First end-to-end Lean SCM solution for SAP SCM
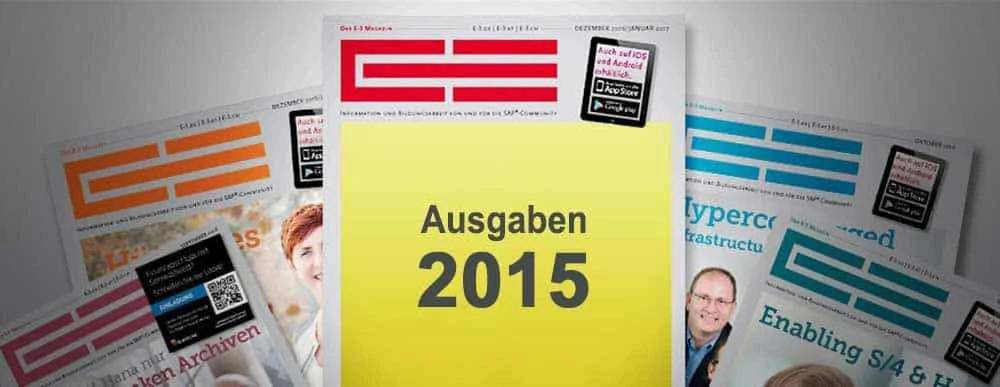
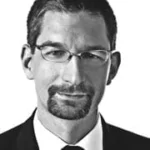
Once originating in the military, the acronym VUCA - composed of the English terms "Volatility", "Uncertainty", "Complexity" and "Ambiguity" - has long been used to describe the central challenges in the modern business world.
For example, manufacturers face increasing volatility and uncertainty of demand, as well as complexity and ambiguity, or ambiguity, of product portfolios and supply chain networks.
Companies in the process industry in particular face the problem of having to adapt their often very lengthy production processes to violent market fluctuations at short notice.
Planning of the entire value chain
For more and more manufacturers, the classic concept of launching their products on the market on the basis of fixed plans has therefore had its day: instead, they are relying on lean supply chain planning.
But while previous lean production approaches were limited to manufacturing in individual plants, the consultants at Camelot Management Consultants and its sister company Camelot ITLab extended the concept for the first time to the entire value chain - across all production stages and country borders.
In collaboration with leading companies from the chemical, pharmaceutical and consumer goods industries, an end-to-end lean SCM concept was created that enables manufacturers to significantly simplify their existing planning processes and improve the synchronization and variability management of their global supply chains.
For the first time, the Camelot Group closes the gap between Lean concepts and special IT solutions with its overall Lean SCM concept through the Camelot Lean Suite.
The add-on, which is certified for SAP SCM, extends the SAP SCM standard with the Lean SCM components of the Camelot Lean Suite. These components were necessary because high demand variability cannot be mastered with the usual planning systems.
On the one hand, these are themselves too complex; on the other hand, they offer too few automated options to respond to a high number of plan deviations.
This means that they only work properly if extremely reliable and stable demand forecasts on market developments and customer demand are available.
Core concepts of the Lean Suite
The Rhythm Wheel supports planning and management concepts that Camelot has developed as core elements of the new Lean Supply Chain approach.
Part of the Camelot Lean Suite is the Rhythm Wheel Designer, which provides the input for the Rhythm Wheel Heuristic, which is integrated into the operational production and detailed planning (PP/DS) of SAP APO.
The Rhythm Wheel Monitor is available for monitoring and as input for tactical planning. It compares the result of the heuristics with the design and serves as a basis for the planner to adjust the design parameters.
Cyclic planning with the Rhythm Wheel
A central function of the rhythm wheel approach is to prescribe a constantly recurring production sequence. Each spoke of the wheel symbolizes the production of a specific product.
For optimal utilization of the equipment, the Rhythm Wheel Designer arranges the products in an optimal sequence. Various optimization approaches are available, e.g. OEE (Overall Equipment Effectiveness) or inventory cost optimization.
The size of the spokes of the wheel - and thus the production quantity - are continuously compared with the existing stocks, receipts and requirements according to a pull logic.
This is a great advantage, especially for companies with long production programs, because it allows them to gear their production specifically to the customer, even when market requirements change, and to optimize makeready processes and campaign sizes.
In this way, they reduce their inventories, increase the utilization of capital-intensive equipment, and at the same time smooth out capacity loads to avoid production peaks.
Synchronous supply chain end-to-end
To implement an overarching lean supply chain concept, it is necessary to include all production stages and sites of a company in the planning: Only effective end-to-end synchronization can avoid waiting times and production downtime and increase responsiveness.
The Rhythm Wheel also plays a central role in this task, as it ensures that production processes are synchronized across all links in an international supply chain.
Since conventional planning concepts only allowed production sequences to be adjusted locally or resource-specifically, it was previously not possible to synchronize them with upstream or downstream production stages.
Variability management
Many companies in the process industry try to compensate for fluctuations in demand primarily by adjusting their production schedules.
Safety stocks, on the other hand, remain untouched and continue to rise in a cost-intensive manner. The Rhythm Wheel, on the other hand, supports manufacturers in handling variability more efficiently and optimally aligning production capacities and safety stocks.
By adjusting the cycle times in production, capacities can be utilized more evenly and production peaks can be avoided. If demand then does significantly exceed expectations, parts of the safety stocks are actively used in planning.
For more than five years, the management and IT consultants of the Camelot Group have been continuously developing their Lean SCM planning approaches, focusing on the specific needs of the process industry.
The pioneers in this development were industry giants from the chemical industry, such as BASF, Dow Chemical and Du Pont. Today, they all rely on cyclical planning with fixed production sequences in order to synchronize their often very complex global production processes in addition to simpler planning.
Similar challenges are facing pharmaceutical manufacturers such as Novartis and AstraZeneca, or companies from the consumer goods industry, for example Procter & Gamble, Coca-Cola and Nestlé.
They all successfully use lean supply chain planning concepts to meet the challenges of the VUCA world.
Global Lean Supply Chain Management:
- Flexibility and agility in the supply chain
- Uniform production
- Shorter production cycles
- Minimum setup times
- Optimal utilization of the production facilities
- Lower production costs
- Fewer inventories
- Higher customer delivery reliability
- Simplified processes for planning and control