Freight costs at a glance
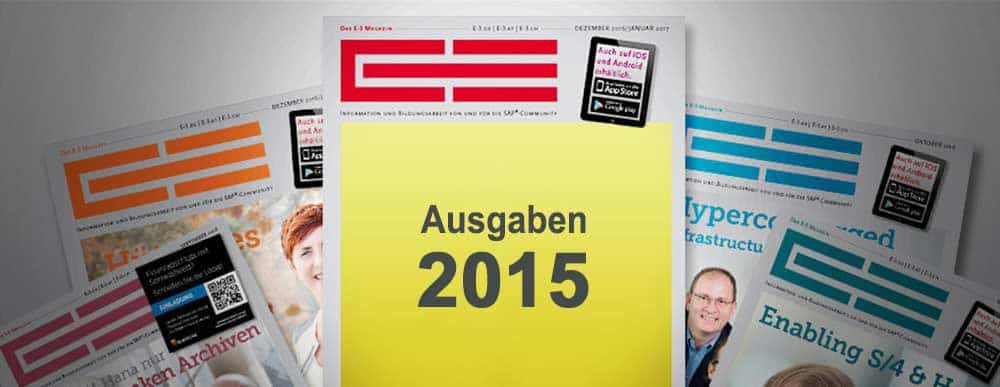
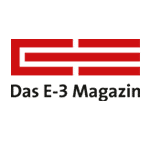
Every year, the company headquarters in Ditzingen receives around 17,500 paper invoices from logistics service providers for freight shipments. These include 210,000 items for spare parts, service parts and small parts as well as 16,000 items for machine shipments. Trumpf handles 90 percent of all freight through five service providers with whom certain conditions have been agreed.
When Trumpf receives the invoices from the service providers, they have to be checked for deviations from the agreed conditions. This is an enormous effort, as some of the invoices are up to 200 pages long.
This process of checking freight costs should now be simplified and combined with a significantly higher quality of checking. The electronic incoming invoices from service providers should be automatically checked and posted by the system within a defined tolerance limit.
Items with deviations outside the threshold value, on the other hand, should be marked and checked manually by the dispatch department in the next step. At the same time, the new solution should be easy for employees to maintain and easy to roll out internationally.
The subsequent tender was won by Serkem with a freight cost solution implemented directly in SAP. All of Trumpf's requirements are mapped in SAP in a user-friendly way.
A freight cost monitor - the heart of the solution - enables clear monitoring and control of all processes.
Automated freight cost check in SAP
The SAP system creates a shipment and a shipment cost document for each outbound delivery. In the freight cost document, the target freight costs are calculated in advance based on the conditions that are stored in SAP for each service provider.
Gross weight, volume weight or loading meters can be set as the basis for the calculation. The conditions can be conveniently maintained by employees using an Excel spreadsheet and easily updated in the SAP system.
Up to 20 condition types with any number of characteristics can be stored and maintained for each forwarding agent. Each condition agreement has its own individual validity period.
Surcharges for distance, weight, hazardous goods, Incoterms etc. are thus taken into account in the target cost calculation. Based on the shipping conditions, the latest delivery time is also determined and later compared with the time from the delivery receipt confirmation, e.g. for Express by 10 am.
Convert invoices
The electronic invoices and proofs of delivery from the individual service providers are delivered to a data converter as individual invoices in various formats, where they are converted into a standardized SAP IDOC format. The converted invoices are then transferred to the PI module of the Trumpf SAP and read into the freight audit monitor.
In the freight cost monitor, the individual items are checked for deviations from the pre-calculated freight costs and delivery times: the target values previously determined are now compared with the actual values of the incoming invoices at item level.
If the deviation is below the pre-set threshold value, the invoice item is automatically posted in the SAP system and is thus released for payment in financial accounting.
If the threshold value is exceeded - e.g. express ordered by 10 a.m., delivery after 10 a.m. or the target costs are exceeded by more than three percent - the shipping department receives a notification from the system. The item is marked in the overview and checked manually by the shipping department.
Controlling delivery times was particularly important to Trumpf. The latest delivery time is now determined on the basis of the shipping conditions and compared with the actual delivery time.
In future, Trumpf will only pay surcharges for express shipping if delivery is made on time. By using the monitor, which is fully implemented in SAP, Trumpf saved over 250,000 euros in the first year alone. At the same time, Serkem's monitor is used to evaluate the delivery reliability of the service providers.