The right machine for the construction project
![[shutterstock:572387182, yuttana Contributor Studio]](https://e3mag.com/wp-content/uploads/2017/02/shutterstock_572387182.jpg)
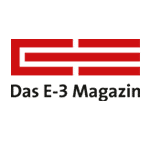
The Leonhard-Weiss construction company was founded in 1900 as a family business. Today, the group employs over 4,400 people.
The business areas include road and network construction, rail infrastructure construction, civil engineering and turnkey construction.
The road and network construction segment covers the construction of roads, paths and utility networks. Mainly in Southern Germany, 400 machines and 180 machinists are in operation.
These have to be scheduled for use on the various construction sites in accordance with the specific requirements.
Ten construction machinery planners are responsible for scheduling construction machinery and machine operators at the main sites in Göppingen and Satteldorf and at the Günzburg and Bad Mergentheim branches.
Renting third-party equipment and ordering transport are also part of their tasks. Until 2009, this planning was done in various ways in Excel, on paper and planning boards.
The big disadvantage of this was that each dispatcher only had his own planning in view, but no insight into the planning and availability of resources of his colleagues.
Thus, consultations and telephone inquiries among the construction machine dispatchers were often necessary.
For this reason, Leonhard Weiss decided to introduce a central tool for IT-supported deployment planning for construction machine scheduling in the Technology department in order to improve planning transparency and clarity.
A decisive criterion for the selection of a solution was its ability to integrate with SAP PM, as this is where the resources for the operations are stored.
The choice finally fell on MobileX-Dispatch from MobileX AG. The solution was introduced in the fall of 2009.
Effectiveness increased
Since spring 2010, the construction machine dispatchers at Leonhard Weiss have been working with IT-supported deployment planning.
Scheduling is usually done one to three weeks in advance, but also from one day to the next - depending on the client.
The advantages of the central scheduling solution come into their own, especially when it comes to short-term planning. Since all construction machine dispatchers now work with the same tool, it is possible to see at a glance which machines are available and where they are located.
For this purpose, the dispatchers can display the resources in a Gantt chart, in a list or on a map.
The resources are divided into certain groups according to machine types. Among them are the individual vehicles such as excavators, caterpillars, rollers or tractors and their respective master machinists.
If a requested machine is not available, the dispatcher must rent the machine from an outside service provider and also organize its transport to the construction site.
Planning transparency across locations
After five years of scheduling with MobileX-Dispatch, those responsible for construction machine scheduling at Leonhard Weiss GmbH & Co. KG draw a positive conclusion:
"Planning transparency and clarity in the area of construction equipment scheduling in the Engineering department has improved through the cross-site use of MobileX-Dispatch."
Technical field service
The technical field service, which is responsible for the maintenance and repair of the machines on site, will also be scheduled with MobileX-Dispatch in the future.
To this end, the rollout of the solution is currently taking place for three workshop dispatchers who control 15 field service employees.
The dispatchers create the orders in SAP PM and plan them in MobileX-Dispatch. The lead time for maintenance here is about one week.
In the event of malfunctions, the field technicians usually have to be sent to a construction site at short notice. Here, the foremen are supported by a telematics system installed in the vehicles.
GPS tracking allows them to recognize the current location of the technicians and thus send the colleague to the job site who is not only available, but also nearby.