Future concept MES 4.0
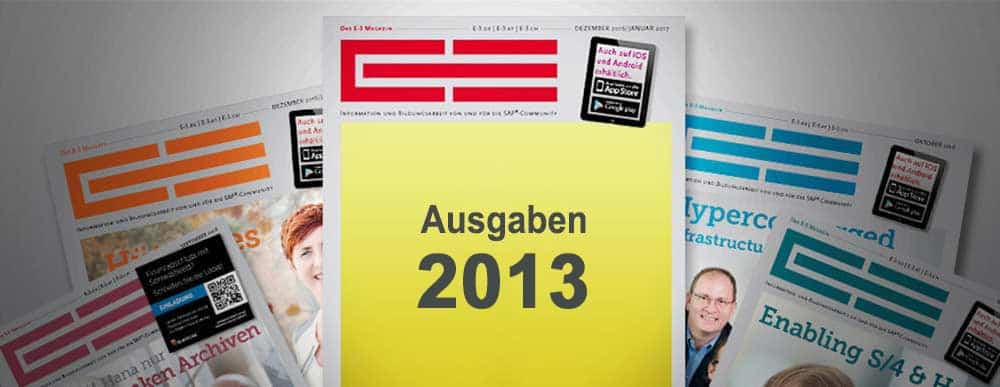
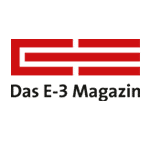
Industry 4.0 describes how intelligent workpieces communicate with machines, independently find the optimal path through manufacturing, and thus become the finished end product without a central controller.
This is referred to as Cyber Physical Systems (CPS). Humans support and intervene in the system only when necessary. This inevitably generates large amounts of data that provide information about the current status of the overall system and the individual workpieces.
Industry 4.0 provides for decentralized IT solutions from the cloud to process this data. So far, we have read little about the connection to an ERP system in this context - in contrast to MES systems.
Currently, many research institutions and manufacturing companies are looking into Industry 4.0 and testing different approaches to realize the visionary ideas.
Starting points for MES
Despite all decentralization, experience has shown that a central instance for coordination and synchronization is beneficial. Today, manufacturing execution systems already benefit from a high recording density and many sensors on the shop floor.
This data is compiled in a central production database and results in an overall picture of production, which provides the basis for secure decisions and the optimization of manufacturing processes.
Industry 4.0 also needs transparency based on real-time data and can be effectively supported by the capabilities of an MES. Thanks to central integrative data management, an MES can work very quickly with the available information, since it is not necessary to first request multiple data sources.
Coupling the autonomous CPS to the MES database makes their communication more efficient - and thus also the overall system. In addition, the coupling to an ERP system is easier to implement centrally than decentrally.
In order for a Manufacturing Execution System to meet the requirements of Industry 4.0, it must bring with it many new functions and capabilities. MES 4.0 combines these requirements into a coherent concept.
Practical use cases
At the forefront of MES 4.0 is horizontal integration, i.e., the linking of data across all resources involved in the manufacturing process with the aim of avoiding autonomous isolated solutions and additional interfaces. VDI Guideline 5600 speaks here of the three areas of manufacturing, quality and personnel. However, these must be viewed holistically.
With its overarching approach, integrative MES data management ensures that all resources (machines, tools, personnel, setting parameters, production resources/tools, inspection plans) are available on time and are optimally utilized.
This promotes the superiority of autonomous Industry 4.0 manufacturing through high variant diversity and flexible delivery capability. The online capability of an MES system is also becoming an absolute must.
In the course of decentralization of manufacturing systems, offline capability of MES components is important in addition to real-time acquisition and processing. If the connection of a machine or sensor to the central database is disrupted, intelligent components must be able to bridge this time.
This is of great importance with regard to seamless documentation and optimal production throughput. Due to different systems, Industry 4.0 requires the use of standardized communication such as UMCM (Universal Machine Connectivity for MES) between the machines and the MES system.
With UMCM, the machines can be easily connected and necessary data such as time stamps, counter readings, machine status, quantities and process values can be transferred.
The management of a manufacturing company is becoming increasingly involved in production-related decision-making processes. However, sound decisions can only be made if those responsible have the necessary information in a suitable form.
The MES of the future provides key figures or other evaluations of important production parameters in a timely manner and suitable for management. The transfer of condensed information from production to an ERP or business intelligence system will also gain in importance in order to be able to evaluate and optimize business processes end-to-end.
The decentralization of processes in manufacturing also means that employees must be able to act more flexibly. Mobile devices and the appropriate MES applications make all data available exactly where it is needed. A few practical scenarios will illustrate this:
Smart maintenance
A maintenance worker is informed of a machine malfunction via his smartphone. Using the same device, the employee can immediately display the necessary information about the affected machine, generate a maintenance order online and document the problem points on site with the built-in camera.
The images are automatically assigned to the maintenance order and the machine history. In the same way, the maintenance technician can view stored information on previous failures.
Based on the historical data and the current status, he can decide which measures need to be taken and initiate them immediately - and all this without travel times and handwriting directly at the machine.
Mobile traceability
Thanks to the camera built into the smartphone, half- or finished
products in WIP inventories can be scanned via identifiers. With a mobile MES solution, a foreman can thus identify material and call up further information during his production tour. The connection of the real world with the virtual image in the MES is established by such functions in an almost trivial way.
Mobile production monitoring
One of the trivial possibilities of mobile clients is the location-independent availability of information about the current status of production or individual resources.
In this way, a shift supervisor can find out about the status of the orders in his area of responsibility even if he is in a production meeting or with his supervisor in the office. This avoids unnecessary calls and reduces waiting times.
Looking Ahead
Some of the topics mentioned can already be implemented in MES. However, the effort required for this is still very high for many MES suppliers. ERP systems are usually not yet prepared for decentralized manufacturing concepts.
Future technologies and concepts such as MES 4.0 will make today's solutions smarter and more flexible. Industry 4.0 will not do without MES. In particular, modern MES solutions will be of elementary importance as a link between the ERP system and autonomous manufacturing.