Trilux optimizes inventories and delivery readiness
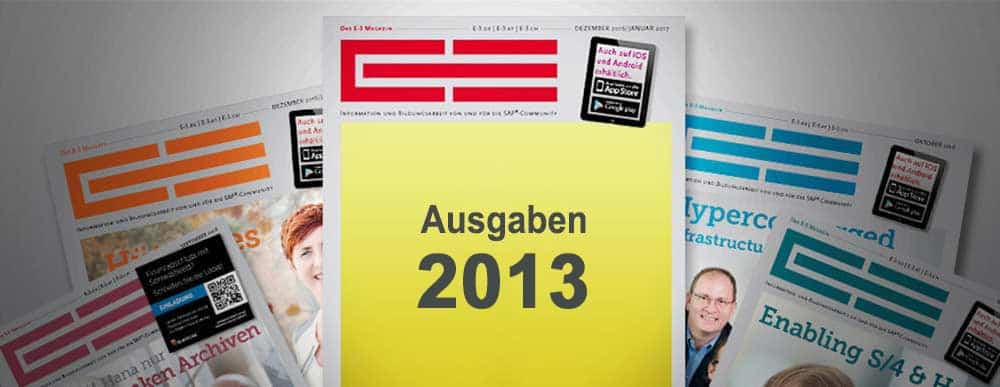
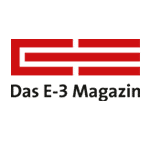
For this purpose, the portfolio available in stock to date was determined manually at irregular intervals, partly at the dispatchers' own discretion and after consultation with Sales.
Therefore, the establishment of a uniform and transparent process for defining and updating the warehouse portfolio was of great importance to Trilux. The focus was also on optimizing binding availability statements such as delivery times or ensuring inventories.
With the successful introduction of the G.I.B Dispo-Cockpit modules Forecast and Controlling, the expert for lighting systems and components has not only succeeded in achieving the project goals, but also in optimally regulating and recording inventories.
Here, the Dispo Cockpit Forecast supports the process of decentralized planning and simultaneously offers functions for consolidation in a central planning monitor. This application regulates and controls the transfer to the ERP system or alternative subsystems.
In addition, various functions are offered in the area of forecasting and monitoring through workflow, traffic light and alarm functions. In addition, the Dispo-Cockpit Forecast is easy to use and optimally unfolds its high efficiency.
Another advantage of using the module is the timely implementation of forecasting procedures to increase performance and optimize inventories. In the future, Trilux's demand will be calculated based on historical sales data, causal factors, marketing campaigns, market information and sales targets.
Thus, planning across all areas is ensured and in the course of this, the competitiveness of the company is further expanded. With the help of the inventory optimization of the G.I.B Dispo-Cockpit controlling, the potentials can be analyzed and the readiness for delivery can be ensured.
Here, the module primarily supports the industry-specific set of rules, which can be based on any number of dimensions such as delivery classes, product life cycle, recoverability (ABC) or consistency (XYZ).
All these sets of rules can be implemented as predefined industry content in G.I.B Dispo-Cockpit Controlling. This shortens the time to market and at the same time leads to an increased efficiency.
By means of the so-called Dispo-Cockpit Controlling Dashboard, the control of inventories and disposition is carried out from a central application. By specifying certain metrics, such as capital turnover and range, the company receives a suggestion for setting the MRP parameters that is optimally tailored to its needs. This has enabled Trilux to significantly improve its key performance indicators.
Along with this form of key figure optimization, the expert for lighting systems and components can now navigate through its inventory key figures with a goal-oriented ease, creating transparency that is relevant for decision-making.
The standardized and automated determination of so-called service classes leads to a significant reduction in the manual maintenance of master data and scheduling parameters. Based on these classes, an overarching set of rules is established for stocking at various stages of the value chain.
The service classes per article and plant are determined automatically on a monthly basis. In addition, an automatic calculation of the safety stocks for the determined warehouse portfolio is carried out as well as a comfortable preparation of the essential disposition key figures and functions for inventory management.
Honored with the G.I.B SCM Award 2012
As part of the G.I.B Success Days 2012, which took place under the motto "High-Performance", Trilux was presented with the SCM Award 2012 for the best optimization of inventories and delivery readiness.
Since the introduction of the G.I.B Dispo Cockpit and the implementation of the service classes, the company has been able to increase its service level, which includes punctual delivery on the promised date, from 85 percent to over 90 percent.
The introduction of the MRP cockpit also had a positive effect on inventory levels, which were successfully reduced by 30 percent.
"With this well-rounded total package from G.I.B, we were able to achieve all of our project goals and are very pleased with the significant improvement in our key figures."
sums up Stefan Renk, Supply Chain Manager at Trilux.
Since its foundation in 1912, Trilux has followed a long tradition. Today, 1300 employees work at the two plants Trilux and Trilux Medical in Arnsberg. Although both plants deal with the business area luminaires, they focus on different product portfolios.
Plant I, for example, develops and manufactures technical and decorative interior and exterior lighting for professional applications, while Plant II designs luminaires for medical supply units and special surgical lighting.