Greenfield: Extended Warehouse Management
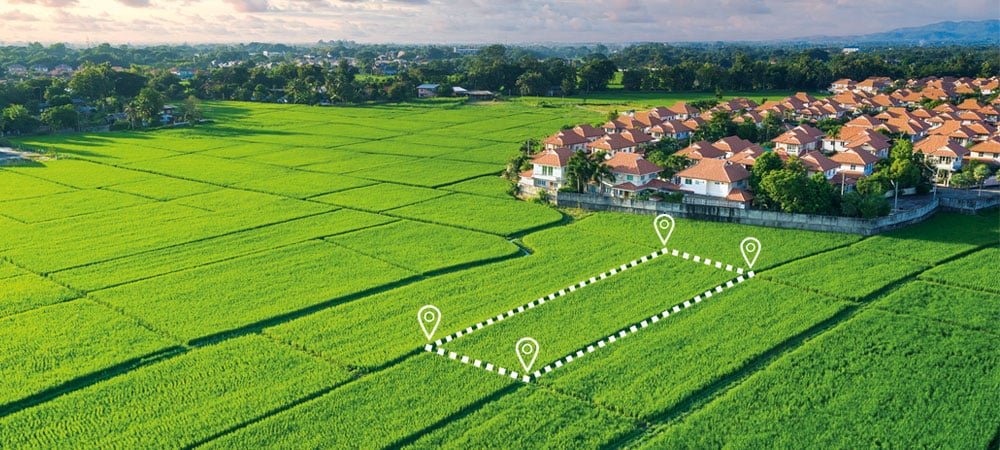

At the family-owned company Fränkische Rohrwerke Gebr. Kirchner, an extensive IT project was due at the beginning of 2018: The previous ERP system had run out of maintenance and was to be replaced by S/4 Hana in the Construction Division and the central areas, initially at the main site in Königsberg. In the logistics area in particular, this was linked to the introduction of the high-performance warehouse management system SAP Extended Warehouse Management (EWM) Embedded.
In addition to the pure conversion to EWM, the foundations were also to be laid for further process digitization. The project team had brought an external implementation partner on board for the planning and introduction in the greenfield approach. "There was no SAP experience in the company at the time. That's why we were particularly dependent on the advice of a partner.explains Uwe Schäfer, Head of SAP IT at Fränkische Rohrwerke, who joined the company in March 2018 and helped set up the internal SAP department.
Implementation was planned within one year. The project followed the classic SAP Activate implementation model: the project plan and phases were defined, and the basic structure for the project flow was created. The first test was successful, but then the difficulties increased. When less than a quarter of nearly 50 test cases worked during the decisive last test due to missing integrations, the decision was made to seek additional support and personnel reinforcement immediately: "It was clear to us that we could no longer handle this extensive project with just the original implementation partner"says Uwe Schäfer.
A recommendation led to the commissioning of FIS Informationssysteme und Consulting. The expertise of the SAP Gold Partner with a focus on consulting and implementation of SAP and logistics projects was convincing. In February 2019, the EWM project management was transferred to FIS, and the previous consulting company also remained in the project. The go-live date was rescheduled for January 2020.
After the first warehouse inspection by FIS, the first thing to do was to take stock and audit. How had the project gotten into such a mess? The main cause had become increasingly clear in the course of the project: The complexity of the processes and the resulting effort for detailed planning had been underestimated in the initial implementation approach.
Complexity and detailed planning
The Construction Division consists of the three business units Drainage Systems, Electrical Systems and Building Services, each of which pursues quite different business models and differs greatly in its respective product ranges, customer structures and sales channels. This complexity is also reflected to a large extent in logistics: "We have very different processes here, also in the handling - small parts that are picked first, products that have to be packed first, as well as large equipment that is loaded directly onto the truck"describes Uwe Schäfer. Up to 160 trucks have to be loaded every day at the Königsberg site alone. Add to this the size of the warehouses: 24 buildings and outdoor storage areas with over 100 different types of storage - the acid test for any warehouse system.
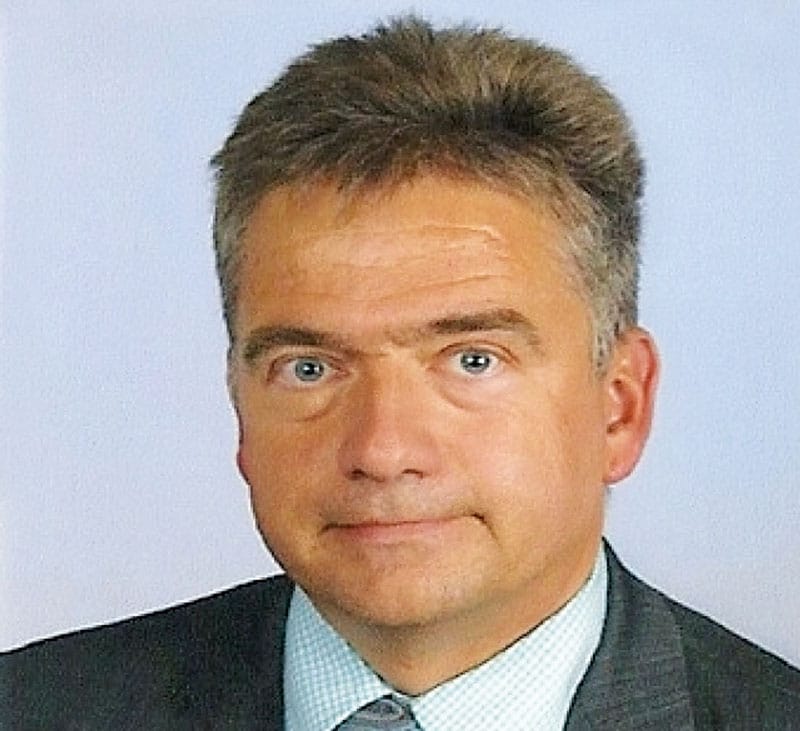
All of this had to be mapped in detail to enable direct implementation, especially integration into SAP processes, and to take into account any necessary adjustments and in-house programming. However, the previous concept did not yet meet these requirements. The decisive task for FIS was therefore to catch up on the detailed planning. For this purpose, the documentation was viewed and individual processes were discussed in detail.
Subsequently, the process descriptions were completed and all future target processes were defined in a technical concept with a very high level of detail. Special developments for individual requirements of Fränkische Rohrwerke, such as a separate radio dialog for picking with mobile devices or the connection of the high-bay warehouse via an individual SAP interface, were also taken into account and co-developed by FIS.
High workload, tight timing
In order to work more efficiently, the project planning and EWM consulting functions were separated. At the same time, prioritization also took place: Concentration on the implementation of the essential processes and functionalities was unavoidable in order to meet the targeted deadline.
Kick-off was in May 2019, and Steffen Will, project manager at FIS, remembers: "The beginning of May was the critical phase. It was clear to all of us that the next few weeks would show how we were progressing and whether the planned go-live date of January 2020 could be met." In practice, the assessments of the high volume of work were confirmed. The project proved to be very labor- and personnel-intensive. In sub-project groups such as incoming goods, outgoing goods or shipping, one employee from Fränkische Rohrwerke worked together with one or two employees from the external consultants. This ensured a constant exchange of information.
In addition to the consultants from the other consulting firm, seven, and at peak times even up to ten consultants were on duty at FIS during the project and were continuously on site in Königsberg. There were intensive discussions and multiple adjustments. The different business areas were examined for consistency in the process flows in order to ensure as homogeneous a process as possible across the entire system as well as process integration. "FIS has provided active support here at all corners".says Uwe Schäfer.
Container wall becomes Kanban board
Keeping track of the current project status was a challenge. Here, the project partners found a pragmatic and effective solution: A huge container wall was converted into a Kanban board. All subtasks and work packages were noted down individually. The corresponding magnetic cards eventually filled the entire width and height of the wall. Depending on the status of implementation, all tasks could thus be assigned to the respective project phases, from detailed concept, development, testing and further development to user testing and training.
In August and September, the first integration tests were carried out - for the first time on a full scale with all adjacent modules, starting with the ordering process.
An important task before the go-live was to train the more than 100 employees in the new system. A multi-stage model was used for this: Lead key users, who were involved in the project from the beginning, first created the training documents for the key users, such as shift supervisors and warehouse managers, with the help of SAP Enable Now. These in turn then took over the instruction in their respective departments. Here, too, FIS provided extensive support. Several managers from the Schwarzheide site have already been trained.
Fast load increase for go-live
In the end, things got exciting once again: "For the go-live, we had planned a ramp-up phase over four weeks. We wanted to start with 30 percent of the usual volume, then gradually ramp up to 100 percent."reports Uwe Schäfer. It turned out quite differently. The season got off to such a strong start that significantly higher volumes had to be handled in the warehouse from day one than had ever been planned - and it worked. The plan was even exceeded. "All the trucks have rolled off the yard and we haven't had a single day of system downtime"says Schäfer. "It's a go-live like we never dreamed possible after the initial difficult course of the project." The management and colleagues were also extremely satisfied, especially with the go-live in the logistics area.
As a result, all SAP modules were introduced at the Königsberg site. In addition, the route plan, inspection and quality management, and the high rack were connected to the new S/4 system via a separate interface. The procedure now serves as a template for implementation in the manufacturer's other warehouses.
"The consultants of FIS have convinced us above all by their high commitment and flexibility, by their motivation to support wherever necessary"sums up Uwe Schäfer. The family-owned company was so satisfied with the cooperation with FIS that further projects have already been planned and partially realized, such as the continued support after the EWM go-live as well as the software transfer of the SAP-based master data maintenance tool.

