Away with paper and Z programs: Digitized production with SAP DM
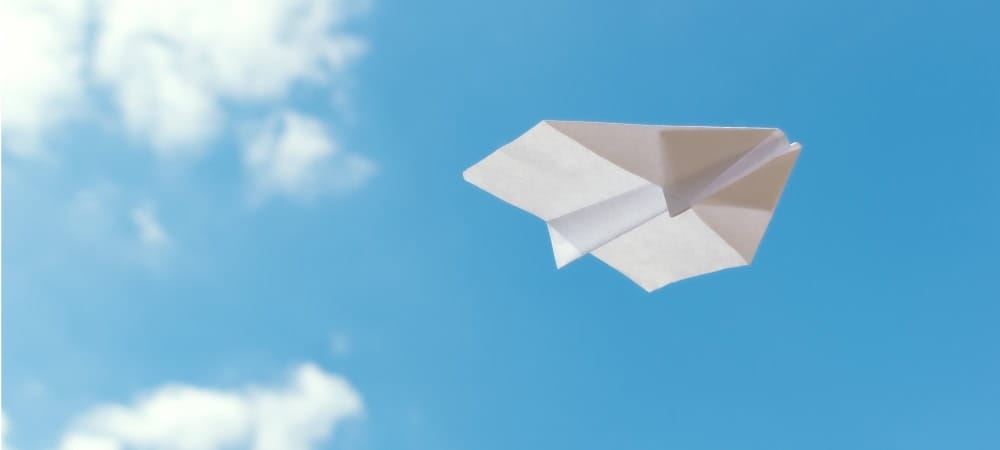
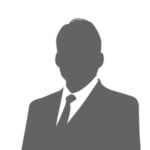
For companies with a broad product portfolio, a modern and flexible Manufacturing Execution System (MES) is a core element for efficient production processes - and ElringKlinger is no exception. With sales of EUR 1.9 billion, 9600 employees and over 40 locations worldwide, the company is one of the leading system partners to the automotive industry for electromobility, lightweight construction solutions, sealing and shielding technology as well as tool technology. The Group is also continuing to grow with its components and systems in the non-automotive sector.
ME support end of 2030
For a long time, ElringKlinger primarily used the functionalities of its ERP system, various site-specific in-house developments for more specific requirements and, in some cases, SAP Manufacturing Execution (SAP ME). This combination worked well, but also led to heterogeneous structures and paper-based processes. In addition, SAP will discontinue support for SAP ME by the end of 2030.
ElringKlinger decided to rely on a new, standardized and more sustainable solution in order to make processes effective, time and resource efficient and environmentally friendly as part of the digital transformation. Starting with injection-moulded parts production in Dettingen/Erms and battery component production in Neuffen, this solution was to be introduced at other sites in the future and comprehensively digitalize the production processes there.
Maximilian Krohmer, IT specialist at ElringKlinger, reports: "The introduction of a new MES presented us with organizational challenges in view of the large number of production sites and product lines, but was ultimately unavoidable for modern production control. The digital transformation is one of the key success factors of our Shape30 Group strategy, with which we want to further shape the Group in all dimensions in order to help shape the future of mobility and be the preferred partner for driving innovative technologies forward."
SAP DM instead of ME
Once the decision for a new MES had been made, the choice quickly fell on the SAP ME successor SAP Digital Manufacturing (SAP DM) as the new solution. Krohmer continues: "The comprehensive digitalization options that SAP offers with DM spoke in favour of this: for example, the option to provide all important information for the next production step bundled via app at the associated workstation, as well as the ability to record and process production data in real time. As a cloud-based solution, SAP DM also offered simple scalability."
In order to initiate the project, a suitable project partner was still missing. From ElringKlinger's point of view, three criteria were particularly important: firstly, relevant project experience, secondly, in-depth knowledge of the relevant SAP environments and thirdly, comprehensive application development skills for any necessary adjustments to the system. Following a tendering process, the decision was made in favor of the management and IT consultancy MHP. Ingo Windshügel, Partner at MHP, recalls: "The discussions were trusting and constructive right from the start. It quickly became clear that we shared similar views on a sensible project process."
Entering the digital factory
The joint project team began to implement the goal defined in advance - a more digitalized production control system. To this end, it introduced SAP DM for the main plant in Dettingen and also integrated various features into the new system that had previously been adopted from Z programs. Kai Roßnagel, Senior Manager Digital Supply Chain Solutions at MHP: "These Z programs were essentially function modules and self-developed applications in SAP ERP that were used by production to handle the production processes. Due to the upcoming S/4 transformation at ElringKlinger, it is essential to get rid of these Z programs in order to return to standard functions." Building on this, the team designed various new functionalities and tools, such as a digital production operator dashboard or an evidence-based and efficient production control system.
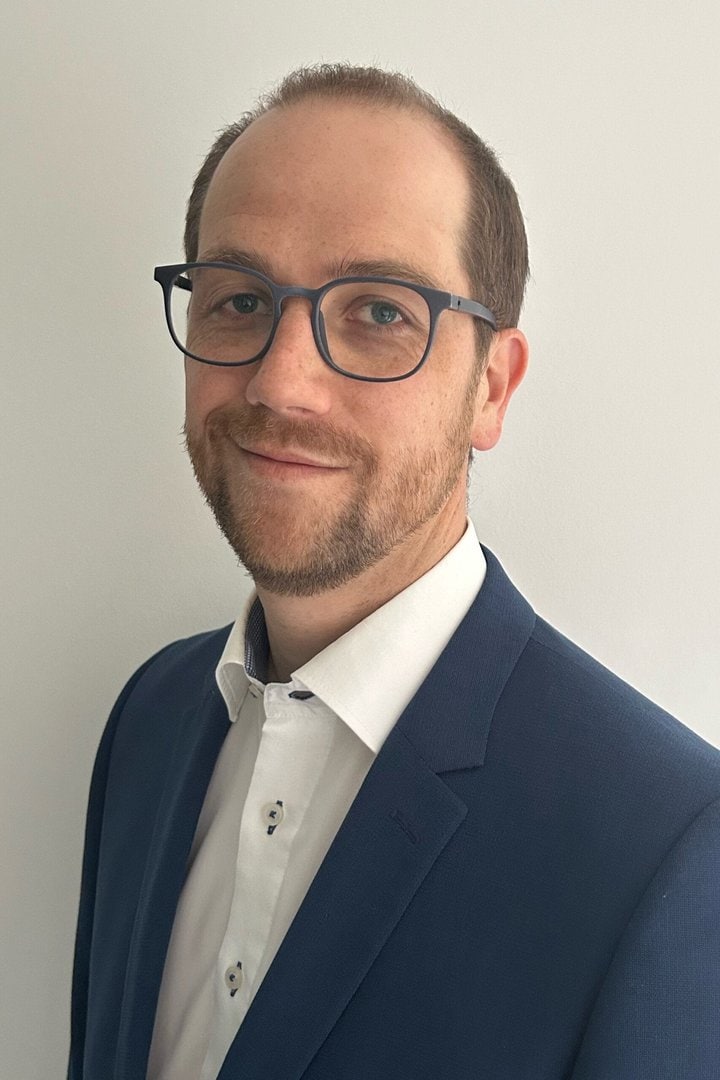
Kai Roßnagel, Senior Manager Digital Supply Chain Solutions, MHP
Production Operator Dashboard
To make production control easier, ElringKlinger equipped all workstations with terminals to use the SAP DM Production Operator Dashboard: Employees on the store floor can now log in and out there, and the dashboard also provides them with all the documents required for the work steps - including technical specifications, drawings and information on the quantities required - in digital form. This means that paper documents no longer need to be stored at the workplace.
As an information medium, the dashboard also supports production control by providing feedback. To this end, it offers employees various features, such as reporting good and reject quantities, recording set-up, machine and personnel times or providing information on the current processing status. In principle, it is also possible to reorder materials, although this has not yet been implemented - just like the extensive machine connection. SAP DM theoretically allows all systems and machines on the store floor to be connected to the MES and machine data to be read out.
The new features also represent a significant improvement for production control: For example, the elimination of paper means that employees no longer have to spend time manually transferring data to the MES. Employees can therefore now focus more on value-adding activities.
Evidence-based management
The feedback functionalities of the Production Operator Dashboard and machine data collection make production much more transparent. The company also gains additional information through more comprehensive data collection, which it can use for evidence-based production planning and control.
The project team's work enabled ElringKlinger to transfer SAP DM to live operation with a defined template in a short space of time: It has been in use at the Dettingen plant since August 2024. Neuffen will follow shortly and other sites will be supplied with the evolving SAP DM production template in the near future.
ElringKlinger thus has a highly modern and very flexible MES that offers numerous further optimization potentials for the future: The introduction of production controlling based on Overall Equipment Effectiveness (OEE) or the use of predictive maintenance processes are just two examples of this. As a cloud-based solution, SAP DM can also be easily scaled and used for any number of additional locations.
Balance sheet CO2 neutrality 2030
Maximilian Krohmer is correspondingly satisfied: "Thanks to the excellent cooperation between MHP and ElringKlinger, we now have an MES that gives us plenty of scope for expansion, brings us closer to our Shape30 targets - including carbon neutrality (Scope 1 and 2) by 2030 - and can also be easily transferred to other sites. We are thus creating the best conditions for sustainable growth."
To the partner entry:
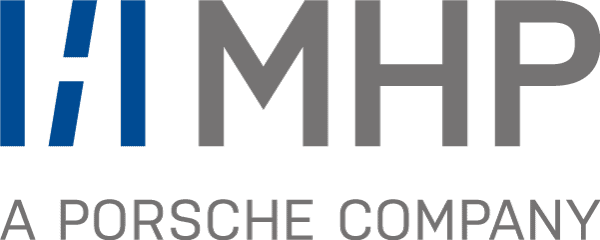