It all started with a control station
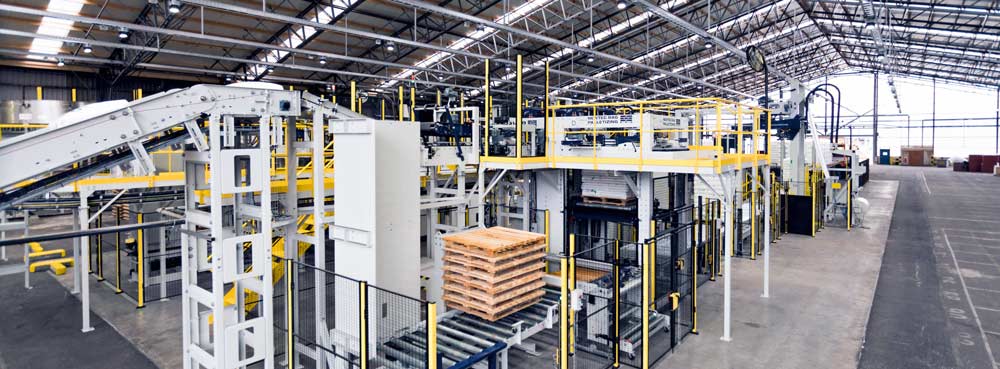
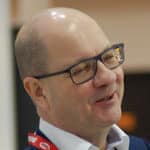
The family-run, medium-sized company Haver & Boecker, headquartered in Oelde, Westphalia, combines two corporate divisions under one roof: wire weaving and machine manufacturing.
In terms of production optimization, the machine factory has been relying on the MES solution Cronetwork from IT service provider and MES supplier Industrie Informatik since 2002.
At that time, the company relied on the extremely powerful FI-2 graphical electronic control station from IDS Scheer. When this state-of-the-art product was taken over by Industrie Informatik in 2000 and further developed under the name Cronetwork Detailed Planning, Haver & Boecker did not have to think twice.
"We were looking for continuity. The clear positioning of Industrie Informatik as a provider of professional MES solutions for discrete manufacturing convinced us."
reports Andreas Bauer, the production manager responsible.
The continuous growth and fast response times made the call for a new solution even louder.
"As much as possible, we wanted to capture data where it was generated. We were looking for a way to improve transparency in order to know about current order situations at any time"
says the production manager.
"With a team of qualified engineers and specialists, we now develop and manufacture around 700 packaging machines per year for the primary industry. In addition, we offer innovative total solutions from processing technology to storage and packaging to shipping technology.
In order to be able to manufacture this wide range of services economically and optimally in the long term, taking existing capacities into account, the introduction of a powerful MES was a logical step."
Bauer reports.
Important requirements placed on the new system were a fast response to process changes, early indications of deviations from the plan, and configurability and adaptation to the respective work task.
The current production situation should be presented to the production planners in the company as transparently as possible - and ideally online.
"Cronetwork was already extremely user-friendly and intuitively designed"
Bauer explains the decision in favor of Cronetwork MES.
SAP Implementation
Another important step from 2011 was the gradual preparation for the upcoming SAP introduction. The client-server environment that had prevailed until then was converted to a web-based solution, and both production data and personnel time recording were henceforth carried out via touch PCs in all production areas.
Since the launch of SAP at the turn of the year 2013/2014, all production employees have been managed and administered using Cronetwork PZE. Together with Cronetwork PDC and detailed planning, order control is now carried out after release via a certified interface from SAP to Cronetwork.
The valuated order data is reported directly back to SAP Controlling (CO).
"Our most important goal during the implementation was to prepare the MES modules BDE and PZE to such an extent that employee messages and order data could be integrated into the SAP system as quickly as possible.
Thus, from the first day after the live start, it was possible to report person bookings and order data from Cronetwork into our new ERP system without any errors."
says Bauer.
Today, order data is transferred from SAP Production Planning (PP) to Cronetwork. After scheduling the orders in the planning board, the detailed planning dates are returned to SAP.
There, the time frame is specified and Cronetwork optimizes the order in this time frame with a defined planning strategy and reports deviations at an early stage. Feedback is sent to SAP PP (order confirmations) and to SAP CO (overhead cost messages).
MES in all areas of the company
Cronetwork MES now supports Haver & Boecker's day-to-day production in a variety of ways - also in interaction with SAP, as Andreas Bauer explains:
"The responsible foremen have an up-to-date overview of all the necessary data. All production data is recorded in one system. The production planner receives information about deviations from the plan at an early stage. In addition, rush orders, sequence changes and adjustments can be carried out very flexibly.
Today, we have reached the point where all deviations, both in operational data and staff time, are reconciled by the first of the month. The processing of error logs at the end of the month has also been drastically reduced."
In general, the Cronetwork modules PZE, BDE and detailed planning are used in all areas of production.
"We only record machine data in the area of machining, but we do not yet evaluate it in detail. In total, more than 300 employees and trainees in production use Cronetwork today.
The transparency in PDA and PZE as well as in detailed planning are unbeatable features for us. There is significantly less material in circulation and the orders remain in flow".
says Bauer.
In addition, there is the simple personnel absence planning and the monthly creation of wage-ready data with transfer via interface to the Infoniqa wage program.
"There's no need for a duplicate system here, either, because we're just adding cronetworks-specific data."
In the area of data visualization, the information control station provides authorized employees with graphically prepared planning results. Workstation monitors always provide an up-to-date view of production.
For Andreas Bauer as the responsible production manager, the following Cronetwork functionalities are of greatest benefit to Haver & Boecker: unique, holistic data acquisition, transparency of production events (online), flexibility in production control, fast, transparent reaction to process changes, and early notification of deviations from the plan.
Looking to the future
In summary, Haver & Boecker's machine factory now has a comprehensive MES in place for all operational employees. The interfaces between SAP and MES function smoothly.
As far as the use of Cronetwork and the cooperation with Industrie Informatik is concerned, Haver & Boecker was particularly helped by the SAP-certified interface and the vast experience from different production areas with different approaches to solutions.
"The cooperation is simply very good - we met on equal terms from the very beginning."
But Haver & Boecker wants to get even more out of its production, as Andreas Bauer knows:
"The operational BI tool Pido is certainly a topic we want to address in the near future to achieve even better key figures and even more transparency in the individual manufacturing areas."