Predictive Maintenance - Giving Meaning to Data
![[shutterstock.com:559228975, Zapp2Photo]](https://e3mag.com/wp-content/uploads/2017/02/shutterstock_559228975.jpg)
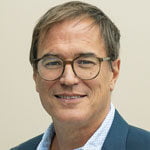
In the Internet of Things, condition data from machine components flows and is ultimately combined with information from third-party systems such as ERP applications from SAP.
This makes it possible to identify conspicuous patterns indicating disorders in good time and to initiate preventive measures.
This reduces the costs incurred by production stoppages, contractual penalties and compensation measures. In addition, the production throughput is shortened and delivery dates can be determined and met more precisely.
Application example
A typical application example for automation based on Internet technologies is a service in engine production that monitors quality in manufacturing.
For example, an auto manufacturer produces thousands of cylinder heads in manufacturing processes ranging from mold making to metal casting and finishing.
During production, a data record is created for each cylinder head, collecting details of the manufacturing process across all stations. The automated production environment records process parameters such as times, dimensions or temperatures in real time.
The production control system then compares this data with the target values and can thus provide initial indications of any deviations, but cannot yet offer a solution for correcting the error.
In such a scenario, huge volumes of data are generated, and experienced specialists are needed to evaluate them manually. Only they can draw the right conclusions based on the raw data supplied.
A solution for data analytics creates more transparency here, provides clear statements on the production process and reveals new correlations that lead to accelerated error analysis.
For this, however, all relevant measurement data from the production process must be permanently collected. An analytics solution can use this information for further statistical analyses.
More productive processes
Production managers can more quickly identify situations where the manufacturing process deviates and when manual intervention is required to meet customer specifications and technical tolerances.
Machine maintenance also becomes more predictable on this basis. But only with real-time analysis do companies receive such information not only after a complete production batch has been manually evaluated for errors. Since information about deviations from the standard is available in real time, tools, for example, need to be replaced less frequently.
Companies thus permanently increase their productivity and also shorten the ramp-up phase of the manufacturing process. Such a scenario requires efficient data management that is capable of handling the huge data streams captured in real time.
Together with partners, NetApp delivers a platform for predictive analytics. Applications such as Hana and the Big Data platform Hadoop are used as the basis for storing sensor data.
The infrastructure consists of the FlexPod solution, a pre-validated converged infrastructure platform with components from NetApp and Cisco.
The modular solution includes servers, network connectivity via switches and storage with flash memory.
Companies are thus able to accelerate their IT projects and execute them with less risk because all components are aligned with each other. At the same time, the solution brings the stability and speed needed to link SAP ERP with the analytics results from the Hana or Hadoop clusters.
In order to be able to use the analytics results on any end device, the solution supports the operation of tools such as Lumira or Tableau.
In addition, the scenario presented requires a central platform for data management that supports a high level of fail-safety.
For this purpose, NetApp offers a backup solution that is specially adapted to Hana technology and based on snapshots in order to back up productive data at short intervals and to restore it very quickly if required.
NetApp flash storage systems also have a built-in RAID feature that provides over 30 percent data reduction compared to traditional Hadoop failure scenarios.
In the event of data loss, companies can thus reduce recovery times by up to 500 percent compared to conventional backup concepts.
Conclusion
NetApp's approach to the Internet of Things is based on an established reference architecture that enables rapid deployment of the hardware environment.
In combination with solutions from SAP and the Hadoop distribution MapR as well as other Hadoop technologies, companies create future-proof analytics applications to realize the Internet of Things.
The application example of a manufacturing environment in the automotive industry shows that data is playing an increasingly important role as a production factor in order to position one's own company competitively.