Maintenance: Reactive - Preventive - Anticipatory
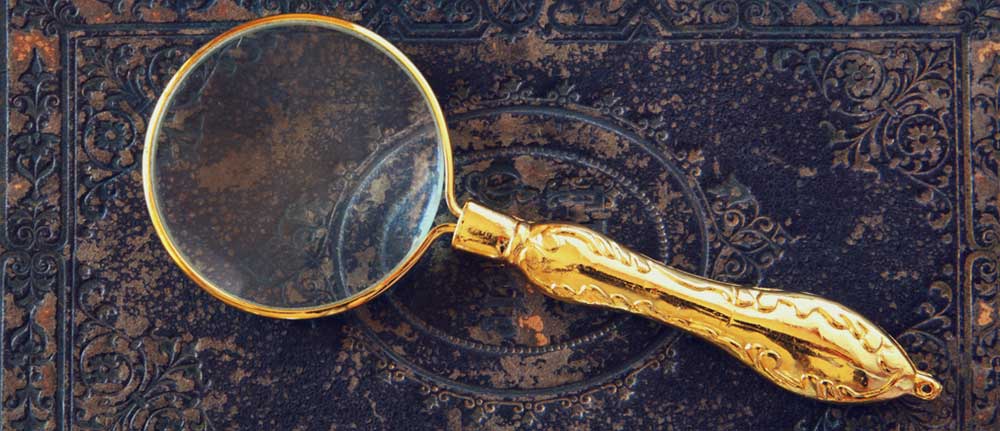
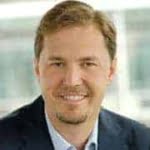
Depending on the industry, unplanned downtime can easily result in costs of several thousand euros per day. This does not include any compensation for damages in the event of delayed delivery.
Predictive maintenance as the key to success
From this originally reactive approach of repairing occurring damage as quickly as possible, so-called proactive preventive strategies have developed, many of which are still valid today.
Of particular interest at present are the digital factory in the context of Industry 4.0 and the associated challenges and opportunities for maintenance. The key to success here is predictive maintenance.
While preventive maintenance aligns the maintenance cycles of plants with average values or the expected service life, predictive maintenance focuses on the current condition of the plant in order to be able to plan maintenance even more precisely.
In addition to a longer service life of the plant and greater plant safety, the goals are fewer accidents, higher productivity, better resource planning, and lower costs.
Digitization and networking of processes and devices are constantly being driven forward and are gaining momentum. In 2017, 27 billion devices were networked, and the market research institute IHS Markit forecasts 125 billion by 2030. According to analysts, global data transfer will also increase by around 50 percent per year over the next 15 years.
The aforementioned technological advances enable the real-time recording of sensor data. These provide information on the current degree of wear of a machine - and form the basis for a potentially higher quality of the decisions made as well as their traceability.
Machine Learning in Maintenance
Two of the foundations for predictive maintenance systems are the acquisition and processing of large amounts of data. Here, early fault detection and temporal forecasting of plant failure determine maintenance planning and optimization of the required resources.
This requires the storage and analysis of large volumes of data (big data). Technologies such as machine learning are suitable for calculating, visualizing and simulating the probability of faults occurring. With the help of such tools, maintenance can be supported by systems technology and placed on a predictive basis.
These approaches are promising. However, in discussions with customers, we often hear that it is already almost impossible to precisely capture the data volumes and keep them up-to-date over longer periods of time.
In a survey of German automotive manufacturers, data management, including inventory data maintenance and change management, is cited as one of the biggest challenges for implementing the digital factory. Automated master data processes (or: automated data maintenance) offer valuable and value-adding support here.
They avoid manual, error-prone entries and thus increase data quality, also in the SAP system and its SAP Plant Maintenance and SAP Predictive Maintenance modules. This in turn pays off in fewer breakdowns, less extra work, optimized inventory, and thus lower costs.
According to IBM, in 2016 alone, the financial loss attributable to poor data quality in the U.S. was approximately $3.1 trillion.
Maintenance 4.0 needs dedicated tools
All indications are that the volumes of data to be handled will increase exponentially in the coming years. Even the best simulation models and evaluations will lead to erroneous statements if they are not based on correct or complete data.
On the way to Maintenance 4.0, therefore, dedicated tools are needed that are capable of getting to grips with the volumes of data. If the maintenance team can focus on core tasks instead of data entry and correction, then predictive maintenance is a viable project.