Self is the production
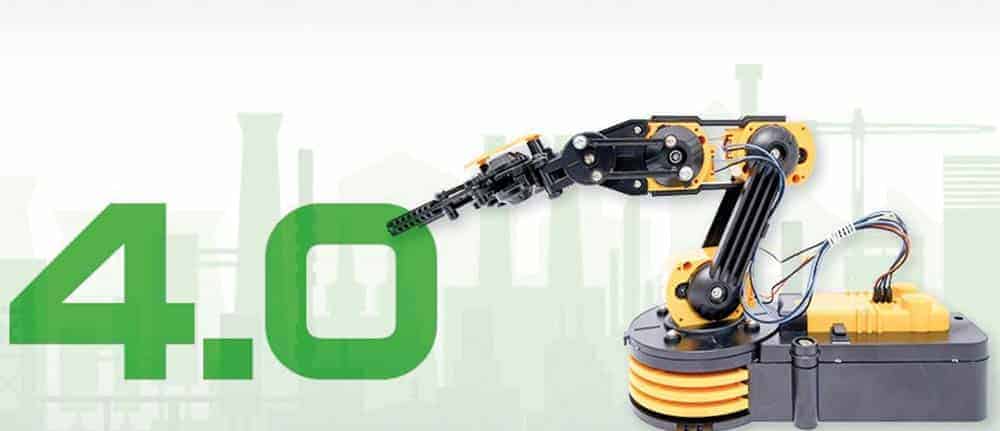
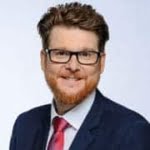
Digitization and networked production are creating smart factories that will eclipse everything that has gone before in terms of energy and speed. But companies still have to overcome a number of hurdles before this can happen.
The Internet of Things (IoT) and its underlying machine-to-machine (M2M) technology are creating a kind of super-transparency in almost every industry.
A now common IoT scenario in industrial manufacturing is as follows: Individual components of the supply chain have become smart devices that continuously deliver real-time data. Physical objects are identified via RFID chips, and their data reaches the cloud via sensors.
Big Data: Vora and Co.
With the right Big Data tools, such as SAP Hana Vora, this data is intelligently linked, analyzed, and completely new insights are gained in an unprecedented level of detail.
Machine learning, data analyses and resulting recommendations for action are implemented automatically. Already during production, the quality of end products is predicted and adjusted in case of corresponding sample or standard deviations.
Ideally, quality control becomes obsolete, as serious quality fluctuations are eliminated immediately. Logistics and manufacturing function almost autonomously; SCM maps the entire supply chain virtually.
A smart factory knows at all times the stock levels, flow of goods and the status of production and permanently ensures self-controlling production processes. Real-time data for the optimization of different production runs can be seamlessly exchanged between the machines.
Cyber-physical systems (CPS) are used to connect software components with parts. Sensors supply huge amounts of data in production every day.
Process zettabytes efficiently
The challenge now is to make efficient use of this data on the order of zettabytes. Industry 4.0 also means harmonizing all processes upstream and downstream of production.
This changes collaboration in the supply chain, as suppliers, logistics service providers and customers must be integrated into the value creation processes. Integration depends on the reliability of systems used and the quality of data.
All participants in the supply chain must agree on common platforms and interfaces. In addition, automation, i.e. the machine level, is coupled with SCM.
Throw old thinking overboard
Big Data technologies such as in-memory data management, analytics, artificial intelligence and machine learning are transforming decision-making processes and businesses.
On the way to the fourth industrial revolution, companies must create standardized system interfaces, especially between manufacturing execution systems and the control level, as well as for the management and provision of data from the cloud.
They have to say goodbye to the classic way of thinking in separate levels. In the smart factory network, devices, sensors, employees, processes, backend systems, supply chains and customers communicate with each other without hierarchies.
This creates completely new opportunities to combine human expertise and computer-generated knowledge. Digitization is the decisive lever for saving resources on a grand scale. But the fourth industrial revolution will only succeed if companies tackle the challenges.