Digitized variant management
![[shutterstock.com:119911057, Vadim Georgiev]](https://e3mag.com/wp-content/uploads/2017/06/shutterstock_119911057.jpg)
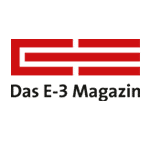
The history of the family-run company with its wire weaving and machine factory divisions began in 1887 and is characterized by innovative spirit and cosmopolitanism. Today, the group of companies has more than 2800 employees and records a turnover of 470 million euros.
The development and maintenance of the design and manufacturing data of modern machines, such as Haver & Boecker's weighing, filling and preparation technology, is highly complex.
Components such as mechanics, electrics, pneumatics and software play equal roles. They all have an effect on the functions of a machine.
Above all, however, the diversity of variants is very pronounced; many machines are unique. Some of the machines consist of up to 5,000 components, and the mechatronic interaction between the technical disciplines and the documentation must be perfect for each variant.
The company from Oelde in the Münsterland region set itself the strategic goal of creating a system that could be used to manage the variant characteristics of the series across all technical disciplines. SAP ERP had already been introduced in 2011.
The mechatronic design department, which is responsible for product standards and order-related custom design, participated in this project from the very beginning. This new system was to be mapped in the ERP system.
The solution was found with the help of the SAP specialists from Itelligence. The integrator for overall ERP solutions was able to contribute its extensive SAP PLM experience and had already proven its ability to implement mechatronic variant management with SAP on several occasions.
Integrated into the SAP ERP complete solution, Haver & Boecker thus introduced SAP PLM 7 (Product Lifecycle Management), SAP PSS (Product Structure Synchronization) and SAP PSM (Product Structure Management).
With the help of product structure management, the machines can now be easily structured in their maximum configuration according to function. The selection conditions for controlling the variants are maintained in tabular form. The parameters of the software, documentation, pneumatic and electrical engineering components can be managed in an integrated manner.
Haver & Boecker relies on a uniform change service for holistic release planning. The PSM structure - the starting point for creating order documents - is synchronized via SAP product structure synchronization to form a complete design bill of materials. From this, the system in turn creates a production and spare parts bill of material.
The PSS stores the differences between the various structures and keeps them synchronized. After the order is placed, the system describes the machines based on the required product characteristics and automatically derives the final structure from the set of rules.
The new solution adds engineer-to-order (ETO), pneumatic and electrical perimeters based on the schematic templates selected by configuration directly in the design BOM.
Furthermore, additional developments can now be used to automatically derive the order-specific and thus differently structured parts lists for the assembly and spare parts documentation. This applies equally to the spare parts lists and the service structures (IBase).
The result is a fully digitized variant management system.
Markus Gerkmann, SAP PLM Inhouse Consultant/mechatronic design at Haver & Boecker, is highly satisfied:
"By implementing function-oriented mechatronic variant management with SAP PLM 7, we are able to live a forward-looking and sustainable process that enables Haver & Boecker to meet the needs of the customer on a daily basis."
At the same time, Haver & Boecker has already created the basis for tapping further PLM potential. These include the integration of CAD systems for electronics and mechanics, the use of 3D documents in assembly, and an expanded change process.