Smart Factory
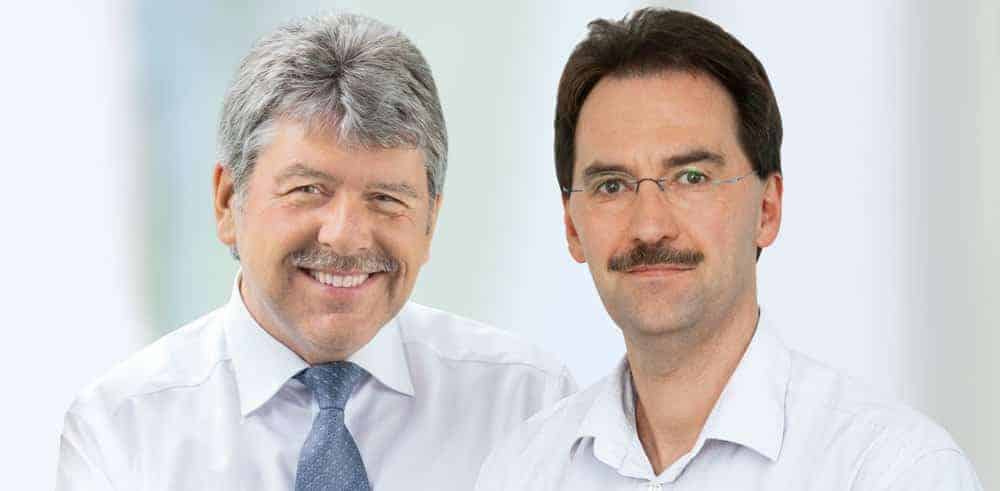
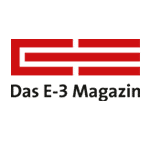
As early as April 2013, the final report of the Industry 4.0 working group, published by Acatech (German Academy of Science and Engineering) and the Research Union, stated:
"Germany is one of the most competitive industrial locations and at the same time the leading factory supplier worldwide. This is due not least to its specialization in the research, development and manufacture of innovative production technologies and its ability to control complex industrial processes.
With its strong mechanical and plant engineering sector, its IT competence, which is remarkable in terms of its concentration worldwide, and its expertise in embedded systems and automation technology, Germany is ideally placed to expand its leading position in production technology.
More than any other country, Germany is capable of tapping the potential of a new form of industrialization: Industry 4.0."
There is nothing to add to this. The optimistic view has hardly changed - but the technology has.
From CIM to Smart Factory
Industry 4.0 expertise did not grow overnight; industrial and IT suppliers have been dealing with the topic of Computer Integrated Manufacturing for more than 25 years.
Naturally, the beginnings of Siemens, Bosch and SAP were very visionary and all too often failed due to the available technology. Names, designations and technology have changed and evolved.
Today, we talk about Manufacturing Execution System (MES), Industry 4.0, Smart Factory and IoT (Internet of Things).
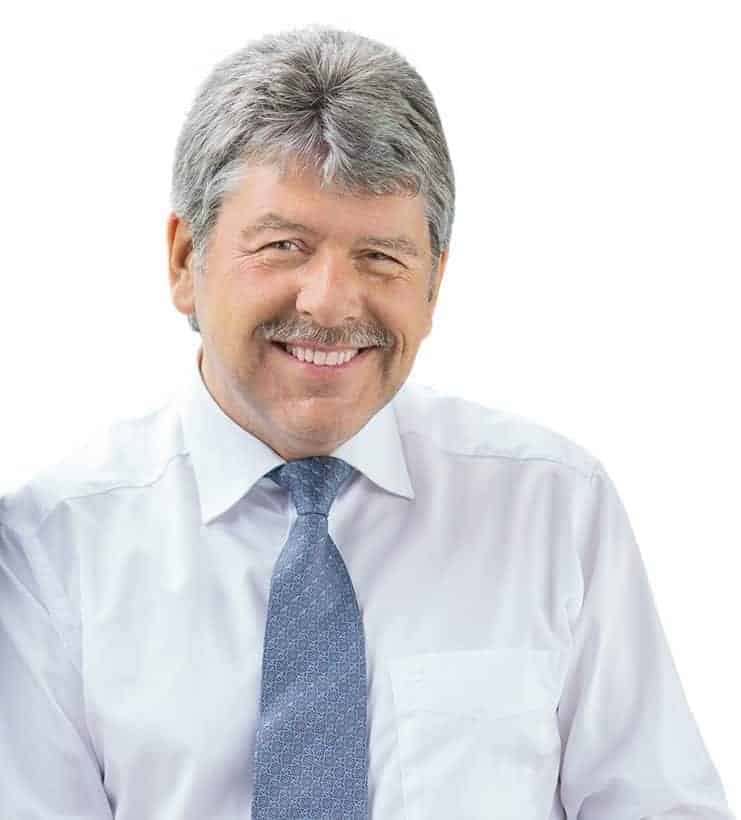
"Even in the past, there has always been a requirement to automate processes and integrate technical objects"
explains Thomas Gard, Spokesman of the Management Board at Orbis and responsible for Sales and Marketing, Investor Relations and the Product Business.
"However, communications technology was not yet ready. The adaptation of Internet technology provided a major boost. Today, systems, machines, devices, etc. can be equipped with an IP address and integrated into internal and external communication. Sensor and RFID technology have also advanced and are affordable. "
In recent years, the ability of machines, software and systems to communicate has improved significantly.
"Thus, it is now possible to take a holistic approach"
emphasizes CEO Thomas Gard, and he knows that there is a growing demand in manufacturing companies to evaluate and process data in "real time" and to integrate it into processes in order to exploit previously unused potential.
Today, the requirements extend far beyond the technical connection of production. The focus is also on the integration of adjacent areas such as logistics, quality, personnel, maintenance and production resources/tools.
"The targeted visualization and evaluation of information, for example via role-based dashboards, is of crucial importance in this context. Information is pushed proactively"
Thomas Gard can report from his professional practice.
Production and process data from manufacturing are clearly visualized in "real time" on web-based, intuitive interfaces. They can be accessed by the end user in accordance with his role and authorization at any time and from anywhere on common end devices.
"The important information is delivered to the right people at the right time"
Gard cites an important aspect.
"Management and employees are always informed about the actual situation and can react immediately to events such as machine downtimes or material bottlenecks. The factory with all its processes becomes transparent."
Visions, goals, reality
"The goal of the smart factory is end-to-end networking and automation of production processes and the actors involved in them, such as people, machines, sensors, actuators, systems, etc. This extends across all levels of the automation pyramid from the ERP system to the control level - in 'real time' and bidirectionally."
defines Thomas Gard, and the result is an autonomously operating, highly available digital factory in which intervention is only required in exceptional cases or in the event of a malfunction - and that economically from series production to customized production in batch size 1.
"This is no longer a vision, but a reality today with SAP ERP and the Orbis digitization suite."
Gard explains.
This includes the basic technology Orbis Multi-Process Suite (MPS), Orbis Manufacturing Execution System (MES) and Orbis Intralogistics. This is demonstrated by the current project of leading enclosure and system supplier Rittal, see page 47.
At Rittal, the world's most modern production plant for compact enclosures with highly automated digitalized manufacturing will be built at the Haiger site by 2018, in line with the principles of Industry 4.0.
Rittal essentially relies on solutions from Orbis and SAP and does so in a 24/7 operation.
"Basically, our offer is aimed at customers who use SAP or would like to use it in the future. This applies to both the SAP Business Suite and S/4."
adds MES team leader Frank Wilhelm from Orbis.
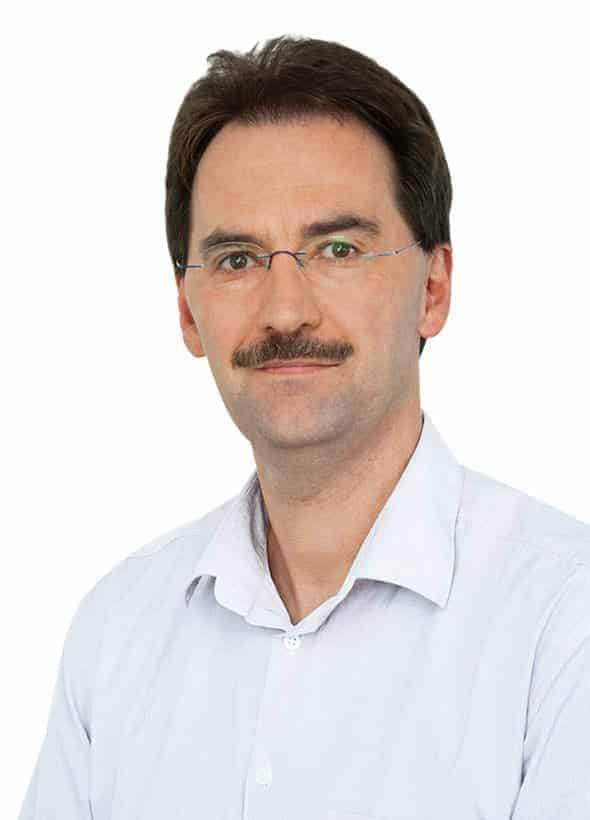
"With our solutions, we offer the possibility of implementing smart factory projects step by step or completely. In doing so, we do not limit ourselves to specific industries or manufacturing methods."
The majority of companies today already have technological components in use that can be used as the basis for a smart factory. For example, machines are often equipped with the necessary sensors and communication technology.
"However, there is often a lack of logical and technical integration of these components into business processes"
Wilhelm knows from numerous customer projects.
Orbis closes this gap with the Multi-Process Suite (MPS), enabling end-to-end, transparent processes. This is achieved by replacing process breaks or "manual" entries with a fast, automated exchange of information.
Machines and devices are integrated bidirectionally into SAP processes. This turns the previous transactional, step-by-step process handling into continuous, integrated process chains.
Orbis MPS thus forms the basis for man-machine processes and machine-machine processes and is the basic technology of Orbis Manufacturing Execution System and Orbis Intralogistics.
These solutions are 100 percent integrated into the SAP ERP processes and use the existing master and transaction data of the ERP system.
"Digitization projects can thus be implemented quickly and easily in an existing SAP environment"
Frank Wilhelm is proud of what he has achieved.
The SAP integration of Orbis MES is certified with the "Powered by the SAP NetWeaver Technology Platform" seal of approval. The solution is the basis for seamlessly linking and synchronizing data and key figures from the store floor with SAP processes and a digitally networked value chain.
Orbis MES is completely implemented with SAP technology (NetWeaver and Abap) and can be flexibly adapted to customer-specific processes (customizing). The necessary know-how for administration and further development is usually available within the company.
It is therefore often not necessary to build up further know-how and additional personnel capacities for further developments, administration of interfaces or system support for the operation, explains Wilhelm in the E-3 interview.
Smart Factory Future
Many companies are hesitant about embarking on Industry 4.0 because they lack a solid guide. Acatech, the German Academy of Science and Engineering, therefore presented the "Industrie 4.0 Maturity Index" at the Hannover Messe on April 25 of this year.
Along a six-stage maturity model, it forms a guideline for companies wishing to develop their individual roadmap. A newly established Industrie 4.0 Maturity Center supports companies in applying the index.
Using this model, companies can analyze their status quo and derive their Industrie 4.0 strategy. The "Industrie 4.0 Maturity Index" was developed in an interdisciplinary consortium of research institutions and companies under the umbrella of Acatech.
"There is a mood of optimism. The target image of Industry 4.0 is shared by many and is in great demand internationally.
Companies are now looking for their individual implementation strategy. Our Industrie 4.0 Maturity Index provides them with neutral, freely available analysis tools for this purpose. The Industrie 4.0 Maturity Center is a contact point for all those who want to use this guide.
said Acatech President and ex-SAP CEO Henning Kagermann in Hanover.
The Industrie 4.0 Maturity Index looks at companies from a technological, organizational and cultural perspective. Six development levels show how data can be obtained, analyzed and made usable in the company.
The approach takes into account the multidimensionality of Industrie 4.0 in the interaction of information systems, resources, corporate organization and corporate culture.
The Acatech study is available free of charge in both German and English.
"The factory of the future operates autonomously"
knows Orbis board member Thomas Gard.
The processes of the value chain are fully integrated via coordinated sets of rules. With the help of control loops, production is largely autonomous and event-controlled. This means that external intervention is only necessary in exceptional cases and in the event of malfunctions.
The intelligence lies in the definition and recognition of these exceptions and the derivation of automated follow-up activities. The networking or integration of the players alone is not yet a smart factory.
That's why Thomas Gard emphasizes:
"Only the definition of the processes and autarkic automatisms enables the process flow in self-controlling control loops."
Smart Factory must be viewed in a differentiated way from the topic of IoT and sensor data. Thomas Gard explains that the core of a smart factory is the end-to-end automation and networking of all processes and the players involved in them in "real time". This is done with defined process-relevant data.
"Our experience shows that it is possible to set up a smart factory project without first defining a holistic IoT strategy"
Board member Gard describes the options.
"IoT can be a way to dissolve boundaries between partners in the value chain. This can give rise to new business models that were not possible before.
Supply chains can be optimized and suppliers can be integrated into demand planning in a timely and more transparent manner. Another example is the development of new service scenarios.
Pure mass data generation in the gigabyte range is not the core of a smart factory in the first step; rather, two aspects must be distinguished.
On the one hand, only the information relevant to the immediate control of the processes is processed in 'real time' in the smart factory.
On the other hand, an analysis of all accruing data, e.g. in the sense of predictive analysis and machine learning, can be carried out. In this way, for example, algorithms can be found that draw attention to future malfunctions at an early stage.
Risks can be continuously minimized and new processes implemented."
Digital transformation
"A major weakness is often the existing evolved isolated solutions and the associated step-by-step handling of individual processes"
Orbis manager Frank Wilhelm knows from many customer inquiries.
Process steps are either operated manually, connected via interfaces or process-relevant data is entered manually. The consequences of these process breaks are incorrect entries and unnecessary process delays, which have a negative impact on throughput times or the current inventory situation, among other things.
"With Orbis MES, there is a fast automated exchange of data between the players on the store floor and SAP."
Wilhelm explains.
"This reduces interfaces to a minimum. The factory is mirrored 1:1 in 'real time' in SAP. In the process, MES processes trigger the operations on machines or plants.
Conversely, machines and systems also control process chains in MES and SAP. This is the only way to automate processes."
Frank Wilhelm from Orbis knows that many machines are already equipped with modern sensor or communication technology.
"However, we also encounter older plants in our projects that are not capable of communicating"
he explains in the E-3 interview.
"Here, elementary signals can be tapped and processed by retrofitting, e.g. with Web IOs, and by electrical cabling. Modern machines offer significantly more advanced possibilities here."
The basic requirement is the establishment of the network connectivity of the end devices (e.g. PLC, sensors, RFID reader...). Manufacturer-specific restrictions must be observed here. This is one more reason to define customer-specific standards.
"Orbis supports the common industry protocols out of the box. Individual connections can also be implemented. In addition, Orbis supports structured object exchange via OData when integrating external computer systems."
is how Wilhelm describes the current situation.
The next step is the technical definition of the processes to be automated and the definition of the associated data exchange. This results in a customer-specific communication model of the smart factory.
"This is the most mission-critical part of the project to implement a smart factory."
emphasizes the MES team leader.
Thomas Gard adds:
"Our solutions create a virtual image of the real events in the factory in SAP ERP in 'real time'. To achieve this, all people and objects involved in the processes - machines, plants, devices, systems, sensors, RFID, etc. - are integrated and networked end-to-end.
All Orbis solutions for Industry 4.0 are fully integrated with SAP."
To enable process integration between store floor and SAP, Orbis has developed the Multi-Process Suite. It is the enabler for Industry 4.0 processes with SAP.
This platform is used to network processes, create dialogs and visualize data. Modular use is also possible. This means that the entire process chain of a factory can be automated, or only individual lines or workstations can be connected initially.
"Currently, it is becoming apparent that we are able to design and verify the behavior of processes at an early stage in the planning of a smart factory"
Board member Gard knows from numerous successful customer projects.
"Process sequences and communication paths can thus be simulated and tested at an early stage without machines and systems already being physically installed. The prerequisite is a company-specific standardization of data communication."
Concluding question: To what extent do digitization projects change the processes and business models of a manufacturing company?
Thomas Gard:
"Process automation is a particular focus of digitization projects in the factory. ERP processes, manufacturing processes and intralogistics processes are fully integrated.
Up-to-date information on stocks, production progress, faults that have occurred, etc. improves plant utilization. Shorter throughput times result in inventory reduction.
Digitization improves the ratio of unit labor costs. This increases competitiveness and safeguards future viability."