The five days factory
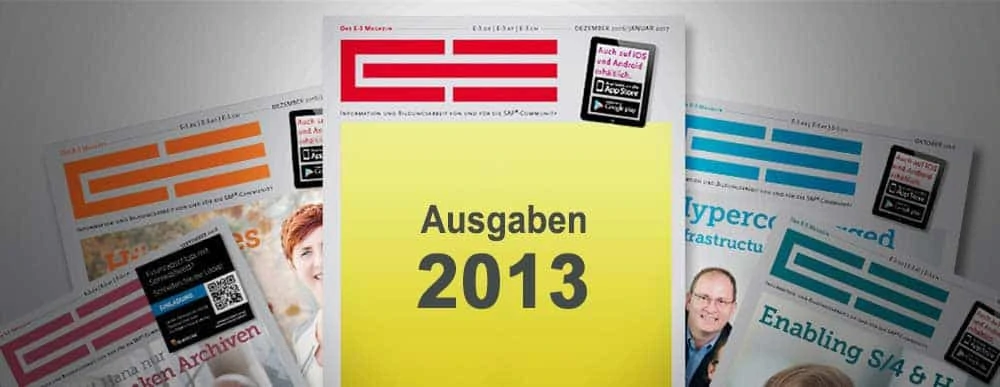
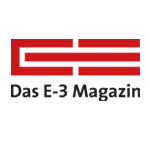
With the construction of the new Budapest factory in 2010, the management of the manufacturer of braking and on-board systems for rail vehicles called for the introduction of the five-day factory.
In the actual implementation, the work areas in production and the physical supply of materials were completely redesigned in line with the latest findings. Knorr-Bremse was also able to fundamentally improve its order planning processes with the help of a specially developed IT solution.
The company was looking for an integrated solution to achieve the goals of the five-day factory and the planned Heijunka process. SAP ERP was already in use, so the task now was to adapt it to the specific challenges in Budapest.
Whereas in the old factory production was still organized on a workshop principle six days a week, Knorr-Bremse reduced bottlenecks by, among other things, investing in an electroplating and painting line, value stream analyses and close dovetailing of the supply chain with the production system. A further step towards a lean manufacturing approach was the changeover of the manufacturing principle to cell production.
Solutions of this kind are considered commonplace in the high-volume automotive sector. In the rail vehicle industry, however, where production tends to be geared to low volumes or one-offs, this concept represents an absolute novelty.
The most important element of the five-day principle is the drastic reduction in the throughput times of internal production. Production and work organization processes were also geared to this.
Knorr-Bremse Budapest was breaking new ground at the time. Previously, for example, the production of a block brake unit took between 15 and 25 working days from the provision of raw materials to final assembly and testing.
In the five-day factory, the entire production must be realized in five working days, which is about 20 to 25 percent of the time previously estimated. Parallel to this, the quantity of materials tied up in the process and thus the inventory values are also reduced to a quarter of the original quantity.
The change to the new production process offers advantages: The processing of customer orders works more flexibly and reliably, changes can be implemented more quickly, capacities are used optimally, and the efficiency of the supply chain has also been improved.
By using modern development techniques, customers receive products that meet the highest quality standards.
The lean manufacturing approach
But how does the five-day factory work in detail? It is important that production reserves agreed throughput times in advance and, if possible, starts mechanical processing on the first day after approval.
The reliability and resilience of the system are greatly influenced by the supplier's ability to deliver, so great importance must be placed on the reliability of the external supply network.
Each part to be coated must arrive at the surface treatment and coating center at the end of the production and purchasing steps, but within the specified time limits (on the third day), which passes all coated parts on to assembly with a turnaround time of about one day (fourth day).
At the same time, the parts required for assembly must also arrive. After all, an absolutely reliable supply of materials of consistently good quality is essential.
The process (fifth day) is completed with final assembly and functional testing. The product is thus ready for delivery to the end user after only five days.
Initial situation
The processes and system implementation in the old Budapest plant were based on classic MRP planning. Here, starting from the independent requirements via the MRP run, the bills of material were exploded, requirements planned and order proposals (planned orders and purchase requisitions/delivery schedule lines) generated.
An attempt was made to manufacture mostly in large batches. Mechanical production was mainly oriented to the deadlines from the MRP and less to the planned assembly program.
The other side of the coin was, among other things, that too much was produced too early, resulting in surplus production. As a result, large batch quantities led to capacity bottlenecks and reduced flexibility in production; the lack of relationship knowledge between component production and final assembly resulted in overproduction at component level; unexpectedly high demand in certain periods led to capacity overload at the supplier and thus to a lack of component availability. Likewise, the effort required for capacity smoothing, control and deadline tracking was higher.
Realization
To achieve the goals of the five-day factory, it was necessary, on the one hand, to change system settings such as lot-sizing procedures and, on the other hand, to adapt the SAP tools for production planning and control to the goals of the five-day factory and the planned Heijunka process.
The graphic planning board was used for the exact planning and control of assembly and mechanical production. In the first step, the bottlenecks in the individual production lines in assembly were analyzed and provided with realistic times in the routings.
Consilio thus enabled finite planning of the lines. With the help of the planning board, the individual assembly lines can now be optimally occupied, taking into account the actual capacity situation. Based on the scheduled orders, the MRP then plans the requirements and generates order proposals (planned orders).
In order to ensure that only that is produced in mechanical production that is also assembled in assembly on the following days, only planned orders can be converted into production orders whose pegged requirements are actually dispatched, i.e. a production date is actually planned in assembly. Mechanical production is also dispatched via the planning board in order to achieve realistic machine utilization.
Result
With the implementation of Heijunka in the context of the five-day factory on the basis of SAP ERP ECC 6.0, it has been possible, on the one hand, to achieve the goals such as reducing lead times and inventories, increasing flexibility and delivery capability and, on the other hand, to increase transparency for all departments involved in the process, such as purchasing, scheduling, planning, production and sales, since Heijunka planning is not only displayed on a board in production, but can be called up in the system by everyone.
The effects of scheduling and rescheduling (schedule changes) are immediately forwarded to everyone and are thus transparent. The implementation of Heijunka with SAP tools also helps to react quickly and flexibly to changes in demand, and this despite the usually lower quantities than in the automotive industry.
In this way, capacities are already taken into account when customer orders are received, optimum inventory levels prevail across all scheduling levels, the production flow takes place without waste, and helpful tools for order sequence planning are also available.
"With the concepts developed in Budapest, we have succeeded in combining two things: a high number of variants with low quantities on the one hand and very short throughput times with high flexibility on the other.
We have thus created measurable added value for our customers and we are very proud of this. A completely new form of cooperation with our suppliers and a value stream-oriented structure of production are very decisive factors for the great success of the five-day factory".
says Albrecht Köhler, member of the Executive Board of Knorr-Bremse Rail Vehicle Systems.