Knowledge platform: Maintenance and servicing of plant and machinery
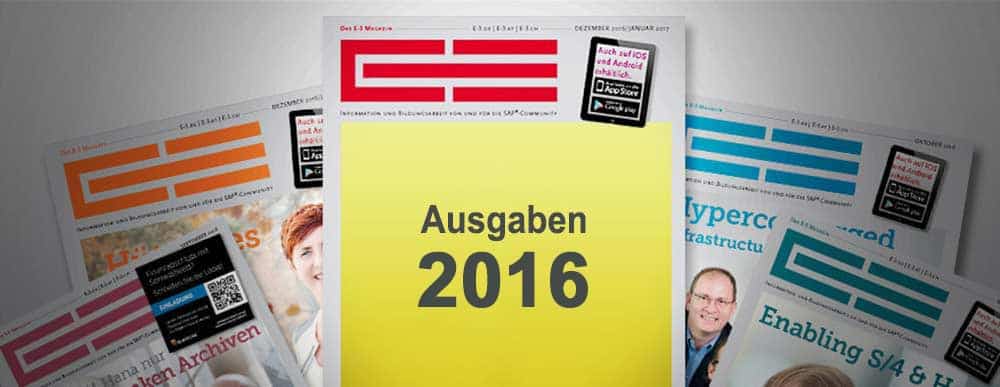
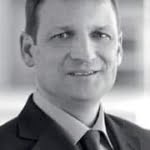
Frequent queries with colleagues, multiple trips to the customer, spare parts problems or lengthy service calls are the result. The integration of a knowledge platform into the mobile application of field service technicians can remedy this.
The customer service center of a construction equipment manufacturer receives an urgent call from its customer's site manager. A dump truck is emitting blue smoke, oil consumption is increased and the truck is no longer fully functional. If the dump truck were to break down, a road construction project would be delayed - with high financial losses.
Customer service or the service desk records the fault report and creates a ticket or service order in the SAP ERP or service management system. The internal service employee uses a central knowledge platform to decide whether he can help the customer himself or whether it is necessary to send a technician to the site.
An order is created from the ticket for the technician deployment, which is transferred fully automatically to the central scheduling system. Based on the qualifications stored in SAP HR, the system suggests to the dispatcher a list of suitable service technicians who are available at the right time and in the vicinity of the deployment site.
He can also schedule other resources such as special vehicles, equipment or material. The technician then receives the new order on his tablet or smartphone via a mobile application such as mobileX-MIP for Field Service.
In addition to the type of fault and the deployment address, this order contains information such as the deployment history, object data and material reservations. The route optimization also ensures the shortest route.
Knowledge for more efficient service
But the technician who is most familiar with the system or already knows the solution from his own experience is not always available. Then it is an advantage if the mobile application is integrated with a knowledge platform such as Empolis Smart Service.
The technician has access to the knowledge platform on site, online and offline. This automatically evaluates the existing structured and unstructured order data, such as vehicle type, year of manufacture, performance data, model designation, the fault description in the form of operation short or long texts and message data, and then offers three different support options.
On the one hand, the technician receives a list of relevant documents, such as the repair manual with a link to the exact text passage. In addition, the system offers decision trees that lead to the correct solution via selection questions. Via case-based reasoning, the knowledge platform also determines solution descriptions that only have similarities to the problem case at hand, but can also lead to the solution.
For example, starting from a fault description such as "blue smoke" on a K1 tipper truck, a technician can find solutions such as "change the oil," "clean the contacts," or "change the turbocharger" within seconds, as well as two decision trees on the topic and a document from the knowledge platform with instructions for "renewing the crankcase ventilation.
If the query does not provide the solution in the first step, the user can vary the search parameters. For example, he deletes the model designation to increase the hit rate and searches the database for further information.
The system recognizes that a decision tree is the best match to gradually narrow down the cause of the problem and starts the decision tree immediately. The technician follows the system's recommendation and clicks on the answer "Lack of power".
The decision tree guides the technician step by step. First, the fault memory is to be read out, which determines the fault code 4721. In the next step, he checks the pressure control valve and detects a defective diaphragm.
The solution is to replace the pressure control valve, which the technician performs according to the instructions in the corresponding document from the knowledge platform. After completing the job, the technician sends the data back to the mobile application to solve the malfunction.
The knowledge record is saved as a solution document on the job and can be used as an activity log for creating the service report. In addition, it can be stored in the knowledge platform, where it is available for future repairs and service calls after review by development or a specialist.
Via the mobile solution, the technician reports back to dispatch that he has successfully completed the job and creates the service report with all services such as travel costs, times and material consumption.
The customer acknowledges this PDF service report on site with a digital signature and also receives it by mail. The report is transferred directly to the back office via the mobile connection and archived, for example, as an SAP CS order.
Together with the feedback, it is used by the office staff for further processing - such as an optional review by the service manager - as well as for creating the invoice.
Digitization of the service process
The combination of IT-supported deployment planning and mobile connection of service technicians with a knowledge-based software platform maps the service process completely digitally from start to finish.
Operational and technical efficiency can be significantly increased as a result. Expert knowledge is thus no longer available only to individuals, but accumulates in a central knowledge platform for all technicians that is constantly growing.
For corporate service processes, this means shorter repair times, fewer callbacks to colleagues, less downtime for equipment, and broader deployment options for service technicians.
This results in higher customer satisfaction and service quality as well as optimization of the entire service process. It sounds sensible and economical to store knowledge centrally and make it retrievable on any device in a decentralized manner. But what is the investment and, above all, the effort involved?
As with all projects, an analysis phase should take place in advance. Not every company is equally suited to the introduction of a knowledge platform due to its internal processes and requirements. For this reason, companies are best advised to check the cost-benefit ratio for their processes on the basis of a test setup.
In terms of the procedure, the actual introduction differs little from a conventional IT project. However, it must be clear that even after the successful introduction, there will still be a manageable maintenance effort.
The crucial difference, however, is that - apart from decision trees - the manual, editorial effort is completely eliminated. A knowledge platform eliminates the manual maintenance effort of the actual content and shifts the manual effort to the meta level. This means a significant cost advantage.
Licenses & Infrastructure
Accessing third-party systems to extract data from them is useful and necessary. Such data silos can include file system, databases and also backend systems such as SAP.
Whether and in what form additional license costs are incurred here is difficult to answer. All the more so as the topic of indirect use has increasingly taken center stage in recent months. SAP must provide the answer to this question itself.
This leaves the question of infrastructure investment, i.e. how much hardware does such an application need? The good news is that here, too, the trend toward the cloud has already taken hold.
A knowledge management system can therefore be sourced from the cloud, while the data remains within the company. This takes account of the security and confidentiality aspect. And for all companies that do not (yet) want to or cannot move to the cloud, a knowledge platform is also available as an on-premise solution.