Consolidation on a great journey
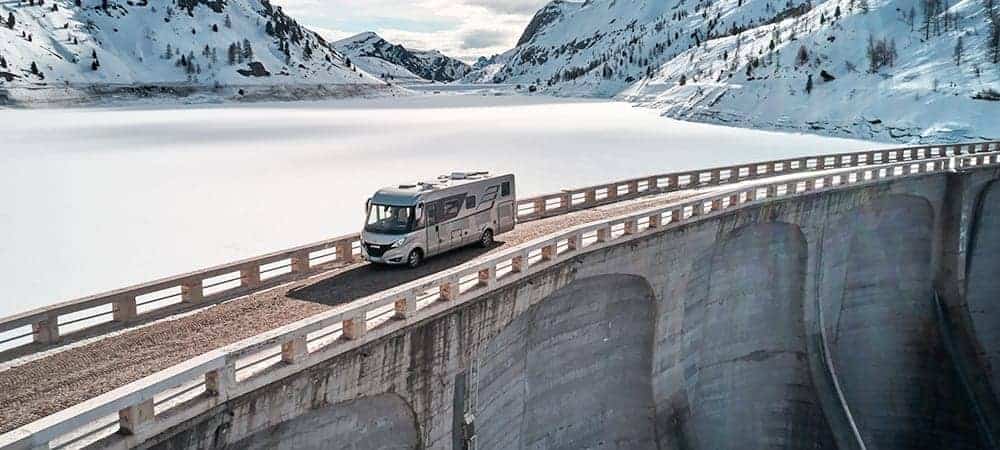
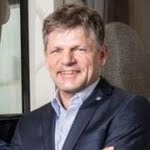
The first step was to convert the ERP/ECC 6.0 system to Hana and S/4 and then migrate the non-SAP ERP system to S/4 Hana. Challenges for SAP partner Consilio were to efficiently manage the highly configurable orders in sales processing as part of planning, to model the existing products in PLM for planning and production, and to transfer the master data.
The high vertical range of manufacture from the production of wood, metal and fabric parts through kitchen and home interior production to vehicle assembly as well as parts procurement and parts provision including integrated quality management had to be migrated to an S/4 Hana solution. In the area of product development, Hymer uses an external PLM that is connected to S/4.
The vehicles are modeled in SAP as configurable materials with up to eight BOM levels due to the high depth in the production of kitchens and home furniture. Customer orders are entered and produced via a dealer portal and the vehicle management system with a quantity of one.
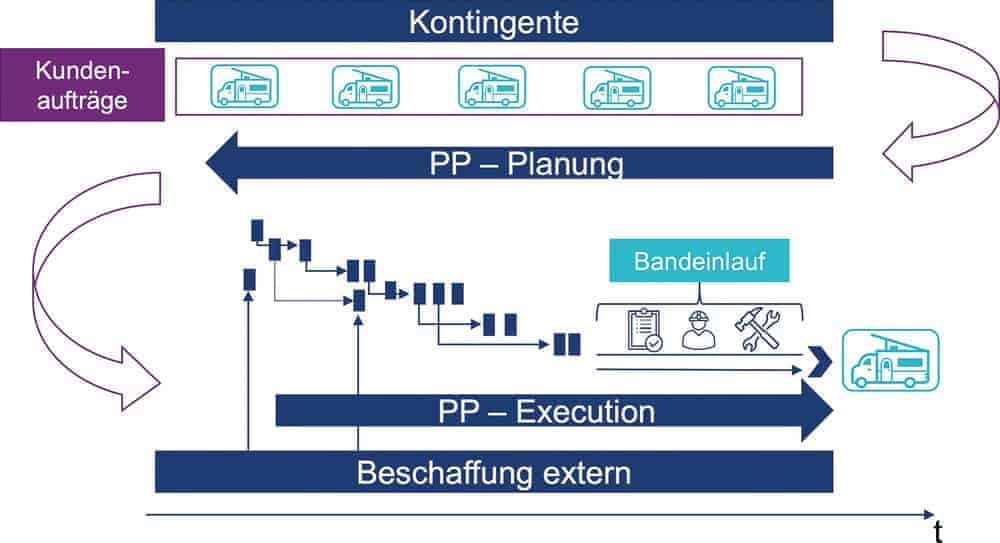
In order to keep the production order volume in the manufacturing areas still within a manageable range, Consilio designed and implemented production planning for Hymer based on characteristics-dependent planning (CDP) in SAP S/4 Hana.
Using CDP, requirements with the same properties can be planned and produced together without the creation of additional material master data, i.e. no classic make-to-order production is necessary, but allows combined production.
Nevertheless, a reference to the vehicles is possible at any time throughout the entire production chain in order to enable the provision of parts to the exact hour. In the vehicle assembly area, the assembly lines had to be mapped with takt-based scheduling in S/4.
Master data and configuration
The master data structure reflects the high complexity of the automotive sector at Hymer. Due to the high in-house production depth, correspondingly high master data volumes with several thousand objects per vehicle type are necessary here. These are partly equipped in the low-level configuration with object dependencies such as procedures, selection conditions or class nodes, e.g. for parts replacement. The master data passes through various Q-gates and is thus checked and released by all departments.
The product structure, material master data and documents are transferred via interface from the external PLM system. The Engineering Bill of Material (EBOM) is already set up for production in the design department and made available as a Manufacturing Bill of Material (MBOM). Structural changes are incorporated in the design via EC (engineering change request) and automatically transferred via interface.
The material master data for product data management (PDM structure) is detailed and completed on a rule basis and via workflow tool in SAP with plant reference. Classification data, MRP and planning parameters are set as part of the workflow processing, as are routings and production versions.
The material status shows the maturity of the master data for planning. It controls the integration of master data for the S/4 Hana embedded PP/DS (ePP/DS), the detailed production planning and optimization solution from SAP. Under S/4, the integration into ePP/DS stipulates that the classification with classes, characteristics, object dependencies, etc. must also be integrated as independent objects for the material master data.
The configuration value assignment is inherited from the sales order to the manufacturing levels. In the subordinate manufacturing levels, the change from make-to-order (CDP-KDE) to CDP-anonymous manufacturing then takes place.
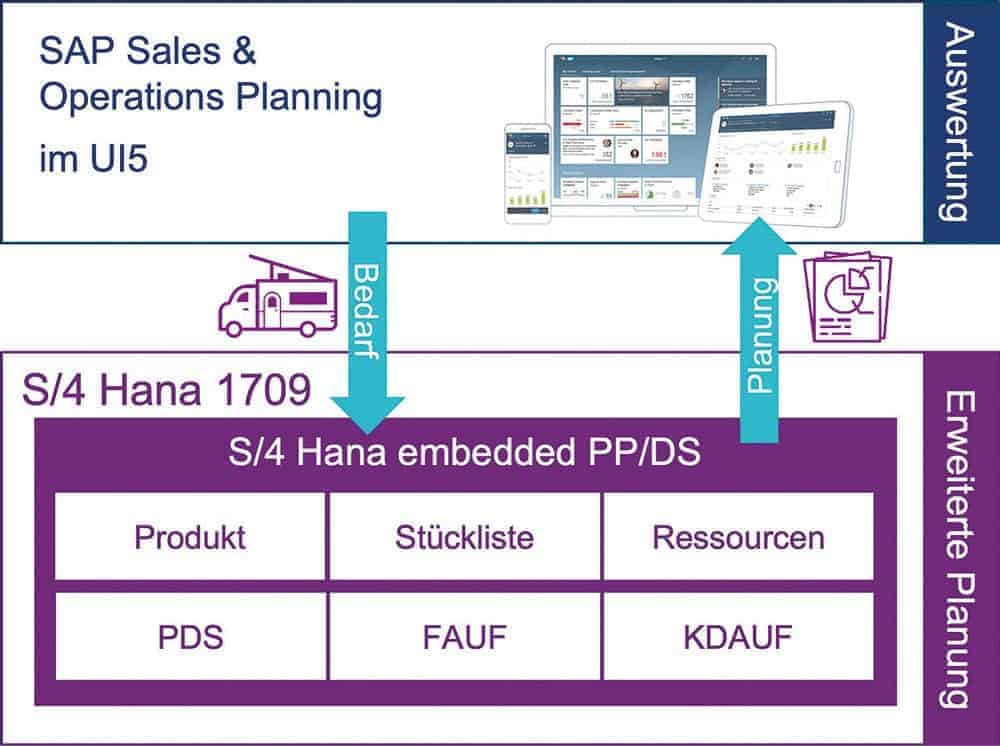
Characteristics-Dependent Planning
Characteristic-Dependent Planning (CDP) can be used to plan in-house production for products using characteristics. The products can be configured in the S/4 system, i.e., product characteristics such as color, furniture decor, upholstery fabric, etc. can be selected on an order-dependent basis without having to create a separate material master for this combination. Planned or production orders for these products can also be configured in S/4.
During planning, the configuration is taken into account and requirements are offset against the appropriate receipts (production orders, purchase orders, purchase requisitions, batch stocks). In ePP/DS, CDP-anonymous the configuration rating and the customer individual segment are available at the order, but no longer in ERP. Here, the configuration is transferred to the batch classification.
The following example will explain this in practice: Several different sales orders for vehicles are entered in S/4. Some sales orders have the characteristic furniture decor identically assigned the value maple, but other characteristics have different values. In S/4, a common planned order and production order are created and produced to manufacture the wooden parts (lot production).
Despite the combination, the reference to the vehicle customer orders is given at any time via the requirements/pegging. Due to this combination of requirements despite configurable products, the production order volume could be reduced from over 40,000 per day to less than 5,000 without having to create material masters, as is necessary for make-to-stock production.
For sales production program planning and allocation, an S&OP solution was designed and implemented on the basis of Fiori, on the basis of which Sales can enter its sales planning and transfer it to Production Planning. In the area of production planning, quantities can be planned and capacities can be determined and simulated on the basis of S/4 ePP/DS in a plan version detached from operational planning. On the basis of production planning, quotas for vehicles are made available to Sales for allocation.
The S&OP solution was developed in-house according to EHG specifications (Erwin Hymer Group specifications). The new Fiori user interface was used for this purpose. A particular challenge here was to map the existing process-related requirements into an integrated and also globally usable, scalable solution. This was one of the reasons why the decision was ultimately made in favor of SAP Fiori.
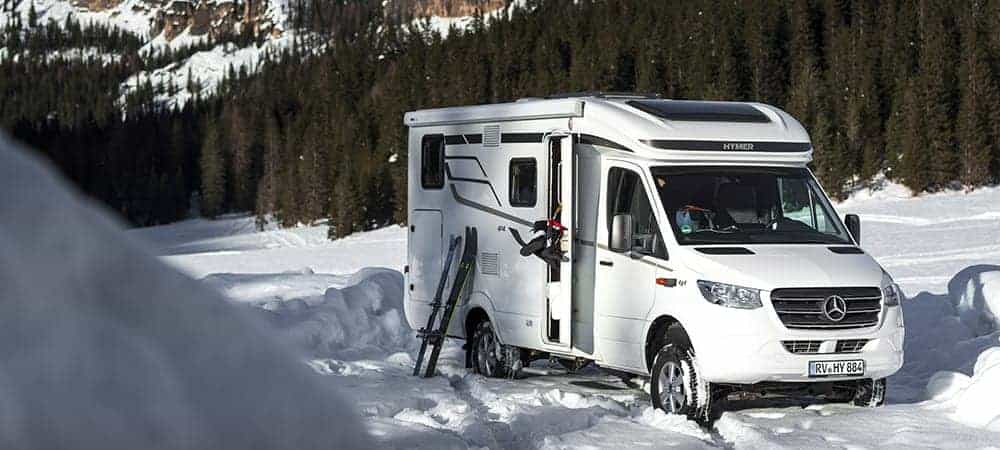
Basically, two goals had to be met. Firstly, the tool should ultimately output quotas at vehicle type level against which sales can confirm customer orders. Secondly, production needed a rough capacity plan to check the sales quantities specified by sales for feasibility in terms of available employees and production capacities. Both objectives should be pursued in a fully integrated manner, which means, for example, that the shift models stored in the system should be taken into account for capacity planning.
Fully integrated also means that real-time data from the back-end system is available to the planning tool. For example, Sales needs the number of sales orders already created to determine its desired sales figures. At the same time, production must take into account the planned and production orders already created in its planning. Both key figures are read in real time from S/4 and embedded PP/DS.
In addition, a possibility of dis- or aggregation had to be provided, since the different areas plan their quantities in different degrees of detail. For example, the quantity per vehicle type and line must be known for capacity planning. Quota planning, on the other hand, is carried out at the type family level, which links several individual types.
Ultimately, the SAP Fiori solution simplified and improved collaboration between the divisions. This created a globally usable solution in S/4 that increases the transparency of sales and operations in connection with feasible production capacities, so that strategic decisions that depend on them can be made in a targeted manner.
Conclusion: SAP standard solution
In the area of procurement, requirements from different vehicles are also combined into one lot, procured and made available on a vehicle-specific basis. The various planning mechanisms ensure that there is always a clear link to the vehicle produced and the customer's desired configuration. Integrated planning with embedded PP/DS enables on-time and lot-based procurement of the required materials. Particularly in the case of body-relevant materials, which are essential for production on the assembly line, timely procurement and provision on the assembly lines is essential.
Integrated monitoring and alerting enables a quick reaction in case of delays or delivery bottlenecks. In conclusion, Consilio has designed and implemented an SAP standard solution with embedded PP/DS in S/4 and characteristics-based planning, which enables Hymer to carry out production planning and order processing efficiently in day-to-day business. As part of the implementation, some teething problems of the embedded PP/DS had to be overcome.

Quality management and integration
The quality information from production is tracked in the system for the vehicle by means of inspections and quality notifications. If defects are detected in components or assemblies during the production process, they are recorded in a follow-up request for the vehicle. At Hymer, follow-up requests are made possible by an S/4-integrated solution with direct integration into production and logistics. This means that parts from the preassembly and prefabrication areas can also be provided at short notice without risking shortages.
Hymer travel experience including S/4
The Erwin Hymer Group is a wholly owned subsidiary of Thor Industries, the world's leading manufacturer of leisure vehicles with over 22,000 employees. The Erwin Hymer Group brings together manufacturers of motorhomes and caravans, accessories specialists, and rental and financing services under one roof. The Erwin Hymer Group includes the motorhome and caravan brands Buccaneer, Bürstner, Carado, Crosscamp, Compass, Dethleffs, Elddis, Eriba, Etrusco, Hymer, Niesmann+Bischoff, Laika, LMC, Sunlight and Xplore, the motorhome rental companies McRent and rent easy, the chassis specialist Goldschmitt, the accessories specialist Movera and the travel portal freeontour. For more information, please visit: www.erwinhymergroup.com
Logistics and integration
With S/4 Warehouse Management, parts are stored, picked, and staged via the production supply interface in production and on the assembly line to the exact hour. In the process, the materials required for the production of the vehicles on the assembly line must be provided at exactly the right time. Different production stages in prefabrication and pre-assembly produce the materials in batches for the customer-specific vehicles. Logistics provides the produced and directly delivered materials from suppliers directly at the assembly line without prior storage. This involves batch-related bundling of the required components with the formation of picking carts from S/4 Warehouse Management. A well-coordinated and integrated solution with direct integration into production logistics is crucial for the efficient handling of internal logistics.