Project Management Cockpit
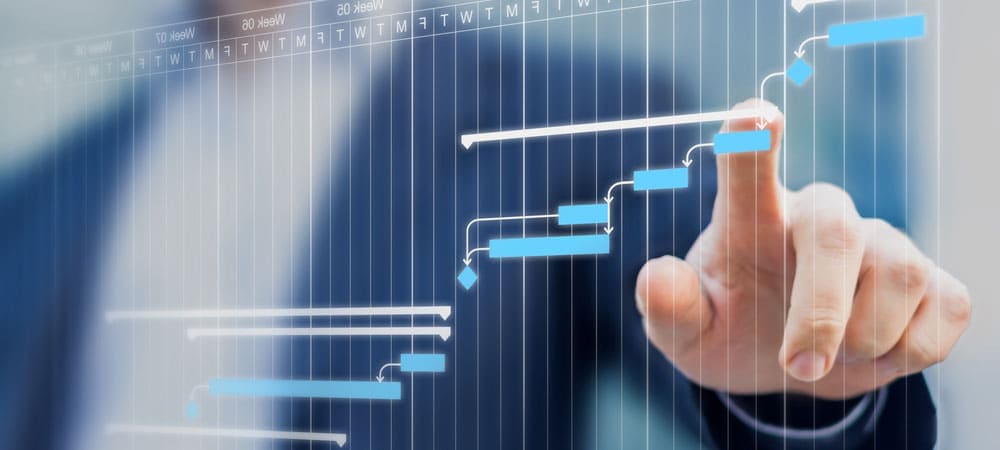
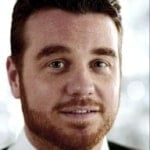
Production processes are becoming more and more demanding
The project business, in which production systems are manufactured according to a customer's individual requirements and installed on site, is a mainstay of the Kuka Group. It can take several years from the placing of an order to the commissioning of a plant; the costs usually amount to several million euros. "In recent years, the complexity of projects has once again increased immensely"says Wilhelm Keppeler, Head of Project Management Office (PMO) Industries Division at Kuka. "This is mainly due to the fact that the production processes of our customers - automotive manufacturers, for example - are becoming increasingly demanding. For us, the increasing complexity has meant that we have reached our limits in project controlling."
Project controlling
The project managers updated their reports regularly. However, it was not possible to call up the status of a project in real time. In addition, only a portion of the fundamentally available data was condensed into key figures. The generated key figures were only partially visualized. To improve project controlling, Kuka decided to relaunch the topic in 2019.
Oliver Kalka, Senior Manager at MHP: "We have been a partner of Kuka for many years and have already implemented several IT projects together. Therefore, it was obvious that the first thing Kuka's managers did was to talk to us about their project controlling plans." On the one hand, Kuka employees developed a new process for multi-project management and built a new key performance indicator system. The goal was to evolve from a primarily economic view to a holistic view that integrates the dimensions of finance, time and performance (quality). Secondly, an individual analytics solution was developed that exactly matched Kuka's functional requirements and could be integrated into the existing system landscape.
The core of the Smart Intelligence Robotic Project Cockpit - as the application is called - is the SAP BW on Hana data warehouse, which has already been in use at Kuka for several years. Here, three successive layers were implemented in Abap and by means of rapid prototyping. The first layer is used to retrieve and harmonize data from different S/4 modules (FI, CO, PS data and concurrent calculations) in real time. This harmonization is necessary on the one hand to standardize the data from the different modules. On the other hand, it is intended to compensate for the individual habits of project managers when entering data. From the processed data, the Calculation Engine calculates a series of key figures on finances, time and performance as a second layer. These include, for example, the material ratio or the percentage of completion.
Oliver Kalka: "When implementing the Calculation Engine, it was not so much a matter of implementing particularly elaborate mathematical procedures. The art was more in finding the right data in the various modules of S/4 and using it to build meaningful data models." As a third layer, the monitoring engine continuously compares the calculated key figures with the target values and reports developments in relation to the previous day and differences to critical threshold values with the daily status report.
Visualization with add-on
For an appealing visualization of the results, different views were realized using QlikView, Qlik Sense and Qlik NPrinting. The portfolio dashboard provides an overview of all ongoing projects and shows the respective milestones. In addition, a traffic light indicates which projects are running smoothly and where things are critical. The project dashboard provides a detailed view of individual projects. Here, for example, financial details with a representation of all cash flows, a Gantt project plan, which among other things enables a simulation of target/actual deviations, and a time and budget overview, which highlights dependencies, are available.
The cockpit has now been in use since 2020. And very successfully at that. Wilhelm Keppeler: "The new cockpit has given us the transparency we were hoping for. For example, we can now see at any time whether we are as far along in a project as we should be. If we are not, we can react immediately and, for example, plan additional resources. Of course, it then also becomes immediately apparent what impact this will have on finances or possibly on other projects." Overall, the transparency gained has helped Kuka take project control to a new level.
Keller and Knappich Augsburg
Once upon a time, Kuka was a telegram abbreviation and stood for Keller und Knappich Augsburg. Today, Kuka is a brand that stands for intelligent automation solutions worldwide. The company, which was founded in 1898 by Johann Josef Keller and Jakob Knappich as an acetylene gas plant in Augsburg, is known beyond industry primarily for its orange robots. However, the range of products and services includes much more: from manufacturing machines for various applications to driverless transport systems and networked production systems. In 2021, the approximately 14,000 employees generated sales of 3.3 billion euros.