Industry 4.0 and the intelligent interaction between ERP and MES - but how exactly?
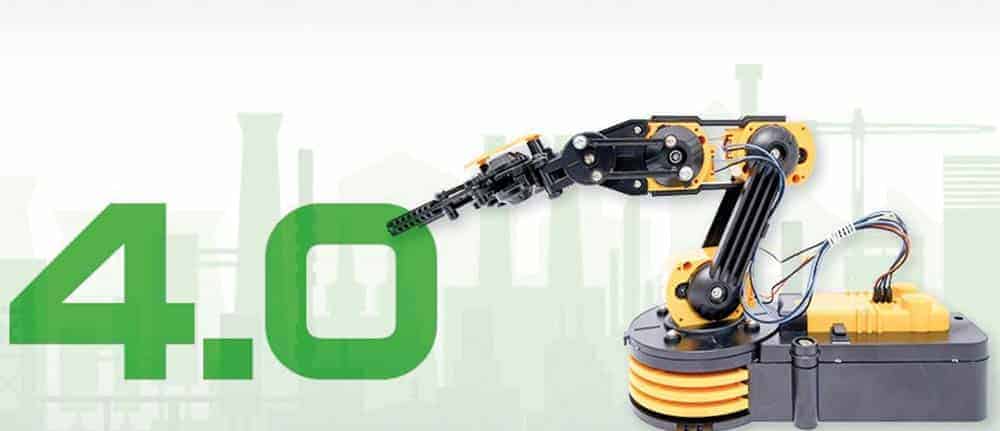
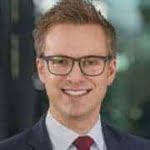
Industry 4.0 is generally understood to mean the real-time, intelligent, horizontal and vertical networking of people, machines, objects and ICT systems for the dynamic management of complex systems. 1
In this context, horizontal networking refers to the integration of the various IT systems for the different process steps in production planning and control, between which a flow of materials and information takes place.
This applies both within a company and to several companies along the entire value chain. The integration of IT systems at internal company hierarchy levels of the automation pyramid (company management, plant management, process management, control and field level) is summarized under vertical networking. ²
The digital networking of the physical production world with the digital planning world should therefore enable autonomous control of production and increase transparency in all processes.
However, this presupposes that planning reflects or predicts the reality in production as realistically as possible and that production control reacts quickly to deviations at the same time.
To this end, conflicting goals, resource bottlenecks and (short-term) disruptions, among other things, must be taken into account as part of the planning process. At the same time, control must take place in real time to avoid delays in initiating measures in the event of deviations from the plan.3
Consequently, one of the key qualifications is a systematic IT landscape to use data for information bundled as a basis for decision-making. Only an efficient IT system landscape that is as uniform as possible, yet specified for each company, can sustainably support the far-reaching, structural change processes and guarantee the synergy effects of internal specialization (vertical networking) and intercompany cooperation (horizontal networking) in the long term.⁴
This sounds simple, but it poses enormous difficulties for decision-makers about investments in IT systems. The main reason for this is that the decision-maker may not be aware of the clear definition of functional responsibilities in the direct interaction between IT systems.
In the past, ERP systems in particular have proven their worth as a central planning and control instance at the corporate management level. They will continue to play this role in Industrie 4.0.
However, one problem of ERP systems is the lack of a bridge to detailed production control. This problem is to be solved by the use of Manufacturing Execution Systems (MES), which often allow a more precise, because more detailed detailed planning and control through an integrated detailed planning logic and offer better real-time capability.⁵
However, it is not possible at this point to clarify for which companies which IT systems must necessarily be in place on the path to digital networking.
There is a lack of user-friendly, unambiguous decision support here for assigning cross-system, functional requirements to best support business processes.
The lack of such a basis for decision-making often leads to barriers within companies when it comes to fundamentally changing legacy IT structures. Remaining with outdated IT architecture leads to decisive competitive disadvantages in the medium term.
This state of affairs, which clearly jeopardizes the goal of Industrie 4.0 - the digitization of the economy - must be assessed as critical and remedied by means of suitable, collaborative approaches to solutions from research and practice.
1: Bauer, W.; Horváth, P.: Industrie 4.0 - Volkswirtschaftliches Potenzial für Deutschland. In: Bitkom 27 (2014) 8-9, pp. 1-46. 2: Kletti, J. (Ed.): MES - Manufacturing Execution System. Modern information technology supports value creation. 2nd ed. Springer Vieweg, Berlin [et al.] 2015. 3: Sontow, K.; Blum, M.: ERP oder MES - Wer führt bei Industrie 4.0 das Zepter? In: IT-Matchmaker (2015), pp. 1-3. 4: Termer, F.: Enterprise Resource Planning auf Wachstumskurs. 5: VDI/VDE-Gesellschaft Mess- und Automatisierungstechnik (GMA) (ed.): Cyber-Physical Systems: Chancen und Nutzen aus Sicht der Automation (2013), pp. 1-12.