Landscape Transformation merges company codes
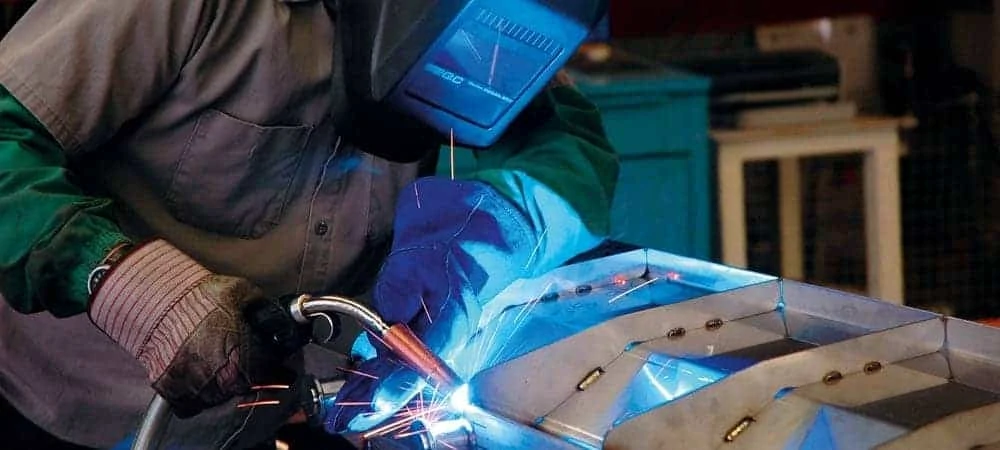

The US plants of Schenck Process were to be merged into one company code. In addition, around 1,300 customer and 800 supplier duplicates were to be harmonized in SAP, data quality was to be improved and the system was to be made easier to use.
All linked master and transaction data also had to be harmonized. The challenging transformation was completed in just five months with the help of cbs Corporate Business Solutions. The go-live took place over a weekend.
In addition to standardized transformation approaches, the cbs Enterprise Transformer (ET) tool was also used. Following the successful completion of the project, the management level can now access reliable real-time data from all areas of the company more quickly and use the meaningful key figures for strategic planning.
In 2005, Schenck Process, which until then had been part of Carl Schenck AG and thus also part of Dürr AG in Darmstadt, became independent through a management buy-out.
The company grew rapidly, particularly through acquisitions in the USA, Australia and Europe. Schenck Process has now decided to harmonize its organizational structure in the USA.
The company has five plants in the USA, which were previously assigned to three company codes and three purchasing and sales organizations.
All company codes shared a controlling area, a chart of accounts and an operating concern. The aim was to merge the plants into one company code and assign them to a common purchasing and sales organization.
In addition, existing customer and supplier master data in SAP was to be harmonized, data quality improved and the system made easier to use. Specifically, this involved around 1,300 customer and 800 supplier duplicates.
As a partner for the development of a transformation concept and the execution of the transformation, Schenck Process called in the consultants responsible for the implementation and realization of the company code merge and data harmonization in the quality assurance and production environment.
Following an in-depth system analysis, a technical concept was drawn up - both for merging the company codes and for customer and supplier harmonization.
As part of the project, an integration test and a user acceptance test were carried out with the involvement of the customer's specialist departments in order to check the transformation.
When merging the company codes, cbs recommended a minimally invasive approach based on business objects. The objects relevant for the migration and conversion were defined in collaboration with Schenck Process, as were the selection and mapping rules. The target company code and the associated purchasing and sales organization were expanded to include the master data of all plants.
An Enterprise Transformer was used for technical transformations of this kind. This standard software can be used to migrate data of any type from different ERP source releases.
At Schenck Process, the data was transferred using cbs ET, i.e. the values were converted directly in the database using the "direct input method". The complete history was transferred in all logistics modules.
SAP standard posting methods (Batch Input/LSMW), which are called up via ET, were used to convert open items and balances in the financial area. In the financial area, only open items, balances and assets were converted. No historical data was transferred to the financial area.
The solution for harmonizing the master data was to merge the duplicates into a leading customer and supplier master. This was defined by Schenck Process itself. All linked master data was also merged.
All customer/supplier numbers in the transaction data have been converted to the leading customer number. Non-leading master data was deleted. The go-live took place over a weekend together with the company code merger.
The go-live took place shortly after the end of the financial year in January 2019. The technical transformation was carried out over a weekend within 24 hours, reducing system downtime to a minimum without interrupting operations.
"We are very satisfied with the course of the project. The migration went completely smoothly from the first test run"
says Stephanie Hanl, CIO at Schenck Process.
Since the restructuring, Schenck Process in the USA now works with one company code and one purchasing and sales organization instead of three different ones. The entire transformation was completed in just five months.
"We are now benefiting from higher data quality and more consistency in the system and can carry out better evaluations of customer and supplier data"
explains Stephanie Hanl.
Further advantages: significantly easier handling of the system for the end user and valuable economies of scale in purchasing, which can be passed on directly to Schenck Process customers.
Schenck Process
Schenck Process is a global leader in the fields of weighing and feeding technology, screening and separation technology for bulk solids, dedusting and air filtration technology, pneumatic and mechanical conveying technology as well as automation and diagnostic technology.
The Group's innovative solutions are used in the food, plastics, processing technology, cement, logistics, construction materials, chemicals, mining and transportation sectors, among others.
Schenck Process can look back on more than 135 years of company history. Today, the company is represented in 20 countries on all continents. The group has 130 agencies, over 30 service centers and 22 modern production facilities worldwide. In 2018, Schenck Process generated a global turnover of 600 million euros with around 2500 employees.