New coat of paint for the EDP
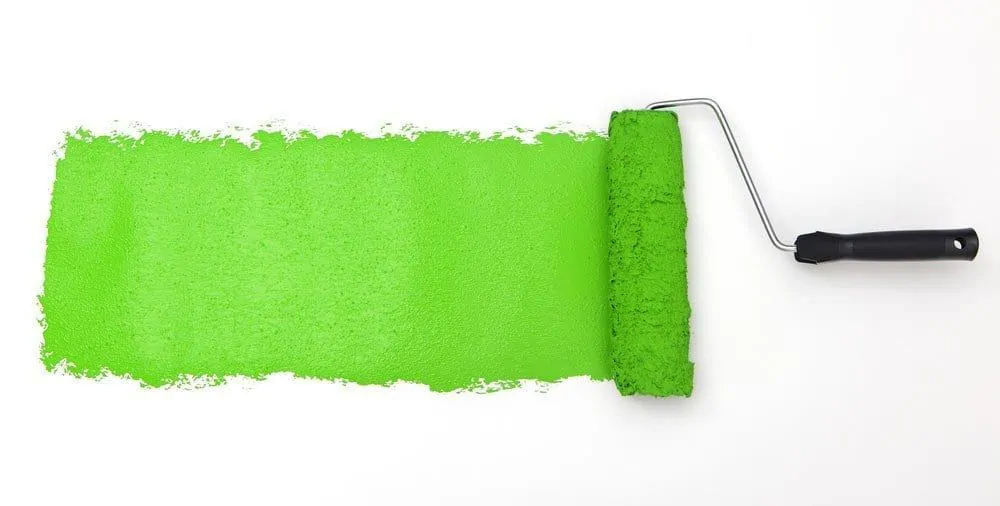
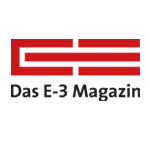
The Hamburg-based Mega Group, a cooperative association of over 5,600 painting companies, will be using Hana from SAP in the future. The wholesaler expects the switch to the in-memory-based database technology to result in faster data processing overall and greater user-friendliness in day-to-day business. Help with the implementation came, among others, from Ettlingen-based SAP partner and industry expert Cormeta.
With 1700 employees at over 100 locations throughout Germany, the Hamburg-based Mega Group is an independent wholesale partner for the specialist trade. In addition to paints and plasters, the product range actually includes everything needed for refurbishment, renovation and modernization: from floor and wall coverings to machines and tools, insulation systems and drywall materials. In addition, the cooperative offers its customers and members a wide range of banking and insurance services.
SAP Basis grows with you
IT grows with the company - this is particularly true of Mega, which was founded in 1901: the cooperative has been an SAP user since 1996. The reason for this was already then the continuous growth caused by acquisitions and mergers with other cooperatives and wholesalers.
In the years that followed, the sales network continued to expand, new branches were added and business management processes were distributed among an increasing number of employees.
To create transparency, further integrations were needed. In the early noughties, Mega integrated a new payroll system and SAP's CRM 4.0 at its headquarters in Hamburg.
Since 2011, the Group has been using CRM 7.0 for field service, and for better processes in service and order processing, both warehouse management software and a BI and ticket system from SAP were introduced in the years that followed.
Cormeta has been a partner from the very beginning. The goal was always to enable the most uniform processing possible for all branches from a central server structure - consequently, a common user interface was also created in 2015 with the installation of the SAP Enterprise Portal.
Another goal was also to improve processes for the benefit of customers. An innovative example of this is certainly the floor cutting machine used in the central warehouse in Hanover, which can be controlled directly via the central SAP system. Customer orders can thus be produced individually according to batch size 1.
"We currently have 74,000 products and process about 1.7 million orders per year for 45,000 customers"
reports Jens Hungershausen, Head of IT at Mega.
"In order to effectively manage the annual growth in orders, we need a powerful IT infrastructure that quickly provides our users with the right information and triggers processes from the ERP in an end-to-end and automated manner."
Hana for faster process control
Accordingly, Jens Hungershausen and his team followed SAP's in-memory database technology SAP Hana closely from the very beginning. A presentation on the topic of SAP Simple Finance, which referred to the new possibilities in financial management, finally convinced the division management and the board of Mega.
When those responsible were then presented with a suitable license and additional purchase offer at the end of 2015, they decided to make the database switch from Oracle to SAP Hana.
"Anyone running an SAP landscape today will have to make the move to Hana at some point"
says the IT manager.
"In order to create transparency, we need fast data processing as well as lean and user-friendly processes - with the switch to SAP Hana, we are creating the conditions to create new or expanded evaluation options that allow us to get the information we need more quickly."
Jens Hungershausen sees a lot of potential for optimization, especially in the area of reporting:
"Evaluation and analysis used to cost us many hours a week - we usually tinkered with some numbers manually in Excel and there were often transcription errors."
As a specialist dealer, Mega attaches great importance to the qualification of its employees.
"We need product-savvy people in sales - they shouldn't be SAP experts, but good salespeople who we can get used to our business processes quickly"
Jens Hungershausen emphasizes and specifies:
"With SAP Hana, we can optimize processes so that our users receive the right information quickly and conveniently. They then make more qualified decisions and this automatically results in an improved operating relationship - i.e. we can train employees more quickly, there are fewer errors in the processes, and the effort required to correct errors is correspondingly lower."
Step by step to the goal
At the end of 2015, Mega started the internal database migration to Hana. In the first step, Hungershausen and his team were primarily concerned with getting to know the appropriate infrastructure for Hana and clarifying the questions that arose in the process.
A workshop was scheduled for this purpose, at which experts from both SAP and SAP partner Cormeta were present. The systems house has been supporting Mega for over 20 years and, among other things, provides service and support for all SAP installations.
The SAP partner has already completely optimized its industry solutions for SAP S/4 Hana and is currently running several S/4 Hana applications in-house for development and testing purposes.
Development of a backup concept
The first major decision Jens Hungershausen and his team had to make during the rollout was whether to pursue the TDI (Tailored Datacenter Integration) approach in the future or use a client-ready system consisting of server and storage.
The decision was made in favor of the former and thus for the possibility of being able to expand the system with any components. In this context, the development of a backup concept was also important.
"Data backup was of course a big issue for us, but here too we were able to work with partners such as Cormeta to define a structure where we are on the safe side"
explains Jens Hungershausen.
Today, SAP Hana runs at Mega both in the data center and in the emergency data center, both are designed identically and are operated with two 2 terabyte servers. Both the ERP and BW systems run on these servers and are immediately available in an emergency.
Faster throughput time already in the standard
A test phase of three weeks was scheduled for the switch to the Hana database. Mega selected 30 employees for this - a cross-section from all areas. A test catalog was drawn up and each employee spent around 2.5 days working in the test system. The changeover took place at the end of March 2016.
Jens Hungershausen and his team are now gradually checking the runtimes of all the reports - at Mega, that's almost 1,000. Some run faster automatically, simply because of the new system.
With the help of SAP's Code Inspector, optimization opportunities are now being identified. For example, some evaluations could be shortened from half a day's processing time to seven minutes. For others, however, a little more work needs to be done.
"We took half a day of training and are just building internal expertise"
says the IT manager.
"In the end, though, it's just the basics of decent and good programming. If you can master those, then you won't have a problem with Hana."
Thus, Hana-specific extension points have already been built in at many points, including in standard programming.
"The standard alone brings a lot of benefits. For example, the customer master sheet always had a very long runtime for us - today, this is done extremely quickly, without us having to do anything there."
Benefits already noticeable
Users are already benefiting from faster results in order processing or scheduling, for example, when they search for customers via CRM or refresh their scheduling lists.
"Those are partial effects that we're having right now just from the new technology, and the next thing we're going to do is build the processes around the S/4 principle of simplification and drive that mindset."
Hungershausen is referring, among other things, to the introduction of SAP S/4 Hana Finance, whose functionalities he expects will improve the quality of evaluations. Thanks to the new database technology, however, business analyses are already running significantly faster.
And this is particularly noticeable in evaluations with a high volume of data, e.g. in the case of an order block, in which the blocked orders from the last six months are selected, or in the case of the order check, which selects the orders from the last three months and checks whether the order-delivery-billing status matches.
"For us, this was a great technological leap. We're excited to see what other possibilities it will open up in the future!"