Digitization for preventive maintenance
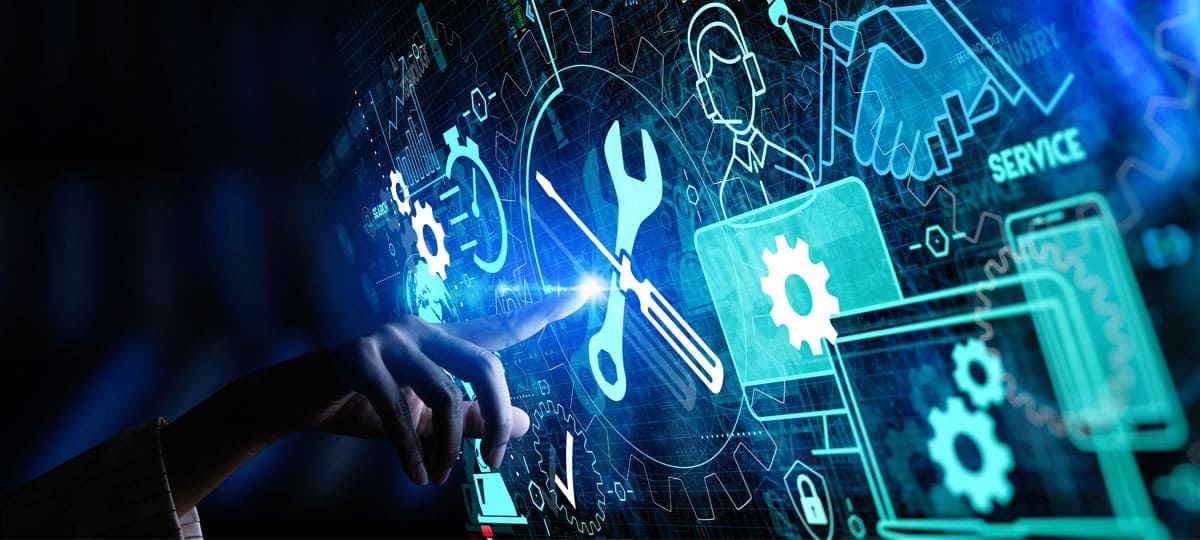
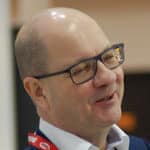
SAP Plant Maintenance at Smurfit Kappa
Smurfit Kappa, one of the world's leading producers of paper-based packaging with 2020 annual sales of €8.5 billion, has implemented the SAP Plant Maintenance (PM) module in its maintenance operations at the Smurfit Kappa Solid Board plant in Herzberg, Lower Saxony. "SAP PM offers us a wide range of possibilities and functions that are essential for a manufacturing company," says Janina Schröder, project manager for maintenance at Smurfit Kappa. As an SAP partner, Argvis has supported Smurfit Kappa in the implementation, optimization as well as mobilization of PM with a Maintenance Portal. "The solution also works perfectly with our other SAP modules Material Management and Financial Accounting," explains Schröder.
The aim of implementing the PM module is to simplify, optimize and digitize the entire process behind maintenance. This includes the documentation of malfunctions on the machines, the master data maintenance of the components, the planning of the activities of the maintenance employees in day-to-day business, the planning of repair activities and the maintenance planning. In the future, SAP PM will provide Smurfit Kappa not only with a good information base - due to a virtually built plant structure - but also with all histories of installed and removed components. This will significantly simplify the planning of repairs and maintenance activities.
"In order to submit messages about defective components in real time, we also wanted a mobile, digitized message submission via smartphone or tablet," reports Danny Polske, Maintenance Manager at Smurfit Kappa. "That's why we started looking for a mobile solution at the beginning of 2022, i.e. in parallel with the implementation of PM, and then we also found what we were looking for with SAP partner and maintenance specialist Argvis." The SAP partner's maintenance portal offers a user-friendly and clear desktop interface and, at the same time, an app that enables mobile use on smartphones. Important features for Smurfit Kappa are, above all, the mapping of the company's plant structure on the smartphone, the planning board, and the clear evaluation of all maintenance-relevant key figures. The maintenance portal is used at Smurfit Kappa in the maintenance and repair of production plants, in scheduling by foremen, in production itself, and in the management of evaluations.
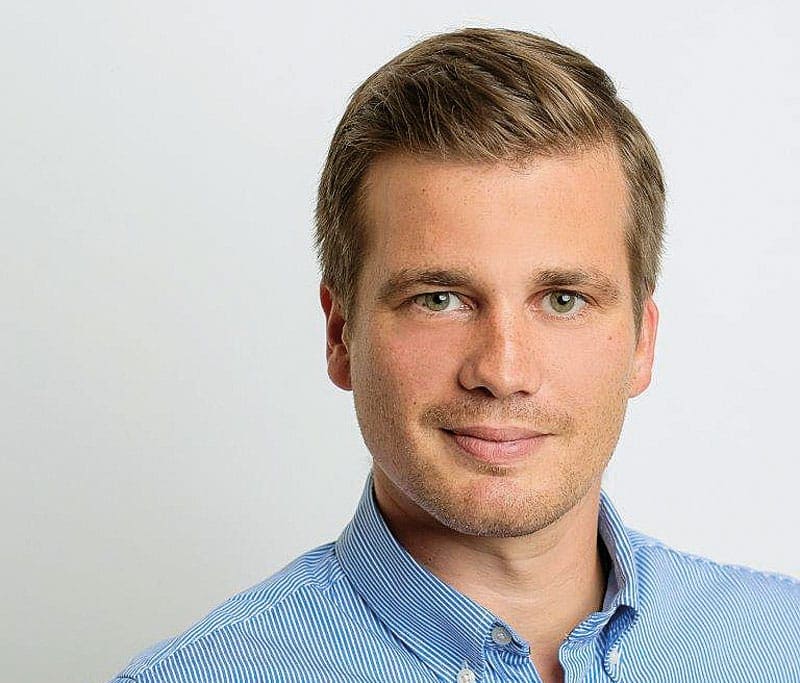
“The close and good cooperation of our IT department with the implementation partners SAP and Argvis was a guarantee for the successful implementation of this project.“
Danny Polske, Maintenance Manager, Smurfit Kappa
Digital maintenance
The major goal that those responsible have set themselves with the introduction of SAP PM and the maintenance portal for the Herzberg site is the complete digitization of maintenance. For Janina Schröder, one thing is clear: "Digitization is the most important and decisive step from reactive to preventive maintenance." After all, this is the only way to significantly reduce or even completely prevent malfunctions and failures of the cartonboard machines and other aggregates in Herzberg. Furthermore, digitalization simplifies spare parts management, maintenance schedules are optimized and "we get good transparency and clarity," adds Danny Polske.
Today, all PM processes are digitally integrated through the Maintenance Portal and can also be easily displayed. But the basis for predictive maintenance is also always a solid collection of information and data. So the big challenge for Smurfit Kappa is also to take the extensive know-how of its employees and incorporate it into the virtual plant structure, "which works very well thanks to the enormous knowledge of our employees," says Janina Schröder, describing the current situation.
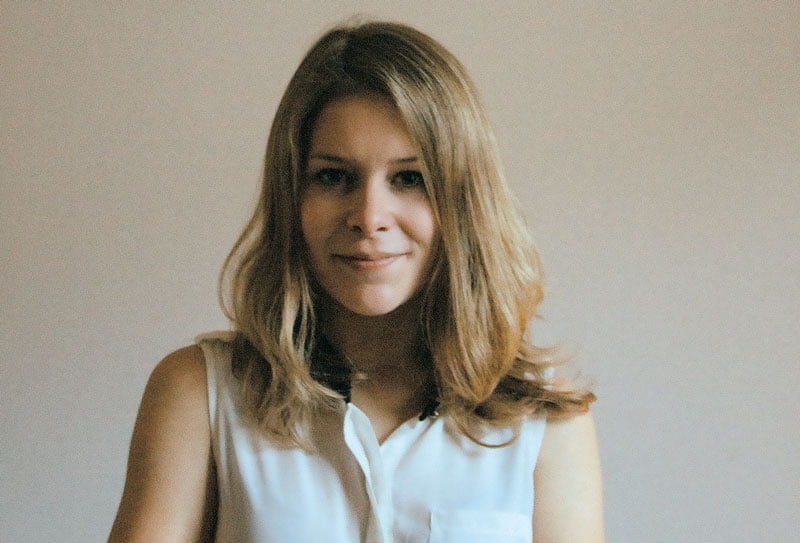
“Digitalization is the most important and decisive step from reactive to preventive maintenance.“
Janina Schröder, Project Manager Maintenance,
Smurfit Kappa
The requirements for the PM module on the one hand consisted essentially of streamlining Smurfit Kappa's internal processes as far as possible, but at the same time remaining close to the SAP standard. The requirements for Argvis, on the other hand, consisted primarily of implementing "our design and usability requirements anyway, even without much flexibility in terms of customizing PM - in this regard, all possible adjustments in the maintenance portal were implemented immediately," reports project manager Schröder.
As a result, Smurfit Kappa received a tool such as the planning board, which makes it much easier for the foremen to plan their employees' days. Likewise, the import of the plant structure to the mobile solution is also possible without any problems. Janina Schröder comments: "The close and good cooperation between our IT department and the implementation partners SAP and Argvis was a guarantee for the successful implementation of this project. In addition, "the standard Argvis solution already covers a large part of our requirements without any adjustments," adds Danny Polske.
The Maintenance Portal
The clarity, intuitive operation and the overall design of the dashboard and mobile use were the criteria for Smurfit Kappa when deciding on the Argvis solution. "Added to this was the professional and constructive cooperation - from the presentation to the further course of the project," sums up Maintenance Manager Danny Polske. The use of so-called device licenses, where several users have access data on one device, also led to a streamlining of license management in shift operations.
The Argvis portal is used in various areas in Herzberg, as Janina Schröder knows: "A work preparation system was created for the day-to-day handling of messages that arise, for repair planning, the structure and for data maintenance of the virtual structure. This covers the specialist areas of mechanics, electronics and production, he says. "Furthermore, our foremen in the respective departments use the portal to assign work as well as to plan repair activities." The reports are then submitted via pool smartphones and tablets provided.
Unplanned machine downtime
A special function in the Maintenance Portal is the attachment of images and voice messages when submitting a message. The quality of a fault message is crucial for avoiding queries and initiating the rapid handling of a fault. With the solution, the fault messages can now be recorded very specifically and in a way that can be understood by any person. "The malfunctions are submitted directly at the machine," says Danny Polske, "the messages are then processed by the work preparation department and the orders for the malfunctions are created."
The foremen can now divide the maintenance orders among their team. This digitized process is very mature in Herzberg and involves all departments in the daily work and in the daily reports. "As a result, all departments know about events or can view them retrospectively," adds Janina Schröder. The risk of faults or messages being forgotten or not submitted at all is therefore drastically reduced. "This also significantly reduces the risk of unplanned machine downtime, which saves us time and money," concludes Janina Schröder.
"In the case of material withdrawal, we also achieve a significant streamlining of the process thanks to the mobile solution from Argvis." For example, the material withdrawal is automatically posted upon confirmation - unplanned material withdrawals are possible via scanner. The clarity of the material management areas in SAP MM, such as purchase requisitions and purchase order monitoring, is another additional benefit for Janina Schröder, "in order to present the link between SAP MM and SAP PM in a user-friendly way".
Company profile: Smurfit Kappa
In Herzberg, Germany, Smurfit Kappa primarily manufactures solid board packaging for beverages, meat, fruit and vegetables, dairy products, confectionery and other fast-moving goods. The complete production of high-quality cartonboard and solid board in the form of reels and sheets is 100 percent recycled.
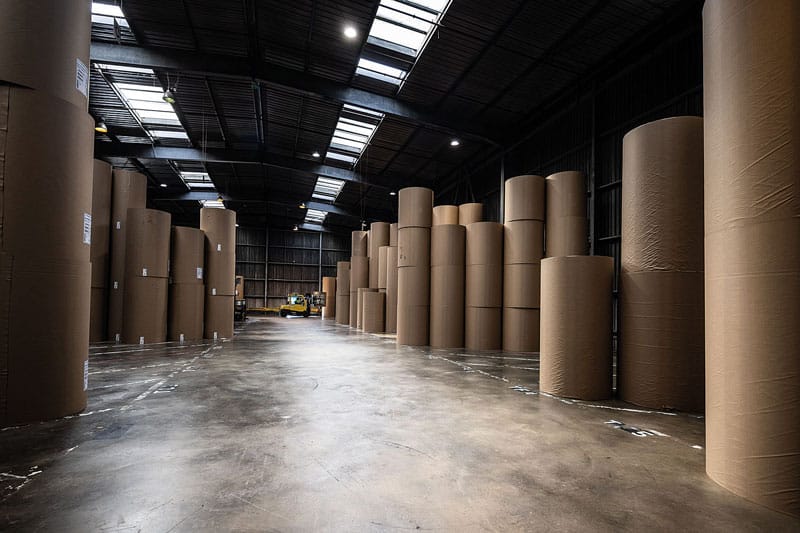
At Smurfit Kappa Herzberg Solid Board, the entire production of high-quality cartonboard and solid board in the form of rolls and sheets is 100 percent recycled.