Foundation stone for the intelligent factory
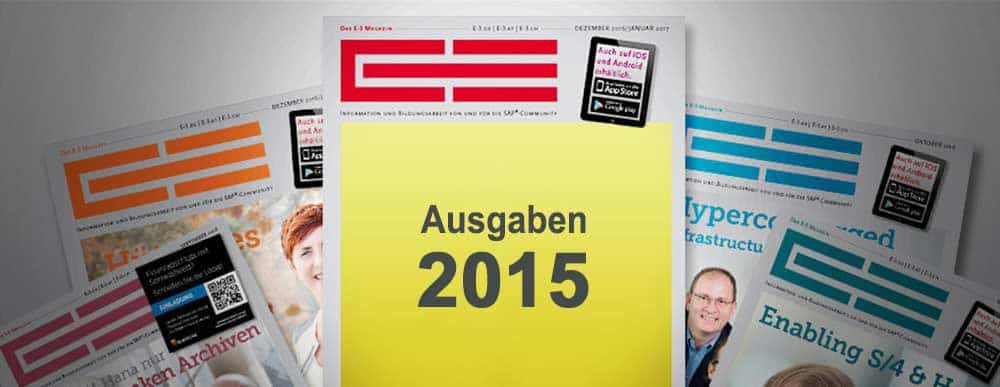

Gas springs, dampers and adjustment systems from Suspa perform their services in the background: They ensure that the tailgate of the Mercedes E-Class closes automatically, the rear spoiler of the Porsche 911 Turbo extends smoothly, washing machines spin quietly and refrigerator doors close almost silently.
Each year, Suspa produces around 70 million parts for 50 products in 1,500 variants for customers in the automotive, mechanical engineering, furniture, medical technology and electrical appliance industries.
Potential on the store floor
However, customer requirements are also rising steadily. They demand prompt and flexible processing of orders and even greater delivery reliability at lower costs.
"A cornerstone of our business strategy is therefore to continuously improve the quality of operations in all areas through a modern and consolidated IT landscape."
knows Jürgen Nothof, Head of Global IT at Suspa.
Through the company-wide standardization and harmonization of business processes in a central SAP ERP system, the company has made great progress in this direction.
But in manufacturing in particular, those responsible at Suspa want to sustainably increase productivity and permanently reduce costs through optimized use and utilization of equipment and faster throughput times.
Real-time view of manufacturing
"To do this, we need an up-to-date view of what is happening in production and - if possible in real time - exact key figures on finished, yield and scrap quantities, downtimes, malfunctions and setup times, or on machine effectiveness (Overall Equipment Effectiveness = OEE)."
Jürgen Nothof explains.
For this reason, data from production-related systems has recently been collected using the modern Manufacturing Execution System (MES) from Orbis, which has also been commissioned with the implementation.
The MES solution is based 100 percent on SAP technology and can be fully integrated into the ERP software. This eliminates the costs of setting up and maintaining a separate IT infrastructure. Acceptance among end users is also high.
The application features contemporary and easy-to-use interfaces based on the Orbis Multi-Process Viewer, a component of the Orbis Multi-Process Suite (MPS).
The key performance indicators (KPIs) are provided in MES in a standardized way according to the VDMA standard sheet 66412. The production KPIs are now recorded electronically and immediately processed automatically. This gives end users, i.e. machine operators, production managers or plant managers, a real-time view of what is happening on the shop floor.
Since the data is available at the time it is generated, rather than hours or days later, the deployment and utilization of machines and personnel can be optimally planned.
The KPIs from production also make it possible to precisely track whether the times calculated in the SAP work schedules, for example for setup and teardown or for personnel deployment, are correct.
Accurately measure improvements
The IT-supported processes also ensure a continuous flow of information from the shop floor to plant management and the executive board. The KPIs from the store floor can be conveniently called up at the push of a button and are graphically visualized on a web-based cockpit interface.
Using traffic light functions, an end user can immediately see whether his machine is above, on or below plan in the processing of an order; malfunction times as well as good and scrap quantities are also displayed.
In this way, exceptional situations can be identified immediately and a response can be made without delay. The causes of malfunctions, downtimes or excessive setup times are now also recorded in the MES, where they can be evaluated in detail by a production controller or engineer and compared with historical data.
"This makes it possible, for example, to find out whether a plant exhibits certain fault patterns. From this, we can then derive targeted measures to improve the runtime and the quality rate."
clarifies Jürgen Nothof.
IT-supported maintenance
The production and plant management can call up the analysis results aggregated at plant level, while the management receives the evaluations in processed form from the plant controlling staff.
Maintenance measures can now also be carried out promptly and proactively, which reduces expensive downtimes. As soon as a fault message is received, regardless of whether it comes from the machine control system or is entered manually at the terminal, the SAP maintenance message is created in the MES solution and flows directly into the SAP software for maintenance.
A maintenance order is generated there and added to the order pool in MES, where it can be processed flexibly and as required. The information relevant for the repair, such as the workstation, serial number or manuals, is clearly summarized in a cockpit.
Once a maintenance technician has completed a task, he records his working time and material consumption in the MES application, which immediately transfers the data to SAP ERP, where it is posted immediately.
Predictive Maintenance
Planned maintenance intervals can also be monitored seamlessly in the MES solution so that technician capacities can be optimally planned and spare parts procured on schedule.
Proactive maintenance reduces the risk of unplanned downtime or defects, and costly repairs can be avoided. Since the MES solution also reports the completion of a production order back to SAP ERP in a partially automated manner, the company gains a clear view of the current material inventory in production.
Material bottlenecks can thus be identified quickly and countermeasures initiated promptly. Currently, all 25 machines of the Suspa plant in Sulzbach-Rosenberg are connected to MES.
Plants that produce racer parts are connected fully automatically, the others manually. Currently, the solution is being introduced at the headquarters in Altdorf and it is already working productively with the first machine.
Starting in 2016, the new Czech plant in Bor and later also the production site in China are to be connected to the MES solution. In the medium term, it is planned to also introduce the SAP software for quality management and to transfer data from the measuring systems directly to the MES.