Bullwhip effect
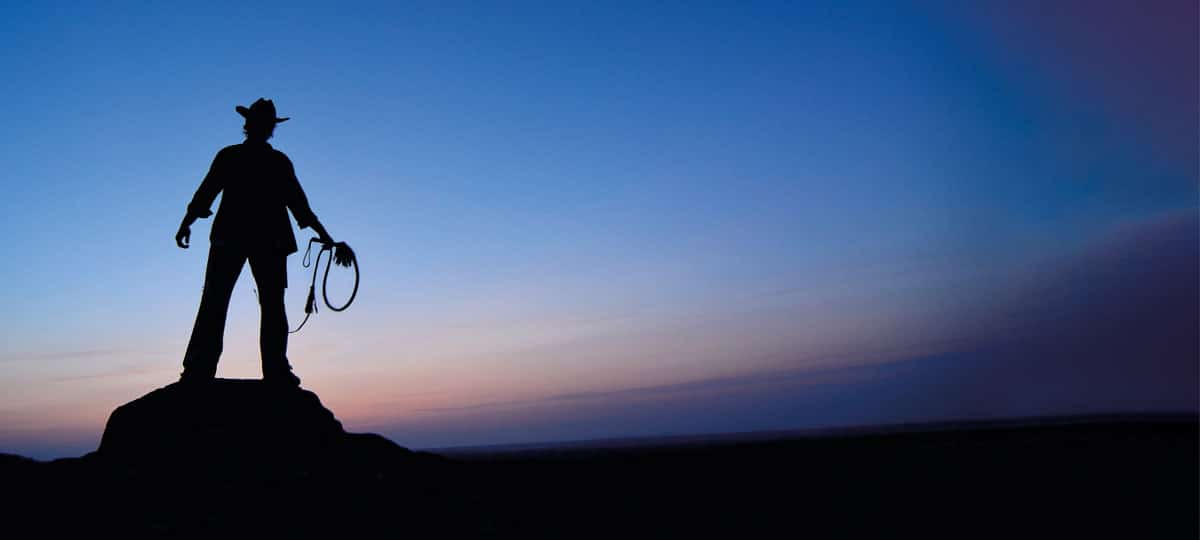
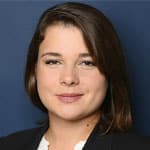
Integrated Business Planning: No more delivery schedule hassles
With processing in SAP IBP, Integrated Business Planning, and the use of machine learning, companies get the most out of their scheduling agreements. A scheduling agreement shows which materials are ordered under which conditions on specified dates within a period of time. But the plan doesn't always work out. In September, 65 percent of the companies surveyed by the ifo Institute were prevented from producing because raw materials and input materials were in short supply. As a result, not all orders could be processed. Material shortages currently have a lot to do with the impact of the Corona crisis and the Ukraine war on supply chains. Not all production can be adjusted quickly enough to fluctuations in supply and demand. But material shortages are also fundamentally a recurring phenomenon - because delivery schedules are often unreliable and also entail changes in the delivery schedule due to last-minute changes. Instead of certainty, the delivery schedule holds growing uncertainty.
Demand and delivery schedules
Here, the idea of delivery plans is a good one: customers and suppliers share information about future requirements and thus help each other to combat uncertainties at an early stage. When it works properly, this creates high delivery reliability for the customer and enables efficiency for the supplier - a win-win.
Fluctuations in information exchange cause headaches. A delivery schedule essentially contains relevant information about requirements and demand dates, which is collected from the customer and then handed over. This creates a picture of future demand patterns. Updated information continuously overwrites the outdated data. Depending on the individual processes, this happens once a week or several times a day. With each time, the demand information and thus the input for demand fulfillment is changed - sometimes more, sometimes less. In the short term, fluctuations are prevented by fixing horizons. In the medium and long term, however, they cause massive headaches - and generate costly inefficiencies.
The problem lies in the matter itself. Supply plans link two supply chains together. How well this works is influenced by many factors: by the company's own processes, priorities and restrictions, but also by suppliers and customers. Once the information is available, companies must first assess their customers' supply plan information. Specifically, the question is which information from which delivery schedule call-off is valid at which point in time and how it can be made usable. This is where the search for the needle in the haystack begins. The "good" information may be contained in yesterday's or last week's delivery schedule. Personal coordination with the customer would be too time-consuming and would not make economic sense.
However, with SAP IBP and extensions like Machine Learning, this search becomes feasible: First, the master data type is configured in IBP. It contains key attributes such as customer information, product information, scheduling agreement information, date and quantity. This information is mapped using IBP with the help of master data and key figures. In the process, the various statuses of the scheduling agreement are saved and stored for further use. In the next step, the scheduling agreement statuses, which were previously mapped in key figures, are integrated into the forecast - so they not only offer an informative added value in SAP IBP, but also an actual one in use: Changes to the scheduling agreements and their items can now be mapped over time.
The next step is to determine the point in time when the delivery schedule was most stable, i.e. closest to reality. The classical algorithms are available in IBP for this calculation. The smallest deviation in the system forms the basis for building a statistical forecast. Planners can now compare this forecast with the most reliable period in the delivery schedule - and continue working with the best key figures in the sales and operations process.
Machine Learning
So much for the helpful, but also limited use in IBP. Because there is much more that can be done. For example, using machine learning. Here, planners can use the calculated errors in the delivery schedule as an independent variable to enrich external algorithms. These can then be used as input to generate better forecasts. If enough data is available, the forecast error itself can also be used. In addition, it is possible to extract the data from the IBP via O-Data services or other integration interfaces. There, the data is enriched with further statistical methods available in the Python Library and then fed back into SAP IBP. The advantage is that such ML environments allow significantly more extensive analyses than the standard from IBP.