The Industry 4.0 operating system
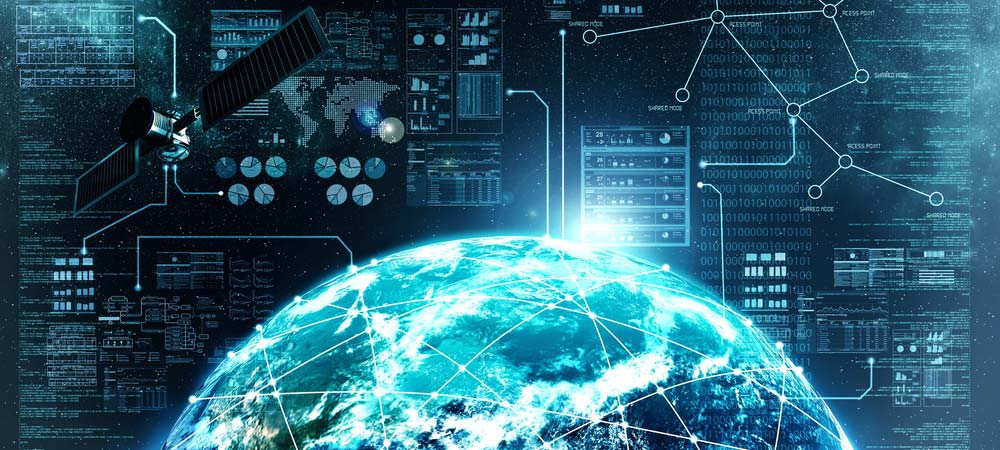
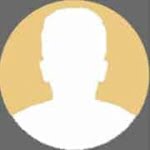
Insights into the IT stack show how the open operating system BaSys 4.0, the data infrastructure and SAP harmonize. Networking production lines is thus much easier in practice than before and leads to one hundred percent digitization - from the shopping cart to production and shipping.
Networked production, in which all work steps are digitized, takes place on less than one square meter. Built in Fischertechnik, the model reproduces real production in detail, which can be followed from the high rack through kilns and robots to manufacturing via quality control and packaging.
A dashboard first shows the order that came in mobile and was entered in the SAP backend. Then, in the background, the SAP SD module generated the sales order. The SAP system reports to the BaSys 4.0 middleware the ordered material - and where it is stored in the warehouse.
On a commercially available tablet, each further step is now visualized from the order to the product shipment. The process chain to be executed is based on real data streams and includes interfaces to the programmable logic controller (PLC) or bus systems, allowing one to intervene in production at any time. The processed sensor data from the networked devices is stored in the Data Lake (ObjectStore, Hadoop, etc.).
This live demo was presented at the Hannover Messe in early April and showed Shopfloor 4.0, the name of the solution developed by the Fraunhofer Institute for Experimental Software Engineering (IESE) together with NetApp and Objective Partner.
Shopfloor 4.0 overcomes the biggest hurdle so far in Industrie 4.0 applications: Data exchange can now take place automatically in a networked production environment. This effect is based on the coordinated interaction of BaSys 4.0 with its digital twins, an efficient data infrastructure and SAP, which has been coupled to the IT stack. But what do these individual building blocks accomplish?
Communication by means of digital twin
The software basis for Shopfloor 4.0 is being created by Fraunhofer IESE, which has developed BaSys 4.0 with 14 partners from research and industry. The result is an operating system for production plants that creates a language standard for Industry 4.0. The project has been funded by the Federal Ministry of Education and Research since 2016.
BaSys 4.0 is a middleware that networks machines - store floor and office floor, i.e. production and IT landscape, now talk to each other. The open source solution ensures communication by taking over the tasks of management shells to which machines send their data.
Building on BaSys 4.0, Fraunhofer IESE, Objective Partner, and NetApp have developed the solution Shopfloor 4.0, which comes up with support functions. For this purpose, the software platform loads a digital twin for each machine component.
A data model structures and specifies how the data sent is to be organized. BaSys 4.0 assigns the production data to a workpiece, merges the values and stores them in a management shell.
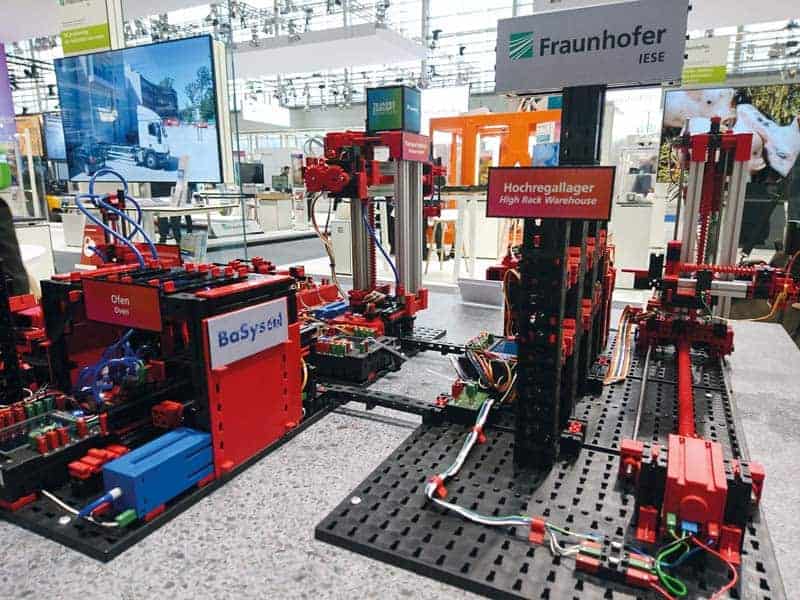
From this point on, data is given a meaning, a semantics. It no longer matters from which machine the data comes via which communication protocol. The values can be processed further. In this way, the workpiece and its data run through the production line together.
This enables the quality of the individual production steps and the manufacturing process as a whole to be tracked. Even before a production order starts, digital twins can prove to be extremely relevant in practice.
For example, what happens if the next order in the machine planning calendar now includes 800 workpieces instead of 500? A digital twin allows you to look ahead. The software-defined simulation illustrates whether the machine can run through or must be serviced beforehand.
Not only can large orders be run through in advance, but also the possible need to replace sensors - of which a machine can have hundreds. Each sensor has its own software. A simulation clarifies whether the software can also communicate with the system in the new version after the update.
Service based programming
In addition to cross-protocol end-to-end communication in the machine park, BaSys 4.0 also combines another decisive advance: Programmable logic controllers provide the services that are called up by service users.
The service users therefore define the production processes and change them. To do this, the machines have to be reprogrammed. This can now be done much more efficiently than if it had to be done with the PLC as before.
This leads to service-based manufacturing, which can be used to run small batches up to batch size 1. In practice, a production manager can also insert the order that is most important. The system simply calls up the necessary service - and the new production series starts.
Establishment of the efficient data infrastructure
However, the BaSys 4.0 middleware generates the effects described only if it runs in a data infrastructure in which the data is highly available. NetApp meets this requirement with its software and data management system for Shopfloor 4.0.
Various technologies work together in the designed reference architecture so that end-to-end processes can be mapped seamlessly on-premises and in the cloud. First, the storage provisioner NetApp Trident and snapshots make BaSys 4.0 highly available in the container.
NetApp is currently the only vendor to solve this challenge by connecting Trident containers with a persistence layer. Otherwise, a container would lose data after a reboot or in the course of a system failure.
The containers can be made available via the NetApp Kubernetes Service (NKS). NKS simplifies and automates the setup, operation, and scaling of containers.
The best choice for this container environment is NetApp hyperconverged infrastructure (HCI) because it offers horizontal scalability and guaranteed performance (quality of service). The missing key building block is the NetApp Data Fabric, which unifies data management across distributed resources.
It seamlessly connects private, public and hybrid cloud environments without the threat of cloud vendor lock-in. As a result, Shopfloor 4.0 gains flexibility and scalability.
Integration in SAP
The Shopfloor 4.0 reference architecture links Objective Partner to SAP, thereby linking production with the commercial and business processes in the company. Only this results in an end-to-end view that includes the client in the sense of a successful customer journey.
Specifically, BaSys 4.0 communicates with the SAP Data Hub, which receives the data in a standard from the middleware, prepares it in an SAP-compliant manner and transfers it to the ERP system or the SAP standard processes.
The data from manufacturing that BaSys 4.0 manages can be used for other applications - for example, machine learning. The SAP Data Hub, which like BaSys 4.0 runs in a Kubernetes cluster, offers the opportunity to combine such an AI application with standard SAP processes.
In addition, the SAP Cloud Platform (SCP) provides algorithms based on open source products from hyperscalers such as Google, Microsoft Azure, and Amazon Web Services. The training of the algorithms with data takes place in the cloud, for which cross-platform data management, as realized by the NetApp Data Fabric, paves the way.
Until now, companies needed a data management solution that would take the data to where it needed to be processed - and retrieve that data afterwards. Copying data end-to-end today, however, is no longer enough. An application must be able to reach through end-to-end.
A native data infrastructure service that integrates with the largest hyperscalers and is ready in seconds solves this challenge. At NetApp, this cloudnative data storage is called Cloud Volumes Service.
It gives applications, whether analytics, databases or DevOps, fast access to data. The ONTAP storage operating system accelerates operations to 20 times the usual speed.
Customization and mass production go together
For the time being, there are no technical limits to connecting everything with everything else. How far companies want to go is up to them. With Shopfloor 4.0, a solution is now available that clears the way to Industry 4.0 for manufacturing companies and simplifies the end-to-end digitization of processes.
Continuous intervention in plant control, the parallel processing of orders and the rapid set-up of a new production line are among the most important features of networked production environments that build on the technology and know-how mix of the cooperation partners.
In the implementation, the partners share the tasks: NetApp provides the IT stack, Fraunhofer IESE integrates its open source software BaSys 4.0, and Objective Partner provides first-level support for the solution, in which BaSys 4.0, data infrastructure, and SAP processes interact perfectly - for service-based manufacturing that brings together customer individuality and mass production.