Production planning with SAP
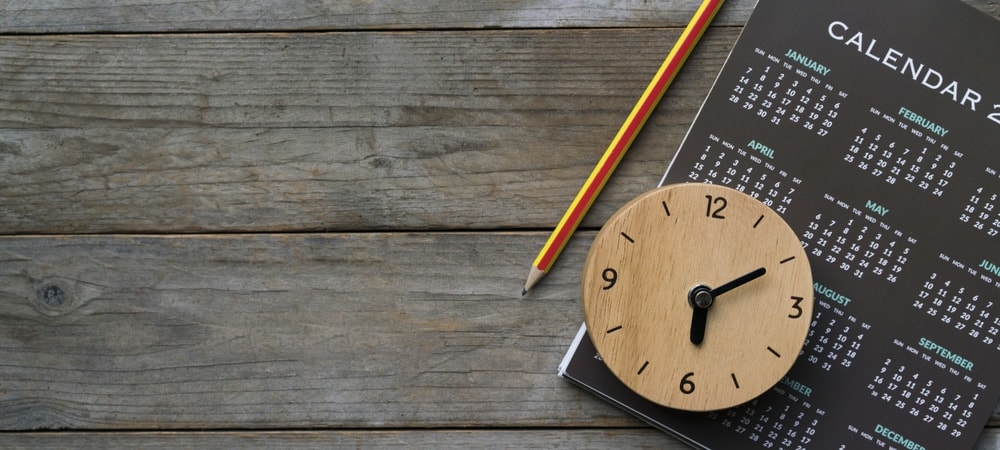
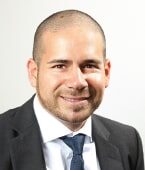
Corporate executives see business interruption as one of the biggest business risks. This is the result of a study conducted by insurer Allianz Global Corporate & Specialty (AGCS) in 2022. This puts the concern of a business interruption ahead of the fear of cyber attacks. RHI Magnesita, a leading global supplier of high-grade refractory products, systems and services, has also struggled with fluctuating demand and hard-to-source raw materials over the past two years. Headquartered in Vienna, Austria, the company produces more than 1.5 million tons of refractory products annually at more than 30 main production sites worldwide, which are used in high-temperature industrial processes above 1200 degrees Celsius - including in the steel, cement, nonferrous metals and glass industries. The products are manufactured in various multi-stage and complex processes. In order to be able to react flexibly to changes and to avoid bottlenecks and shutdowns, RHI Magnesita has decided to optimize its production planning at the operational level.
More efficient production planning is achieved with Production Planning and Detailed Scheduling (SAP PP/DS). In order to meet the constantly changing market requirements, demand and detailed production planning is to be further optimized. For this purpose, a worldwide template for the planning process was defined at RHI Magnesita and SAP PP/DS was implemented as Advanced Planning and Detailed Scheduling.
duling system introduced.
Planning and scheduling
With the PP/DS optimizer, a multi-stage production plan is created taking into account raw materials, bottleneck resources as well as tools. Production sequences can be created quickly, taking into account setup times as well as setup and delay costs, and in such a way that the production planner no longer has to intervene manually (customer's own heuristics). This saves the manufacturer time and effort. In similar projects, inventory costs have been reduced by around 10 percent, setup times by 20 percent, and the degree of delivery readiness increased to over 90 percent.
The main advantage, however, is that alert-based planning enables a flexible and rapid response to fluctuations on the procurement and sales side. This avoids bottleneck situations and prevents a shortage of raw materials. The basis for this was the close interlinking of the adjacent systems and a digital twin of production developed from this. The physical image of SAP PP/DS enables simulation models and provides real-time data for demand planning. RHI Magnesita can now view production quantities, machine states, power, quantities or even material consumption. This not only allows problems to be identified more quickly in real time, but also provides transparency about the actual situation and can be used as a basis for corporate decisions.
The implementation of a PP/DS is accordingly an important part of the overall context in the realization of modern production planning. However, it is important that the existing processes, systems and organizational structure are also taken into account and adapted if necessary. Finally, the acceptance of the tool is another key success factor. RHI Magnesita ensures all this through effective and smooth cooperation with SAP and MHP.
