Technology 4.0 needs transformation culture 4.0
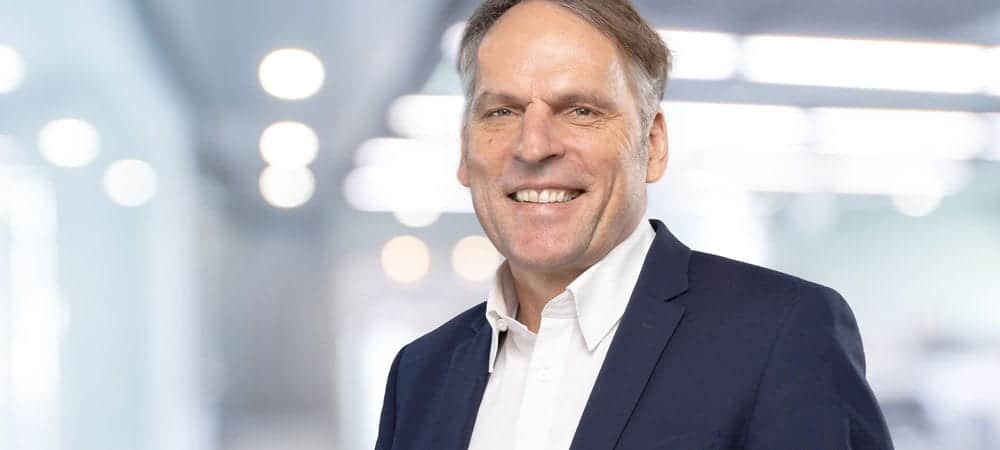
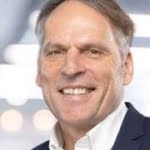
The shutdowns in almost all developed economies in the wake of the Covid 19 pandemic will have serious consequences. The International Monetary Fund estimates that the global economy as a whole will shrink by three percent in 2020, "much worse than during the financial crisis of 2008/09". Accordingly, the developed economies are expected to be hit with an average decline of 6.1 percent.
In the corona year 2020, the following applies to the industry in a completely unsentimental way: Managers must cut costs very quickly because sales have collapsed and current expenses remain high. "Cash is king" is the priority. All other plans must be subordinated to short-term cost management.
The crisis as an opportunity
But crises also harbor the opportunity for change for the better. And there is a time after Corona that responsible managers must keep in mind. A digital transformation with a sustainable plan beyond a pure focus on costs is necessary.
The tried-and-tested principle of modern management doctrines, whether CIP, TPM or others, applies here: every project needs two wings in order to fly. For digital transformation, the formula is: First motivate people, then optimize machines.
Managers of successful digital change projects all agree that the Smart Factory will only succeed with a comprehensive change process and a modern management culture. That is why the Smart Factory is a matter for the boss - and not just one IT project among many.
Technology 4.0 in production requires Transformation Culture 4.0 throughout the company. First, employees must be credibly convinced that technological progress makes sense - also in their interest. Only then can the joint task of optimizing processes and products with new technology be tackled.
Be open, address fears
Let's face it: computers today are actually superior to all of man's physical senses and abilities - they are better at calculating, seeing, touching, tasting, smelling, reasoning, lifting, moving around.
Fears of more technology should therefore be taken seriously. But fears can be countered with facts. For example: Digital technology works for a company's location and jobs, not against them.
In his presentation at an Industry 4.0 event organized by Forcam, Kuka manager Heinrich Munz provided impressive figures to prove that, internationally speaking, unemployment rates are always significantly low where the number of robots per employee in the manufacturing industry is high - South Korea and Germany, for example. Heinrich Munz's conclusion: "We need Industry 4.0 for our well-being and for the future of our children."
Safeguarding locations through personal responsibility
Digitization is not an end in itself. Companies want a smart factory so that they can increase productivity and reduce costs. In Germany, too, it has been possible to maintain sites or bring back production operations because they have significantly increased their productivity through change processes and digital technology, in some cases by more than 30 percent.
The teams in factories can contribute directly to such successes. They need to be trained in this. Education is also the key to any digital transformation.
It means more personal responsibility when people can precisely control processes and products in their area of responsibility via touchscreen, tablet and smartphone along incorruptible analyses.
It means more appreciation when people can do the tasks on the most expensive equipment more easily and better. It means more motivation when people can help ensure that the equipment on the store floor is used optimally and ROCE - return on capital employed - is improved.
In this way, digital transformation becomes a way of securing locations and jobs from within the company. It then offers the best opportunities for reducing costs in the short term, manufacturing more productively in the medium term, and maintaining future viability in the long term.
