NETZSCH implements uniform and interoperable store floor platform
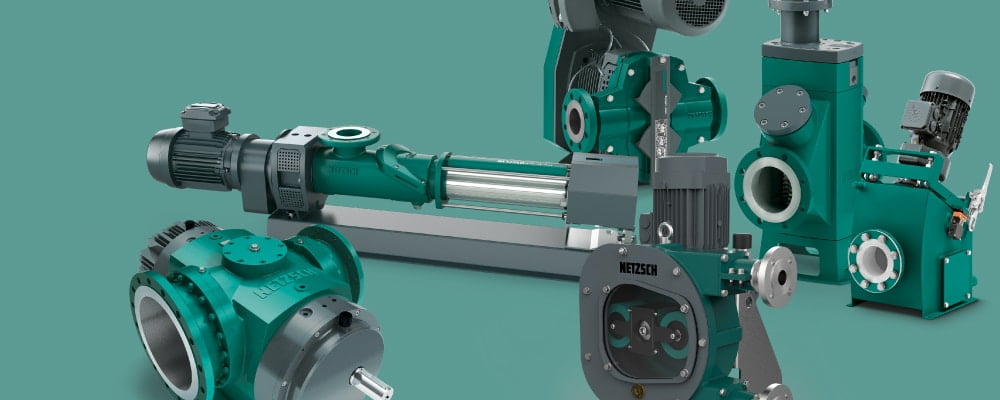

At its heart is the ORBIS Distributed Shopfloor Processing (ORBIS DSP) solution, which works interoperably with all applications. Virtually nothing moves without rotary positive displacement pumps - neither in the oil and gas industry, the environmental and energy sector nor in the food, pharmaceutical, chemical and paper industries or in mining. The pumps are needed to treat waste water, pump oil and gas, lubricating and hydraulic oil, sewage sludge, explosives or highly viscous substances containing solids, or when unloading crude oil.
Leading specialist for positive displacement pumps
NETZSCH Pumpen & Systeme GmbH is a leading specialist in the development and manufacture of these pumps. The company from Waldkraiburg in Upper Bavaria produces around 60,000 of these devices every year, from screw pumps to rotary lobe and progressing cavity pumps to peristaltic pumps tailored to specific customer requirements.
NETZSCH Pumps & Systems is part of the NETZSCH Group, which is also active in the Analyzing & Testing and Grinding & Dispersing business segments and employs over 4,000 people in 210 sales and production centers in 35 countries. Combined under the umbrella of a holding company, the individual divisions operate independently in order to offer each customer the best possible solution. The company relies on constant innovation, excellent performance in all areas - keyword "Proven Excellence" - and digital services in order to maintain and expand its leading position on the market and increase the value of the company.
Store floor digitization with an interoperable platform
However, key factors for continued success on the market are also the digitalization, standardization and sustainable optimization of processes in production and at a business management level. The pump manufacturer has already laid the foundation for this in commercial processes with the system conversion to the SAP S/4HANA platform, on which the existing ORBIS MES can also be used. This has laid the foundations for the introduction of a modern, future-proof, standardized, scalable and, above all, interoperable store floor platform in the production and logistics area that can be used at all production sites worldwide.
"The development and implementation of this platform was of strategic importance. It enabled us to establish digital, paperless and inter-operable processes on the store floor from a single source, covering everything from maintaining parameters with production specifications, order processing and machine control to reporting key production figures," says Andreas Freiberger, SAP Inhouse Consultant at NETZSCH. The new platform from ORBIS replaces a locally installed proprietary legacy solution for ME and QM processes, parameter maintenance and reporting, which could not be connected directly to SAP's ERP (SAP S/4HANA or previously SAP ERP) and whose support is no longer guaranteed as it is not being developed further.
ORBIS DSP ensures interoperability
The store floor platform combines on-premises and public cloud solutions: the SAP-based ORBIS Manufacturing Execution System (ORBIS MES), which integrates seamlessly with SAP S/4HANA and was already in use in some areas of stators production, with a low-code app based on the Microsoft Power Platform for creating and managing the production specifications and the Azure IoT platform. Process data from the machines is stored there and analyzed using Microsoft Power BI. At the heart of the platform is the ORBIS Distributed Shopfloor Processing (ORBIS DSP) solution, a functional extension that ensures interoperability, i.e. the smooth interaction of the individual applications. The innovative application from ORBIS SE consists of a stand-alone EDGE component and the SaaS cloud-based management system ORBIS DSP.
Cockpit.
The EDGE component of ORBIS DSP is the local instance for the standardized connection of the production machines. The complete administration of the locally used services takes place in the cloud-based management cockpit, i.e. the mapping of the organization (plants and machines/systems installed there) and the configuration of the data and process flows. The cockpit therefore regulates which data flows into which applications and processes, whether in Waldkraiburg, in the USA or in Asia.
Entry into digital, paperless production
Six machines for the production of pump stators are currently connected to the inter-operable and scalable store floor platform. With their help, order processing has been optimized and significantly shortened, and production control has been made noticeably more efficient. This was possible, among other things, because ORBIS MES interacts perfectly with ORBIS DSP and SAP S/4HANA to reliably guide the workers through their tasks with dialog support. The platform also enables the reporting of key production figures at product, machine and location level. All processes can be carried out digitally throughout, i.e. without manual intermediate steps and therefore without system and media disruptions.
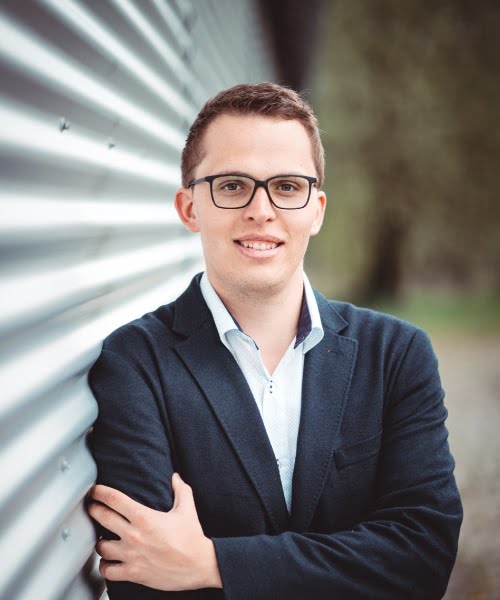
We combine SAP, Orbis and Azure cloud applications to create a hybrid platform for digital store floor management.
Andreas Freiberger,
SAP Inhouse Consultant,
Netzsch
In practice, this works as follows: The parameters for the machines used to manufacture the pump stators are maintained and saved in the Microsoft Power App. Depending on the production material, the specifications/conditions that a machine must fulfill, for example with regard to its horizontal and vertical position, pressure or temperature, are defined so that the production process can start. If the values correspond to the specifications, the worker approves them in the app and the parameter sets are transferred to the EDGE component of ORBIS DSP.
The relevant production orders are created in SAP S/4HANA. The EDGE links the FAUF from SAP with the associated parameter sets, which are loaded from the cloud, and triggers the setup of the machine. As soon as this process is complete, feedback is sent to the MES, which starts production via the EDGE. If a machine indicates that production is complete, this information is transmitted to SAP S/4HANA via the EDGE component and the MES and the production order is completed there.
But that's not all. The downstream inspection of the stators in the measuring room, which is carried out on the basis of inspection lots, is also processed via ORBIS DSP. The solution records the measurement results and transfers them to the actual values of the relevant inspection characteristics, which are stored in the SAP inspection lot.
Process data analysis in Power BI
The process data generated by the machines on set-up and production times, as well as production parameters such as pressure, temperature and speed, flow into the Azure IoT platform via EDGE. They are stored there and evaluated in detail using the Power BI analysis tool. This enables efficient reporting of key figures, which can provide information on optimization potential in production, for example in terms of set-up times. In addition, the stored process data and production parameters can be used to fully trace the way in which a stator was manufactured (traceability). This is an important aspect in terms of product liability and an essential part of quality management.
Implementation with a proven IT partner
ORBIS SE, which has already implemented several SAP projects at NETZSCH, including the system conversion to SAP S/4HANA, was commissioned to implement the new store floor platform. The international IT service provider has extensive expertise in relation to the store floor and offers a portfolio of solutions ranging from EDGE and ORBIS MES to Power Platform, Azure IoT and Power BI.
Thanks to the collaborative partnership between the ORBIS and NETZSCH project teams, the extremely demanding project was completed quickly. The development of the power app for creating, storing and maintaining the parameters with the production specifications and the transfer of a large amount of legacy data, process data and measured values to stators in a wide variety of formats and their harmonization posed particular challenges. The ORBIS experts used the Azure Data Factory data integration service for this.
ORBIS was also commissioned to redesign and implement the entire material flow in SAP in the new production hall in Waldkraiburg, which includes the assembly plant and the fully automated high-bay warehouse for pump components: from the connection of automatic pallet and small parts warehouses to the supply of production via tugger trains.
Andreas Freiberger is satisfied with what has been achieved so far: "We are combining solutions from SAP and ORBIS as well as Azure-based cloud applications to create a modern, hybrid platform for digital store floor management. ORBIS DSP is the central building block that ensures the interoperability of the individual applications and choreographs the data flows."
But this is just the beginning: a further six machines are to be connected step by step to the platform, which is constantly being improved and further developed. There are also plans to roll it out to other locations, including internationally, and it has already started at the new plant in Asia.
