MES - Putting the Value Chain on the Front Burner
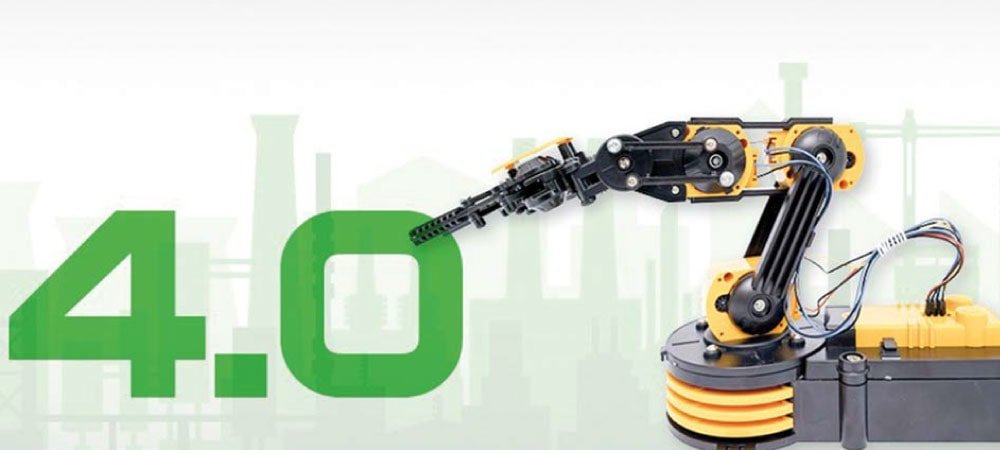
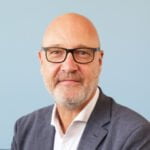
Meeting for a presentation at the event of a business association. We discuss the topic of MES. The association representative gives the following advice: "Better go for the topic of connectivity. Everyone already knows about MES. But how to digitally connect heterogeneous machines - that's what people are interested in. Many companies are not yet ready for that."
As a silver partner of SAP for the connectivity of heterogeneous machines, we are happy to give such a presentation. But the association representative's assessment is remarkable: data is actually the basis of every digital business model. I agree with the association representative's assessment. At the same time, I ask myself the question: Have we in industry put the cart before the horse? After all, industrial value creation takes place in the factory: Shouldn't the digital use of shop floor data actually be preceded by digital data acquisition on the shop floor? Historically, it was the other way around: The first step was taken in the 1970s with the SAP business planning software. Enterprise Resource Planning revolutionized the standardization of tasks in accounting, human resources, materials management and sales.
In the mid-1990s, the term Manufacturing Execution System (MES) developed in the USA. Since then, MES has been globally about data-supported control and monitoring of production processes. Today, SAP is also present in the MES field with its Digital Manufacturing (DM) solution.
Today, in 2023, we are still talking in Germany - and worldwide, for that matter - about the fact that many manufacturers do not have a proper digital machine connection. In the consumer sector, it went the other way: platform providers like Amazon, Facebook (Meta), Google (Alphabet) and Co. are capitalizing on their users' data. Their business models proceed according to the sequence: Collect data, analyze data, monetize data. In the consumer space, user data is the source of value creation. The matching web wisdom: "If something is free to you, you are the product." In industry, data from the shop floor is the source of value creation - semantically and digitally processed information from machines, sensors and factory inputs. Only machine connectivity on the shop floor leads to the real asset of industrial companies, the treasure in the data lake.
It is implemented and analyzed in many places - but probably often without precise and semantically clean process data. No one should be ashamed of this: Industrial manufacturing is complex, every need is different and cannot be compared with the consumer sector, where users' needs can be met with standardizable offerings. Industrial production must never come to an unplanned standstill, otherwise there is a risk of lost sales.
Every factory has its own mix of machines and equipment. Industrial manufacturing requires individual software architectures per manufacturing type and product variance. Each company needs its own digital transformation roadmap - strategy, people, machine connectivity, new systems, new processes, etc. Manufacturing is capital intensive: assets need to run for 10, 20, sometimes 30 years to be profitable.
For companies, this all means that they should plan their digital journey in stages with a sensible sequence of steps. If they want to operate more efficiently, more resiliently and more sustainably, they should put machine connectivity and the associated data semantics at the top of the itinerary - and, of course, rely on high-performance solutions like those from my company. Then connectivity to MES and ERP solutions can follow, so these systems can work with actual real data from the shop floor in real time.
