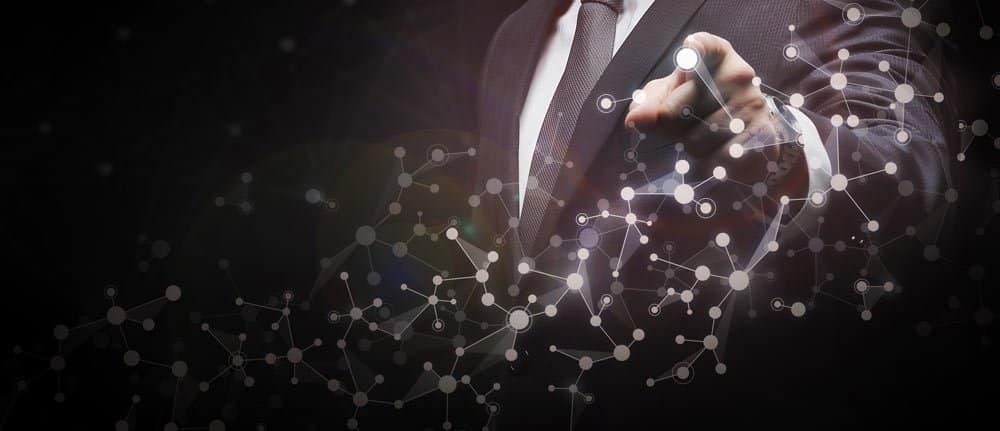
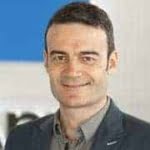
A self-organized and self-learning production hall is the declared target for Industry 4.0 - and ever new IT innovations are bringing it within reach.
A study by the Berlin Institute for Innovation and Technology commissioned by the German Federal Ministry for Economic Affairs and Energy shows that artificial intelligence has enormous potential for future value creation in the manufacturing industry.
For example, the use of AI is expected to generate additional gross value added of around EUR 31.8 billion for the industry in Germany within the next five years. This means that AI would be responsible for a good third of the expected total growth.
According to the study, AI applications such as predictive analytics, robotics, intelligent assistance systems, automation and sensor technology are considered particularly promising.
Predictive maintenance was the entry point to smart production for many industrial companies, but the need for automation and efficiency now prevails here.
This is the result of a survey conducted by data management specialist NetApp among 120 German IT experts from the healthcare, automotive, finance, and manufacturing industries.
It shows that AI is currently being used in the manufacturing industry primarily for the automation of repetitive manufacturing processes (robotic process automation, RPA) and for supply chain and warehouse management. This was stated by 66.7 percent and 60 percent of the industry respondents, respectively.
However, many companies are just at the beginning of their AI strategy: 46.7 percent of decision-makers in the manufacturing industry were in the first year of actively using AI at the time of the survey.
Other industries such as the financial sector are (still) a step ahead here. However, the manufacturing industry has a particularly high success rate in AI projects - so it has recognized the importance of AI for the future.
However, there are still some stubborn reservations standing between business and the next step in digital transformation: On the one hand, companies fear high costs for the holistic digitization of all production processes - precisely because this would also involve the modernization of outdated IT infrastructures. Costs would therefore be incurred on both the software and hardware sides.
The duration of such an implementation also contributes to the hesitant behavior. And as with all data-driven processes, there is of course the question of data protection, which will take on even greater significance than before once the GDPR comes into force.
However, many of these concerns can be eliminated or at least mitigated with the appropriate know-how. To bring the appropriate expertise in-house, manufacturers are pursuing several strategies.
For example, they explicitly target the establishment of an internal AI department, the targeted hiring of individual AI experts, and collaboration with external consultants and companies.
This is because, especially at the beginning of one's own AI strategy, the exchange with parties outside one's own ecosystem is important in order to avoid fundamental mistakes and omissions that would affect any subsequent projects.
In the medium to long term, however, the establishment of an in-house AI team is definitely advisable, especially to stimulate the internal exchange of knowledge and facilitate the integration of new employees.
Even though the next stage of digitization requires a high level of investment on the part of the manufacturing industry, this is a necessary step to continue the development towards the intelligent production hall.
The former flagship project Predictive Maintenance has now become the standard, and the task now is to integrate new technological innovations into the processes.
A methodical approach has so far enabled the manufacturing industry to establish itself as a testing champion and successfully integrate machine learning into production, customer support and quality assurance. So there is no reason why it should now stop at artificial intelligence.