Interoperability on the store floor: Smooth interaction of all solutions in decentralized IT architectures with Orbis DSP
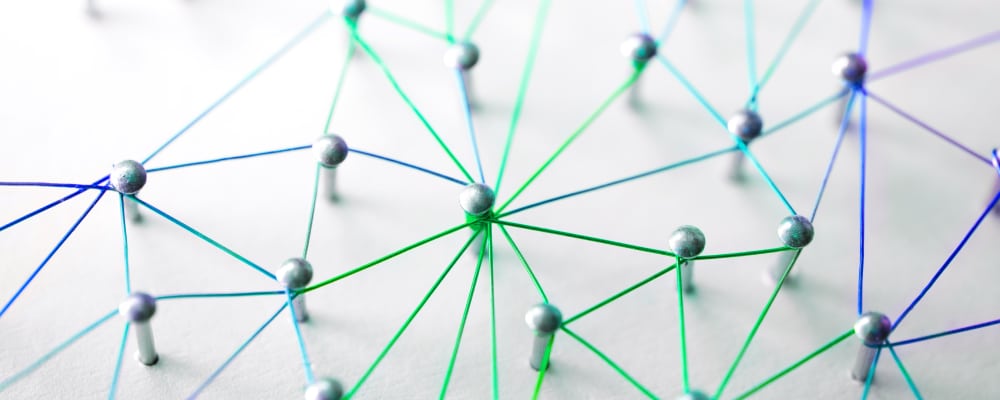
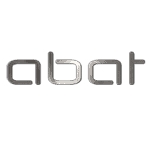
But this only works if the interoperability of all IT systems involved in such a decentralized IT landscape is guaranteed, from the store floor to the ERP back end. The innovative Orbis Distributed Shopfloor Processing (DSP) solution makes this possible and at the same time creates the basis for greater process excellence and efficiency. Thanks to automation and the use of methods such as lean management, the manufacturing industry has made shopfloor processes noticeably more efficient in recent years and significantly increased the speed and performance of systems. However, the potential in the production sector is far from exhausted.
Holistic optimization
Modern technologies such as the Industrial Internet of Things (IIoT), intelligent sensors (Sensor Intelligence Devices, SID), cloud computing, artificial intelligence (AI) and big data analytics enable holistic optimization in the sense of Industry 4.0. A study by Deloitte, "The Fourth Industrial Revolution. At the intersection of readiness and responsibility", for which over 2,000 C-level decision-makers in 19 countries were surveyed, confirms the great importance of the individual technologies for optimizing production, at the end of which the smart factory will emerge.
The smart factory digitally connects all players involved in production in real time: people, i.e. manufacturers, customers, suppliers, machinery, devices, sensors, actuators and, of course, IT systems. This creates the flexibility that is needed for adaptive production in view of increasing individualization - keyword batch size one - constantly changing customer requirements and volatile supply chains. It goes without saying that in networked manufacturing, the production and control systems must also be optimally protected against IT attacks.
Manufacturing Execution Systems
In order to overcome the associated challenges, the trend is towards decentralized IT architecture in which SAP and store floor processes and data storage are separated from each other. Where it makes sense and promises added value, the ERP back-end (S/4 or ECC) is being expanded using the best-of-breed approach with cloud-based services on different platforms, low-code apps or analysis tools from other providers. The use of a modern manufacturing execution system (MES) is a prerequisite for setting up a smart factory and a digitally networked value chain in which the data and activities from the store floor are seamlessly linked with ERP processes. It acts as a central hub between the data from the production level and the business applications such as S/4 or ECC.
In the SAP environment, this vertical integration of data and processes, for example in maintenance and quality management, can be achieved via the SaaS cloud solution SAP Digital Manufacturing or via the tried-and-tested SAP-based Orbis Manufacturing Execution System (MES), which integrates seamlessly with S/4 Hana or ECC 6.0. However, many SAP customers also use the MES of a third-party provider, for example because it is tailored to their specific requirements in terms of manufacturing type, production type or industry focus. According to the "Marktspiegel MES 2022/2023" published by the MES-D.A.CH Association, there are around 180 MES providers in Germany alone that use an MES integrated into SAP or third-party solutions.
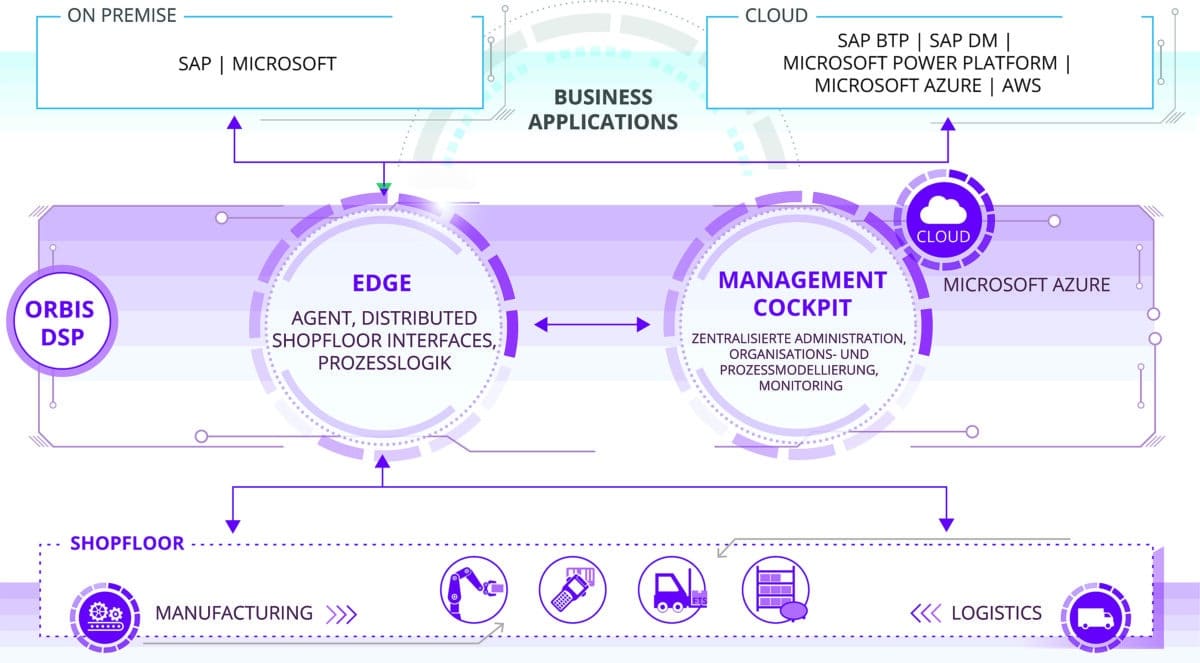
Interoperability on the store floor has many important on-prem and cloud components that Orbis orchestrates perfectly.
Industry 4.0 uses interoperability
Networking and data exchange between different systems, machines and devices is usually achieved through compatibility or on the basis of de facto standards. However, interoperability based on open standards is required to link the machinery and all components relevant to a process in a decentralized IT landscape. It is the key to enabling the automated and seamless bidirectional exchange of data between the store floor, back-end and cloud platforms and creating a digital twin. Interoperability thus also paves the way for networked, adaptive production that can be flexibly adjusted and continuously optimized with the help of AI data analyses in real time (machine/deep learning).
This is where the innovative Distributed Shopfloor Processing (DSP) solution developed by Orbis comes in, which enhances and extends the tried-and-tested Orbis MES and is already being used in practice by several customers. DSP harmonizes the connection of machines across plants and, thanks to open standards, can be linked to any SAP or non-SAP back-end or SaaS cloud application and exchange information with it.
The interoperability and platform independence of Orbis DSP represent real added value for customers. The solution can be used in conjunction with low-code apps based on Microsoft Power Platform or SAP BTP with SAP Build, SAP Digital Manufacturing, Orbis MES or a non-SAP MES and is independent of the hyperscaler's public cloud platform in which the applications run. The central ERP and MES processes meet decentralized process modules on the store floor. In technical terms, Orbis DSP consists of two components that ensure the greatest possible interoperability and flexibility: an edge solution (edge node) and the SaaS cloud-based management cockpit.
Local EDGE component
The platform-independent edge solution is installed locally in a network or in the network periphery. It does not matter whether it is a Windows or Linux server, an industrial PC or a (Docker) container. This ensures high connectivity and short latency times. The native connection with the production systems, as well as with the back-end systems, whether ERP, MES, analytics tool or cloud platform, takes place via so-called asset units. All well-known protocols are supported natively or via OPC UA.
The edge component establishes the connection and communication with the cloud-native management cockpit via agents and routers. It is operated in the TÜV-certified German data centers of Blue Stec, which is part of the Orbis Group, and is therefore completely manufacturer-independent. Process data is stored temporarily in the edge component, for example for visualization in real time. Process data that is relevant for reporting is processed and stored in the cloud for analysis purposes.
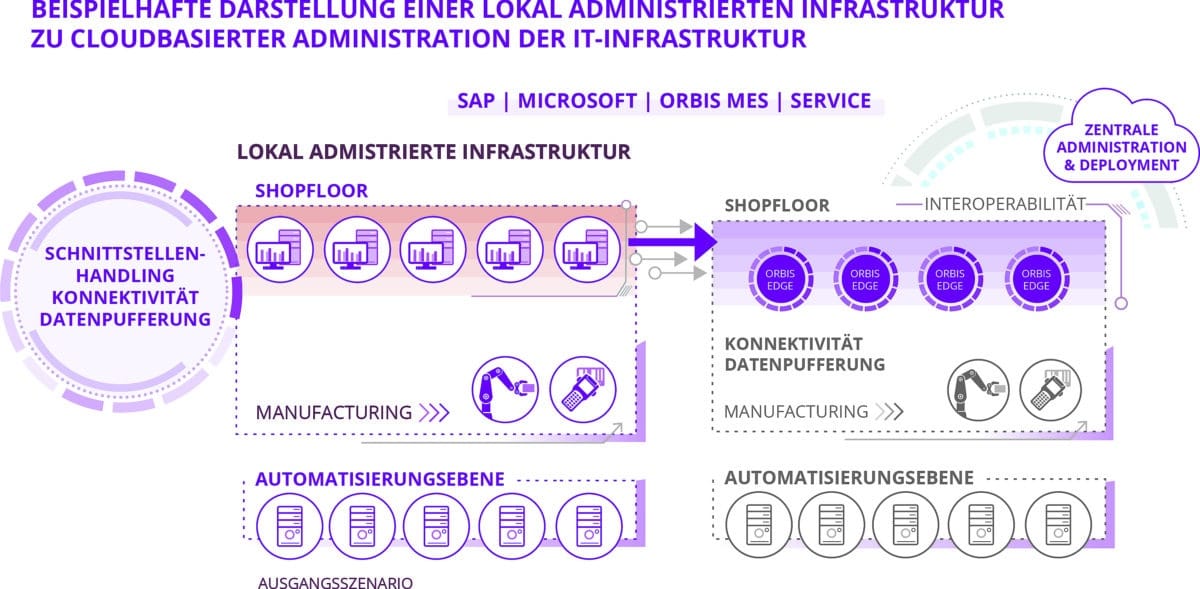
SaaS cloud-based management cockpit
The management cockpit is used to administratively map the store floor organization (plants, halls, production lines/islands), the process objects (from 1 to n) and the back-end systems involved, as well as to model and manage the organization and processes. Data is not stored there.
For example, the management cockpit determines which of the machine data recorded on the EDGE is to be transferred to which back end (ERP, MES, cloud IoT platform, low-code app) and, in turn, which data from the higher-level applications (MES, IoT platform, etc.) flows into the EDGE solution. Furthermore, roles and authorizations are managed in the cockpit.
EDGE and Cloud Cockpit in interaction
The interaction between the two components works as follows: The edge solution collects data provided by the machine controllers in various protocols, stores it and transfers it to the connected back-end systems in accordance with the rules defined in the management cockpit. In return, it transmits the information relevant to production from the released production orders, which originate from an ERP or MES, to the machines.
In order to save expensive (cloud) storage space, it is advisable to condense the machine data in the edge component or with the help of intelligent sensors (Sensor Intelligence Devices, SID) into process-relevant information (= material characteristics) at the hardware level. This significantly reduces the data stream that is transferred to Orbis DSP and higher-level IT systems.
All edge nodes, regardless of which or how many plants they are installed in (1 to n), are configured and managed centrally and uniformly in the Management Cockpit. Additional plants, components and back-end systems can be added as required. This flexibility enables the creation of a modern store floor platform in which all solutions, whether from SAP, Microsoft or another manufacturer, interact smoothly in real time and which can be expanded at any time - another major advantage.
The advantages in practice
The heart of an IT system landscape is naturally the ERP system, such as S/4 or ECC. For production and logistics processes, these are complemented by ORBIS MES. Data from these systems as well as machine-specific parameters are required for communication with a machine. This could be status data from a
This can be the energy consumption (e.g. to determine a CO2 footprint) of the electric motor of a paper machine and the flow rate of an injection molding machine, but also parameters such as the pressure required to start a machine and the necessary start-up temperature.
This information does not necessarily have to be stored in the ERP or MES system. In line with the motto "Keep the core clean", it is instead advisable to store and maintain the data records and parameters in a separate cloud app. This is also where the parameters for controlling the process are released, for example the start conditions for a machine, provided the specified values are adhered to. Such an app can be created quickly using a low-code platform such as SAP Build or the Microsoft Power platform and helps to relieve the storage capacities in the ERP.
Orbis DSP establishes interoperability between the technical data, processes at production level, the cloud app or an IoT platform and "classic" business systems such as Orbis MES and S/4 or ECC 6.0. The edge component triggers the setup process on the machine and immediately reports the end of setup back to the MES, which then starts production. The configuration and administration of the individual plants and the systems installed there, as well as the data and process flows, are carried out centrally in the cloud-based management cockpit.
15 percent more productivity in production thanks to IoT analyses
The set-up times recorded at the edge can also be fed into the IoT platform, where they can be evaluated in the same way as downtimes, operating and production times, planned and unplanned downtimes and energy consumption data. These analyses provide important information on optimization potential in production - a business-critical factor. The process data indicating the operating states can also be used to calculate the availability, throughput and reliability of a system, which are important indicators of machine efficiency.
Due to their enormous scalability, SaaS cloud-based solutions are ideal for such data-intensive processes and analyses. For example, process data from Orbis DSP can be stored in the Azure IoT platform and evaluated using the Microsoft Power BI analysis solution, or the data is stored in the SAP Hana Cloud database (part of SAP BTP) and SAP Analytics Cloud (SAC) is used for evaluation. The results provide a reliable basis for decision-making, which can be used to derive targeted improvement measures for production, for example a reduction in energy consumption or opportunities to increase manufacturing productivity.
In one specific case, a manufacturer of cutting tools found out by analyzing machine data from the manufacturing process that a change in production-relevant parameters could increase productivity by 15 percent. However, such analyses can also be used to identify inefficient energy consumers such as an electric motor, whose performance steadily decreases over a certain period of time with the same power consumption, at an early stage and repair them in good time as part of predictive maintenance. This prevents expensive breakdowns and downtimes.
Conclusion and outlook
With the Orbis Distributed Shopfloor Processing (DSP) solution, Orbis is providing an answer to the future challenges of interoperability in decentralized IT landscapes on the shopfloor. In this context, the internationally active IT service provider is realigning its strategy and organization and bundling its expertise in the areas of (intra)logistics and production in the newly created "Manufacturing & Logistics" division in order to give this field of activity even more weight, and it goes without saying that DSP will be continuously improved and further developed in a targeted manner as part of the defined product roadmap.
In order to meet future requirements in the IoT environment, the solution will be expanded to include cross-system process modelling based on the BPMN standard (Business Process Model and Notation), with a decentralized, model-based logic layer as an integral component. This will be a central point for the next two releases. Another core aspect is the collaboration in various research projects on the topic of sustainability in order to create added value with the help of Orbis DSP in the development of special sustainability solutions, which can be used to determine the CO2 footprint, for example. In addition, new DSP applications for process data acquisition and parameter set maintenance will be developed.
Of course, integration into cloud applications of all kinds is also being continuously optimized and expanded, for example in the direction of SAP BTP or SAP Digital Manufacturing (DM). Given the deep integration of MES and DSP into the processes of S/4 Hana Cloud, customers are ideally positioned for the future. In addition, Orbis can also position itself as a provider of SaaS-based IT architectures in the future; a first step has already been taken with the SaaS operation of the management cockpit in the Azure Cloud in the data centers of Orbis subsidiary Blue Stec. Blue Stec's managed services offering also guarantees the high availability of the solution, including optional 24/7 support.
