Celonis - Process Mining
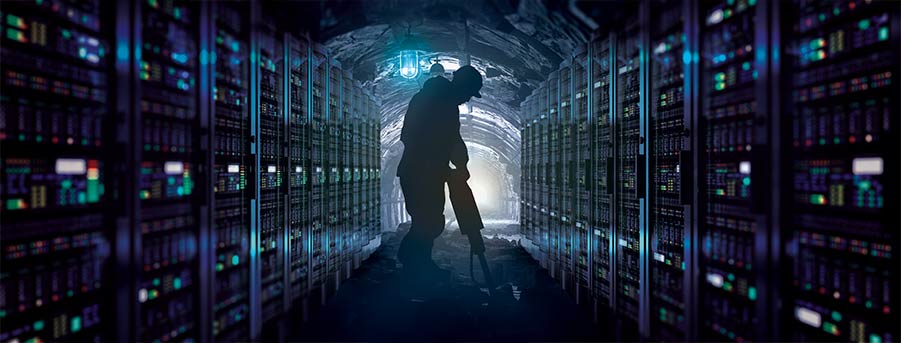
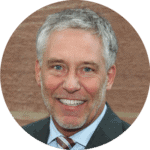
In order to understand and optimize business processes, it is necessary to unearth the treasure trove of data in companies. Celonis Process Mining takes advantage of the digital traces that almost every transaction leaves in the global IT systems of the company.
The idea behind it: Understanding the actual business processes brings clarity, transparency, agility and solves conflicts and bottlenecks in the organizational and process structure.
What data mining is for the data analyst and BI expert, process mining is for management.
Quality tool
Process Mining analyzes and visualizes the business processes. This makes it a quality tool that supports SAP's existing customer in terms of efficiency and agility.
Unlike the purely quantitative improvement of a faster Hana system, Celonis is focused on quality improvement - a bad system that merely runs faster after a Hana and S/4 upgrade is still a bad system.
Celonis offers SAP existing customers a completely different approach: The processes are analyzed. A visual representation illustrates the optimization potential.
The goal is transparency, harmonization, efficiency and agility.
In the first approach, process mining sounds like magic:
How can you visualize and find vulnerabilities of something you don't know?
At first glance, every ERP system is a black box, right?
"That may be true for the time before process mining"
"Access to systems and data was often only possible via detours. Long waiting times and cumbersome access paths not only frustrated employees. They also made it impossible to make the kind of responsive, flexible decisions that agile companies need to make today.
With our technology, we've made this treasure trove of data accessible - in a simple way that anyone can understand."
Digital forensics
For the existing SAP customer, this is the first opportunity to map processes exactly as they actually run.
"This involves collecting the digital traces that every transaction leaves behind and transferring them into an image, i.e. visualizing them"
explains Bastian Nominacher.
The weak points result from this very analysis:
"You can see at a glance what's really happening and get right into root cause analysis"
he knows from numerous very successful deployments of Celonis software in the meantime.
Classic methods for error analysis quickly reach their limits. They may be able to determine that a process is not being handled optimally. However, they often do not provide any information on why these bottlenecks occur in the organizational structure and process organization and how exactly the individual processes are interlinked.
"Process Mining from Celonis, on the other hand, has no limits here. With our technology, we are able to use and evaluate even enormous data sets with millions of process instances."
Nominacher emphasizes the difference to traditional analysis tools.
"One of the really nice aspects is the 'aha' effect we so often see. The insights gained from our process analyses are often very surprising for customers."
reports the Celonis co-managing director in an E-3 interview, and he explains what may be new here for an existing SAP customer:
"Many people suspect that there is a problem in a particular process or area. But for a long time, it took a lot of effort to find concrete evidence for this assumption.
Also, the causes of detours or delays may be in a completely different place than first suspected."
With Celonis, you can see at a glance where the actual process deviates from the target process and how this deviation affects the efficiency of the entire company.
If, for example, orders or invoices are reworked manually or orders are placed too early or too late, efficiency is quickly over.
Without deep interventions
Questions that are probably on the minds of every SAP manager:
Which default settings are necessary and how deeply does the Celonis software intervene in the ERP system - which authorizations are required?
"There is no need to dig deep into the ERP system"
Bastian Nominacher gives the all-clear, because Celonis uses a variety of standard connectors for a company's core processes.
The connection to SAP thus works quickly and smoothly.
"If you process data directly on the productive Suite-on-Hana or S/4 instance, you also save on replication, additional hardware, etc., and can apply process mining directly in real time to all SAP processes"
Nominacher explains.
The principle of positioning specialized connectors and software agents at specific points in the system is not new. In system monitoring and especially in network monitoring of wide and local area networks, agents are a lived reality.
Until now, however, no one had the idea of applying this technology to business processes and business organizational structures and workflows.
Celonis is an absolute pioneer in this field and therefore it took some time and hundreds of emails to convince even SAP.
Another important question for the CIO and CCC leader:
When Celonis software goes looking for vulnerabilities, does the performance of the production system suffer?
Here, too, Bastian Nominacher can give the all-clear:
"Celonis Process Mining runs in the background and is optimized to have no impact on production system operations."
And the CEO and CFO may be wondering:
Can certain processes and functions in an ERP system "hide" from the Celonis software? Are there blind spots?
"Blind spots only exist in the case of media breaks when the process is continued manually"
Nominacher explains.
As soon as a process runs digitally, it leaves traces. Process mining requires only three components in the event log: a timestamp, an event identifier (for example, "Pay invoice"), and a case key such as the invoice number.
"Our process mining technology works independently of the actual implementation of the process logic. The only thing that matters is which traces, i.e. database entries, are created. From these traces, the process mining algorithms can reconstruct the process flow.
If a customer has created tables in the Z namespace, these must be registered once, i.e. made known to the system as an event source - and can then be processed further without any problems."
Abap and Java vulnerabilities
And does Celonis also find vulnerabilities in the Hana database functions that are programmed out in Abap or Java? And in the NetWeaver Java stack?
"Celonis identifies process variants based on digital traces, i.e. entries in tables, at the database level.
This method has the great advantage that it is completely independent of the underlying stack.
Whether Abap or Java stack, process mining technology can be applied unchanged to gain process transparency"
the Celonis co-founder once again describes the basic system function.
Thus, for Celonis, an SAP system is like a transparent patient?
"Patient may not be the right word"
says Bastian Nominacher
"but in fact we can pull all the data relevant to the process flow from SAP."
There is also no difference between on-premise and cloud systems:
"No, for us it is only important that we have access to the system. Where the data is located is absolutely secondary.
In the case of cloud systems, it is often possible to establish data access even more quickly, as the providers already offer appropriate interfaces."
Nominacher knows from his professional practice.
"Of course, there is an incredible amount of human intelligence in Celonis: a large team of developers and architects have done and are doing their best here.
In addition, the latest knowledge from artificial intelligence was applied"
knows the Celonis co-managing director.
Celonis Pi (Proactive Insights), the latest generation of process mining, aims to set the standard in combining artificial intelligence (AI), machine learning and process mining.
"Celonis Pi correlates millions of process-related data in an extremely short time - and it does it with state-of-the-art machine learning techniques"
says Nominacher.
"The result is thought from the user's perspective: the sticking points in a process are automatically identified.
This eliminates a lot of analysis work for the user. Better yet, Celonis Pi learns along the way and makes suggestions as to which measures might be successful."
In the past, the cause of a faulty and inefficient SAP system was investigated by the company's own IT team together with the CCC manager or by an external consultant from an SAP partner.
Will Celonis software make this expertise obsolete?
"Not at all." answers Bastian Nominacher, "with Celonis Process Mining, weaknesses and inefficiencies in processes are uncovered. The insights enable teams and IT admins to focus on their core competencies and the optimization of the analyzed processes.
So the software helps to work more efficiently and leads to enormous time savings. Thus, Celonis primarily helps companies to work more agilely and improve customer satisfaction."
Accordingly, who is the contact person for Celonis in a company? Who investigates the causes?
The SAP base, the CCC manager, the CIO, CFO?
"It all depends on the company"
"Our tool is open to users at all levels, and that's what makes our work so exciting!
In our opinion, there is no point in offering analytics solutions only for a handful of specialists. Everyone needs to be able to look at their process and optimize it.
At Celonis, we rely on an intuitive solution that can be used across departments and for all processes. You don't need any special IT knowledge to use it - but a bit of process knowledge is certainly an advantage."
And then the result:
What is the result of a root cause analysis at an existing SAP customer?
Adaptation of the customizing, optimization of the Abap code and/or the Z-functions? Or change in the organizational structure and process organization?
"This is a difficult question"
says the Celonis inventor to the E-3 editor-in-chief.
"It all depends on what problem the customer has identified and what their starting point is.
All of the measures you mention can be the result of a process mining analysis."
Practice often shows that it is a combination of technical and organizational measures. What is really helpful is that the success of the measures can be seen immediately due to the live connection of the data.
"If a particular measure does not have the desired effect, you can counteract it. If the approach works, it is worth rolling it out broadly within the organization".
Nominacher recounts from his practice with customers.
"It's this shift in thinking - away from big-bang optimization and toward fact-driven, continuous process optimization - that makes our customers so successful and is the reason for sustainable process improvements."
It is always up to those acting to decide what measures to take, but of course identifying weaknesses can and should bring about change.
These changes can take place in all areas, in technology or in the organization.
"We only offer companies the prerequisite"
Nominacher defines and explains:
"This means comprehensive insight into processes, indications of the causes and even recommendations for action.
What's more, with Celonis you can see almost in real time whether a measure is taking effect, and you can readjust if necessary."
The added value of the efforts turns out to be quite different for the existing SAP customer:
"The great thing about our technology is that processes in all areas are made transparent and visualized - and so the benefit is always elsewhere.
In purchasing, for example, the focus is more often on organizational benefits; in production, the focus is more on technology. Our technology gives customers real-time insight into processes and complete visibility into their operations, and almost always results in an extremely fast ROI."
Celonis customers confirm it: In many cases, the investment pays off after only half a year.
BPMN exports
For many existing SAP customers, SolMan, especially the latest version 7.2, has established itself as the central platform for documenting business processes:
To what extent can the results of the root cause analysis be transferred to the ERP documentation and the BPM of SolMan?
"The process patterns identified using Celonis Process Mining can be exported as BPMN models and thus transferred directly into process documentation. Either to create them from scratch or to add to and update them."
Bastian Nominacher describes a solution for existing SAP customers.
Currently, there is no automatic, bidirectional interface between Celonis and SolMan. However, extracted process models can already be exported as BPMN models from Celonis and processed directly.
Via Pi Conformance it is possible to load existing business blueprints into Celonis and thus directly identify deviations from the lived processes.
"Machine learning algorithms help identify causes and possible solutions for such deviations"
Nominacher adds.
And the final questions:
Where does Celonis still need to act in the future? What's next? What is the importance of Machine/Deep Learning for Celonis? What else can existing SAP customers expect from Celonis?
"We are continuously working on our solution and developing it further. I am firmly convinced that there is still a great deal of hidden potential in the process data.
Celonis Pi was a quantum leap for us - especially with the use of the latest algorithms from the fields of AI and machine learning.
We are very proud of what we have achieved. But of course we are constantly developing - SAP customers can expect some more innovations!"
Bastian Nominacher explains at the end of the E-3 conversation.