Process transition from ERP to MDM
![[shutterstock: 622306598, m.mphoto]](https://e3mag.com/wp-content/uploads/2020/12/shutterstock_622306598.jpg)
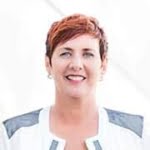
Master data management of static basic data or reference data on objects relevant to operations, such as customers, suppliers, materials, employees and finances, is one of the essential tasks of today's corporate management. The example of SAP's existing customer KTM in Austria shows how effective management of material master data improves data quality and data governance.
KTM is a premium manufacturer of high-performance motorcycles for off-road and on-road use. The company develops and produces motorcycles under the KTM, Husqvarna and Gasgas brands, of which more than 280,000 vehicles were sold worldwide in 2019, as well as the X-Bow super sports car. With a turnover of 1.5 billion euros, KTM has become the largest European motorcycle manufacturer, and the group employs around 4000 people worldwide.
In 2016, KTM introduced the ERP from SAP. This involved partly migrating existing material master data - which was over 20 years old - and partly creating new material master data. The quality was initially "quite sobering," as Patrick Berger, Head of Master Data Governance at KTM, notes. The status of articles and materials that were to be used in production was often not correct. Individual fields were maintained - or not. In addition, translations of material designations were missing, or they were in the wrong language. In sum, these data quality problems also affected production and sales processes.
Since decentralized maintenance of master data was desired, a solution was needed that would enable workflows and better verification of the data entered. To this end, a master data initiative was launched in 2017. Together with the departments, the processes were analyzed: Who maintains which data and why? At what point in time? What possibilities are there for a clean organization of the workflow?
Many cooks spoil the broth
One problem was the large number of people who could maintain the (material) data - at least in theory. This number should be reduced significantly to the necessary minimum. In addition, it should be determined which area is responsible for which steps in master data maintenance. In addition to the reduction of users and authorizations as well as the distributed maintenance of material master data by the relevant departments, mass data maintenance was one of the central issues - aftermath of the SAP implementation and the associated migration.
"We kept coming across a lot of items that required a process in SAP that didn't exist before." Berger explains.
Another example would be operating instructions for the models of the new model year. For this, several hundred to several thousand materials would have to be created, all of which are basically the same or differ only in details.
On the part of KTM, there was a desire to provide Excel maintenance, with the help of which the employees in the material warehouse could make all information available via Excel. After uploading, quality assurance should take place, just as if the data were maintained manually. In addition, templates were to ensure that "uncontrolled growth" did not occur again when creating material master data.
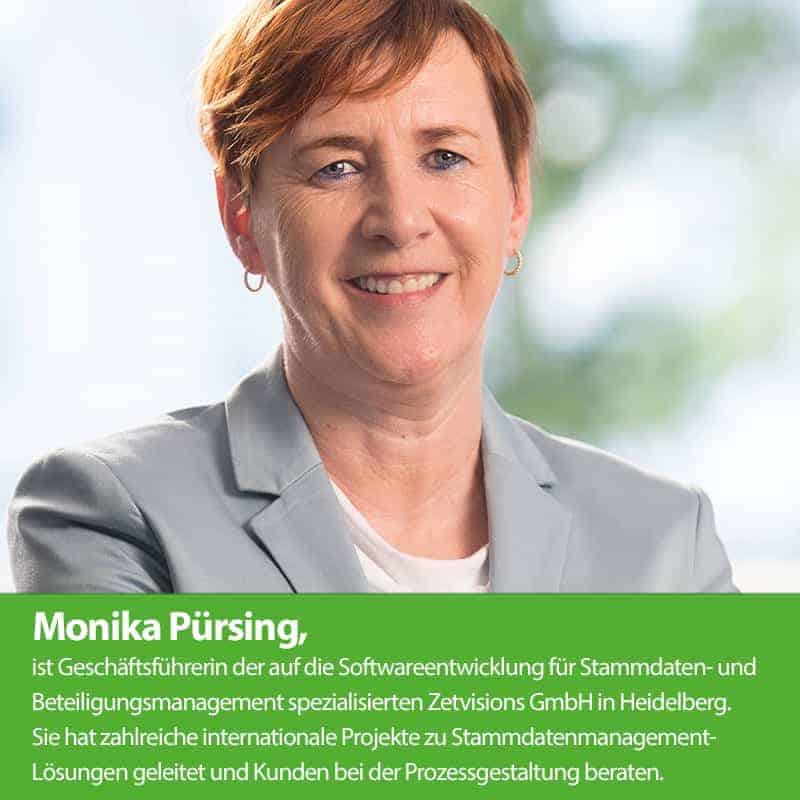
Who, what, when and how?
One important point was to move data sovereignty to the MDM software, i.e., to lock the transactions in SAP for creating and changing material masters for all "normal" users. The focus for material creation was on templates. Even before the introduction of the new software, KTM had defined templates for materials that were created in SAP with a specific number; moreover, with rudimentary data that should be transferred to a new material as exactly as possible.
A completely free material installation was not planned. For a new material, the existing template of an existing material had to be used. The template material was also defined in the new software. The user receives predefined values for the material and only has to make adjustments at certain points.
This means two things: convenience and data quality. On the one hand, the templates should relieve users of as much work as possible, and on the other hand, they should not even release as many data fields as possible for maintenance, which can be filled by default anyway, in order to achieve quality improvements. On the one hand, the approach via templates has led to a relatively large number of processes being mapped. On the other hand, it can be controlled much more precisely.
For example, it can be specified that a template may only be changed by the central MDM unit - and not by everyone. The maintenance of material fields in the three-digit range - based on the template materials - has been simplified. Among other things, the maintenance of data from the various sales organizations and plants (storage locations, storage types, warehouse numbers) can be carried out more centrally.
In the validation rules for safeguarding data quality, dependencies on each other can also be displayed in addition to purely mandatory fields. For materials, for example, a check is made before a process step as to whether a purchasing info record already exists; the next step is only possible if this data record is available.
MDM authorization concept
With the introduction of the new MDM software, authorizations were blocked where necessary. All materials are created via the defined processes; all departments (research and development, materials planning, purchasing, finance) maintain the data in the new software. Approximately 180,000 materials with an average of ten to fifteen plant records each, 60 plants and 50 sales organizations as well as 200 classifications with seven material classes are managed in it.
70 users work in the system every day, around 100 processes and 140 validation rules are in use. A separate process has been defined for each template, including region-specific ones, i.e. for America, Europe, etc. Users select the right process and thus automatically have the appropriate template. Each process also includes the option to "jump" directly to additional data, for example to maintain prices or special MRP data.
The software can be used to control who is allowed to change templates (by adding the respective process to the individual permissions). Changes can then be checked again in master data management. However, KTM does not have a central office that releases data. Some (administrative) process types allow more freedom, more flexibility in master data maintenance.
They also still run via the MDM team. In contrast, the MDM team is not involved in the standard processes for material creation and maintenance. It is validated "beforehand", otherwise KTM relies on the users having the correct information and recording it accordingly. Of course, the new technical solution also helps to improve data quality, but just getting to grips with the processes and the system has led to "us finding a lot of skeletons in the closet," Berger sums up.
In addition to a shared understanding of the requirements of the business departments, the MDM team and the software service provider, the lessons learned include the early involvement of the responsible business departments. According to Berger, it is not easy to find the departments that are involved in the relevant processes. In addition, there are regularly "sideshows" that are not even thought of at first. This also applies to processes that are not run through on a daily basis and in which someone is involved who is not otherwise involved.
The early demarcation between the MDM software and SAP ERP proved to be an important issue, i.e., which data (prices, etc.) should be maintained in the master data software and which in SAP ERP. In this context, it is important to ensure the data sovereignty of the MDM solution. For this purpose, it must be defined at field level which is the leading system.
"Finally, non-functional requirements, such as usability and performance, should always be kept in mind. These are often neglected in the beginning, cautions Berger.
Customer-specific developments were replaced as part of a system update in spring 2019. Furthermore, in the first half of 2020, KTM expanded the use of the now established material master data solution for another domain: customer master data.

Validations
The MDM software also ensures validations during process transitions so that it is not only recognized at the end if something did not fit "up front". The main advantages of the new solution for the management of material master data are:
- Fewer users allowed to maintain/change material master data
- Good user acceptance through guided processes
- Greater transparency about data maintenance and the status of the data
- Shorter processing times until a material is fully maintained
- Easily and flexibly expandable system for validations and processes, for example