Information, identification and integration
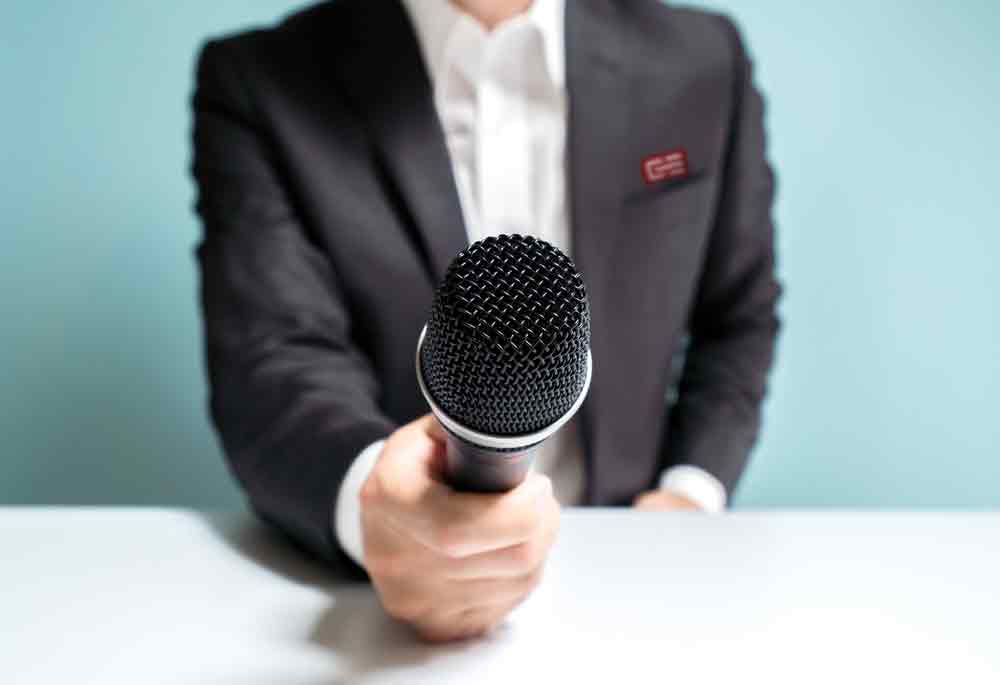
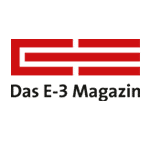
Highlights include customer-specific mapping of the machine fleet with matching parts, the ability to directly maintain maintenance information for each machine, and seamless SAP integration.
This first phase is the beginning of a vision at the end of which Bühler machines will communicate with the portal and order their spare parts independently.
E-3 spoke with Mathias Bösch, Head of Digital Business at Bühler and Gerd Bart (right), Solution Principal E-Business at Sybit.
Mr. Bösch, you recently set up the Customer Portal called myBühler with Sybit. What possibilities does the portal offer?
Mathias Bösch: We wanted to achieve three things in particular with the project for our customers: Information, identification and integration.
Information includes the extensive provision of information on our customers' machines and the parts they require.
In addition, the identification of the correct parts plays an important role. We achieve this on the one hand by mapping so-called "as-built" structures and on the other hand by using novel 360-degree photo views of the parts.
And for our customers, of course, integration into their existing procurement processes plays a key role.
In summary, myBühler offers our customers a clear and efficient way to find and order the spare parts they need for their custom-built machines.
It also supports the management of the machines from operation to maintenance.
What is the objective behind this decision?
Bösch: In the private sphere, e-commerce is a daily companion. This trend is also becoming more and more apparent in our industry.
Our main goal was therefore to offer our customers a service that they are already familiar with from their private everyday lives, and thus also to be prepared for future digital services.
The difference between our store and a classic B2C store is nevertheless huge, as we build on the customer's machinery maintained in SAP.
However, this enables us to offer our customers optimum service for their machines.
You decided to implement the portal on the basis of Hybris. Why?
Bösch: Hybris is one of the market leaders in the e-commerce sector and the acquisition of SAP gave us strategic advantages.
Even though the integration with SAP still has potential, we see many opportunities for the future.
In addition, Hybris offers a broad product portfolio with very good basic functionality and the necessary flexibility.
How do your customers benefit from this?
Bösch: The direct and uncomplicated access to information about machines, parts and the status of quotations and orders is an aspect that our customers greatly appreciate.
We have managed to significantly simplify order processing for customers and make it more transparent.
And further, easy identification of the right parts is certainly a key to success.
If that is not possible, we offer enormous advantages through the Find-a-Part service: The customer can upload a picture of the spare part they are looking for to the portal and we will find it for them.
The project is firmly anchored in the company and known all the way up to the board of management. How does this affect the project?
Bösch: The idea had been in the company for some time and there had already been various initiatives. We are all the more pleased that we were finally able to tackle the issue and bring it to fruition.
On the one hand, the aforementioned management attention naturally brings shorter decision-making paths and provides a great boost within the project team and the organization.
But on the other hand, of course, pressure and expectations are rising.
Mr. Bart, the Customer Portal was implemented in around six months. What was the challenge for the Sybit team?
Gerd Bart: That was quite a sporting challenge: from the start of the project in April to the go-live in September, but it welded us together enormously as a team.
We proceeded in such a way that we delivered results every two weeks, which boosted the implementation quite a bit.
Added to this was the good cooperation with the Bühler AG team. There were more than 30 employees who gave us excellent support.
What are the highlights of the portal from your point of view?
Beard: Two things in particular excite me: One is the enormous amount of data in the background, which the system juggles with great ease when displaying it in different ways.
The other is the customer's path through the portal: starting from his individually manufactured machine, he first sees all spare parts, can call up the associated documents, can order wear parts, view prices and get help via the Find-a-Part service.
From my point of view, this portal is perfectly tailored to the needs of customers.
The Sybit team worked according to the agile project methodology. Did this method boost the project?
Beard: Yes, definitely. The bi-weekly sprints, i.e. the requirement to deliver results every two weeks, originate from the agile project methodology.
This accelerated the project and ensured that we were able to meet the target.
What are the next steps after the go-live?
Bart: In the short term, the connection of digital spare parts catalogs and interfaces to customers' ERP systems will play an important role, along with smaller functional enhancements.
In Bühler's vision, however, the customer portal will be further expanded and supplemented with some additional functions and processes.
Topics such as e-learning, e-monitoring and e-maintenance will certainly keep us busy.
Where will the future focus or challenges lie?
Beard: We are clearly focusing on the further automation of processes.
One challenge I am personally very much looking forward to will be to realize the path of digital data from the machines to the portal.