Optimized material flow
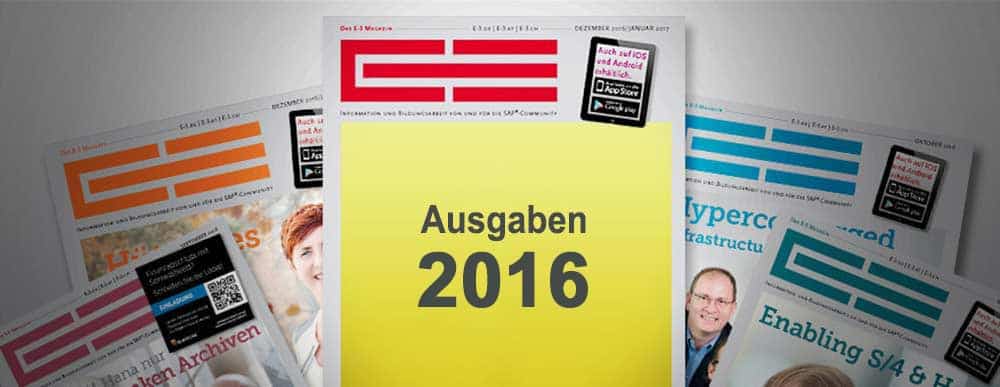
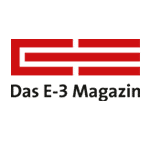
In addition to products for laser cutting, waterjet cutting, and bending, Bystronic offers its customers software and automation solutions, enabling them to implement user-friendly programming and individually tailored process solutions.
To ensure the highest quality standards, modern and efficient spare parts logistics are essential. Every month Bystronic ships 8000 to 10,000 spare parts items to customers all over the world - usually on the day the order is placed.
"To meet our ambitious targets, our workforce regularly worked overtime. During high load peaks, we also hired new employees."
explains Fabian Furrer, Head of Logistics at Bystronic.
Warehouse employees had to take the printed picking slips from storage location to storage location and from employee to employee. This manual circulation lasted until every single item of a customer order had been processed.
The process was error-prone and time-consuming. Therefore, the company decided to record the complete warehouse logistics on a mobile basis and to control the material flow independently of the storage location.
Bystronic has been working with the SAP consulting company Trimaster on various projects for some time now. The consultants from Trimaster are now familiar with the operational procedures and processes at Bystronic.
In addition, it played a role in the selection that Trimaster's headquarters are located in Zurich, only an hour's drive from Niederönz. This meant that the "detailed concept workshops" could be held without any great organizational effort.
"It was important for us to discuss the project steps and further process optimizations in detail with our partner during these workshops"
says Furrer.
In this case, the solution for mobile scanner-based mapping of logistics processes was called MSB Mobisys Solution Builder from SAP Software Solution Partner Mobisys. The mobile SAP add-on is logically structured, and the MSB Client user interface is clearly laid out.
In addition, the company was able to map all processes in spare parts logistics on mobile handheld scanners with a lean integration into the SAP ERP system, regardless of location.
"In the past, we had to deal with a veritable flood of paper in places. With the MSB Client, we have reduced this to the bare minimum.
explains Stefan Gygax, warehouse manager at Bystronic.
With paperless spare parts management, errors could also be avoided. The entire process chain, from ordering to picking to delivery, can be implemented quickly and efficiently via the MSB Client.
"We guarantee our customers the highest level of service. This also includes getting spare parts on their way unerringly from one day to the next. We should not make any mistakes in the process.
says Furrer.
"Because if a customer from Australia, Asia or South America orders a spare part and we ship the wrong part, we can't make up for that mistake immediately the next day."
The less efficient throughput with printed picking slips is a thing of the past with the new mobile solution.
"With the use of the MSB Client, we are just at an error rate of 0.05 percent of the scaffolded positions"
says Fabian Furrer.
"A value that is respectable when measured against common industry benchmarks."
This is made possible by the MSB Mobisys Solution Builder integration platform, which allows all mobile scanners to be seamlessly integrated into the SAP ERP system. When a spare parts order is received from a customer, a sales order is created in the SAP system, which in turn generates a delivery.
This lists the individual items of the ordered goods. Whereas in the past this list was printed out and manually forwarded to the responsible warehouse areas, warehouse employees now receive the necessary information on their mobile devices.
The MSB Client installed there clearly shows them open delivery items that they can select and process. Once all the items of an order have been removed from the respective areas and merged, the MSB Client posts the goods issue directly in the SAP system and the delivery bill is printed automatically. The employee packs and weighs the order and gets the delivery ready for shipping.