SCM and IIoT
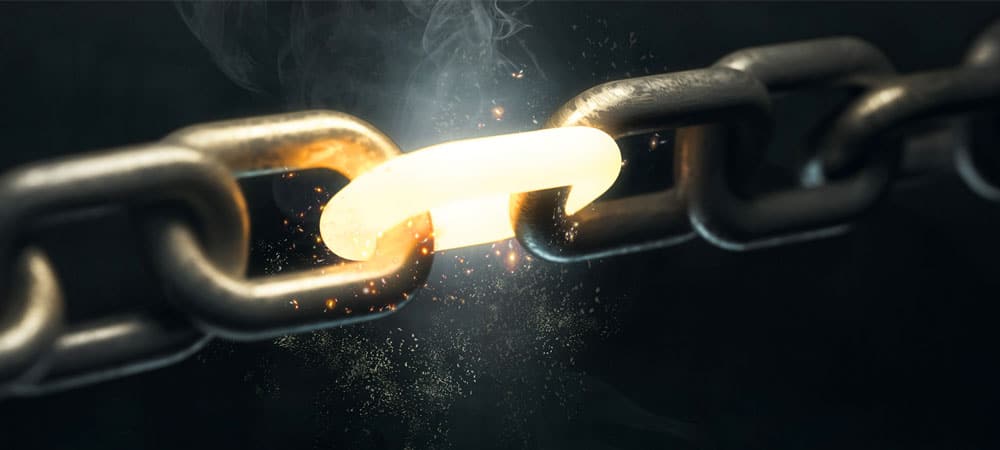
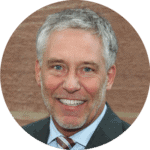
According to a new PwC study, industrial companies around the world invest more than one trillion euros each year in building digital factories. This spirit of optimism can also be observed in the SAP community, see E-3 cover story June 2022: from IoT to ERP. Despite high investments, however, more than half of the 700 companies surveyed worldwide (including 100 headquartered in Germany) are still at a very early stage of implementing digital systems and technologies. This is according to the Digital Factory Transformation Survey 2022, published by the auditing and consulting firm PwC on the occasion of the Hannover Messe this year. Where the focus used to be on cost reduction and efficiency, today the emphasis is on flexibility and resilience.
On the occasion of the Hannover Messe, the digital association Bitkom surveyed that 65 percent of industrial companies with 100 or more employees use special applications for Industrie 4.0, and another 25 percent are planning to use them. According to Bitkom, Industry 4.0 has arrived in the manufacturing sector. Overall, 90 percent of companies are focusing on Industrie 4.0 - and are investing around 6 percent of their total annual revenue in it. Last year, according to Bitkom, the figure was slightly lower at 83 percent, and in 2019 it was only 74 percent. Only 8 percent are not currently planning to use special applications, but can imagine doing so in the future. For all of the companies surveyed without exception, Industry 4.0 is an issue today.
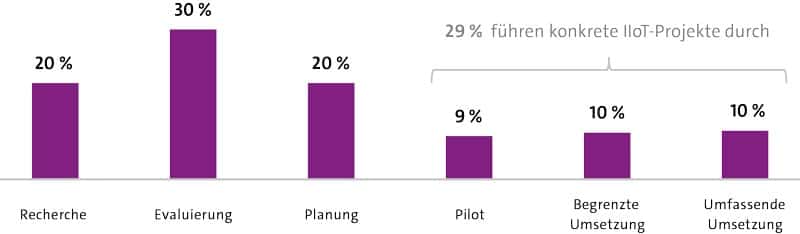
SAP's Ariba offering clearly shows that the digitization of production and trade goes far beyond the topics of Industry 4.0 and IIoT, however. End-to-end then also includes SCM, logistics and marketplaces. Every second company now uses digital marketplaces to buy or sell products and services, PwC has surveyed. Another 17 percent are planning to enter e-commerce in the next twelve months. For every fifth company, however, digital marketplaces are not an issue.
For manufacturing companies, the current situation is characterized by ongoing crises: Disrupted supply chains, major fluctuations in demand and acute inflationary pressure are just some of the challenges facing businesses. As a result, almost all companies are being forced to make their production more flexible and to rely on a value chain model that focuses on resilience. Many existing SAP customers are therefore investing in their digital transformation - but a differentiated picture is emerging, to which SAP has only partially responded: PwC's global survey of 700 industrial companies shows that the number of companies using digital technologies to reduce costs has plummeted, while the number of companies investing to strengthen their flexibility and resilience has increased by 76 percent overall.
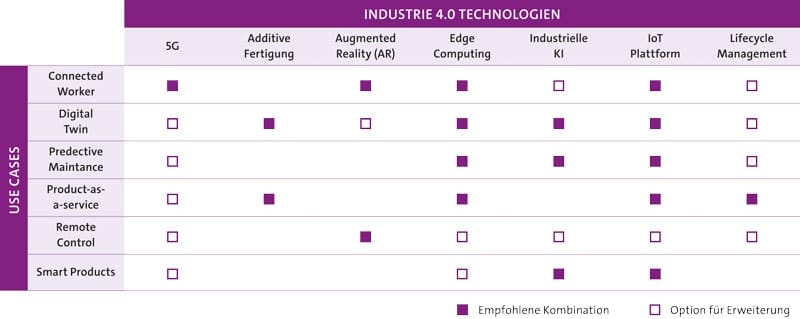
Remote monitoring and real time
IoT platforms that can be used to network data, products, machines or processes are used by 35 percent of manufacturing companies and almost as many are planning to do so, according to a survey by Bitkom for Germany. Almost every second company sees the greatest potential in remote monitoring and real-time insights into manufacturing processes. 42 percent value the acceleration of processes. 39 percent see potential in predictive maintenance. This refers to the predictive maintenance of machines and systems, where, for example, parts are only replaced when necessary and then in good time before a defect occurs. According to Bitkom, IoT platforms also help to achieve higher-level operational goals such as increasing sales, improving quality and reducing costs. IoT platforms network products, machines and people in industry and thus drive the digital transformation.
The growing importance of sustainable production processes has also greatly changed the way SAP's existing customers invest in the future. Fears that the Corona crisis would push the issue of sustainability into the background among large industrial companies have turned out to be wrong. The opposite is true: The number of companies investing in digital technologies to operate more sustainably has more than doubled. "The study shows that investment in sustainability has already been driven strongly by increasing regulatory requirements. The need for operational resilience has added to this momentum."said Reinhard Geissbauer, Partner and Head of Digital Transformation Europe at PwC.
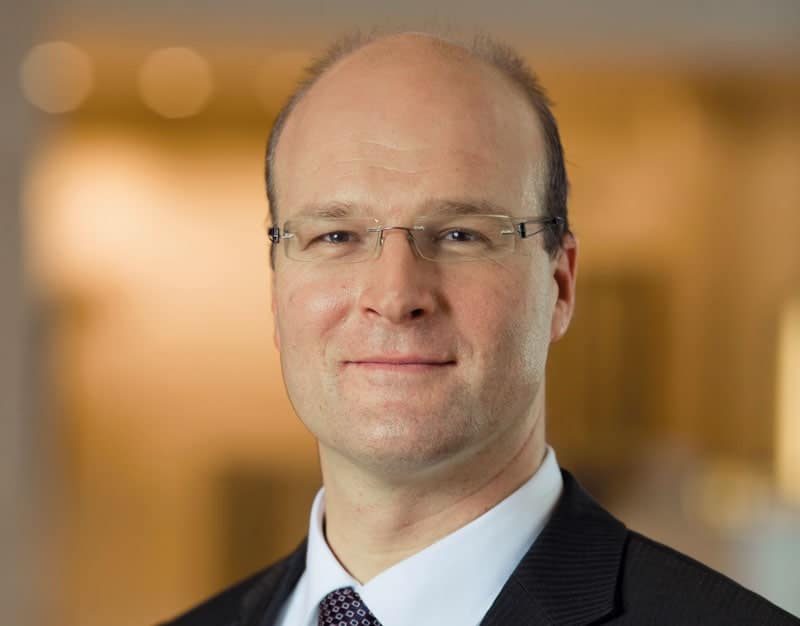
Digitization of industry offers great potential in the reduction of CO2 emissions. For example, if the use of digital technologies is accelerated, up to 64 million tons of CO2 can be saved in Germany alone in 2030 - that's 17 percent of the total planned CO2 savings under the 2030 climate target, according to the Bitkom study "Climate effects of digitization". According to the study, the use of digital twins, i.e. the simulation and optimization of physical products or processes, can save 33 million tons of CO2. A further 31 million tons can be avoided through increased automation in production, as digital technologies reduce manual interventions and the use of materials and optimize processes.
The PwC study shows that digital transformation in industry has many facets: Companies rely on back-bone IT systems such as the widely used enterprise resource planning suites (ERP) and manufacturing execution systems (MES), but also on new innovations such as operating platforms for devices and sensors networked via the Industrial Internet of Things (IIoT). In addition, software-based business applications or use cases such as systems for production quality control or machine maintenance can be found in many plants. In addition, technologies such as drones, wearables or automated robotic vehicles are in use in many places. "Manufacturing companies are now realizing that many of these digital innovations need to be combined to transform manufacturing processes - from design to distribution", said Michael Bruns, partner at PwC.
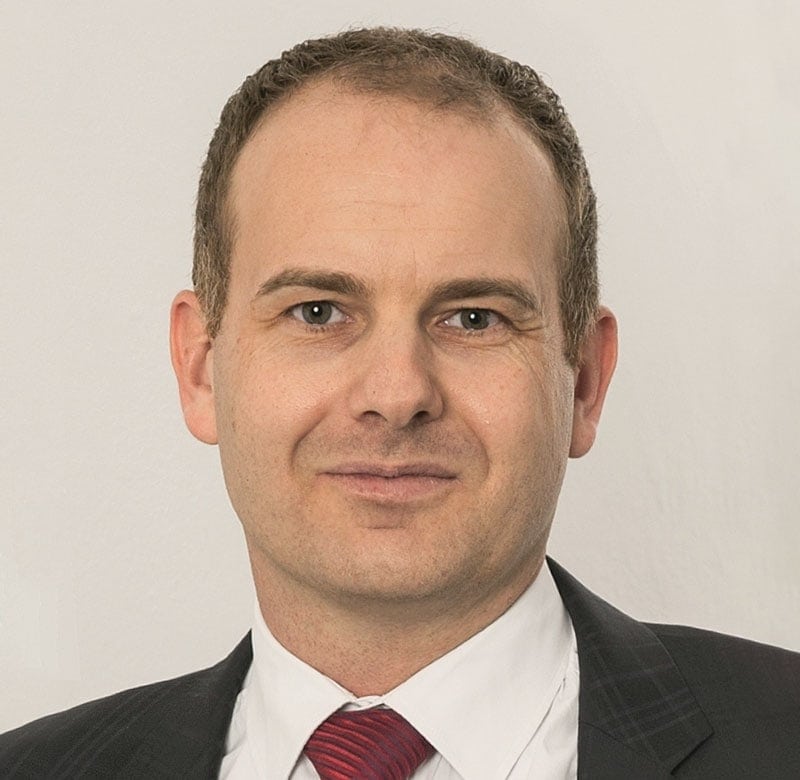
The companies in the PwC survey plan to invest 1.8 percent of their annual net sales in the coming years - a significant increase in capital commitment compared to previous PwC studies. This represents an estimated total volume for digital investments in the manufacturing industry of more than one trillion euros. Nevertheless, some companies should continue to increase their investment rates, as the study shows a strong correlation between high investments and high returns.
The PwC study also shows that companies that make larger investments in digitization and accept the associated risk often achieve better results and recoup their investments more quickly. Most investments in digital technologies have a payback period of around three years, but in some cases even large investments in basic technologies such as IT backbone systems can pay for themselves within a year. "There is no universal formula for digital transformation, because success is only achieved through a complex interplay of systemic changes to the IT architecture, the elaboration of business use cases and the implementation of specific technologies", said Michael Bruns. "Investing too little means missing out on transformative technologies, but conversely, it can also mean investing too much in applications that aren't relevant to the business."
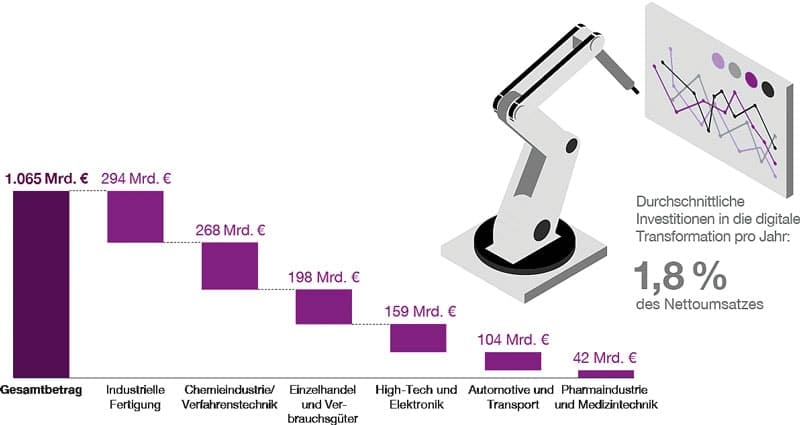
Source: PwC 2022.
Conserving resources, saving energy, reducing CO2 emissions: Industry plays a key role on the road to greater sustainability and climate protection. Digitization is the key lever for achieving these goals. Thus, this year's Hannover Messe was also held under the guiding theme of "Digitalization and Sustainability". A recent representative survey commissioned by the digital association Bitkom highlights the importance of digital applications for greater climate protection. According to the survey, eight out of ten companies say that Industry 4.0 contributes to sustainable production. Around 550 industrial companies in Germany with 100 or more employees were surveyed.
At the same time, 91 percent emphasize that Industry 4.0 is indispensable in order to survive in international competition. Six out of ten companies say that work will become less error-prone and conventional business models will change. "Through consistent digitization, the industry can face two urgent challenges at the same time: Digitization makes companies more sustainable and more competitive"said Christina Raab, member of the Bitkom Executive Board.
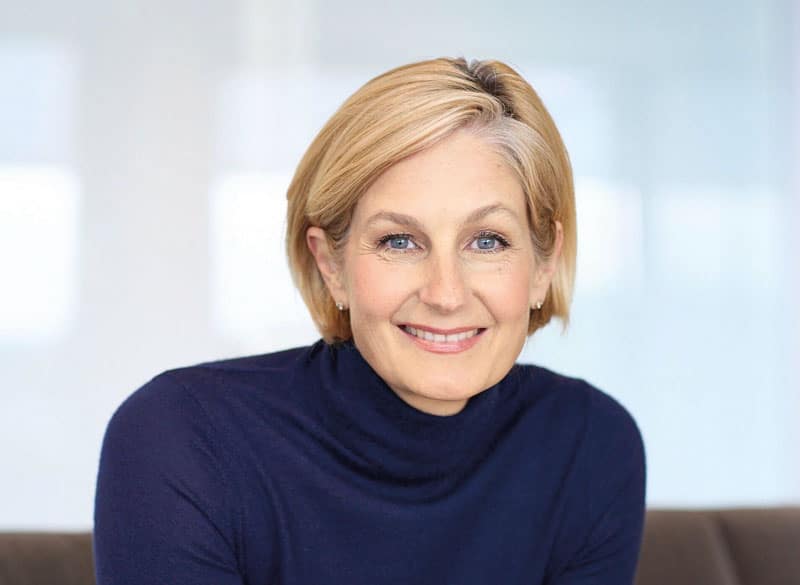
Digitization deficits
The PwC study, on the other hand, shows that despite the abundance of new technologies and the high level of investment, many companies are unable to implement their digitization plans. The PwC results show that it is often more difficult than expected for companies to consistently drive forward digitization. To put this in perspective, in a 2014 PwC survey, 80 percent of companies said they planned to complete their digitization projects by the end of 2019. These optimistic expectations were disappointed in many places. Although the implementation rate of new IT systems, digital business applications and applied technologies has risen sharply over the past four years, the digital maturity level at many of the world's largest industrial companies is still not where it should be. More than 60 percent of companies are still in the early stages of their digital transformation. Only 10 percent of companies are already benefiting from the high returns, flexibility and resilience of their fully completed digital transformation, or are at least close to doing so.
After all, 39 percent of German industrial companies see themselves as pioneers of Industry 4.0. On the other hand, one in two groups themselves as laggards, Bitkom surveyed on the occasion of the Hannover Messe. 7 percent of companies feel left behind. Small and medium-sized enterprises have the greatest need to catch up. For example, 58 percent of companies with 100 to 499 employees describe themselves as laggards and only 30 percent as pioneers. Among large companies with 500 or more employees, the reverse is true: only 37 percent see themselves as laggards, while more than half see themselves as pioneers.
The biggest obstacle to establishing Industrie 4.0 is a lack of financial resources, according to the companies' own statements to Bitkom. But two-thirds also see data protection requirements as an obstacle. 61 percent identify IT security requirements as a problem, and for 58 percent the issue is too complex. Around half see a lack of skilled workers as an obstacle, and four out of ten companies complain about the susceptibility of systems to faults. 29 percent lack an exchange with companies facing similar challenges.
In contrast, a lack of external advice, a lack of knowledge about best-practice solutions or insufficient availability of marketable solutions play only a minor role. Just 6 percent complain about a lack of acceptance among the workforce. Christina Raab, member of the Bitkom Executive Board: "According to their management, one in three companies simply does not have time to deal with digitization. In the future, industrial business will be close to 100 percent digital. Digitization belongs at the top of every manager's to-do list."
Artificial intelligence is one of the key technologies in industry. It has found application in almost four out of ten companies - 66 percent of them use AI in production to automate processes, 64 percent for data analysis in process monitoring, 35 percent apply both uses. Concrete plans for the use of AI are in place for 17 percent of the companies. For one in four companies, AI is not yet an issue. Forty-two percent of all industrial companies see the biggest obstacle to the use of AI in the lack of data. 40 percent think the effort involved in implementation in particular is too high, 36 percent lack standards and 32 percent are hindered by the certification process. A good one in four companies (28 percent) cite ethical reasons as an obstacle to the use of AI.
At the Hannover Messe, it became clear that there are only a few pioneers and many stragglers for the Industrial Internet of Things (IIoT) in Germany. Only 10 percent of industrial companies are carrying out comprehensive IIoT projects, and another 10 percent to a limited extent. Most companies are currently still busy with research, evaluation, planning and pilot projects. This is shown in the study "Industrial IoT in Germany 2022" by IDC.
According to the study, IIoT use in German industry has remained at a low level for around two years. As a result, many companies are missing the opportunity to respond better to problems in supply and value chains. Yet the needs for industry in Germany would be enormous: from rising energy and high freight costs to disrupted supply chains and war in the middle of Europe. Especially in times as volatile as these, reliable information and flexible business processes are necessary. This is exactly what IIoT enables. It enables companies to readjust their processes in the event of unforeseeable developments or to quickly adapt their production to new products. In addition, resources can be used in a more targeted manner in order to produce more sustainably and avoid rejects.
Despite these advantages, IIoT is only slowly gaining acceptance in Germany. This is partly due to the economic situation in recent years, which has been marked by crises. As a result, business metrics such as profit and costs, productivity and customer loyalty have become the focus for companies. However, the reasons for low IIoT adoption are not so much a lack of will or interest, but rather the implementation challenges themselves. Skepticism, lack of know-how and outdated technologies are at the forefront.
Digital Twins
According to the Capgemini study "Digital Twins: Adding Intelligence to the Real World," 60 percent of companies in key industries are already using digital twins as catalysts not only to improve operationally, but also to meet their sustainability agenda. Digital twins can simulate the physical world, thereby making better use of resources, reducing CO2 emissions, optimizing delivery and transportation networks, and increasing employee safety.
Bitkom has surveyed that digital twins are used in every third company. Another fifth are planning to use them. "Digital twins are digital copies of real-world objects - from products and machines to entire factories. Thanks to them, production and maintenance processes can be massively accelerated and continuously optimized in everyday use," explained Christina Raab at the Hannover Messe. The importance of digital twins will continue to grow in the medium term. A large majority of companies, for example, believe that the use of digital twins will increase over the next five years. Only 17 percent assume that the relevance will not change.
A digital twin is a virtual image of a physical system that can model, simulate, monitor, analyze and continuously optimize the physical world. It aims to bridge the gap between physical and digital with the right frequency and accuracy, improving performance and sustainability. The technology is used in a variety of cases across the value chain - from design and conceptualization to manufacturing and production - and enables a decentralized, collaborative and flexible way of working. It can serve as a tool to experiment with different scenarios and evaluate the impact of each decision without real risks, resulting in shorter time-to-market, lower costs and higher safety.
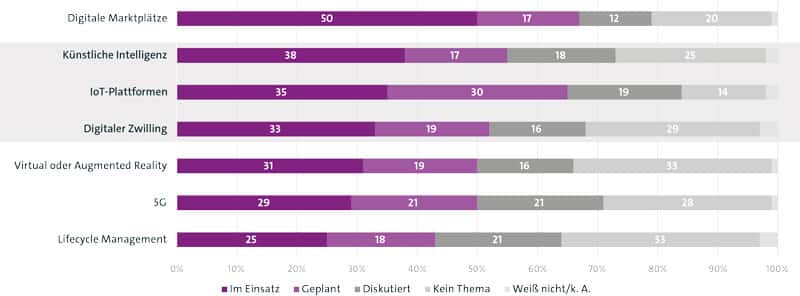
Source: Bitkom Research 2022.
Environmental, Social, Governance
According to the Capgemini study, 57 percent of companies believe that digital twin technology is critical to improving sustainability efforts. Which in turn aligns with their ESG (environmental, social, governance) goals. Digital twins enable flexible ways of working that can minimize risk and encourage collaboration. This creates a unique opportunity to increase profitability while optimizing the use of resources along the value chain. Supply chain challenges arising from the pandemic and Russia's attack on Ukraine could result in a potential cumulative loss of €920 billion in eurozone GDP by 2023, says a study published by consultancy Accenture.
The study suggests that supply chains need to be reinvented to meet a paradigm shift. Supply chains were designed primarily to optimize costs. However, in today's world, they must also be resilient and flexible to respond to supply uncertainties. At the same time, they are becoming an important competitive advantage to enable future growth.
Supply chains must be able to absorb, adapt to, and recover from disruptions whenever and wherever they occur. Improved dynamic insights, risk detection, and mitigation solutions enable companies to deal with sudden changes in the supply chain. Scenario planning and risk and opportunity analysis help adapt to evolving supply and demand. Network modeling and simulation, stress testing, strategic buffer sizing, and multi-sourcing options enable companies to manage uncertainty.
Supply chains need to be customer-centric and flexible to adapt quickly and cost-effectively to changes in demand. Capturing new data sets, including real-time data, inside and outside the enterprise across the value chain will be critical. Automation and artificial intelligence will enable companies to quickly identify new data patterns to make better decisions. Moving from centralized, linear delivery models to decentralized networks with on-demand production, and in some cases moving production closer to the point of sale, can help companies better meet customer expectations for order fulfillment.
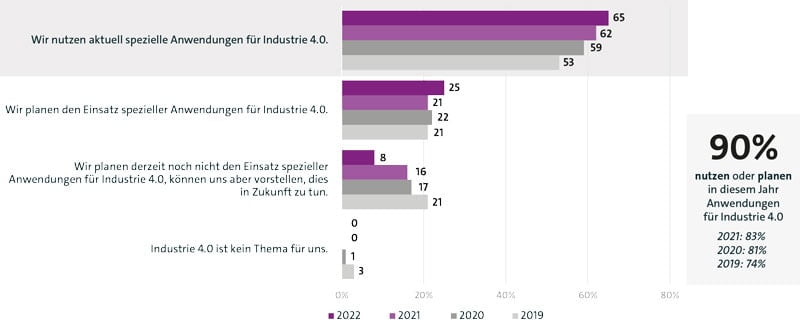
