Service purchasing with SAP and its limitations
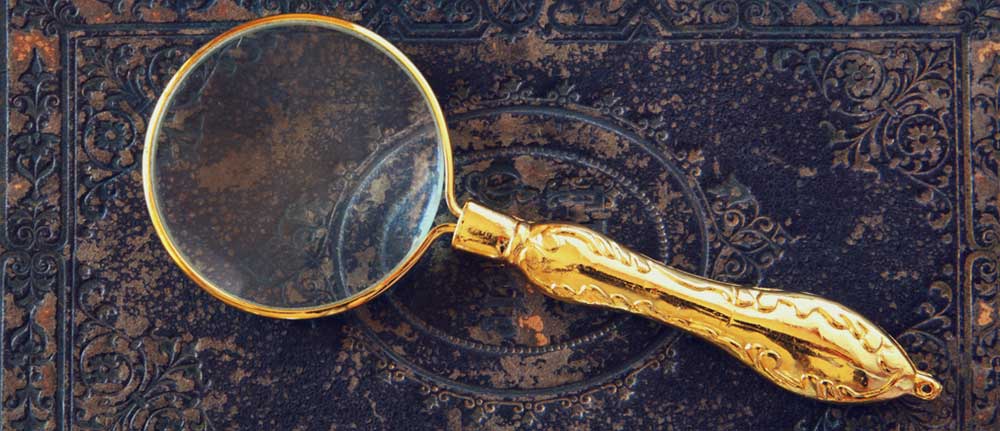
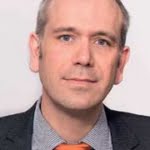
Whether utilities, industrial parks or financial institutions: In most industries, significantly more services are purchased than materials.
As a result, SAP user companies are also faced with the difficult task of having to handle multi-layered service bundles with little market and spending transparency and a low level of standardization.
This makes the operational purchasing processes extremely complex and requires close integration between clients and suppliers: from the creation of service specifications based on the ERP service and material masters, to the request for quotation and submission, to the purchase order and service entry.
These requirements are exacerbated by the fact that the performance of many projects - in the construction sector, for example - extends over longer periods of time.
Since suppliers are then often paid on a performance-related basis at monthly intervals, keyword: partial allowances, they must precisely document the current progress of their activities.
Requirements cannot be met with SAP
However, the SAP standard cannot meet the high integration requirements in service procurement. In order for suppliers to connect seamlessly with their customers' ERP systems, they also need EDI (Electronic Data Interchange) software.
EDI makes it possible to exchange electronic documents in a standard format and thus implement end-to-end digitization.
For larger service providers, the associated expense is perfectly acceptable, and the penetration rate of electronic transfer processes is correspondingly high. The situation is different, however, for smaller providers who employ only a few people.
Since these suppliers usually do not have EDI, all purchasing documents must be sent by e-mail at best and manually entered and processed in the systems involved when processing services. This takes a great deal of time and worsens data quality, which in turn leads to higher error rates.
Lack of support for national standards
As another shortcoming of the SAP standard when working with construction and service providers, I repeatedly hear the complaint from the ranks of SAP user companies that national standards are not supported.
In Germany, this primarily affects the GAEB format (Gemeinsamer Ausschuss Elektronik im Bauwesen), which standardizes the exchange of construction information.
Web-based collaboration platforms
One way out is offered by web-based collaboration platforms that ensure end-to-end digitization of procurement processes. The effort for suppliers is very low: They only have to register on these platforms to be able to communicate automatically with their customers.
In addition, the integration of GAEB interfaces ensures that the applications involved in the construction projects can correctly accept and process the transmitted data.
In short: Collaboration platforms reduce time and costs, increase transparency and help clients to comply with regulations, for example because the supplier services provided can be monitored at every stage of the project.
Web-based collaboration platforms are integrated as add-ons into the client's SAP system environment. One example is the Bits Supplier Collaboration Suite (SCS), which supports the digitization of all operational purchasing processes.
Because buyers access ERP service and material masters directly, there is no need to replicate sensitive purchasing data in the cloud and address related data protection requirements.
With its simple and intuitive user interfaces, the 2Bits Supplier Collaboration Suite enjoys a high level of acceptance among users and provides access to new digital technologies. For example, suppliers can use mobile devices to record performance directly on site and thus automatically document their performance progress.
If GPS coordinates are also used, serial numbers can be used to prove which materials were used in a project at which location and at what time: Potential complaints benefit from this.